Multi-Chip FC-BGA Substrates Manufacturer.A Multi-Chip FC-BGA Substrates Manufacturer specializes in designing and producing advanced flip-chip ball grid array (FC-BGA) substrates that support multiple semiconductor chips. These substrates are critical in high-performance computing and consumer electronics, offering superior electrical performance, thermal management, and miniaturization. The manufacturer ensures precision engineering, reliability, and innovation to meet the demanding requirements of modern integrated circuits and complex electronic assemblies.
As electronic devices become more complex and high-performance, the requirements for printed circuit boards (PCBs) are also increasing. Among these technological developments, multi-chip FC-BGA (Flip Chip Ball Grid Array) substrates have become one of the key factors promoting the advancement of electronic products. Multi-chip FC-BGA substrate integrates multiple chips on one substrate through flip-chip technology and ball grid array technology to achieve high-density integration and excellent electrical performance. This article will explore the materials, manufacturing processes, application areas and advantages of multi-chip FC-BGA substrates.
What are Multi-Chip FC-BGA Substrates?
Multi-chip FC-BGA substrate is a highly advanced packaging technology that represents the latest progress in integration and performance in the electronics industry. It uses flip chip technology and ball grid array technology to integrate multiple chips on a substrate in a high-density manner. In this package, the soldering method of the chip is reversed, and the connection pins of the chip are directly connected to the solder balls on the substrate rather than through cables or other media. This design not only enables higher integration, but also significantly reduces the size of the circuit board and improves the performance and reliability of electronic equipment.
The core of the multi-chip FC-BGA substrate is its unique flip-chip technology. In traditional packaging technology, the chip is soldered to the substrate upright, but in the multi-chip FC-BGA substrate, the chip is turned upside down and soldered directly to the substrate, making the chip’s pins more compactly distributed on the surface of the substrate. This design not only increases the connection density between chips, but also significantly reduces the electrical path length between chips, thereby improving signal transmission speed and performance.
In addition, the multi-chip FC-BGA substrate also uses ball grid array technology, which means a large number of tiny solder balls are placed on the substrate to connect the chip and the substrate. This technology can not only achieve high-density chip connections, but also provide a good heat conduction path, effectively dissipate heat, and ensure the stability and reliability of the chip during high-performance operation.
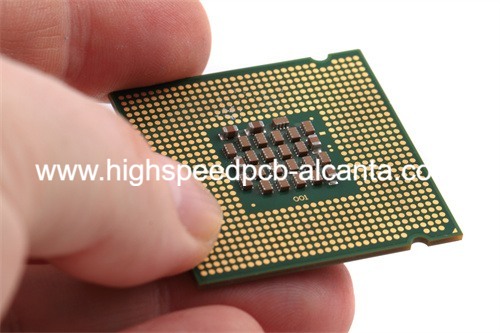
Multi-Chip FC-BGA Substrates Manufacturer
Multi-chip FC-BGA substrates are suitable for various high-performance electronic devices, including but not limited to high-performance computers, communication equipment, consumer electronics and automotive electronic systems. Their application in these fields can greatly improve the performance, reliability and stability of equipment and promote the development and innovation of the electronics industry.
In summary, multi-chip FC-BGA substrate represents the latest development trend of electronic packaging technology. Its high degree of integration, excellent electrical performance and excellent heat dissipation effect make it an ideal choice for high-performance electronic equipment and will be used in the future. Electronic design plays an increasingly important role.
Multi-Chip FC-BGA Substrates design Reference Guide.
Multi-chip FC-BGA substrate design is one of the important links in the design of modern electronic equipment. Its good design can ensure the performance, reliability and manufacturing cost of electronic products. This guide will introduce key considerations and best practices for multi-chip FC-BGA substrate design.
Design planning
Before starting the design, the overall requirements and functionality of the circuit need to be fully planned. Clarify the functions and connection methods of each chip, and determine the signal transmission path and power distribution plan.
Substrate layout
Proper substrate layout is the key to successful design. Considering the communication needs and heat dissipation requirements between chips, the optimal chip layout and pin assignment scheme is designed.
Signal integrity
Special attention should be paid to maintaining signal integrity during the design process. Use appropriate stacked wiring techniques, differential signal design, and ground level separation to reduce signal crosstalk and delay mismatch.
Power distribution
Reasonable power distribution design can ensure stable chip power supply and improve system stability and reliability. Adopt the design principles of regional power supply and reduced resistance to reduce power loss and heat generation.
Thermal management
In multi-chip FC-BGA substrate design, thermal management is a crucial part. Through reasonable heat dissipation design, heat conduction paths and heat dissipation material selection, ensure that the temperature of the chip is controlled within a safe range during operation.
Design verification
After the design is completed, rigorous design verification is an essential step. Verify that the design meets specifications and performance requirements through electromagnetic simulation, thermal simulation, and prototype testing.
Manufacturing feasibility
Manufacturing feasibility should be considered during the design process to avoid overly complex designs and unnecessary manufacturing costs. Reasonable selection of materials and processes ensures that the design can be smoothly transformed into actual products.
Multi-chip FC-BGA substrate design is a complex and critical task that requires comprehensive consideration of signal integrity, power distribution, thermal management and other factors. Through the design reference provided in this guide, designers can design multi-chip FC-BGA substrates more systematically and effectively, providing a strong guarantee for the performance and reliability of electronic products.
What material is used in Multi-Chip FC-BGA Substrates?
Making multi-chip FC-BGA substrates is a complex and precise process, in which the materials used play a vital role. The following are the key materials required to make multi-chip FC-BGA substrates:
Substrate material
Commonly used substrate materials include BT resin (Bismaleimide-Triazine Resin) and ABF (Ajinomoto Build-up Film). These materials were selected for their excellent electrical properties and mechanical strength. BT resin is known for its high temperature stability and excellent dielectric properties, making it suitable for high-performance electronic devices. ABF is a highly reliable thin film substrate material, especially suitable for high-density integration and fine circuit requirements.
Conductive layer
High-purity copper foil is usually used as the conductive layer, and its thickness is generally between 18μm and 35μm. High-purity copper foil has good electrical conductivity and mechanical strength, ensuring the stability and reliability of the circuit.
Solder ball material
A commonly used solder ball material is tin silver copper (SAC) alloy. This alloy has good electrical conductivity and soldering properties, ensuring a reliable connection between the chip and the substrate. In addition, SAC alloy also has good thermal stability and is suitable for high-temperature welding processes.
Filler
In multi-chip FC-BGA substrates, filler materials play an important role in filling the gaps between chips and enhancing the mechanical strength and heat dissipation performance of the substrate. Commonly used filling materials include epoxy resin fillers. Epoxy resin has excellent adhesion and heat resistance, can effectively fix the chip and provide good heat dissipation effect.
To sum up, the production of multi-chip FC-BGA substrates requires the use of a variety of high-performance materials. These materials can not only ensure circuit performance and stability, but also meet the requirements of high-density integration and micro-processing. By carefully selecting and optimizing these materials, multi-chip FC-BGA substrates with excellent performance and high reliability can be produced, promoting the continuous development and progress of electronic technology.
What size are Multi-Chip FC-BGA Substrates?
The dimensions of multi-chip FC-BGA substrates vary depending on their application and design needs. Typically, multi-chip FC-BGA substrates can have different size ranges to meet the needs of various electronic devices. The following are some common multi-chip FC-BGA substrate sizes and their applications:
Small size substrate
Some lightweight portable electronic devices, such as smart watches, headphones, etc., usually require small-sized multi-chip FC-BGA substrates to achieve compact design and lightweight requirements. The dimensions of these substrates may range from a few millimeters to tens of millimeters, depending on the specific product design.
Medium size substrate
Most consumer electronics products, such as smartphones, tablets, laptops, etc., usually require medium-sized multi-chip FC-BGA substrates. These substrates can range in size from tens to hundreds of millimeters, capable of meeting complex circuitry and high-performance processing needs.
Large size substrate
Certain high-performance computing equipment, communication equipment and industrial control systems may require larger size multi-chip FC-BGA substrates. These substrates can range in size from hundreds of millimeters to several meters to accommodate more chips, circuits and connectors.
Overall, multi-chip FC-BGA substrates are available in a wide range of sizes and can be used in applications ranging from small portable devices to large industrial equipment. When selecting the substrate size, designers need to comprehensively consider factors such as product functionality, performance, heat dissipation requirements, and manufacturing costs to ensure that the substrate size can optimally meet the needs of the product and maintain manufacturability.
The Manufacturer Process of Multi-Chip FC-BGA Substrates.
Manufacturing multi-chip FC-BGA substrates requires a series of delicate process steps and processing using advanced equipment. These steps not only require a high degree of technical proficiency, but also require precise operations and strict quality control to ensure that the final product has excellent performance and reliability.
First, substrate fabrication is one of the key steps in manufacturing multi-chip FC-BGA substrates. At this stage, engineers need to select a suitable substrate material. Commonly used high-performance materials such as BT resin and ABF are laminated with copper foil to form a conductive layer. Selecting the appropriate substrate material is critical to the electrical performance and mechanical strength of the entire substrate.
Next is the patterning process, which uses photolithography technology to transfer the designed circuit pattern to the surface of the copper foil. Through photoresist and photolithography machine, the designed circuit pattern is projected onto the surface of the copper foil, and exposed, developed and other processes are performed to form a conductive path and pad area.
Then comes chip flipping, which is one of the key steps in the multi-chip FC-BGA substrate manufacturing process. With flip-chip technology, multiple chips are accurately flipped onto a substrate and connected using solder balls. This technology not only enables high-density chip integration, but also improves circuit reliability and stability.
Filling and encapsulation are the next steps, with engineers filling the flip-chip with epoxy or other filling materials to enhance mechanical strength and heat dissipation. Filling material selection and control of the filling process are critical to overall substrate performance and reliability.
The last step is testing and inspection. Engineers will conduct strict electrical testing and optical inspection on the manufactured multi-chip FC-BGA substrate to ensure that its performance is stable and reliable. This step can identify potential problems and repair them, ensuring that the quality of the final product meets standard requirements.
To sum up, manufacturing multi-chip FC-BGA substrates is a complex and delicate process, which requires engineers to have rich experience and technology, as well as advanced equipment and processes, in order to produce high-performance, high-reliability electronic products.
The Application area of Multi-Chip FC-BGA Substrates.
As an advanced packaging technology, multi-chip FC-BGA substrate is widely used in high-performance electronic equipment. Its application fields include but are not limited to the following aspects:
high performance computing
In the field of high-performance computing, such as servers and supercomputers, multi-chip FC-BGA substrates play a key role. These devices need to process large amounts of data and perform complex computing tasks, placing extremely high demands on high-density and high-speed data processing capabilities. The multi-chip FC-BGA substrate provides stable and reliable electrical connections for these devices with its high-density integration and excellent electrical performance, thereby ensuring the performance and stability of the device.
Communication device
In the field of communication equipment, such as 5G base stations, optical fiber communication equipment, etc., multi-chip FC-BGA substrates also play an important role. These devices require high-speed signal transmission and processing to meet growing data demands. Multi-chip FC-BGA substrates can achieve fast data transmission and processing through optimized electrical design and high-density integration, providing key support for performance improvement of communication equipment and network connections.
Consumer Electronics
In the field of consumer electronics, such as high-end smartphones, tablet computers and other products, multi-chip FC-BGA substrates are widely used. These products pursue higher performance and smaller size while requiring stable and reliable electrical connections. With its miniaturization and high performance, multi-chip FC-BGA substrate provides stable and reliable electrical connections and high-speed data transmission for consumer electronics products, meeting users’ needs for high-performance electronic products.
Vehicle electronics
In the field of automotive electronics, such as autonomous driving systems, in-vehicle entertainment systems, etc., multi-chip FC-BGA substrates also play an important role. These devices need to be highly reliable and durable to handle harsh working environments and long-term use. Multi-chip FC-BGA substrates can achieve high-reliability electrical connections and stable performance through optimized manufacturing processes and material selection, providing an important guarantee for the reliable operation of automotive electronic products.
In summary, multi-chip FC-BGA substrates have broad application prospects in high-performance electronic equipment, and their applications in high-performance computing, communication equipment, consumer electronics, and automotive electronics will continue to expand and deepen, driving the The continuous development and progress of electronic technology.
What are the advantages of Multi-Chip FC-BGA Substrates?
The advantage of multi-chip FC-BGA substrate is not only that it can integrate more functions in a limited space and improve device performance, but also shows excellent performance and advantages in many aspects.
First of all, the high-density integration of multi-chip FC-BGA substrate is one of its significant advantages. Through flip-chip technology and ball grid array technology, multiple chips can be tightly integrated on a substrate to maximize the use of limited space. This high-density integration not only enables more functions in miniaturized devices, but also improves the overall performance and efficiency of the device.
Secondly, the multi-chip FC-BGA substrate has excellent electrical performance. The use of low inductance and low resistance design can reduce the impedance of the circuit and reduce the power consumption during signal transmission, thereby improving signal integrity and transmission speed. This is particularly important for high-speed data processing and communication equipment to ensure the stability and reliability of data transmission.
In addition, the multi-chip FC-BGA substrate also has efficient heat dissipation capabilities. Through effective heat dissipation design, the heat generated by the chip during high-power operation can be quickly conducted and dissipated, ensuring that the chip operates within a safe temperature range and improving the stability and reliability of the equipment. This is particularly important for high-performance computing and communication equipment to ensure stable operation of the equipment for a long time.
In addition, the miniaturization of multi-chip FC-BGA substrates is also one of its advantages. The compact design helps reduce the size and weight of electronic equipment, making the equipment more lightweight and portable, while also meeting the size requirements of modern electronic products. This makes multi-chip FC-BGA substrates widely used in consumer electronics products, such as smartphones, tablets, etc.
Finally, the multi-chip FC-BGA substrate has high reliability. The use of advanced materials and manufacturing processes can ensure the long-term stability and reliability of the product. This is particularly important for applications in industrial control, automotive electronics and other fields. It can ensure the stable operation of equipment in harsh environments and improve the service life and reliability of equipment.
To sum up, multi-chip FC-BGA substrate has become one of the key factors in promoting the progress of electronic products due to its many advantages such as high-density integration, excellent electrical performance, efficient heat dissipation, miniaturization design and high reliability. It provides strong support and guarantee for the development of modern electronic equipment.
FAQ
What is FC-BGA substrate?
FC-BGA substrate is a Ball Grid Array (BGA) package using Flip Chip technology. In FC-BGA, the electrical connection of the chip is achieved by connecting directly to the solder balls on the substrate, rather than through wires. This design improves signal transmission speed and reliability and enables higher chip density.
What is the difference between FC-BGA substrate and traditional BGA substrate?
The biggest difference between FC-BGA substrate and traditional BGA substrate is the chip connection method. Traditional BGA substrates use solder balls to connect chip pins, while FC-BGA substrates use flip-chip technology to directly connect the metal contact surface of the chip to the solder balls on the substrate. This design enables the FC-BGA substrate to have a shorter signal transmission path and higher signal integrity.
What applications are FC-BGA substrates suitable for?
FC-BGA substrate is suitable for electronic equipment that requires high performance and high-density integration, including high-performance computing, communication equipment, consumer electronics, and automotive electronics. Due to its excellent electrical performance and reliability, FC-BGA substrates are widely used in these fields.
How complex is the design and manufacturing process of FC-BGA substrate?
The design and manufacturing process of FC-BGA substrate is relatively complex and requires precise processes and equipment. The design process involves chip layout, pin connection, heat dissipation design, etc., while the manufacturing process includes multiple steps such as substrate production, patterning, chip flipping, filling and packaging. Although complex, the high performance and reliability of FC-BGA substrates can be ensured through reasonable design and advanced manufacturing processes.
What is the heat dissipation effect of FC-BGA substrate?
FC-BGA substrate can achieve good heat dissipation effect by designing a reasonable heat dissipation structure. Filling materials usually have good thermal conductivity and can effectively conduct the heat generated by the chip and dissipate the heat through the heat dissipation structure on the surface of the substrate. In addition, the flip-chip design also helps improve heat dissipation because the direct contact between the chip and the substrate can transfer heat to the substrate faster.