Multi Cavity PCB Manufacturing.Multi cavity PCB manufacturing refers to the process of creating printed circuit boards with multiple cavities or cutouts within a single board. This advanced technique enables the integration of diverse components and functionalities into a compact space, optimizing electronic device design. By accommodating various modules and components within the PCB, it enhances functionality while reducing overall size. This approach is pivotal in industries demanding high-density electronics, such as telecommunications, automotive, and medical devices. Multi cavity PCB manufacturing involves intricate routing, precise drilling, and meticulous layering to ensure seamless integration and optimal performance of electronic systems.
In the electronics world, printed circuit boards (PCBs) serve as the backbone of countless devices, enabling connectivity and functionality. As technology continues to advance, the demand for PCBs with enhanced efficiency, performance, and compactness continues to increase. A notable solution to meet one of these evolving needs is the adoption of multi-cavity PCB manufacturing processes.
What is a multi-cavity PCB?
Multi-cavity PCB, that is, multi-cavity printed circuit board, is a design that integrates multiple circuit cavities on the circuit board. Traditional printed circuit boards tend to be single-chamber designs, while multi-cavity PCBs provide greater flexibility and advantages in the layout and performance of electronic devices by integrating multiple cavities on a single board.
In multi-cavity PCBs, different circuits can be separated into their own cavities to avoid interference between circuits. This design not only improves the isolation between circuits, but also effectively reduces signal interference, thereby improving the performance and stability of the entire electronic device. In addition, multi-cavity PCB can also achieve a more compact design, save space and improve equipment integration.
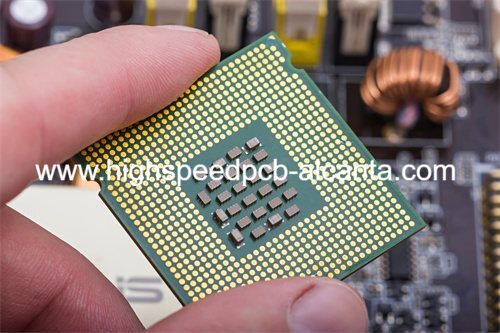
Multi Cavity PCB Manufacturing
Multi-cavity PCB is also unique in its wide range of applications. It is suitable for various types of electronic equipment, including but not limited to communication equipment, medical equipment, automotive electronics, industrial control systems, etc. By integrating multiple circuit chambers on one board, multi-cavity PCB provides highly customized solutions for electronic equipment in different industries, meeting the needs of different application scenarios.
Overall, the design and manufacturing of multi-cavity PCBs represents an important advancement in the field of electronics. It not only improves the performance and stability of electronic devices, but also provides more flexible and efficient solutions for applications in various industries. plan.
How to design a multi-cavity PCB?
Designing a multi-cavity PCB is a complex and sophisticated job that involves the application of multiple techniques and tools to ensure effective layout of electronic components and minimal signal interference. The key points of designing a multi-cavity PCB will be discussed in detail below:
First of all, designing multi-cavity PCB requires skilled use of PCB design software, such as Altium Designer, Cadence Allegro, etc. These software have powerful placement and routing capabilities that can help engineers effectively arrange the layout of electronic components in different cavities and optimize signal paths, thereby reducing the risk of signal interference.
Second, engineers need to consider the spatial layout and connections between the various chambers. By rationally planning the location and interconnection of electronic components, cross interference and electromagnetic interference on the circuit board can be minimized and stable signal transmission ensured.
In addition, for high-frequency circuits and sensitive circuits, designers need to pay special attention to the layout of ground wires and power supplies to reduce crosstalk between power lines and signal lines, thereby ensuring the stability and reliability of the circuit.
When designing multi-cavity PCBs, engineers should also consider thermal management considerations. By rationally arranging the location of heat dissipation components and enhancing heat dissipation design, the operating temperature of electronic components can be effectively reduced and the performance and reliability of the system can be improved.
In addition, designers also need to fully consider PCB manufacturing and assembly requirements. Taking manufacturing and assembly requirements into consideration at the design stage can greatly simplify the subsequent production process, improve manufacturing efficiency and reduce costs.
In summary, designing multi-cavity PCBs requires a combination of techniques and tools to ensure effective layout of electronic components and minimal signal interference. The high performance and reliability of multi-cavity PCBs can only be achieved through careful planning and design.
What are the advantages of multi-cavity PCB manufacturing?
In the field of electronic design and manufacturing, multi-cavity PCB manufacturing technology brings many significant advantages, making it the preferred solution for many industries. Compared with traditional single-chamber designs, multi-cavity PCBs have significant improvements in performance, efficiency and flexibility.
First of all, one of the most significant advantages of multi-cavity PCB is the optimization of space. By consolidating multiple circuit cavities into a single board, multi-cavity PCBs enable higher circuit density to accommodate more components and functionality on the same size board. This compact design not only makes the device lighter and more compact, but also helps reduce product volume and meet the demand for miniaturization and portability.
Second, multi-cavity PCB designs can significantly improve performance. Due to the isolation between various circuit chambers, multi-cavity PCB can effectively reduce signal interference and crosstalk problems. This optimized layout helps ensure stability and reliability between individual circuits, thereby improving overall performance and product quality. In addition, multi-cavity PCB can also realize the optimized layout of power supply and signal lines, further improving the efficiency and response speed of the circuit.
In addition to this, multi-cavity PCB manufacturing is cost-effective and flexible. Although it may require some investment in design and manufacturing, multi-cavity PCBs can achieve long-term cost savings by minimizing additional components and assembly processes. In addition, the design of multi-cavity PCB can be customized according to specific application requirements, providing personalized solutions for different industries and application scenarios.
To sum up, multi-cavity PCB manufacturing technology is of great significance in the field of modern electronics, and its advantages are obvious. By optimizing space utilization, improving performance and flexibility, multi-cavity PCB brings new possibilities to the design and manufacturing of various electronic devices, promoting the progress and development of the industry.
What is the manufacturing process of multi-cavity PCB?
The process of manufacturing multi-cavity PCBs involves a series of precise steps designed to ensure the quality and performance of the final product. The following is a typical process for manufacturing multi-cavity PCB and its quality control measures:
Design Verification: First, the manufacturing process begins with the verification of the PCB design. This stage ensures that the design complies with specifications and meets the customer’s needs. Design verification includes verifying component layout, signal routing, and chamber placement to ensure optimal performance and signal integrity.
Material preparation: Next, select the appropriate substrate material based on the design specifications. Commonly used substrate materials include FR-4 fiberglass composites and flexible polyimide (PI) materials. At this stage, materials must undergo rigorous inspection to ensure their quality and consistency.
Graphics Conversion: PCB design files are converted into production graphics that can be used for manufacturing. This includes converting design data into Gerber files to facilitate subsequent graphics imaging and processing.
Image processing: Gerber files undergo graphic imaging processing, and the circuit pattern is transferred to a substrate covered with photosensitive material through photolithography or laser irradiation.
Chemical Etching: The uncovered portions of the PCB will be removed by chemical etching to form the pattern of the circuit board. This process requires strict control of time and chemical concentration to ensure accuracy and consistency.
Drilling: Drilling holes in a circuit board for mounting electronic components and connecting circuits. The drilling process requires high-precision drilling machines and drill bits to ensure accuracy of hole diameter and location.
Surface treatment: The PCB surface may require surface treatment, such as metal spraying, tin spraying, or lead spraying, to improve soldering performance and corrosion protection.
Component mounting: The surface-treated PCB will be transferred to the automated component mounting line. Here, electronic components will be mounted precisely to their designated locations and secured to the PCB via soldering or other connection techniques.
Quality Control and Testing: Once manufactured, each multi-cavity PCB goes through strict quality control and testing procedures. This includes steps such as visual inspection, soldering quality inspection, electrical connectivity testing and functional testing to ensure each PCB meets specifications and achieves expected performance levels.
Through the above steps, the process of manufacturing multi-cavity PCB not only ensures production efficiency and accuracy, but also ensures the quality and reliability of the final product. Manufacturers must strictly follow each step and continuously improve their manufacturing processes to meet changing market demands and customer expectations.
What materials are used in multi-cavity PCBs?
When manufacturing multi-cavity PCBs, choosing the right materials is crucial because the materials not only affect the performance and reliability of the PCB, but also directly affect the cost and complexity of the overall design. The following are some common materials used in multi-cavity PCBs and their characteristics and effects:
Commonly used substrate materials include FR-4 (glass fiber reinforced epoxy resin), high TG FR-4, metal substrates, etc. FR-4 is the most common choice, offering good insulation properties, mechanical strength, and heat resistance.
Selecting the appropriate substrate material can affect the thermal stability, mechanical strength and chemical resistance of the PCB.
Copper cladding is a commonly used conductive layer material in PCB manufacturing. Common thicknesses include 1oz, 2oz, 3oz, etc. Thicker copper pours can be used to enhance the PCB’s thermal performance and current carrying capabilities.
The thickness and performance of copper cladding directly affect the conductive performance and thermal management capabilities of PCB.
Surface treatment materials such as HASL (tin-lead dip coating), ENIG (electroplating gold), OSP (organic protective film), etc. are used to protect the PCB pads and improve the welding quality.
Different surface treatment methods are suitable for different application scenarios and requirements. Choosing the appropriate surface treatment can improve the solderability and corrosion resistance of PCB.
In some special applications, such as high frequency, high speed, high temperature and other scenarios, special materials such as PTFE (polytetrafluoroethylene), Rogers materials, etc. may be required.
These special materials have better dielectric properties, low losses, higher frequency response and other characteristics, and are suitable for specific electronic devices and systems.
Choosing the right materials is critical to the performance and reliability of multi-cavity PCBs. Reasonable material selection can improve the working stability, anti-interference ability and lifespan of PCB, while reducing manufacturing costs and maintenance costs. During the design phase, engineers should select the most suitable materials based on specific application requirements and performance indicators to ensure that the final product can meet customer needs and achieve expected performance levels.
Who are the leading multi-cavity PCB manufacturers?
In today’s highly competitive PCB manufacturing market, finding a leading multi-cavity PCB manufacturer is crucial. These manufacturers not only possess advanced technology and facilities, but also have rich experience and good reputation. As a renowned electronics manufacturing company, we are proud to be one of the leaders in multi-cavity PCB manufacturing.
Our success is inseparable from our professional team and advanced technology. We have a team of experienced engineers who are proficient in all aspects of multi-cavity PCB design and manufacturing. They constantly pursue innovation and are committed to providing customers with the highest quality solutions. In addition, we invest in state-of-the-art production equipment and process technology to ensure the highest levels of product quality and production efficiency.
As a comprehensive electronics manufacturer, we have complete production capabilities covering the entire process from PCB design to assembly and testing. Our manufacturing facilities are equipped with state-of-the-art equipment capable of fulfilling orders of all sizes and complexity. Whether it is small batch customization or large-scale mass production, we are able to meet customer requirements in an efficient and reliable manner.
Quality is always at the core of what we do. We adopt a strict quality management system and strictly control every aspect from raw material procurement to production process. Our quality team performs rigorous inspection and testing procedures to ensure that each multi-cavity PCB meets customer specifications and standards.
We always put our customers first and strive to meet their needs and exceed their expectations. We have established long-term and stable cooperative relationships with our customers, providing them with customized solutions and personalized services. No matter what kind of multi-cavity PCB our customers need, we are able to flexibly adjust our production schedule to best meet their needs.
Over the years, we have actively participated in industry exchanges and exhibitions, and have established good cooperative relationships with experts and customers in the same industry. Our products and services are highly recognized and have won widespread praise and praise. We will continue to strive to continuously improve our own strength and competitiveness and provide customers with better multi-cavity PCB products and services.
When choosing a multi-cavity PCB manufacturer, we firmly believe that our professional team, advanced technology, comprehensive production capabilities, strict quality control, customer orientation and good reputation will bring you a satisfactory experience and quality products.
How to provide excellent customer service?
In the multi-cavity PCB manufacturing industry, excellent customer service is a key factor in ensuring customer satisfaction and business success. A great multi-cavity PCB manufacturer should have the following customer service traits:
Prompt Response: Excellent customer service starts with prompt response. Manufacturers should ensure that they can respond quickly when customers have questions or needs, providing necessary support and advice.
Clear communication: Clear and effective communication is key to building good customer relationships. Manufacturers should maintain close contact with customers to provide timely updates on project progress, answer questions, and negotiate any changes or adjustments with customers.
Technical expertise: Customers want to be able to work with a team that has specialized knowledge and experience. Manufacturers should have strong technical expertise and be able to provide valuable advice and solutions to customers.
Reliability: Customers need partners they can trust. Manufacturers should prioritize reliability, keep their promises, deliver products on time, and ensure product quality meets expected standards.
Personalized service: Every customer’s needs are likely to be different, so manufacturers should be able to provide personalized service, tailoring solutions to the customer’s specific requirements to meet their unique needs and expectations.
By actively implementing the above customer service attributes and satisfaction guarantee measures, an excellent multi-cavity PCB manufacturer can establish a solid cooperative relationship with its customers and jointly achieve business success and development.
FAQs
What are the primary applications of Multi-Cavity PCBs?
Multi-Cavity PCBs find extensive applications across various industries due to their compact design and enhanced functionality. They are commonly used in telecommunications equipment, automotive electronics, aerospace systems, consumer electronics such as smartphones and tablets, and medical devices. The ability to integrate multiple circuit cavities into a single board makes Multi-Cavity PCBs versatile and suitable for diverse electronic applications.
How does Multi-Cavity PCB manufacturing differ from traditional PCB fabrication?
Traditional PCB fabrication typically involves the production of single-layer or double-layer boards with a single circuit. In contrast, Multi-Cavity PCB manufacturing integrates multiple circuit cavities within a single board. This allows for more compact designs, reduced space requirements, and improved performance. Additionally, Multi-Cavity PCBs require specialized design and manufacturing techniques to ensure optimal layout, signal integrity, and thermal management across multiple cavities.
What factors should be considered when designing Multi-Cavity PCBs?
Designing Multi-Cavity PCBs requires careful consideration of various factors to ensure optimal performance and reliability. Key considerations include component placement to minimize signal interference, routing of high-speed signals to minimize transmission line effects, thermal management to dissipate heat efficiently, compatibility with assembly processes, and adherence to industry standards and regulations. Additionally, designers must assess the specific requirements of the application and optimize the PCB layout accordingly.
What materials are commonly used in Multi-Cavity PCBs?
Multi-Cavity PCBs utilize a range of materials selected based on their electrical properties, mechanical strength, thermal conductivity, and compatibility with manufacturing processes. Common substrate materials include FR-4 epoxy fiberglass, which offers excellent electrical insulation and mechanical stability. For flexible PCBs, polyimide (PI) substrates are often preferred due to their flexibility and high-temperature resistance. Advanced laminates such as Rogers Corporation’s RO4000 series are used for specialized applications requiring high-frequency performance and low dielectric loss.
How do Multi-Cavity PCBs contribute to space optimization and cost efficiency?
Multi-Cavity PCBs enable significant space savings by integrating multiple circuit cavities into a single board, eliminating the need for separate boards or additional components. This consolidation of circuits reduces the overall size and complexity of electronic devices, resulting in space-efficient designs. Additionally, Multi-Cavity PCB manufacturing offers cost efficiencies by minimizing material wastage, streamlining production processes, and reducing assembly time and labor costs.