Minimum Spacing PCB Manufacturer.A Minimum Spacing PCB Manufacturer specializes in crafting printed circuit boards with exceptionally narrow gaps between electrical components. Employing cutting-edge technology and precise engineering, they ensure the closest proximity possible between conductive traces and components, optimizing efficiency and performance in electronic devices. With a focus on compact design and high-density integration, their PCBs enable the creation of sleeker and more sophisticated gadgets while maintaining reliability and functionality. This manufacturer’s expertise lies in pushing the boundaries of spatial constraints, delivering solutions that cater to the demands of modern electronics with minimal footprint and maximum capability.
In the world of minimum pitch PCB manufacturing, we will explore exciting areas! Printed circuit boards (PCBs) are the backbone of modern electronics, enabling the seamless flow of power and data by etching or printing conductive paths on a non-conductive substrate. With the continuous development of technology, PCB manufacturing has entered a new stage, especially in the pursuit of higher performance and smaller size products. In this guest post, we’ll take an in-depth look at the process, materials, and cost factors of minimum pitch PCB manufacturing, as well as its importance and applications in the modern electronics industry.
What is a Minimum spacing PCB ?
Minimum pitch PCB is an important part of electronic equipment. It provides a platform for electronic components to connect circuits and transmit power and data through conductive paths. Compared with traditional PCBs, minimum pitch PCBs have tighter spacing between wires and lines, making the circuit board more compact and efficient. It is designed and manufactured to minimize the spacing between conductors to achieve higher circuit density and superior performance.
In electronic equipment, minimum pitch PCB plays a vital role. Not only does it provide mechanical support, it also enables electrical connections between electronic components via copper wires on the circuit board. This dense circuit design allows more functions and components to be integrated into a smaller space, making the device more compact and lightweight while improving performance and efficiency.
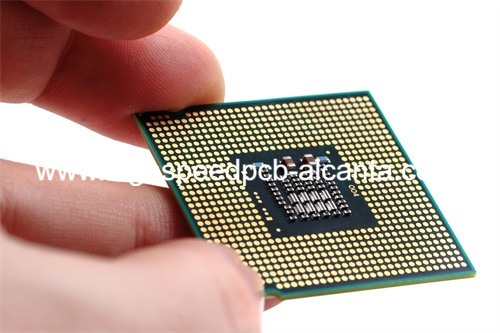
Minimum Spacing PCB Manufacturer
The manufacturing process of minimum pitch PCB requires a high level of precision and technology. From the selection of raw materials to the control of the production process, each step needs to strictly follow industry standards and quality control requirements. During the manufacturing process, it is important to ensure that the spacing between wires is as small as possible to maximize the density of the circuit board while maintaining good electrical characteristics and reliability.
In terms of applications, minimum pitch PCBs are widely used in electronic equipment in various fields, including communications, medical, industrial control, automobiles, etc. In these fields, the requirements for device size and performance are getting higher and higher, and the design and manufacturing of minimum pitch PCBs is one of the keys to meeting these requirements.
In short, minimum pitch PCB is an indispensable component of modern electronic equipment. Through compact design and optimized manufacturing process, it achieves high performance and high efficiency of the circuit board and promotes the development and innovation of electronic technology.
How to Design a Minimum spacing PCB ?
Designing a minimum pitch PCB involves multiple key steps, each of which is critical and requires careful design and professional skills from engineers. Here are the general steps for designing a minimum pitch PCB:
The first step in the design process is to create a schematic, which is the blueprint of the circuit design. In the schematic, the engineer will identify all the electronic components and the connections between them. This stage is fundamental to ensuring circuit functionality and performance, so the selection and placement of each component requires careful consideration.
After determining the structure and function of the circuit, the engineer will begin placing the electronic components on the PCB board. This includes selecting appropriate component sizes and shapes and locating them to minimize wire lengths and minimum spacing requirements.
Once the components are placed on the PCB, the next step is to route them. During the wiring process, engineers will draw wire paths to ensure the circuit’s connections. When designing a minimum pitch PCB, routing becomes even more important as the minimum spacing between conductors must be ensured to meet specification requirements.
Once the routing is complete, engineers will generate an initial version of the PCB, often called a prototype. This prototype will be used to test the functionality and performance of the circuit, as well as confirm that minimum spacing requirements are met. At this stage, multiple revisions and optimizations may be required to ensure the PCB design is at its best.
To complete these steps, engineers usually use professional PCB design software, such as Altium Designer, Cadence Allegro, or Eagle. These software provide a wealth of features and tools to help engineers easily perform schematic design, component placement, routing and prototyping, and ensure that the final PCB design meets requirements.
When designing minimum pitch PCBs, engineers need to pay special attention to circuit complexity, power distribution, signal integrity, and minimum pitch requirements. Through careful design and effective layout, engineers can achieve high performance and reliability in minimum pitch PCB designs that provide critical support for modern electronic devices.
What is the Minimum spacing PCB Fabrication Process?
Minimum pitch PCB manufacturing involves multiple stages, each of which is critical and requires precise operation and strict adherence to industry standards to ensure the quality and reliability of the final product.
The first step in manufacturing a minimum pitch PCB is to prepare the substrate. The substrate may be a non-conductive base material made of FR4 or other materials. At this stage, the manufacturer needs to carefully inspect the surface of the substrate to ensure there is no dirt or defects.
When performing layer alignment, manufacturers align the substrate with the copper foil layer to ensure that the final conductive pattern is accurately aligned with the substrate. This step requires a high degree of precision and careful handling to ensure the final PCB has accurate electrical connections.
Once the substrate and copper foil layers are aligned, the next step is the formation of the copper pattern. This can be achieved through a variety of methods, such as chemical etching or photolithography. The purpose of copper patterning is to create conductive paths on the substrate that will connect electronic components.
Etching is the process of removing unwanted copper material from a PCB. This step ensures that only the desired conductive pattern remains to avoid short circuits and other electrical problems. Precisely controlling the corrosion process is key to ensuring PCB quality.
Drilling holes in a PCB is used to mount components or connect wires between layers. These holes must be in precise locations and have the correct diameter to ensure that the components fit correctly and the connection is reliable.
Surface preparation is the final stage and provides a protective layer to the PCB and a good contact surface for soldering components. Common surface treatment methods include tin spraying, gold spraying or silver spraying, etc.
Overall, minimum pitch PCB manufacturing involves multiple complex stages, each of which requires a high degree of specialized knowledge and skills. Only through precise operations and strict quality control can high-quality, reliable PCB products be produced to meet the performance and reliability requirements of modern electronic equipment.
How to manufacturing a Minimum spacing PCB ?
Manufacturing minimum pitch PCBs requires a series of precise steps and advanced manufacturing techniques to ensure the quality and performance of the final product. Here are the details on how to make a minimum pitch PCB:
First, manufacturing a PCB involves choosing the right materials. In minimum pitch PCB manufacturing, commonly used substrate materials include FR4 fiberglass substrates, which have good mechanical properties and high temperature resistance and are suitable for most electronic applications. In addition, the conductive layer usually uses copper foil, because copper has good conductivity and processability and can meet the requirements of high-density wiring.
Secondly, the use of advanced manufacturing technology is the key to manufacturing minimum pitch PCBs. One of them is photolithography, which works by covering the surface of a copper foil with a photosensitive adhesive and then using a photomask and UV exposure to define the shape of the conductive lines. After exposure, the unexposed portions are removed by chemical etching, creating conductive lines.
Chemical etching is another important manufacturing technique that removes unwanted portions of copper by dipping copper foil into a solution containing an etchant. This approach enables high-precision line shapes and dimensions to meet minimum spacing requirements.
Minimum pitch PCB manufacturing also focuses on achieving tight tolerance requirements. During the design and manufacturing process, the distance between conductive lines must be strictly controlled to avoid short circuits or electrical interference. To optimize space utilization and performance, manufacturers typically use high-precision equipment and processes and conduct strict quality control and testing.
To sum up, manufacturing minimum pitch PCB requires selecting appropriate materials, adopting advanced manufacturing technology, and strictly controlling tolerance requirements. These steps ensure the quality and performance of the final product, making it suitable for a variety of high-density electronic applications.
How Much Does a Minimum spacing PCB Cost?
The cost of minimum pitch PCB is a complex and variable issue, affected by multiple factors. Let’s dive into these factors to better understand the cost structure of minimum pitch PCBs.
First of all, size is one of the important factors that determine the cost of minimum pitch PCB. Larger size PCBs usually require more materials and longer manufacturing time, so the cost is relatively higher. On the other hand, smaller size PCBs may be more economical in terms of material cost and manufacturing time.
Secondly, the complexity of PCB also has a direct impact on cost. PCBs with complex wiring, multi-layer structures and high-density components require more processes and precision processing, so the cost will increase accordingly. In comparison, a simple single-layer PCB may cost less.
Material quality is another important consideration. High-quality materials typically cost more but provide better performance and reliability. For minimum pitch PCBs, high-precision materials and manufacturing processes are required to ensure the accuracy of wire spacing and size, further increasing costs.
Finally, production volume also affects the cost of minimum pitch PCBs. High-volume production often reduces the cost of a single PCB because manufacturers can save costs through bulk purchasing and automated production. However, low-volume production or custom orders may result in increased costs because more labor and custom processing are required.
To summarize, the cost of a minimum-pitch PCB depends on several factors, including size, complexity, material quality, and production volume. Although minimum pitch PCBs may incur higher costs, through reasonable design and manufacturing processes, as well as selecting the right manufacturer, costs can be minimized while ensuring product quality and performance.
What materials are Minimum spacing PCB made of?
Minimum pitch PCB is a highly precise electronic component, and its constituent materials are crucial. Typically, minimum pitch PCB consists of substrate material, conductive layer and protective layer.
First, let’s look at the substrate material. In minimum pitch PCB manufacturing, a common substrate material is FR4 fiberglass board. FR4 is a substrate material with high strength and good heat resistance. It has good insulation properties and can effectively isolate electrical signals between conductive layers to ensure stable operation of the circuit. In addition, the FR4 substrate also has good mechanical strength and can withstand various vibrations and impacts of electronic equipment during transportation and use.
Next is the conductive layer. The conductive layer is the main component on a minimum pitch PCB and is responsible for transmitting current and signals. During the manufacturing process, copper foil is bonded to the FR4 substrate to form a conductive layer. Copper foil has excellent electrical conductivity and good processability, and can meet various circuit needs of PCB in electronic equipment. Through precise wiring design on the conductive layer, the connection between different components can be achieved and the stability and reliability of signal transmission can be ensured.
Finally, there is the protective layer. The protective layer plays an important role in the minimum pitch PCB. It not only provides protection for the PCB circuit, but also achieves identification and beautification of appearance. Common protective layers include solder film and silk screen. Solder film is usually coated on the PCB surface to protect the conductive layer from the external environment, such as moisture, chemicals, etc. Silk screen printing is used to mark the location, model and direction of components on the PCB surface to facilitate assembly and maintenance.
To sum up, the constituent materials of minimum pitch PCB include substrate material, conductive layer and protective layer. These materials work together to ensure the stability, reliability and durability of PCB circuits and meet the high performance and high quality requirements of modern electronic equipment.
Who manufactures Minimum spacing PCB ?
Manufacturers play a vital role in manufacturing minimum pitch PCBs. For many companies, choosing the right manufacturer is a critical part of ensuring product quality and performance. So, who makes minimum pitch PCBs?
Here, I would like to emphasize that our company is ideal for manufacturing minimum pitch PCBs. As an experienced and professional PCB manufacturer, we are committed to providing customers with high-quality, high-performance PCB solutions. Here are some of the key benefits of our company manufacturing minimum pitch PCBs:
Advanced manufacturing equipment and technology: We have advanced production equipment and technology, including high-precision photolithography machines, chemical etching equipment and precision drilling machines. These equipment and technologies enable us to achieve tight tolerance requirements and complex circuit layouts, ensuring the quality and reliability of the final product.
Rich experience and professional team: We have an experienced and skilled professional team, including engineers, technicians and quality control experts. They have extensive experience and expertise in the field of PCB manufacturing and are able to provide customers with a full range of technical support and solutions.
Strict quality control and inspection standards: We strictly follow the ISO quality management system and have developed a series of strict quality control and inspection standards. From the procurement of raw materials to the delivery of finished products, each manufacturing step is carefully monitored and strictly inspected to ensure that the products meet customer requirements and expectations.
Flexible production capacity and delivery time: We have flexible production capacity and an efficient production management system, which can meet customers’ various mass production needs and delivery time requirements. Whether it is small batch customized production or large-scale mass production, we are able to complete orders in a timely and accurate manner.
Customer first service concept: We always adhere to the “customer first” service concept and put customer needs and satisfaction first. Our customer service team will wholeheartedly provide customers with personalized and professional services to ensure that customers receive satisfactory experience and support throughout the entire cooperation process.
To sum up, our company is the best choice for manufacturing minimum pitch PCB. Whether you need high-performance electronic equipment or customized circuit boards, we can provide you with high-quality, reliable PCB solutions. Look forward to working with you!
What are 5 qualities of a good customer service?
In minimum pitch PCB manufacturing, excellent customer service is a key factor in ensuring customer satisfaction and business success. Here are five traits that can help manufacturers provide excellent customer service:
Professionalism: The first attribute of great customer service is professionalism. Manufacturers should have professional knowledge and skills in the industry, be able to accurately understand customer needs, and provide targeted solutions. They should be aware of the latest technology trends and industry standards to ensure product quality and reliability.
Responsiveness: Responding quickly to customer needs and questions is an important part of great customer service. Manufacturers should promptly respond to customer emails, phone calls, and messages and provide immediate support and solutions. By quickly resolving customer issues, manufacturers can enhance customer trust and satisfaction.
Personalized care: Understanding customers’ individual needs and providing customized services is the key to excellent customer service. Manufacturers should develop close working relationships with customers to understand their preferences, goals and challenges and tailor solutions for them based on this information. Personalized care can enhance customer loyalty and promote the establishment of long-term relationships.
Problem-solving skills: Another attribute of great customer service is effective problem-solving skills. Manufacturers should be able to quickly identify and solve problems faced by customers and provide practical solutions. They should have good communication and coordination skills and work closely with customers to ensure that problems are resolved in a timely manner and customers’ interests are protected.
Continuous improvement: Continuous improvement and improvement of service quality are the core values of excellent customer service. Manufacturers should regularly collect customer feedback and make adjustments and improvements based on the feedback results. They should actively listen to customers’ opinions and suggestions and continuously optimize products and services to meet customers’ changing needs and expectations.
To sum up, in minimum pitch PCB manufacturing, quality customer service is not only a basic requirement to meet customer needs, but also the key to establishing long-term cooperative relationships and achieving business success. Through the attributes of professionalism, responsiveness, personalized care, problem solving and continuous improvement, manufacturers can provide customers with an exceptional experience and earn their trust and loyalty.
FAQS
What is the minimum spacing requirement for PCB wires?
The minimum spacing requirements for PCB traces depend on the complexity of the circuit design and the application environment. Typically, minimum spacing requirements are determined by the PCB manufacturer or design specifications. For high-density PCBs, the minimum spacing is usually between tens to hundreds of microns, while for regular PCBs, it may be more relaxed.
How does minimum pitch PCB manufacturing improve circuit performance?
Minimum pitch PCB manufacturing improves circuit performance and reliability. By reducing the distance between wires, crosstalk and signal loss during signal transmission can be reduced, thereby improving the transmission rate and stability of the circuit. In addition, minimum pitch PCB can also reduce the size of the circuit board, making it more suitable for compact device design.
What are the factors that affect the cost of minimum pitch PCB?
The cost of minimum pitch PCB is affected by multiple factors, including material selection, number of layers, complexity and production scale. The use of high-precision manufacturing techniques and special materials increases costs, while mass production and standardized designs reduce costs.
How to ensure the reliability of minimum pitch PCB?
Ensuring the reliability of minimum pitch PCB requires strict control from design to manufacturing. During the design stage, appropriate spacing and insulation distances should be considered to avoid signal interference and short circuits. During the manufacturing process, process specifications need to be strictly enforced to ensure quality and accuracy at every step.
For high-frequency applications, what are the special considerations when designing minimum pitch PCBs?
For high-frequency applications, designing a minimum pitch PCB requires considering the frequency and baud rate of signal transmission. During layout and routing, crosstalk and reflections between signal lines need to be avoided, and appropriate layer stacking structures and impedance matching techniques should be used. Additionally, selecting the appropriate materials and surface treatments are critical to circuit performance.