Multilayer Ceramic PCB Manufacturing.Multilayer Ceramic PCB Manufacturing involves the creation of printed circuit boards (PCBs) with multiple layers of ceramic materials. This process enhances thermal management, provides high-frequency performance, and ensures superior mechanical stability. Ideal for applications in aerospace, medical devices, and high-power electronics, these multilayer ceramic PCBs are produced through precise layering, sintering, and metallization techniques, ensuring reliability and efficiency in demanding environments.
Multilayer ceramic printed circuit boards (PCBs) play a vital role in modern electronics. As core components of electronic equipment, they provide reliable electrical connections and structural support, promoting the development and innovation of electronic technology. A thorough understanding of the manufacturing process, materials used, and cost factors of multilayer ceramic PCBs is crucial for engineers and electronics enthusiasts. By mastering the design method of multi-layer ceramic PCB, they can better understand and apply this key technology and promote the progress and development of the electronics industry.
What is a multilayer ceramic PCB?
Multilayer ceramic PCB, that is, multilayer ceramic printed circuit board, is a special circuit board that forms multi-layer conductive paths on a ceramic substrate. Compared with traditional PCBs based on glass fiber reinforced epoxy resin (FR-4), multilayer ceramic PCBs have significant advantages in performance, especially suitable for high-frequency and high-power application environments.
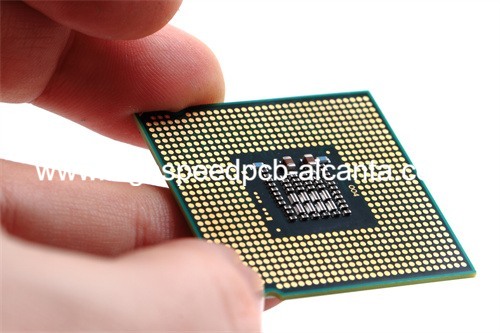
Multilayer Ceramic PCB Manufacturing
First of all, multilayer ceramic PCB uses ceramic as the substrate material instead of the common FR-4. Ceramic substrates have excellent thermal conductivity and electrical properties and can effectively conduct and disperse the heat generated in the circuit, thus improving the temperature stability of the entire circuit board. This advantage enables multi-layer ceramic PCBs to maintain stable electrical performance in high-temperature environments and are less susceptible to performance changes due to temperature effects.
Secondly, multi-layer ceramic PCB has higher reliability. Ceramic substrates have excellent mechanical strength and chemical stability and can withstand the effects of external environments such as vibration, impact, and chemical corrosion, thereby increasing the service life of the entire circuit board. This reliability feature makes multi-layer ceramic PCB widely used in fields that require high circuit stability and reliability, such as aerospace, military and medical equipment.
In addition, multi-layer ceramic PCB also has better high-frequency characteristics. The low dielectric constant and low dielectric loss angle of the ceramic substrate enable multi-layer ceramic PCB to maintain low signal attenuation and distortion in high-frequency circuits, thus ensuring the transmission quality and stability of circuit signals. This feature makes multilayer ceramic PCB widely used in high-frequency fields such as radio frequency (RF) and microwave circuits.
In summary, multilayer ceramic PCB has become the preferred circuit board material for many high-performance electronic devices due to its excellent temperature stability, reliability and high-frequency characteristics, providing electronic engineers with a broader design space and more reliable circuit solutions.
How to design multilayer ceramic PCB?
Designing multi-layer ceramic PCBs is a precise and complex task that requires engineers to use professional software for schematic capture, component placement, routing and layout design. These software are not only tools, but also a bridge between designers and circuits, able to transform abstract circuit schematics into concrete physical layouts.
First, the first step in designing a multilayer ceramic PCB is schematic capture. At this stage, engineers convert the logical structure of the circuit and the connection relationships between various components into a circuit schematic diagram. This requires engineers to have a deep understanding of the circuit’s functionality and performance to ensure accurate design requirements are captured.
Next is the component layout stage. Engineers need to reasonably place various components on the PCB board based on the components and connection relationships in the circuit schematic diagram. Through reasonable layout, the performance of the circuit can be optimized to the maximum extent, while ensuring connectivity between components and good heat dissipation.
Routing is the most critical step in designing multi-layer ceramic PCB. At this stage, engineers need to draw the connection lines between components on the surface of the PCB board and ensure the stability and reliability of signal transmission. Through reasonable wiring design, signal interference and crosstalk can be effectively reduced and the anti-interference ability of the circuit can be improved.
Finally, layout design is a stage that combines component placement and routing for comprehensive optimization. Engineers need to comprehensively consider factors such as circuit functionality, space utilization, and manufacturability to optimize the overall layout of the PCB board. This includes determining the size and shape of the PCB board, the location and number of mounting holes, etc.
In general, designing multi-layer ceramic PCBs requires engineers to use professional software for schematic capture, component placement, routing and layout design. Through reasonable design processes and comprehensive optimization, the performance and reliability of PCB boards can be maximized to meet the needs of different application scenarios.
What is the manufacturing process of multilayer ceramic PCB?
The multilayer ceramic PCB manufacturing process is a complex and precise process designed to ensure the quality and reliability of the final product. The following are the key steps of this manufacturing process:
Multilayer ceramic PCBs usually use high-purity ceramic substrates as base materials. These substrates have excellent thermal conductivity and mechanical strength and are able to withstand high temperature and high frequency operating conditions.
During the lamination stage, multiple ceramic substrates are stacked together to form a multilayer structure. The bonding and positioning between these layers is critical to ensure the accuracy and stability of the circuit.
Once lamination is complete, ceramic compacts are applied to the multilayer structure. These compacts help maintain spacing and flatness between layers while ensuring good thermal conductivity and mechanical support.
During the forming stage, the multilayer structure is processed into the desired shape and size. This may involve cutting, drilling and trimming to meet the requirements of a specific application.
During the soldering process, wires and components on the circuit board are connected to the multilayer structure. This usually involves surface mount technology (SMT) or plug-in assembly technology (THT) to ensure good electrical connections and mechanical stability.
During the drilling phase, holes are drilled through the multi-layer structure to create component mounting locations and electrical connection points. These holes must be precisely positioned and aligned to ensure proper operation of the circuit.
Final inspection is the final step in the manufacturing process to ensure that multilayer ceramic PCBs meet design specifications and quality standards. This may involve aspects such as visual inspection, electrical testing and functional verification.
The manufacturing process of multilayer ceramic PCB is a comprehensive engineering project involving multiple critical steps and precision operations. Accurate execution and quality control of each step is critical to the performance and reliability of the final product. By continuously improving and optimizing the manufacturing process, the quality of multilayer ceramic PCBs can be improved and meet the needs of evolving electronic applications.
How much does a multilayer ceramic PCB cost?
The cost of multilayer ceramic PCBs varies based on factors such as size, complexity, materials, and quantity. Understanding these cost drivers is critical to budget and production cost optimization.
First of all, size is one of the important factors affecting the cost of multilayer ceramic PCB. Larger PCB sizes require more substrate material and conductive layers, increasing manufacturing costs. Additionally, larger PCB sizes may require more production cycles and process steps, resulting in additional labor and equipment costs.
Secondly, the complexity of PCB also directly affects the cost. Complex circuit layouts, multi-layer stacking and high-density wiring may require more production steps and advanced technology, increasing manufacturing costs. In addition, complex PCB designs may require more manual review and adjustments, increasing design and engineering costs.
Material selection also has an important impact on the cost of multilayer ceramic PCBs. High-performance ceramic substrates and conductive materials are generally more expensive than traditional materials. Additionally, special surface treatments and solder mask materials may add additional costs. Therefore, there is a trade-off between cost and performance when selecting materials.
Finally, production quantity is also one of the factors that determine the cost of multilayer ceramic PCBs. Generally speaking, mass production can reduce the unit cost per PCB because fixed costs can be spread over more efficient production processes and higher utilization rates. In contrast, low-volume production may result in higher unit costs because fixed costs need to be spread over fewer PCBs.
In summary, understanding multilayer ceramic PCB cost drivers is critical to budgeting, optimizing designs, and selecting the appropriate production process. By balancing factors such as size, complexity, materials and quantity, costs can be effectively controlled and production costs maximized.
What materials are used in multilayer ceramic PCBs?
Multilayer ceramic PCB is a printed circuit board with multiple layers of conductive pathways on a ceramic substrate, usually using a range of materials to ensure its performance and reliability. These materials include ceramic substrates, copper conductive layers and pads, etc.
First of all, ceramic substrate is one of the core materials of multilayer ceramic PCB. This substrate is usually made of high-temperature ceramic materials such as aluminum oxide (Al2O3) or aluminum nitride (AlN). Ceramic substrates have excellent thermal conductivity and mechanical strength, and can maintain stability in high-temperature environments, making them ideal for high-performance electronic applications.
Secondly, the copper conductive layer is another important component of multilayer ceramic PCB. These conductive layers are formed on the surface of the ceramic substrate through chemical evaporation or electroplating, and constitute the conductive path of the circuit. Copper has good electrical conductivity and workability, which can ensure the stability and reliability of the circuit.
Finally, the solder pad is a critical part for connecting electronic components. The pads are located on the surface of the multilayer ceramic PCB and are connected to the pins of the electronic components through a soldering process. These pads are usually made of gold-plated or tin-plated copper material to ensure good soldering quality and corrosion resistance.
To sum up, multilayer ceramic PCB uses materials such as ceramic substrates, copper conductive layers and pads. These materials have excellent thermal conductivity, electrical properties and high temperature resistance, making them very suitable for high-performance electronic applications. By carefully selecting and combining these materials, the performance and reliability of multilayer ceramic PCBs can be ensured to meet a variety of demanding application requirements.
Who will make the multilayer ceramic PCB?
In the process of manufacturing multi-layer ceramic PCBs, choosing the right manufacturer is crucial. A reliable supplier guarantees product quality, on-time delivery, and provides excellent customer service. For many companies, choosing a reputable and experienced supplier is one of the most crucial decisions.
Our company understands the importance of supplier selection, so we independently produce multi-layer ceramic PCBs based on our own manufacturing plant. As a PCB manufacturer with more than ten years of experience, we have advanced production equipment, a professional technical team, and a strict quality control system. This enables us to meet our customers’ needs in an efficient and reliable manner and ensures that the quality of our products is of the highest standard.
Our manufacturing process covers the entire process from raw material procurement to final product delivery. We select high-quality ceramic substrate materials and process them into multi-layer structures that meet design requirements through advanced processes. Our production lines are equipped with advanced automation equipment to achieve efficient production and precise processing, thus ensuring product stability and reliability.
In terms of quality control, we strictly implement the ISO quality management system and adopt a variety of inspection methods to ensure product quality. From raw material inspection to online inspection during production to comprehensive inspection of final products, we always put quality first to ensure that every multi-layer ceramic PCB meets customer requirements and expectations.
In addition to high-quality products, we also focus on communication and cooperation with customers. Our customer service team is always available to support and assist customers to ensure they have a satisfactory experience throughout the entire purchasing process. We listen to our customers’ needs and feedback and continuously improve and optimize our products and services to meet changing market needs.
To sum up, as an independent supplier of multi-layer ceramic PCBs, our company has won the trust and praise of customers with its high-quality products, advanced manufacturing processes and excellent customer service. We will continue to work hard to provide customers with better products and more satisfactory services, and work with them to create a better future.
What are the 5 qualities of great customer service?
In today’s highly competitive market, providing excellent customer service is one of the keys to business success. Great customer service not only makes customers happy, it also builds good reputation and loyalty. Here are five key qualities of great customer service:
Being able to respond promptly and effectively to customer inquiries and concerns is an important component of excellent customer service. Customers expect quick feedback when raising questions or expressing concerns, and a quick response not only demonstrates the company’s emphasis on customer concerns, but also enhances customers’ trust.
Excellent customer service requires empathy, understanding and attention to your customers’ needs. By listening to customer feedback and needs, and actively finding solutions to meet customer needs, we can build emotional connections with customers, thereby increasing customer satisfaction and loyalty.
Reliability is the cornerstone of great customer service, and businesses need to consistently deliver on their promises and commitments to their customers. Whether in terms of product quality, delivery time or after-sales service, customers hope to receive reliable support and guarantee. Only in this way will customers trust the company and continue to choose and support the company’s products and services.
Clear and transparent communication is an important guarantee for establishing good customer relationships. Throughout the service process, promptly conveying information to customers, answering questions, and maintaining communication with customers can reduce misunderstandings and dissatisfaction, improve customer satisfaction, and enhance the tacit understanding of cooperation between customers and enterprises.
Actively solving problems and striving to achieve customer satisfaction is the ultimate goal of quality customer service. When customers face problems or difficulties, they hope to receive quick and effective solutions. Only by solving problems and ensuring customer satisfaction can a company win the trust and support of customers.
To sum up, high-quality customer service is not only related to a company’s reputation and competitiveness, but also a key factor in maintaining customer relationships and improving customer satisfaction. Through key attributes such as responsiveness, empathy, reliability, communication and problem-solving, companies can establish close connections with customers and achieve win-win development.
Frequently Asked Questions
How do you ensure the reliability of multilayer ceramic PCB assemblies?
Ensuring the reliability of multilayer ceramic PCB assemblies involves rigorous quality control measures at every stage of the manufacturing process. This includes thorough inspection of raw materials, precise fabrication and assembly techniques, comprehensive testing, and adherence to industry standards and specifications. Additionally, proper handling, storage, and environmental considerations are essential for maintaining the integrity and longevity of ceramic PCB assemblies.
Can multilayer ceramic PCBs be repaired or modified?
While multilayer ceramic PCBs are more challenging to repair or modify compared to single-layer or double-layer PCBs, it is still possible under certain circumstances. Repair techniques may include rework of solder joints, replacement of defective components, or modification of existing traces or pads. However, such operations require specialized equipment, skills, and careful consideration of the PCB’s material properties and design constraints.
What are the environmental considerations associated with multilayer ceramic PCB manufacturing?
Multilayer ceramic PCB manufacturing involves the use of various materials and processes that may have environmental implications. Proper handling and disposal of hazardous substances, such as ceramic powders and chemical etchants, are essential to minimize environmental impact. Additionally, efforts to reduce waste, energy consumption, and emissions through recycling, waste treatment, and sustainable practices are increasingly important in promoting environmentally responsible manufacturing processes.
What are the benefits of using multilayer ceramic PCBs over traditional PCBs?
Multilayer ceramic PCBs offer several advantages over traditional PCBs, including higher temperature stability, better reliability, and improved electrical performance. Additionally, they provide enhanced thermal conductivity and insulation properties, making them ideal for high-power and high-frequency applications.
How does the manufacturing process of multilayer ceramic PCBs differ from that of traditional PCBs?
The manufacturing process for multilayer ceramic PCBs involves specialized techniques for layer stacking, ceramic pressing, and sintering. Unlike traditional PCBs, which primarily use fiberglass-reinforced epoxy resin (FR-4) substrates, multilayer ceramic PCBs utilize ceramic substrates and require precise control of firing temperatures and pressures during production.