Mixed Dielectric PCB Manufacturing.Mixed Dielectric PCB Manufacturing involves the fabrication of circuit boards using a combination of different dielectric materials. This advanced technique enables the creation of boards with varied electrical properties tailored to specific applications. By strategically incorporating materials like FR-4 and Rogers RO4000 series, it optimizes signal integrity, impedance control, and thermal management. Through precise layering and bonding processes, manufacturers ensure seamless integration of diverse dielectrics, fostering enhanced performance and reliability in electronic devices. This innovative approach revolutionizes PCB design, catering to the evolving demands of modern technologies with unparalleled efficiency and versatility.
Mixed media PCB (Printed Circuit Board) plays a vital role in modern electronic equipment. By combining the characteristics of different media, mixed media PCBs provide electronic designers with more flexible and diverse solutions. This article will delve into the design, manufacturing and cost aspects of mixed-media PCBs, aiming to provide readers with a comprehensive guide to help them better understand and apply knowledge in this area.
What is a mixed media PCB?
Mixed media PCB is a printed circuit board that combines different materials. By combining different media, it achieves the purpose of taking into account multiple performance requirements on a single circuit board. Traditional PCBs usually use a fixed material, such as FR4 (fiberglass reinforced epoxy), while mixed media PCBs incorporate different types of materials, such as FR4, Rogers, Isola, etc., to meet the electrical requirements of specific application scenarios. , mechanical and thermal requirements.
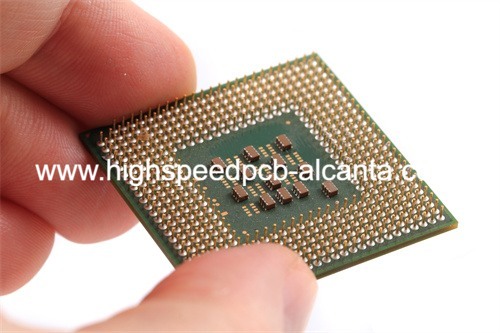
Mixed Dielectric PCB Manufacturing
The key to mixed-media PCBs is their ability to cleverly combine the properties of different materials. In traditional PCB manufacturing, the use of a single material may be subject to performance limitations. For example, in high-frequency, high-speed or high-temperature applications, conventional FR4 materials may not be able to meet the requirements. Mixed media PCBs layer different materials together to optimize electrical performance, mechanical strength, and thermal conductivity.
For example, for circuits that require high-frequency transmission, such as radio frequency (RF) or microwave (Microwave) applications, specialized materials such as Rogers or Isola may be more suitable because they have lower dielectric constants and losses, thereby reducing Signal attenuation. For applications that require higher mechanical strength, such as automotive electronic systems, traditional FR4 materials may be more suitable. By mixing different materials, mixed-media PCBs can achieve performance advantages in different application scenarios and meet a variety of complex design requirements.
The emergence of mixed-media PCBs allows designers to more flexibly select materials and optimize them according to the needs of specific application scenarios. During the design stage, they can select appropriate material combinations and perform stack-up designs based on factors such as circuit layout, signal transmission requirements, thermal management needs, etc. to achieve optimal performance and reliability. Therefore, mixed media PCB not only provides a wider range of applications, but also provides new possibilities for improving the performance of electronic products.
How to design a mixed media PCB?
The design of mixed-media PCBs is a precise and complex process that requires designers to comprehensively consider the characteristics, electrical performance and manufacturing processes of different materials. The following are the main steps of the mixed media PCB design process:
Determine application requirements: Designers first need to understand the specific fields and functional requirements of the circuit board. Different application scenarios may require different combinations of materials to achieve optimal performance.
Material Selection: Select appropriate mixed media materials based on application needs and design goals. Common materials include FR4, Rogers, Isola, etc., which have different properties such as dielectric constant, heat resistance, and mechanical strength.
Layer-up design: Take the layering of different materials into account during the design process. Reasonable stacking design can effectively control signal transmission and electromagnetic interference, and improve the performance and reliability of the circuit board.
Signal integrity analysis: Perform signal integrity analysis, including analysis of transmission line characteristic impedance matching, signal transmission delay and crosstalk. Ensure designs meet expected performance specifications through simulation and verification.
PCB layout design: Carry out PCB layout design based on circuit functions and layout requirements. Reasonable layout can reduce signal interference, improve heat dissipation, and simplify the manufacturing process.
Consider thermal management: For mixed media PCBs, the thermal conductivity properties of different materials vary greatly, so thermal management measures need to be considered, such as heat sinks, heat sinks, and thermal pads.
Impedance control: For circuits with high-speed signal transmission, special attention needs to be paid to impedance matching. By controlling the width of the transmission line and the distance between layers, the impedance matching of the signal is ensured and signal integrity is improved.
Design Rule Check (DRC): After completing the layout design, design rule check is performed to ensure that the design meets the requirements and standards of the manufacturing process and avoid potential manufacturing defects.
Prototyping and Testing: Prototype mixed media PCBs and undergo rigorous functional testing and performance verification. Based on the test results, adjust the design and make necessary optimizations.
To sum up, the design process of mixed media PCB involves multiple key steps, from material selection to layout design, to manufacturing and testing. Designers need to consider multiple factors and take corresponding measures to ensure the performance of the design. and reliability.
What is the manufacturing process of mixed media PCB?
The manufacturing process of mixed media PCB is a precise and complex process that requires strict control of each step to ensure the quality and performance of the final product. The manufacturing process of mixed media PCB will be introduced in detail below:
The first step in manufacturing a mixed media PCB is to prepare the required materials and create a layup design. Designers select different materials based on the requirements of the product and determine the structure and thickness of each layer. During the stack-up design process, factors such as electrical performance, thermal management, and mechanical strength need to be considered to ensure that the final product meets design specifications.
Once the stack-up structure is determined, the next step is the production of printed circuit layers. This involves the process of transferring circuit patterns to the PCB substrate surface through a photomask. In the manufacturing of mixed media PCBs, there can be interfacial adhesion issues between layers of different materials, so special attention needs to be paid to the bonding and consistency between materials during this step.
After completing the printed circuit layer, the next step is chemical etching. Chemical etching removes unnecessary copper layers to form circuit patterns by immersing the PCB in an etching solution. In the manufacturing of mixed-media PCBs, due to the presence of different materials, the etching solution formula and soaking time may need to be adjusted to ensure that the interface between the layers is not damaged.
After etching is complete, the PCB needs to be thoroughly cleaned to remove residue and dirt generated during the etching process. The cleaning process is a key step to ensure that the PCB surface is clean for subsequent processing and coating work.
The next stage in PCB manufacturing is drilling and plating. Drilling is done to create connection points and fixing holes on the PCB for mounting components and connecting wires. In the manufacturing of mixed media PCBs, due to different materials, drilling may require different types of drill bits and drilling parameters to ensure the quality and consistency of the hole walls.
After drilling is completed, the PCB needs to be electroplated to increase the conductivity of the surface. Electroplating is a process in which a PCB is immersed in an electrolytic bath containing a metal salt solution and an electric current is applied to deposit metal on the surface of the PCB. This step can improve the corrosion resistance and solderability of the PCB and ensure reliable connection of components.
The final stage is PCB assembly and testing. At this stage, components are mounted on the PCB and soldered and connected. Functional testing and performance evaluation follow to ensure the PCB meets design specifications and customer requirements.
The manufacturing process for mixed media PCBs is a complex and sophisticated process that requires close collaboration between designers, engineers and manufacturers. By strictly controlling each step and using advanced processes and equipment, high-quality and high-performance mixed-media PCBs can be produced, providing strong support for the development and innovation of electronic products.
How much does a mixed media PCB cost?
When discussing the cost of mixed-media PCBs, we need to consider multiple factors, including material costs, manufacturing processes, design complexity, and market competition. How to evaluate the manufacturing costs of mixed media PCBs is explained in detail below.
First, material cost is one of the major factors affecting mixed media PCB manufacturing costs. Different PCB materials, such as FR4, Rogers, Isola, etc., have different costs. Generally speaking, high-performance materials cost more, while conventional materials cost relatively less. Therefore, when selecting PCB materials, performance and cost should be balanced based on project needs.
Secondly, the manufacturing process also affects the cost of mixed media PCB. Complex manufacturing processes often require more labor and equipment investment, thereby increasing manufacturing costs. For example, special processes for mixed-media PCBs, such as stack-up design, special material handling, etc., may increase manufacturing costs. Therefore, when formulating the manufacturing process, efforts should be made to optimize the process and reduce costs.
In addition, design complexity is also one of the factors affecting the cost of mixed media PCB. Complex designs may require more layers, greater precision, and more processes, which increases manufacturing costs. Therefore, when designing PCB, the design should be simplified as much as possible to avoid unnecessary complexity to reduce costs.
Finally, market competition will also affect the manufacturing cost of mixed media PCBs. In a highly competitive market environment, manufacturers may adopt price reduction strategies to attract customers, thereby reducing the cost of mixed media PCBs. Therefore, as a customer, you can get better prices by competing with multiple manufacturers.
To sum up, the manufacturing cost of mixed media PCB is the result of comprehensive considerations, involving many aspects such as material cost, manufacturing process, design complexity and market competition. In order to evaluate the manufacturing cost of mixed-media PCBs, these factors need to be considered comprehensively and the appropriate manufacturer and reasonable design solutions need to be selected to achieve a balance between cost and performance.
What materials are mixed media PCBs made of?
The manufacturing of mixed media PCB involves a variety of materials, and the selection of these materials directly affects the performance, cost and applicable fields of the PCB. Here are some common mixed media PCB materials and their characteristics:
FR4 (fiberglass reinforced epoxy resin): FR4 is one of the most common PCB substrate materials and has good insulation properties, mechanical strength and heat resistance. It is widely used in common electronic equipment, has low cost, and is a common choice for manufacturing mixed media PCBs.
Rogers: Rogers material is a special type of ceramic substrate with excellent high-frequency characteristics and thermal performance. It is often used in high-frequency circuit design, such as radio frequency signal transmission, microwave communications and other fields. It is especially important for circuit design that requires high speed, high frequency and low loss.
Sola: Isola is a well-known PCB material supplier. Its products cover a variety of high-performance resin substrates with excellent thermal stability and mechanical properties. Isola materials are suitable for a variety of demanding electronic applications, including aerospace, military equipment and medical equipment.
Polyimide: Polyimide material has good high temperature resistance and flexibility, and is suitable for manufacturing flexible circuit boards (Flex PCB). This material is often used in applications that require bending or bending, such as portable electronics, flexible displays, etc.
Aluminum (aluminum substrate): Aluminum substrate is a special PCB covered with copper foil on an aluminum-based material, which has excellent heat dissipation performance. It is often used in heat dissipation modules for high-power electronic equipment, such as LED lighting, power modules, etc.
In addition to the above common materials, there are many other special materials, such as PTFE (polytetrafluoroethylene), Nelco (liquid crystal polymer), Arlon (polyamide amide), etc., which play an important role in specific fields or special applications. .
In summary, the material selection for mixed media PCB should be comprehensively evaluated based on factors such as circuit design requirements, environmental conditions, and cost considerations to ensure that the final product has good performance and reliability.
Who makes mixed media PCBs?
In today’s electronics industry, more and more manufacturers provide mixed media PCB manufacturing services to meet the needs of different customers. As a professional PCB manufacturer, our company is committed to providing customers with high-quality mixed media PCB solutions.
Our company has advanced production equipment and rich experience, and can flexibly respond to various PCB manufacturing needs. Our manufacturing processes are carried out in strict accordance with international standards to ensure product quality and stability. At the same time, we also focus on technological innovation and R&D investment to continuously improve production efficiency and product performance.
As a leading PCB manufacturer, we are committed to providing customized solutions to our customers. Our engineering team has extensive design experience and expertise and is able to work closely with customers to understand their needs and provide the best design solutions. We also offer flexible production capabilities and fast lead times to ensure customers receive products that meet their needs in a timely manner.
Our customer base covers various industries, including communications, medical, industrial control, automotive electronics and other fields. Whether it’s a small startup or a large enterprise, we can provide them with quality products and services. We know that the needs of our customers are the driving force for our progress, and we will wholeheartedly provide the best support and services to our customers.
In short, as a professional PCB manufacturer, our company has strong technical strength and rich experience, able to provide customers with high-quality mixed media PCB solutions. We will continue to work hard to create greater value for our customers and work with them to create a better future.
Five Characteristics of Great Customer Service
When choosing a mixed media PCB manufacturer, excellent customer service is crucial. Here are five characteristics a quality mixed media PCB manufacturer should have:
Prompt response: A quality manufacturer should be able to respond promptly to customer needs and questions. Whether it is a design consultation, quote request or order tracking, manufacturers should maintain efficient communication and feedback mechanisms. Timely response can help customers better plan and manage project progress and ensure orders are completed on time.
Expertise: Manufacturing mixed-media PCBs involves complex material selection, stack-up design, process control, etc., so manufacturers should have professional technical knowledge and experience. They should be able to provide customers with professional advice and solutions to help customers optimize designs, improve production efficiency and reduce costs.
Customized solutions: Every customer’s needs may be different, so manufacturers should be able to provide customized solutions based on the customer’s specific needs. Whether in material selection, lamination design or process flow, manufacturers should be able to flexibly adjust and meet customer requirements to provide customers with the best products and services.
Good communication: Maintaining good communication with your customers is key to building long-term relationships. Manufacturers should be able to establish good communication channels with customers, promptly update project progress, provide technical support, and solve problems encountered by customers during use. Through effective communication, manufacturers can better understand customer needs and adjust and improve services in a timely manner.
After-sales support: A quality manufacturer should provide comprehensive after-sales support and services. Whether it is solving product quality problems, providing technical support, or following up on order tracking, manufacturers should be able to provide timely and effective support to customers. High-quality after-sales service can enhance customers’ trust and satisfaction with manufacturers and promote the establishment and development of long-term cooperative relationships.
To sum up, a high-quality mixed media PCB manufacturer should have five characteristics: timely response, professional knowledge, customized solutions, good communication and perfect after-sales support. Through the combination of these characteristics, manufacturers can provide customers with high-quality products and services, meet customer needs and achieve mutual development.
FAQS
How does the choice of dielectric materials impact the performance of a mixed dielectric PCB?
The choice of dielectric materials significantly influences the performance of a mixed dielectric PCB. Different materials have distinct electrical, thermal, and mechanical properties, which can affect signal transmission, heat dissipation, and overall reliability. Selecting the appropriate materials based on the application requirements is crucial for achieving desired performance.
What are the challenges in manufacturing mixed dielectric PCBs?
Manufacturing mixed dielectric PCBs poses various challenges due to the complexity of combining different materials. Challenges may include ensuring uniformity in layer bonding, controlling impedance variations, minimizing material compatibility issues, and maintaining dimensional stability during processing. Overcoming these challenges requires advanced manufacturing techniques and meticulous process control.
How can one ensure the reliability of mixed dielectric PCBs?
Ensuring the reliability of mixed dielectric PCBs involves thorough testing and validation procedures. This includes conducting electrical testing to verify signal integrity, thermal analysis to assess heat dissipation capabilities, mechanical testing to evaluate structural integrity, and reliability testing under various environmental conditions. Additionally, adherence to industry standards and best practices throughout the design and manufacturing process is essential for achieving reliability.
What are the advantages of using mixed dielectric PCBs over traditional PCBs?
Mixed dielectric PCBs offer several advantages over traditional PCBs, including improved signal performance due to optimized dielectric properties, enhanced thermal management capabilities, greater design flexibility with the ability to tailor material properties for specific applications, and enhanced reliability through the use of multiple materials to mitigate single-point failures. These advantages make mixed dielectric PCBs ideal for demanding electronic applications where performance and reliability are critical.