Module Substates Manufacturer, Small size module substrates with Ultra-small gap. The finished substrate surface has high smoothness. We are a professional substrate supplier.
Module substrates, also referred to as packaging substrates, are vital components in electronic devices, providing the foundational structure for supporting and connecting diverse electronic elements. They fulfill critical roles including signal transmission facilitation, heat dissipation, mechanical support, and electromagnetic shielding. Across the design and manufacturing stages of electronic products, module substrates wield significant influence, directly affecting the performance, reliability, and cost of the final product.
These substrates carry diverse electronic components, including chips, resistors, and capacitors, connecting them through conductive elements like copper foil and lines to form a complete circuit. This electrical connectivity ensures effective communication between components and influences the overall efficiency and stability of the electronic system.
Beyond electrical connections, module substrates contribute to mechanical support within the product. They furnish a robust structural foundation for various components, guaranteeing the stability and durability of the entire system. Simultaneously, module substrates facilitate heat dissipation, efficiently conducting the heat generated by components to the external environment and maintaining a stable temperature during prolonged operation.
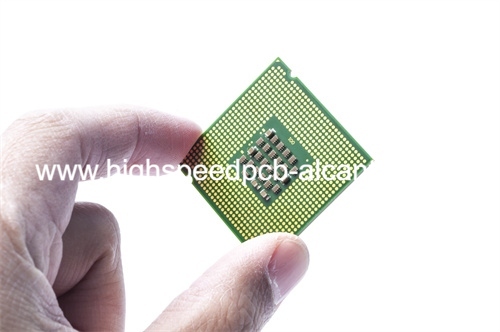
Module Substates Manufacturer
Module substrates, also referred to as packaging substrates, are vital components in electronic devices, providing the foundational structure for supporting and connecting diverse electronic elements. They fulfill critical roles including signal transmission facilitation, heat dissipation, mechanical support, and electromagnetic shielding. Across the design and manufacturing stages of electronic products, module substrates wield significant influence, directly affecting the performance, reliability, and cost of the final product.
What types of module substrates are there?
In the field of electronic manufacturing, the diverse types of module substrates provide engineers and designers with a wealth of choices to meet different product needs and application scenarios.
Module substrates come in various types, each tailored to specific application needs. Rigid substrates, such as fiberglass-reinforced epoxy or polyimide, offer high mechanical strength and stability, ideal for products like computer motherboards and industrial equipment. Flexible substrates, made of materials like polyester or polyimide film, prioritize flexibility, suiting applications like wearable devices and flexible displays. Combined substrates merge the stability of rigid types with the bendability of flexible ones, commonly seen in foldable electronics. Specialized substrates, like metal or ceramic, cater to unique needs such as high-power LED lighting. When selecting substrates, designers weigh factors like functionality, size, and cost to ensure optimal support for product performance and reliability. Understanding these options empowers designers to leverage substrate advantages effectively, driving successful product development.
What are the advantages of module substrates compared to other boards?
In modern electronic manufacturing, module substrates have significant advantages over other boards, which is why many electronic products choose to use them. Below we will delve into the advantages of module substrates over other boards and why these advantages are favored by the industry.
The module substrate offers enhanced flexibility in design, enabling higher integration and density compared to traditional rigid or flexible substrates. Its precise design allows for the integration of more components into a smaller space, facilitating the implementation of complex circuit functions.
Utilizing advanced materials and manufacturing processes, the module substrate boasts excellent electrical performance and signal transmission characteristics. This ensures stable and reliable performance, particularly in high-frequency and high-speed transmission scenarios, meeting the stringent data transmission requirements of modern electronic products.
Emphasis is placed on optimizing heat dissipation and mechanical strength in the module substrate design. Through strategic layout and material selection, effective heat conduction and dispersion are achieved, maintaining stable temperatures for electronic components during prolonged operation. Additionally, the substrate exhibits ample mechanical strength to withstand external environmental factors such as vibration and impact, ensuring product reliability and durability.
Compared to traditional substrates, the design and production process of module substrates offer greater flexibility. Manufacturers can tailor designs to meet customer specifications and adjust production processes accordingly, making module substrates well-suited for customized and innovative products.
To sum up, module substrates have many advantages over other boards, including high integration and density, superior electrical performance and signal transmission characteristics, optimized heat dissipation performance and mechanical strength, and flexible design and production processes. It is these advantages that make module substrates the first choice for many electronic products, injecting new vitality into the development of modern electronic manufacturing.
How are module substrates made?
The manufacture of module substrates is a complex process involving several critical stages, each crucial for the quality and performance of the final product. It begins with design and layout, where circuit connections, wiring paths, and component placement are determined using professional design software. Material selection is vital, with options like FR-4 fiberglass or polyimide, requiring pre-treatment for contaminants and surface adhesion.
Once materials are prepared, processing begins, encompassing printing, etching, deposition, and soldering, with PCBs often used for circuit patterns and component layout. Throughout production, rigorous inspection and testing are essential, covering visual, electrical, and solder joint reliability tests to detect and rectify any defects promptly.
In summary, manufacturing module substrates demands coordination across design, materials, processes, and quality control. Only through meticulous design and strict production protocols can reliable, high-performance module substrates be achieved, providing a dependable foundation for electronic product manufacturing.
What are the application fields of module substrates?
In the field of communications, module substrates play a vital role. From smartphones to communication base stations, almost all communication equipment requires high-performance module substrates to support their functions. The application of module substrates in communication equipment not only provides circuit connections, but also includes key functions such as signal processing, data transmission and network connections.
Module substrates play a crucial role in various industries such as automotive electronics, industrial control and automation, and medical equipment. In automotive settings, they are vital for supporting electronic control units (ECUs) responsible for functions like engine control, in-vehicle entertainment, and safety systems. This underscores the importance of stability and reliability in their design and implementation.Similarly, in industrial control and automation, these substrates are essential for control systems in factory automation, robot control, and intelligent warehousing, ensuring high performance for real-time data processing. In the medical equipment field, module substrates play a crucial role in devices such as electrocardiographs, blood pressure monitors, and medical imaging equipment, supporting functions like data acquisition and signal processing, with reliability and performance directly impacting patient safety.
Beyond these major sectors, module substrates are also integral in consumer electronics, aerospace, energy, and various other fields. Their high-performance capabilities are essential for diverse application scenarios across almost all electronic products and systems.
In conclusion, module substrates play a pivotal role in diverse industries, providing crucial support for the development of modern science and technology. As technology advances and application scenarios continue to expand, the prospects for module substrates are poised to broaden further.
How to choose a suitable module substrate manufacturer?
When selecting the appropriate manufacturer for module substrates, it’s essential to consider various factors to ensure the chosen supplier can meet your requirements and offer optimal service. Here are the crucial aspects to ponder:
Initiate an appraisal of the supplier’s production capabilities and expertise initially. Ascertain whether they possess ample manufacturing capacity to fulfill your orders and possess sufficient experience in handling analogous projects. Production capacity and proficiency are crucial in ensuring the timely delivery of top-notch products.
The efficacy of the supplier’s quality management system holds utmost importance. Confirm their adherence to stringent quality control procedures and their ability to deliver products that meet established standards. This encompasses quality inspections and testing throughout the manufacturing process, coupled with the capacity to consistently improve product quality.
Additionally, the level of technical support and service rendered by the supplier is pivotal. Ensure they can provide swift and efficient technical assistance, addressing any challenges encountered during manufacturing. Exceptional customer service ensures the punctual fulfillment of your requisites and encourages seamless communication and collaboration.
Lastly, factor in cost-effectiveness as a significant criterion in supplier selection. Evaluate whether the supplier’s pricing is reasonable and confirm that you obtain high-quality products while keeping costs within acceptable limits. Beyond the unit price, consider aspects such as production lead times and delivery schedules to accurately assess the total cost.
In summary, the process of selecting a suitable module substrate manufacturer entails a comprehensive evaluation of factors such as production capacity, quality management systems, technical support, and cost-effectiveness. Through meticulous assessment and comparison of various vendors, you can pinpoint the ideal partner to meet the requirements of your company.
What is the quotation for module substrate?
Determining the pricing of module substrates is a multifaceted and pivotal task. Manufacturers must weigh numerous factors to ensure their quotations are both reasonable and competitive. Below are several pivotal elements influencing module substrate quotations:
Material Expenses: The cost of module substrates is contingent upon material expenditures. Prices for different substrate materials fluctuate significantly, influenced by market dynamics such as supply and demand. While high-performance materials typically command higher prices, they also offer superior functionality and dependability.
Production Processes: Manufacturers must factor in the array of procedures involved in production, encompassing activities like printing, etching, and welding. Each process incurs its own expenses, with varying complexities contributing to price differentials. Employing high-precision, cutting-edge techniques often amplifies manufacturing costs.
Order quantity is also a crucial factor in pricing. Generally speaking, large-volume orders can enjoy lower unit prices because costs can be reduced through mass production. On the contrary, the unit price for small batch orders is usually higher.
If customers have special technical requirements, such as high frequency, high speed or high density requirements, these may lead to additional process adjustments and increased costs. Therefore, technical requirements will also have an impact on the final quotation.
Some clients may necessitate prompt delivery, which might entail overtime or accelerated processing, consequently escalating manufacturing expenses. Hence, the timeframe for delivery also stands as a crucial determinant impacting the pricing estimate.
In conclusion, devising a quotation for module substrates entails a multifaceted process influenced by various factors. Manufacturers must holistically evaluate elements such as material expenses, manufacturing procedures, volume of orders, technical specifications, and delivery deadlines to devise a judicious pricing strategy that caters to customer requirements while ensuring optimal profit maximization.
Frequently Asked Questions
How does the design of module substrates impact product performance?
The design of module substrates plays a crucial role in determining product performance. Factors such as layout, wiring, and material selection directly influence signal transmission, thermal dissipation, and mechanical stability. A well-designed module substrate can enhance product reliability and functionality.
What advantages do Module Substrates hold over other board types?
Module Substrates provide higher integration density, better electrical performance, superior heat dissipation, and increased mechanical strength. These advantages make them a preferred choice for many electronic products.
How do module substrates differ from other boards?
Module substrates offer higher integration and density, better electrical performance and signal transmission, improved thermal management, and mechanical strength compared to other boards, making them preferred choices for various electronic applications.
How does the design of module substrates affect product performance?
The design of module substrates plays a crucial role in determining product performance. Factors such as layout, wiring, and material selection directly impact signal transmission, thermal dissipation, and mechanical stability. Optimal design practices ensure efficient functionality and reliability of electronic products.
How to choose the right module substrate manufacturer?
Selecting the appropriate module substrate manufacturer requires careful consideration of several factors. Assess the manufacturer’s production capabilities, quality management systems, technical support, and service levels. Additionally, evaluate their track record and client testimonials to ensure reliability and compatibility with your project requirements.
How does the design of module substrates affect product performance?
The design of module substrates plays a crucial role in determining product performance. Factors such as layout, wiring, and material selection directly impact signal transmission, thermal management, and mechanical stability. A well-designed module substrate can enhance overall product reliability and functionality.