Multi Cavity Substrates Manufacturing.Multi cavity substrates manufacturing refers to the process of producing substrates with multiple indentations or hollow spaces. This technique is commonly employed in electronics and semiconductor industries for various applications like microelectronics, sensors, and integrated circuits. The process involves precision engineering and meticulous attention to detail to ensure uniformity and consistency across all cavities. It encompasses various stages such as substrate preparation, cavity formation, material deposition, and quality inspection. Multi cavity substrates offer advantages like higher integration density, improved thermal management, and enhanced functionality, making them indispensable in modern electronic devices.
Multi-cavity substrates are key components in today’s electronic devices, and their highly integrated designs provide important solutions for various applications. This article takes an in-depth look at the manufacturing process of multi-cavity substrates, providing readers with a comprehensive guide covering everything from design to cost. Whether you are a beginner or a professional, this article will help you understand the importance of multi-cavity substrates and their applications in the electronics industry.
What exactly is a multi-cavity substrate?
Multi-cavity substrate is a key component in electronic equipment. It is not only a printed circuit board, but also a specially designed circuit board that contains multiple cavities in its structure. These cavities can accommodate various electronic components, such as integrated circuits, sensors, antennas, etc., making multi-cavity substrates a key component for realizing highly integrated and feature-rich electronic devices.
In electronic devices, multi-cavity substrates play an important role. First, it provides support and connection for electronic components, allowing each component to work stably and reliably. Secondly, the design of multi-cavity substrates can achieve a high degree of circuit integration, reduce the size of the device, and improve the performance and functionality of the device. In addition, multi-cavity substrates can also achieve circuit isolation and shielding, reduce interference, and improve system stability and anti-interference capabilities.
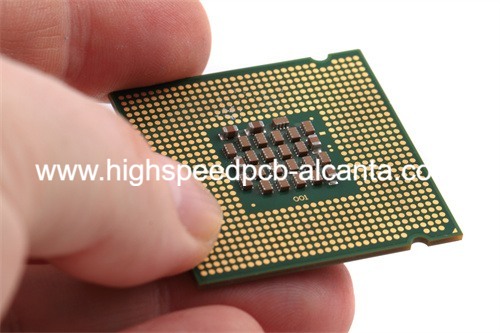
Multi Cavity Substrates Manufacturing
In general, the multi-cavity substrate is not only a printed circuit board, but also a specially designed circuit board. Its structure contains multiple cavities, which can achieve a high degree of integration and rich functions of electronic components, and provides a good foundation for electronic equipment. Performance improvements and size reduction provide significant support.
What is the design principle of multi-cavity substrates?
The design of multi-cavity substrates is a complex and critical task, which involves a variety of key principles. The reasonable application of these principles can directly affect the performance and reliability of multi-cavity substrates. The key principles of multi-cavity substrate design and their application in the design process will be introduced in detail below.
In the design of multi-cavity substrates, ensuring signal integrity is crucial. Signal integrity involves issues such as timing, interference, and impedance matching in signal transmission. During the design process, the layout, length matching, differential signal processing, etc. of signal lines need to be considered to ensure stable signal transmission.
Different circuits in a multi-cavity substrate may interfere with each other, so electromagnetic compatibility needs to be considered. Through reasonable layout and shielding design, electromagnetic interference can be effectively reduced and the anti-interference ability of the entire system can be improved.
Electronic components in multi-cavity substrates generate heat when working, and excessive temperatures will affect the performance and life of the circuit. Therefore, heat distribution and heat dissipation design need to be considered during the design process to ensure that the system can maintain a stable temperature under various operating conditions.
Multi-cavity substrates are usually installed in complex mechanical environments, so they need to have certain mechanical strength and earthquake resistance. During the design process, the thickness of the board, connection method, support structure, etc. need to be considered to ensure that the multi-cavity substrate can withstand the challenges of the external environment.
Each circuit module in the multi-cavity substrate requires a stable power supply, so power supply stability is one of the key factors to consider in the design. During the design process, it is necessary to rationally plan the power supply lines, filter circuits and voltage stabilizing circuits to ensure that each circuit module can receive a stable power supply.
By rationally applying the above key principles, engineers can design multi-cavity substrates with excellent performance, stability and reliability to meet the needs of various complex electronic systems. At the same time, with the continuous development of technology, the principles of multi-cavity substrate design are also constantly evolving, providing strong support for the functional improvement and size reduction of electronic devices.
What is the manufacturing process of multi-cavity substrates?
Fabricating multi-cavity substrates is a complex and delicate process that requires multiple critical steps, from material preparation to final testing, each step is critical.
First, the process of fabricating multi-cavity substrates begins with the material preparation stage. At this stage, a suitable substrate material needs to be selected, usually FR-4 fiberglass composite or metal substrate. The choice of substrate material directly affects the performance and cost of multi-cavity substrates.
Next is the graphical cavity design stage. Using advanced CAD software, designers graphically design circuit graphics and cavity structures. This step is critical because the accuracy of the design directly affects the functionality and stability of the multi-cavity substrate.
This is followed by the printed circuit stage. Using printing technology, a circuit layer is printed on the surface of the substrate to ensure accurate and reliable circuit connections. This requires sophisticated equipment and processes to ensure the quality and accuracy of the circuit.
Next comes the cavity packaging stage. At this stage, electronic components are assembled into individual cavities and packaged. This involves welding, bonding and other processes, which require a high degree of technology and experience to ensure the quality and stability of the package.
After packaging is completed, it is the final testing stage. Functional testing and quality checks are performed on multi-cavity substrates to ensure stable and reliable performance. This includes electrical testing, signal testing, etc. to ensure that multi-cavity substrates meet design requirements and standards.
The entire manufacturing process involves multiple links, each of which requires a high degree of professional knowledge and technical support. Only by strictly controlling every aspect can we ensure the production of high-quality multi-cavity substrate products.
To sum up, the process of manufacturing multi-cavity substrates includes multiple steps such as material preparation, graphic design, printed circuits, cavity packaging and final testing. Every step is critical and requires sophisticated equipment and processes to ensure product quality and performance.
How much does it cost to manufacture a multi-cavity substrate?
The cost of manufacturing multi-cavity substrates is a complex issue influenced by multiple factors, from material selection to manufacturing processes, which all have a significant impact on the final cost.
First, one of the main factors affecting the cost of multi-cavity substrates is material cost. The choice of substrate material plays a critical role in cost. Common substrate materials such as FR-4 fiberglass composites and metal substrates have significant differences in cost. FR-4 is a common low-cost material suitable for most applications, while metal substrates are generally more expensive due to their excellent thermal conductivity and mechanical strength.
Secondly, the complexity of the manufacturing process is also one of the important factors affecting costs. The manufacturing of multi-cavity substrates requires multiple processes, including graphic cavity design, printed circuits, cavity packaging and other steps. Each step requires corresponding investment in manpower, equipment and time, which will directly affect the manufacturing cost.
In addition, design requirements and degree of customization will also have an impact on costs. If a customer requires specific design requirements or a customized solution, additional engineering and adjustments are often required, which increases manufacturing costs.
In addition to the above factors, market competition and supply chain conditions will also have an impact on costs. Competition among manufacturers may lead to price fluctuations, and instability in the supply chain may also lead to fluctuations in raw material prices, which in turn affects the final cost of multi-cavity substrates.
Taking the above factors into consideration, generally speaking, the cost of manufacturing a multi-cavity substrate will usually range from a few hundred to a few thousand dollars, depending on the customer’s needs and requirements. For mass production orders, the cost will usually be relatively low, while small batch custom orders may be more expensive.
Overall, understanding the cost factors of multi-cavity substrate manufacturing is important for customers to make informed decisions, so they can optimize costs and meet their specific needs by taking the above factors into consideration.
What materials are multi-cavity substrates made of?
When manufacturing multi-cavity substrates, it is crucial to choose the right materials because the properties of the materials directly affect the quality and performance of the multi-cavity substrates. The following are common materials used to manufacture multi-cavity substrates and their characteristics:
FR-4 is one of the most common multi-cavity substrate materials and has excellent insulation properties and mechanical strength. It is composed of fiberglass cloth and epoxy resin, has good heat resistance and chemical resistance, and is suitable for most general applications.
Metal substrates are usually composed of aluminum or copper bases and have excellent thermal conductivity and heat dissipation properties. This material is suitable for applications with high heat dissipation requirements, such as high-power LED lighting, power modules, etc.
Ceramic substrates have excellent high temperature resistance and insulation properties, and are suitable for applications in high-frequency, high-speed circuits and microwave radio frequency circuits. Their low dielectric constant and low loss tangent make them excellent in high frequency circuits.
Polyimide substrates have excellent high temperature resistance, chemical stability and mechanical strength, and are suitable for electronic equipment in high temperature environments. Their low dielectric constant and low dielectric loss make them ideal for high frequency circuits.
PTFE substrate has excellent dielectric properties and chemical stability and is widely used in microwave and radio frequency circuits. Their low losses and low dielectric constant make them excellent in high frequency applications.
Aluminum oxide ceramic substrate has good insulation properties and thermal conductivity, and is suitable for the manufacture of power modules and high-frequency circuits. Their high thermal conductivity and high dielectric constant make them ideal for high power applications.
The above are the materials commonly used in manufacturing multi-cavity substrates and their characteristics. Selecting the appropriate material depends on specific application requirements, including circuit performance, thermal needs, operating environment and other factors. During the manufacturing process, the selection and use of materials should be based on actual needs
Proper matching is carried out to ensure the performance and reliability of multi-cavity substrates.
Who are the manufacturers of multi-cavity substrates?
In the field of manufacturing multi-cavity substrates, there are many professional manufacturers who have advanced technology and rich experience to provide customers with customized solutions. The following is an introduction from one of the representative manufacturers:
Our company is a manufacturer with a good reputation in the field of multi-cavity substrate manufacturing. We have advanced production equipment and a professional technical team, dedicated to providing customers with high-quality multi-cavity substrate solutions.
Our company has an experienced technical team with deep professional knowledge and rich manufacturing experience. We continuously introduce the latest manufacturing technology and conduct continuous technological innovation to meet the changing needs of our customers.
The company can provide customized multi-cavity substrate solutions according to customers’ specific needs. Whether designing complex circuit layouts or special manufacturing requirements, we are able to provide customers with high-performance multi-cavity substrate products that meet their needs.
As a professional multi-cavity substrate manufacturer, our company always puts quality first. We strictly implement a quality management system in accordance with international standards to ensure that each batch of products can meet customer requirements and provide long-term after-sales technical support.
The company focuses on communication and cooperation with customers, and always takes customer satisfaction as the ultimate goal. We provide timely response, professional technical support and customized solutions to provide customers with a full range of services to ensure that customer needs are met in a timely manner.
As a member of the multi-cavity substrate manufacturing field, our company will continue to adhere to the principles of quality first and customer first, continuously improve product quality and service levels, and provide customers with better multi-cavity substrate products and solutions.
What are the five characteristics of great customer service?
When it comes to a quality multi-cavity substrate manufacturer, the quality of its customer service is paramount. Here are five key characteristics to ensure quality customer service:
Prompt response to customer needs: A quality manufacturer should be able to respond quickly to customer inquiries, suggestions or complaints. Whether by email, phone, or online chat, timely responses convey the importance of customer needs and establish efficient communication channels.
Professional technical support: Manufacturing multi-cavity substrates involves complex processes and technologies, and customers may encounter various technical problems or challenges. A high-quality manufacturer should be equipped with a professional technical team that can provide customers with accurate and professional technical support and solutions to help customers overcome various technical problems.
Customized solutions: Different customers may have different needs and requirements, and a quality manufacturer should be able to provide customized solutions based on the customer’s specific needs. By in-depth understanding of customers’ needs and combining their own technology and resources, manufacturers can tailor multi-cavity substrate products to meet their needs, thereby improving customer satisfaction.
Transparent communication: Establishing a transparent and good communication mechanism is crucial to ensuring the quality of customer service. Manufacturers should provide customers with project progress, production status and quality control information in a timely manner to ensure that customers always know the latest status of the project and can make timely feedback and adjustments.
Ongoing after-sales support: A quality manufacturer should provide ongoing after-sales support services to its customers. Whether it is technical support, quality assurance or after-sales maintenance after product delivery, manufacturers should always keep in touch with customers and provide customers with necessary support and assistance to ensure customer satisfaction and trust.
To sum up, a high-quality multi-cavity substrate manufacturer should have five key characteristics: timely response to customer needs, professional technical support, customized solutions, transparent communication and continuous after-sales support. By continuously improving customer service quality, manufacturers can enhance customer satisfaction and loyalty, thereby gaining more market competitive advantages.
What are the answers to common multi-cavity substrate design and manufacturing questions?
What are the common challenges in designing multi-cavity substrates?
Designing multi-cavity substrates presents several challenges, including ensuring signal integrity between cavities, managing thermal dissipation, and optimizing the layout for efficient manufacturing. Addressing these challenges requires careful consideration of routing, placement of components, and thermal management techniques.
How can signal integrity be maintained in multi-cavity substrate designs?
Signal integrity in multi-cavity substrates can be maintained through techniques such as controlled impedance routing, minimizing signal crosstalk between cavities, and employing ground planes and signal layers to provide shielding and reduce interference.
What strategies can be employed to manage thermal dissipation in multi-cavity substrates?
Effective thermal management in multi-cavity substrates involves optimizing the layout to ensure efficient heat transfer, utilizing thermal vias to dissipate heat from components to outer layers or heat sinks, and selecting materials with high thermal conductivity.
What considerations should be taken into account for manufacturing multi-cavity substrates?
Manufacturing multi-cavity substrates requires attention to detail in processes such as cavity formation, layer alignment, and component placement. Ensuring consistency in etching, drilling, and plating processes is crucial to maintaining quality and reliability.
How can the reliability of multi-cavity substrate designs be ensured?
Reliability in multi-cavity substrate designs can be ensured through thorough testing and validation, including electrical testing, thermal cycling, and environmental testing. Additionally, adherence to industry standards and best practices is essential for achieving reliability.