A Military PCB Manufacturer specializes in crafting circuit boards tailored for stringent military applications, ensuring robustness and reliability in extreme conditions. With a focus on precision engineering, they employ cutting-edge technologies to produce boards that withstand harsh environments, electromagnetic interference, and mechanical stress. These manufacturers adhere to rigorous quality standards and security protocols to meet the exacting demands of defense systems, aerospace projects, and other critical missions. Their expertise lies in developing circuitry that guarantees optimal performance, resilience, and longevity, essential for safeguarding sensitive military operations worldwide.
In modern military equipment, electronic components play an increasingly critical role. And one of the most important components is the printed circuit board (PCB). As the foundation for connecting and supporting electronic components, the quality and design of PCBs are critical to the performance of military equipment. Military PCB manufacturers play a key role in ensuring the performance and reliability of military equipment. They provide critical support to the military industry through precision design, high-quality materials and rigorous manufacturing processes, ensuring the reliability and performance of their equipment on the battlefield. In this article, we will delve into the importance of military PCB manufacturers and their critical role in military equipment.
What is a military PCB?
In the manufacturing of modern military equipment, printed circuit boards (PCBs) are regarded as one of the core components of electronic systems. Military PCBs are printed circuit boards designed and manufactured specifically for military applications. They play a vital role in military equipment, with almost every aspect from missile systems to communications equipment relying on their stability and reliability.
There are significant differences in design, material selection, and manufacturing processes between military PCBs and traditional commercial PCBs. Since military equipment often needs to operate in extreme environments, such as high temperature, high pressure, vibration and electromagnetic interference, the design of military PCBs must take these challenges into account and ensure that their performance is not affected.
Military PCB design requirements are often more stringent and require consideration of board reliability, durability, and safety. In some cases, military PCBs even need to have protective properties to protect the internal electronic components from external interference and attacks.
Additionally, military PCBs are often required to meet specific military standards and certification requirements, such as MIL-STD-810G, MIL-PRF-31032, etc. These standards specify various performance indicators and test methods for PCBs in military environments to ensure that they meet the requirements of military applications.
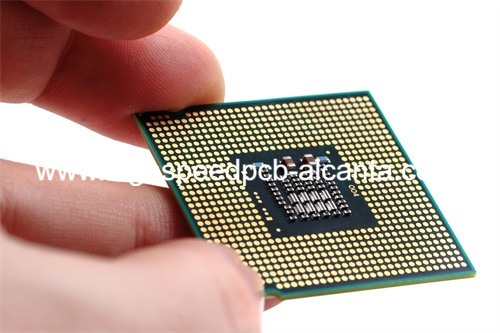
Military PCB Manufacturer
In general, a military PCB is a printed circuit board that is specially designed and manufactured to meet the needs of military applications. They play a key role in modern military equipment, providing the military with necessary technical support and strategic advantages.
Military PCB design Reference Guide.
In the military field, PCB design is crucial because it directly affects the performance and reliability of military equipment. Military PCB designs must adhere to strict standards and guidelines to ensure reliability and stability in extreme environments. Here are some design guidelines to help military PCB manufacturers consider performance under various harsh conditions during the design phase:
Consider environmental factors
Military equipment is often exposed to harsh environmental conditions such as high temperature, high pressure, humidity and vibration. Therefore, the impact of these factors on electronic components and circuits must be taken into account when designing PCBs. Choose materials that are resistant to high temperatures and corrosion, and take effective heat dissipation measures to ensure the stability of the PCB under extreme conditions.
Shock-resistant design
Military equipment often operates in environments subject to vibration or shock, so PCBs must be designed with these challenges in mind. Reduce the movement and damage of electronic components due to vibration through appropriate layout and fixation methods. In addition, choose materials with good mechanical strength and use appropriate buffering measures to improve the shock resistance of the PCB.
Electromagnetic Compatibility (EMC)
Military equipment often needs to operate in an environment with electromagnetic interference, so the design of PCB must take into account electromagnetic compatibility (EMC) requirements. Reduce interference and coupling between circuits through good wiring design, grounding planning and shielding measures. In addition, choose materials with good anti-interference capabilities and use appropriate filters and suppressors to ensure the stability of the PCB under electromagnetic interference.
Reliability test
After the design is completed, the PCB must be subjected to rigorous reliability testing to ensure that it meets military standards and specifications. These tests include environmental suitability testing, vibration and shock testing, EMC testing, etc. Through these tests, potential problems can be discovered and solved, improving the reliability and stability of the PCB.
The design of military PCBs is a complex and critical task that must take into account various environmental factors and challenges. By following strict design guidelines and conducting reliability testing, military PCB manufacturers can ensure the performance and reliability of their products under extreme conditions. This sophisticated design and manufacturing process provides critical support to the military industry, ensuring the smooth operation of its equipment on the battlefield.
What material is used in Military PCB?
In the military sector, PCB quality and stability are critical to the performance of the device. Therefore, military PCB manufacturers usually choose high-quality materials to ensure their reliability and durability under extreme conditions. Here are some common materials used in military PCBs:
R-4 epoxy fiberglass
FR-4 is a widely used substrate material composed of fiberglass and epoxy resin. It has excellent mechanical strength and heat resistance, and can maintain stability in high temperature environments. In addition, FR-4 material also has good corrosion resistance and can resist the erosion of chemical substances, making it suitable for military applications in various harsh environments.
Polyimide (PI)
Polyimide is a high-performance polymer material with excellent high temperature resistance and chemical stability. It has a very low coefficient of thermal expansion and can maintain dimensional stability under extreme temperatures, making it suitable for PCB designs in military equipment that need to withstand high-temperature environments.
Polyimide nitrile (PIA)
Similar to polyimide, polyimide nitrile is a high-performance polymer material with excellent heat resistance and chemical stability. Its mechanical strength and stiffness are very high, and it can maintain stability under harsh conditions, making it suitable for components in military PCBs that need to withstand high pressure and vibration.
These materials are widely used not only in the manufacturing of military PCBs, but also in other high-end electronic devices. Their excellent performance and stability provide important support for military equipment, ensuring its reliable operation at critical moments.
To sum up, military PCB manufacturers choose these high-quality materials not only to meet the stringent requirements of military applications, but also to ensure the stability and reliability of military equipment under various harsh conditions. The selection of these materials has been rigorously tested and verified, providing a reliable basis for the design and manufacturing of military PCBs.
What size are Military PCB?
Military PCB size plays a vital role in military applications. Their size can vary depending on the specific application needs. From small and compact boards to large and complex boards, different sizes of PCBs have their own unique uses and advantages.
Small PCB
In military applications, small PCBs are often used for assembly in missiles, aircraft, and other space-constrained equipment. These PCBs require compact designs and lightweight properties to fit into limited spaces and reduce the weight of the equipment. Despite their small size, small PCBs still host important functions such as control systems, sensor interfaces and data processing units.
Large PCB
As opposed to small PCBs, large PCBs also have their importance in the military field. They are commonly used in radar systems, communications equipment, and other complex electronic equipment. These PCBs may need to support multiple components, complex circuit layouts, and high-performance processing capabilities. Due to their larger size, they typically have higher complexity and more stringent design requirements.
Variety of sizes
Military PCB manufacturers must be able to flexibly respond to different size requirements. They need to design and manufacture suitable PCB sizes based on customer requirements and application scenarios. Some projects may require a small, customized PCB to meet specific space constraints and performance requirements, while other projects may require a larger, more complex PCB to support the operation of a multi-function system.
Military PCB dimensions vary based on specific application requirements. Whether they are small and compact boards or large and complex boards, they all play an irreplaceable role in military equipment. Military PCB manufacturers must be able to flexibly respond to different size requirements and ensure optimal levels of performance and reliability through sophisticated design and manufacturing processes.
The Manufacturer Process of Military PCB.
The manufacturing process of military PCBs is a complex and precise process involving multiple critical steps, each of which is crucial. The manufacturing process of military PCB is described in detail below.
Design and layout
The first step in manufacturing a military PCB is design and layout. This involves determining the functional and performance requirements of the PCB and translating them into an actual circuit layout. During this stage, engineers use CAD (computer-aided design) software to create a prototype of the PCB and ensure that it meets specifications and requirements.
Forming
Forming is the next critical step in manufacturing PCB boards. At this stage, the substrate material is processed into the desired shape and size. This may involve processes such as cutting, drilling and milling to ensure the board meets design specifications.
Chemical processing and gold plating
Next comes the chemical processing and gold plating steps. At this stage, the surface of the PCB is chemically treated to clean and prepare it to receive metal plating. The PCB surface is then electrochemically plated with a metal layer, usually copper. This step is key to ensuring that the PCB conducts electricity well.
Punch and print
Drilling and printing are one of the two critical steps in the PCB manufacturing process. During the drilling stage, the required connection holes are created on the PCB by drilling or laser drilling. Next, in the printing stage, the required circuit patterns and markings are printed on the PCB surface using printing technology.
Assemble
Assembly is another important step in PCB manufacturing. At this stage, electronic components are mounted onto the surface of the PCB and then connected to the PCB through methods such as soldering. This includes the installation of various components such as chips, resistors, and capacitors.
Test
The final step is testing. At this stage, the manufacturer conducts rigorous testing on the manufactured PCB to ensure its performance and reliability. This may include aspects such as electrical testing, functional testing and environmental testing.
Every manufacturing stage requires strict quality control to ensure the reliability and performance of the final product. Only PCBs that have undergone rigorous testing and verification can be considered part of qualified military equipment.
The Application area of Military PCB.
Military PCBs are widely used in various military equipment, and their high performance and reliability provide critical support for military operations. Here are some common application areas:
Communication Systems
Military communication systems require stable connections and efficient data transmission under extreme conditions. Military PCBs are used to manufacture a variety of communications equipment, including satellite communications terminals, RF transceivers, data links, and more. Their design must take into account factors such as immunity to interference, resistance to electromagnetic interference, and high-speed data processing.
Radar system
Radar plays a vital role in military reconnaissance, target tracking and navigation. Military PCBs are widely used to manufacture key components such as control units, signal processors, and antenna arrays in radar systems. These PCBs must have a high degree of accuracy and stability to ensure the accuracy and reliability of the radar system.
Navigation equipment
Military navigation equipment requires precise positioning and navigation capabilities to support the movement and actions of troops on the battlefield. Military PCBs play a key role in manufacturing GPS receivers, inertial navigation systems, autonomous driving devices, and more. They must be able to ensure accurate position information and stable navigation performance under various environmental conditions.
Missile system
Military missile systems require highly sophisticated control and navigation systems to ensure accurate target hitting and mission execution. Military PCB is used to manufacture key components such as missile control units, flight calculators, and attitude control systems. These PCBs must be able to operate stably at high speeds and in extreme environments to ensure the missile’s accuracy and reliability.
Overall, military PCBs play a vital role in various military equipment. Their high performance and reliability provide critical support for military operations and ensure the military’s superior position and combat capabilities on the battlefield.
What are the advantages of Military PCB?
In modern military equipment, military PCBs (Printed Circuit Boards) have significant advantages, making them an indispensable component. Compared with traditional connection methods, military PCBs incorporate advanced technologies and processes to provide critical support for military operations. Here are a few advantages of military PCBs:
Higher density
Military PCBs allow for high-density wiring, allowing electronic components to be placed more compactly on the board. This high-density design not only saves space, but also improves system performance and functionality.
Better electrical performance
Military PCB manufacturers use high-quality materials and advanced processes to ensure excellent electrical performance of the board. Characteristics such as low loss, low noise and high frequency response make military PCBs excellent in data transmission and signal processing.
Lower failure rate
Because military PCBs undergo rigorous design, manufacturing, and testing, their failure rates are far lower than traditional connection methods. This means that military equipment can operate stably for a long time under extreme conditions, improving combat efficiency and the safety of soldiers.
Easier maintenance
The modularity and disassembly of military PCBs makes maintenance easier. When a component fails, just replace the corresponding PCB board without having to perform tedious welding and connection work. This saves maintenance time and reduces maintenance costs.
To sum up, military PCBs have important advantages in modern military equipment. Its high density, excellent electrical performance, low failure rate and easy maintenance make it an indispensable key component in military operations. The continuous innovation and technological progress of military PCB manufacturers will continue to promote the development of military equipment and make greater contributions to national security and national defense.
FAQ
What is the life cycle of a military PCB?
The life cycle of a military PCB depends on its design, materials and conditions of use, but can typically last for many years. In military applications, PCBs undergo rigorous testing and quality control to ensure their long-term stable operation. However, as technology advances and needs change, sometimes upgrades or replacements may be necessary.
Can military PCBs be used in extreme environments?
Yes, military PCBs are designed and tested to operate reliably under extreme temperature, pressure, and vibration conditions. These PCBs use high-quality materials such as FR-4 epoxy fiberglass, polyimide (PI), and polyimide nitrile (PIA) for excellent high temperature resistance, corrosion resistance, and mechanical strength. In addition, military PCBs undergo rigorous testing to ensure their reliability under a variety of harsh conditions.
Is the manufacturing process for military PCBs complex?
Yes, the manufacturing process of military PCBs involves multiple complex steps including design, layout, molding, chemical processing, gold plating, drilling, printing, assembly and testing, etc. Each step requires strict quality control and technical expertise to ensure the performance and reliability of the final product. Manufacturers are usually equipped with advanced equipment and technology and follow international standards and industry best practices.
Do military PCBs require special licensing or certification?
Yes, military PCB manufacturing is often subject to specific licensing and certification requirements. These requirements may include defense sector accreditation, compliance with international standards and certification of quality management systems. Manufacturers must meet relevant standards and undergo rigorous audits and reviews to ensure that their products meet the requirements of the military industry.
How much does a military PCB cost?
The cost of military PCBs depends on several factors, including design complexity, material selection, manufacturing process, and quantity. Because military PCBs need to meet strict standards and requirements, their manufacturing costs are typically higher. However, these costs are often considered a reasonable investment when compared to the performance and reliability of the equipment.