Minimum Pad Clearance PCB Manufacturing.Minimum pad clearance in PCB manufacturing refers to the smallest allowable distance between copper pads on a printed circuit board (PCB). This critical specification ensures that adjacent pads don’t short-circuit or interfere with each other during assembly or operation. Achieving an optimal minimum pad clearance demands precision in design and manufacturing processes, accounting for factors like solder mask application and component placement. Strict adherence to these specifications ensures reliable functionality and prevents electrical failures in electronic devices. Manufacturers employ advanced techniques and stringent quality control measures to meet or exceed minimum pad clearance standards, ensuring the integrity of the final product.
In today’s digital age, printed circuit boards (PCBs) are the unsung heroes that support our daily devices. From smartphones to smartwatches, PCBs are the invisible connectors. However, a deeper dive into the world of PCB manufacturing reveals a critical aspect that is often overlooked: minimum pad clearance. Minimum pad clearance plays a critical role in ensuring the integrity and reliability of electronic circuits, but it is a complex and esoteric area. This article will delve into the mysteries of Minimum Pad Clearance PCB manufacturing and reveal its key position in modern electronics manufacturing.
What is the minimum pad gap?
In PCB (Printed Circuit Board) design and manufacturing, the minimum pad gap is a key concept. Simply put, it refers to the minimum distance between the edge of a pad on a PCB and any other nearby conductive elements. These conductive elements may be other pads, wires, or ground planes. The purpose of minimum pad clearance is to ensure circuit integrity and reliability.
First, the minimum pad gap plays a vital role in preventing short circuits. On a PCB, sufficient clearance is required between different wires and pads to prevent them from accidentally touching during the manufacturing process and causing short circuits. By ensuring adequate spacing, manufacturers can reduce the risk of errors during welding, thereby increasing production efficiency and quality.
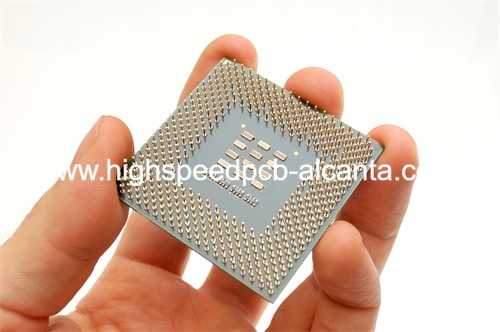
Minimum Pad Clearance PCB manufacturing
Secondly, minimum pad clearance is also critical to reduce signal interference. When wires or pads are too close together, signal interference can occur, causing circuit performance degradation or even failure. By increasing the gap between the pads, the possibility of signal interference can be effectively reduced, thereby ensuring stable operation of the circuit.
Additionally, minimum pad clearance ensures PCB reliability. In harsh environments such as high temperature and high pressure, if the gap between the pads is insufficient, the solder joints may become loose or broken, thereby affecting the stability and durability of the entire circuit. By following minimum pad gap specifications, manufacturers can improve PCB reliability and extend its service life.
In summary, minimum pad clearance plays a vital role in PCB design and manufacturing. It not only affects the integrity and reliability of the circuit, but is also directly related to the performance and stability of the circuit. Therefore, designers and manufacturers must fully consider the minimum pad gap requirements when designing and manufacturing PCBs, and take appropriate measures to ensure that they meet the standards.
How to achieve minimum pad clearance in PCB design?
Achieving minimum pad clearance in PCB design requires careful attention to detail by engineers. First, engineers must carefully lay out components and traces. This means that during the PCB layout stage, they need to consider the position and orientation of each component to minimize the distance between pads and ensure there is enough space between them to avoid the occurrence of short circuits and signal interference.
When it comes to component layout, engineers need to consider the electrical and physical interactions between different components. They may place key components on one side of the board to minimize interference with other components. In addition, they need to take into account the length and direction of the signal transmission path to ensure signal stability and reliability.
In addition to component layout, routing is also key to achieving minimal pad clearance. Engineers must carefully plan trace paths to ensure pads are not too close together and avoid crossing or staggered traces. They may utilize multilayer board designs to separate signal and power planes, thereby reducing the risk of signal interference.
During the design process, engineers should also pay close attention to the design rule checking functions provided by PCB design software. These features can help them detect and correct potential layout or routing errors early, ensuring that the final PCB design meets minimum pad clearance requirements.
In addition, engineers can also consider using some advanced design techniques to further optimize the PCB design, such as using integrated circuits such as microcontrollers or FPGAs to reduce component count and layout complexity, thereby reducing pad gap requirements.
In summary, achieving PCB design with minimal pad clearance requires engineers to pay careful attention to detail in layout and routing. By carefully planning component locations and trace paths, and leveraging design rule checking capabilities and advanced design techniques, engineers can ensure the final PCB design meets high quality and reliability requirements.
How to make a PCB with minimal pad gaps?
Manufacturing PCBs with minimal pad gaps is a complex and delicate process that requires multiple critical steps, each of which is critical. The following are the main steps in manufacturing this type of PCB:
The first step in PCB manufacturing is to prepare the substrate. Typically, the substrate is made of fiberglass reinforced epoxy (FR-4). At this stage, the surface of the substrate will be cleaned and treated to ensure that the material’s surface is smooth and suitable to accept subsequent process steps.
After the substrate is prepared, the next steps involve transferring the designed circuit pattern onto the substrate. This is usually achieved through patterning and photographic techniques. In this process, a photosensitive overlay is applied to the substrate surface, and UV light is used to project the designed pattern onto the overlay.
After patterning and exposure, the substrate is fed into an acidic solution for etching. The etching process removes copper from the surface of a substrate by applying an acidic solution to uncovered areas, creating circuit patterns. Precise control of etching time and temperature is critical to ensure the required gap size and accuracy of circuit connections.
After etching is completed, the copper layer on the surface of the substrate will be exposed. In order to establish the circuit connection, a layer of copper needs to be redeposited on the surface of the substrate. This is usually achieved through electrochemical deposition or electroplating techniques, ensuring that the copper is deposited evenly and tightly bonded to the substrate surface.
Quality control is crucial throughout the entire manufacturing process. By using high-precision measurement tools and strict quality inspection processes, manufacturers can ensure that each PCB meets the specified minimum pad gap requirements. Any parts that do not meet the requirements are promptly detected and corrected to ensure the quality and reliability of the final product.
After copper deposition, the PCB may require final processing, such as a protective coating on the surface to prevent oxidation or corrosion, and may require final inspection and testing to ensure compliance with specifications.
To summarize, manufacturing PCBs with minimal pad gaps requires a rigorous manufacturing process, including substrate preparation, patterning and photography techniques, etching, copper deposition, quality control, and final processing. Every step requires precision and accuracy to ensure the performance and reliability of the final product meet requirements.
What is the cost of minimum pad clearance?
Although achieving minimum pad clearance adds some complexity to the PCB manufacturing process, as technology continues to advance, it is easier to achieve and more cost-effective than ever before. Modern manufacturers are able to take advantage of economies of scale and process optimization to reduce production costs without sacrificing product quality.
First of all, technological advancement has brought many innovations in the field of PCB manufacturing. New manufacturing processes and equipment make it easier to achieve minimum pad gaps. For example, high-resolution imaging technology and precise control systems allow manufacturers to more accurately control the distance between pads, thereby reducing manufacturing costs.
Second, manufacturers can take advantage of economies of scale to reduce production costs. As PCB demand increases, mass production can reduce the production cost per unit. Manufacturers can achieve effective cost control by purchasing raw materials and equipment in large quantities and optimizing the production process.
Process optimization is also a key factor in reducing costs. Manufacturers improve production efficiency by optimizing each production step and reducing scrap rates and production cycle times. These optimization measures not only reduce direct production costs, but also reduce indirect costs such as human resources and energy consumption, further reducing overall costs.
Additionally, increased competition is forcing manufacturers to seek more cost-effective solutions. Facing fierce market competition, manufacturers have to constantly seek ways to reduce costs in order to remain competitive. This prompts them to continuously innovate and adopt more effective production technologies and management methods to reduce the manufacturing costs of their products.
Overall, while achieving minimum pad clearance may add complexity to the manufacturing process, advances in technology and efforts by manufacturers have made it easier and more cost-effective to achieve than ever before . By leveraging economies of scale, process optimization, and continuous innovation, manufacturers have successfully reduced production costs to provide customers with high-quality, minimum pad gap PCBs while remaining competitive.
What materials are Minimum Pad Clearance PCB made of?
When manufacturing minimum pad gap PCBs, proper material selection is critical. Not only do these materials need to meet strict clearance requirements, they must also ensure reliability and durability. The following are the most commonly used materials:
FR-4 substrate is a fiberglass reinforced epoxy resin material widely used in PCB manufacturing. It has excellent insulation properties and mechanical strength, and can effectively prevent signal interference in the circuit. The thermal and chemical stability of FR-4 substrates make them ideal for manufacturing PCBs with minimal pad gaps.
Copper foil is the conductive layer material of PCB and is used to form wires and pads in circuits. For minimum pad gap PCBs, the copper foil must have precise thickness specifications to ensure minimum gaps between the wires and pads in the circuit. High-quality copper foil can provide good electrical conductivity and reliable connections, ensuring the stability and reliability of the circuit.
Pad cover usually uses a pad cover agent or solder mask to cover the area between the pad and the connected device to prevent short circuits and oxidation. For minimum pad gap PCBs, the selection of pad coverage is critical. The thickness and quality of the coverage need to be ensured to ensure that the gap requirements are not affected.
Printing inks are used for marking and marking printed circuit boards. For minimum pad gap PCBs, the printing ink must have good adhesion and abrasion resistance to ensure clarity and durability of logos and markings. Choosing high-quality printing ink can effectively improve the appearance and quality of PCB.
To summarize, the selection of appropriate materials is critical to manufacturing a minimum pad gap PCB. High-quality FR-4 substrates, precise thickness specifications of copper foil, and excellent pad coverage and printing inks ensure PCBs have excellent performance and reliability while meeting strict clearance requirements. In the PCB manufacturing process, material selection and quality are key factors to ensure circuit stability and reliability, and deserve high attention and careful selection by manufacturers and engineers.
Who is the supplier of minimum pad gap PCB?
When looking for a supplier of minimum pad gap PCBs, it is critical to choose a trustworthy partner. As a supplier to our company, we are committed to providing our customers with high-quality PCB products, including boards that meet the most stringent clearance requirements. Here are some reasons why we are the best choice:
Technical expertise: We have the technical expertise and experience to meet a wide range of minimum pad clearance requirements. Our engineering team is well versed in PCB design and manufacturing and is able to provide customized solutions based on our customers’ specific needs.
Advanced Equipment: We are equipped with advanced manufacturing equipment and technology, including high-precision laser drilling and imaging systems, to ensure that our PCBs maintain high quality and consistency while achieving minimal pad gaps.
Quality Control: We strictly implement the quality management system to ensure that each production stage meets international standards and customer requirements. From raw material procurement to final shipment, we conduct strict inspection and testing to ensure product quality.
Fast Delivery: We understand that time is of the essence to our customers, so we have adopted effective production planning and supply chain management measures to ensure timely delivery. No matter the size of your order, we can meet your needs.
Customer service: We value communication and cooperation with customers and are committed to providing excellent customer service. Our team is on hand to resolve any questions and provide technical support and advice to ensure your project runs smoothly.
As a supplier of minimum pad gap PCBs, we are known for quality products, reliable delivery, and excellent customer service. No matter the size of your project, we have the ability to meet your needs and exceed your expectations. Looking forward to establishing a long-term cooperative relationship with you and contributing to your business success.
What are 5 qualities of a good customer service?
In the world of minimum pad gap manufacturing, excellent customer service is paramount. Manufacturers must possess a range of qualities to ensure that customer needs are met quickly and efficiently, building long-term relationships and enhancing industry reputation. Here are five key qualities of great customer service:
Responsiveness: Being able to respond quickly to customer inquiries, questions or complaints is at the core of great customer service. In the field of minimum pad gap manufacturing, customers may need to urgently solve problems or seek technical support, so it is crucial to respond promptly and provide effective solutions.
Knowledge and ability: The customer service team must have sufficient product and industry knowledge to accurately understand customer needs and provide professional advice. In the field of minimum pad gap manufacturing, customers may need to understand complex technical details or specific manufacturing processes, so a high level of knowledge is indispensable.
Compassion: Understanding and empathizing with your customers’ needs and concerns is an important part of building great customer relationships. In the world of minimum pad gap manufacturing, customers may face project delays, quality issues, or technical challenges, so it is critical to empathize and proactively support customers.
Adaptability: Customer service teams must be flexible and adaptable, able to adapt their services to the specific needs and circumstances of their customers. In the world of minimum pad gap manufacturing, customers’ project requirements may change due to design changes or emergencies, so adaptability is key to successfully meeting a variety of challenges.
Effective communication: Clear, timely and effective communication is the foundation for building trust and cooperation. Customer service teams must be good at listening to customers’ needs and communicating the information in a clear way. In the world of minimum pad gap manufacturing, accuracy and timeliness of communication are critical to coordinating production schedules and resolving issues.
To summarize, great customer service plays a vital role in the world of minimum pad gap manufacturing. By demonstrating qualities such as responsiveness, knowledge, empathy, adaptability, and effective communication, manufacturers can build strong customer relationships, increase customer satisfaction, and stand out in a competitive marketplace.
FAQ
What are the typical clearance requirements for Minimum Pad Clearance PCBs?
Clearance requirements for Minimum Pad Clearance PCBs vary depending on factors such as the specific application, design complexity, and manufacturing capabilities. However, industry standards commonly dictate minimum clearance distances ranging from a few mils to tens of mils. These specifications ensure that there is adequate separation between conductive elements on the PCB to prevent short circuits and signal interference, thereby maintaining the integrity and reliability of electronic circuits.
How does Minimum Pad Clearance impact signal integrity?
Minimum Pad Clearance directly influences signal integrity in electronic circuits. By maintaining sufficient distance between pads and other conductive elements on the PCB, Minimum Pad Clearance helps minimize the risk of signal distortion and crosstalk. Signal integrity is crucial for ensuring reliable communication between electronic components and optimizing overall circuit performance. Therefore, adhering to Minimum Pad Clearance specifications is essential to preserve signal integrity and prevent potential issues such as data corruption or loss.
Are there any environmental considerations associated with Minimum Pad Clearance PCB manufacturing?
Yes, environmental considerations play a significant role in Minimum Pad Clearance PCB manufacturing. Manufacturers are increasingly adopting environmentally friendly practices to minimize the ecological footprint of PCB production. This includes utilizing lead-free soldering techniques, which reduce the environmental impact of soldering processes by eliminating hazardous substances. Additionally, waste recycling initiatives are implemented to minimize the generation of electronic waste and promote sustainability in PCB manufacturing. By embracing environmentally conscious practices, manufacturers can contribute to the preservation of the environment while producing high-quality PCBs with Minimum Pad Clearance.
What are the key challenges in achieving Minimum Pad Clearance during PCB manufacturing?
Achieving Minimum Pad Clearance during PCB manufacturing presents several challenges, primarily related to precision and complexity. Ensuring precise alignment and spacing between pads and other conductive elements requires advanced manufacturing techniques and high-resolution imaging technologies. Additionally, factors such as substrate material properties and surface finish options can impact the feasibility of achieving Minimum Pad Clearance. Manufacturers must carefully consider these challenges and employ specialized equipment and processes to overcome them while maintaining adherence to clearance specifications.