Minimum Clearance PCB Manufacturer.A Minimum Clearance PCB Manufacturer specializes in crafting circuit boards with precise spacing between components, ensuring optimal performance and reliability in tight spaces. Employing advanced manufacturing techniques, they meticulously engineer boards with minimal separation between conductive elements, enabling efficient electronic signal transmission while conserving valuable real estate within devices. With a keen focus on precision and adherence to industry standards, they cater to clients requiring compact, high-density PCB solutions for cutting-edge electronics, ranging from miniature IoT devices to aerospace applications demanding utmost reliability in constrained environments.
With the continuous development of electronic products, the demand for PCB has gradually increased. When designing a PCB, ensuring the stability and reliability of the circuit is a crucial consideration. In this regard, the emergence of minimum gap PCB technology has become an important innovation. By reducing the spacing between wires, this technology enables higher-density circuit layouts, allowing electronic products to accommodate more functions and components in limited space.
What is Minimum Clearance PCB?
Minimum clearance PCB technology is an advanced PCB design concept that aims to minimize the spacing between conductors and between conductors and other components on the PCB. In traditional PCB design, the spacing between wires is usually large to ensure the stability and reliability of the circuit. However, in some application scenarios that require extremely high circuit performance, such as high-frequency communications, high-speed data transmission, and miniaturized electronic devices, traditional PCB design can no longer meet the needs. Therefore, minimum clearance PCB technology came into being.
Minimum gap PCB technology uses advanced manufacturing processes and design methods to greatly reduce the spacing between conductors on the PCB, even to the level of tens of microns. This technology makes the circuit layout of electronic products more compact, the signal transmission path is shorter, and the resistance is lower, thereby improving the performance and efficiency of the circuit.
In minimum clearance PCB technology, one of the key challenges is how to effectively prevent interference and cross-coupling between conductors. In order to solve this problem, designers usually adopt various measures, such as rationally laying out wires, using shielding technology, using ground planes and power planes, etc. In addition, the precision and stability of the manufacturing process also play a crucial role in the performance of minimum gap PCBs, requiring high-precision manufacturing steps such as pattern transfer, etching, and drilling.
Minimum clearance PCB technology has a wide range of applications. It can be used not only in high-performance communication equipment, computers and network equipment, but also in medical equipment, automotive electronics, industrial control and other fields. In these areas, minimum gap PCB technology can help designers achieve higher signal transmission rates, more stable circuit performance, and more compact product designs, thereby increasing product competitiveness and market share.
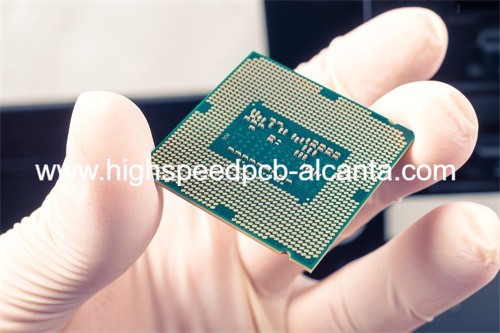
Minimum Clearance PCB Manufacturer
In general, minimum gap PCB technology is an important PCB design innovation that provides strong support and driving force for the development and advancement of electronic products. With the continuous advancement of technology and changing market demands, it is believed that minimum gap PCB technology will play an increasingly important role in the future and become an important technological breakthrough in the field of electronic product design.
Minimum Clearance PCB design Reference Guide
In the design of modern electronic products, minimum clearance PCB technology is widely adopted to achieve higher performance, more compact designs, and lower manufacturing costs. Here is a minimum clearance PCB design reference guide to help you better apply this technology:
Design planning
Before proceeding with PCB design, adequate design planning must first be carried out. Determining the overall requirements and functions of the circuit and clarifying the components and signal transmission paths that need to be accommodated will provide important guidance for subsequent design.
Layout design
When designing PCB layout, the requirements of minimum clearance PCB technology should be fully considered. Arrange various components and wires rationally, minimize the spacing between wires, and ensure that the gaps between wires and other components meet design requirements.
Wire routing
When routing wires, minimize the spacing between wires and adopt appropriate routing methods to minimize signal interference and cross-coupling. Using professional PCB design software can help you achieve this goal better.
Circuit debugging
After completing the PCB design, be sure to debug and test the circuit. Check whether the gaps between the wires meet the design requirements and whether there is signal interference or other problems. If necessary, make adjustments and optimizations to ensure the stability and reliability of the circuit.
Manufacturing process
During PCB manufacturing, special attention should be paid to the requirements of minimum clearance PCB technology. Select appropriate manufacturing processes and materials to ensure that the minimum clearance required in the design can be achieved and to ensure the accuracy and stability of the manufacturing process.
QC
Throughout the manufacturing process, strict quality control is carried out to ensure that the quality of the PCB meets the design requirements. Carry out necessary inspections and tests to discover and solve problems in a timely manner to ensure the quality and reliability of the final product.
By following the above design reference guidelines, you can better apply minimum clearance PCB technology to achieve high performance, compact design and low-cost manufacturing of electronic products. This will help enhance the competitiveness of your products and meet growing market demand.
What material is used in Minimum Clearance PCB?
Minimum Clearance PCB (Minimum Clearance PCB) is an innovative design technology that involves the selection and use of various materials to ensure the stability and performance of the circuit. The following materials are commonly used in minimum clearance PCBs:
Substrate material
In minimum clearance PCBs, choosing the right substrate material is critical. Common substrate materials include FR4 (fiberglass reinforced epoxy), aluminum substrates, and flexible substrates such as polyimide. These materials have good insulation properties, mechanical strength and high temperature resistance, making them suitable for high-density circuit layouts and compact designs.
Conductive layer material
In minimum clearance PCBs, copper foil is often used as the material for the conductive layer. Copper foil has good electrical conductivity and processing properties, allowing precise circuit layout and efficient signal transmission. In addition, copper foil also has good welding properties, helping to ensure welding quality and connection stability.
Insulating layer material
In minimum clearance PCBs, the choice of insulation layer is critical to ensure circuit stability and reliability. Common insulation layer materials include epoxy resin, polyimide, etc. These materials have good insulation properties and high temperature resistance, which can effectively prevent short circuits and cross-coupling between wires, improving the stability and reliability of the circuit.
Surface treatment materials
In minimum clearance PCBs, it is often necessary to treat the circuit surface to improve the circuit’s corrosion resistance and connection stability. Common surface treatment materials include tin, gold, silver, etc. These materials can effectively prevent oxidation and corrosion while ensuring good electrical conductivity, ensuring long-term stable operation of the circuit.
Solder mask material
Solder mask is an important component in minimum clearance PCBs, used to protect the circuit surface from the outside environment while improving the circuit’s corrosion resistance and reliability. Common solder mask materials include green solder mask ink, transparent solder mask ink, etc. These materials have good insulation properties and corrosion resistance, which can effectively protect the circuit surface and extend the service life of the circuit.
Through reasonable selection and use of the above materials, minimum gap PCB can achieve higher performance, more compact design and higher reliability, providing strong support and guarantee for the development and application of electronic products.
What size are Minimum Clearance PCB?
The size of the minimum clearance PCB depends on the design requirements and application scenarios, and can usually be determined based on the following factors:
Number of features and components
The size of a PCB is usually related to the number of functions and components that need to be accommodated. If an electronic product needs to contain a large number of features and components, the size of the PCB may be relatively large to accommodate all the necessary parts and maintain a good layout. On the contrary, if the product function is relatively simple, the PCB size may be smaller.
Space constraints
When designing a PCB, the form factor and size constraints of the product must be taken into consideration. Some electronic products may have very strict space constraints that require a PCB as small as possible to fit. Therefore, functional requirements and space constraints need to be balanced when sizing the PCB.
Manufacturing cost
PCB size also affects manufacturing costs. Generally speaking, larger PCB sizes result in increased material costs and manufacturing process costs because more material and longer manufacturing time are required. Therefore, manufacturing costs also need to be taken into consideration when determining PCB size.
Cooling requirements
If the electronic product has high power consumption or requires good heat dissipation performance, the size of the PCB may be relatively large to accommodate the heat sink or heat dissipation structure and ensure sufficient surface area for heat dissipation.
To sum up, the size of the minimum clearance PCB is a comprehensive consideration of many factors. Typically, they can come in many different sizes, ranging from a few millimeters to tens of millimeters. When designing and manufacturing minimum clearance PCBs, reasonable choices need to be made based on specific application requirements and design parameters to achieve optimal performance and results.
The Manufacturer Process of Minimum Clearance PCB.
The manufacturing process of minimum clearance PCB is a precise and complex process that requires strict control and a high degree of expertise. The following are the main steps of the minimum clearance PCB manufacturing process:
Design preparation
First, based on the customer’s needs and specifications, the design team performs PCB layout design. During the design process, the minimum gap requirements need to be taken into consideration, and circuit components and wires should be reasonably arranged in the layout to ensure the realization of the minimum gap.
Material selection
Selecting high-quality materials suitable for minimum clearance PCB manufacturing is a critical step. High-quality substrate materials are typically used, such as FR4 fiberglass-reinforced epoxy, and the material selection for the conductive and insulating layers also needs to take into account minimum clearance requirements.
Image transfer
The next step in PCB manufacturing is image transfer, which is the process of transferring a designed pattern onto the PCB board using photolithography. In minimum gap PCB manufacturing, high-precision photolithography equipment and precision photoresists are required to achieve fine lines and spacing.
Etching and etching
After the image transfer is completed, the next step is the etching and etching steps, which remove the unprotected portions of the copper foil, leaving the designed lines and gaps. In the manufacture of minimum gap PCBs, high-precision chemical etching and mechanical etching equipment are required to ensure the accuracy of small gaps and lines.
Drilling and Plating Holes
After completing the fabrication of the circuit, the next step is to drill and plate holes to create through holes and blind holes for electrical connections and component mounting. In the manufacture of minimum clearance PCBs, the accuracy and quality of drilled and plated holes is critical to ensure trace stability and reliability.
Surface treatment
The final step in minimum clearance PCB fabrication is surface preparation, including the application of solder mask and silkscreen layers. The solder mask is used to protect the circuits and reduce the risk of soldering shorts, while the silk screen is used to identify the location of components and circuits. During the surface treatment process, high-precision printing and coating equipment is required to ensure the smoothness and accuracy of the surface treatment layer.
By strictly controlling the precision and quality of each manufacturing step and employing advanced manufacturing equipment and technology, minimum clearance PCB manufacturers can produce high-quality, high-performance PCB boards that meet the needs of a variety of application fields.
The Application area of Minimum Clearance PCB.
Minimum clearance PCB technology is widely used in various electronic products, and its high performance, compact design and stable circuit characteristics make it the first choice in many industries. The following are the applications of minimum clearance PCB in different fields:
Mobile device
In the mobile device industry, such as smartphones, tablets, etc., minimum gap PCB technology is widely used. As consumer demand for mobile device functionality and performance continues to increase, circuit boards need to achieve higher levels of integration and more compact designs. Minimum clearance PCB technology makes it possible to accommodate more functional modules in a limited space, while improving the performance and response speed of the device.
Computers and network equipment
In the field of computers and network equipment, such as servers, routers, switches, etc., high-density circuit layout is crucial to achieve higher performance. Minimum gap PCB technology can help designers implement more functional modules in a limited space and reduce interference and cross-coupling between circuits, thereby improving the stability and reliability of the device.
Vehicle electronics
In the field of automotive electronics, such as on-board computers, driving assistance systems, etc., the requirements for compact design and stability of circuit boards are particularly prominent. The complex automotive environment places higher requirements on the reliability and stability of electronic equipment. Minimum clearance PCB technology can help designers achieve more compact designs, reduce the size and weight of circuit boards, while improving circuit stability and anti-interference capabilities.
Industrial control
In the field of industrial control, such as PLC (programmable logic controller), frequency converter, etc., the performance and reliability requirements of circuit boards are very strict. The complex industrial environment places higher requirements on the stability and durability of equipment. Minimum clearance PCB technology can help designers achieve higher density circuit layouts, thereby improving device performance and reliability.
Medical equipment
In the field of medical equipment, such as medical monitoring equipment, diagnostic equipment, etc., there are very high requirements for the stability and accuracy of circuit boards. Medical equipment usually needs to operate stably for a long time, which places higher requirements on the reliability and stability of the equipment. Minimum clearance PCB technology can help designers achieve higher density circuit layouts, thereby improving device performance and accuracy.
Overall, minimum clearance PCB technology plays an important role in various electronic products, providing strong support for product performance, reliability, and stability. As technology continues to advance and innovate, minimum gap PCB technology will continue to play an important role in future electronic product design.
What are the advantages of Minimum Clearance PCB?
Minimum gap PCB technology plays a vital role in modern electronic design, and the series of advantages it brings make it the first choice for many electronic product manufacturers. Here are a few advantages of minimum clearance PCBs:
Improve circuit performance
Minimum gap PCB technology can effectively reduce the distance between wires, thereby reducing circuit impedance, crosstalk and signal transmission delay. This can improve the response speed and stability of the circuit, making electronic products more reliable and efficient.
Optimize space utilization
By reducing the spacing between wires, minimum gap PCB technology enables higher-density circuit layouts to accommodate more functions and components in a limited space. This is especially important for compact electronic products, such as smartphones, wearable devices, etc.
Reduce manufacturing costs
Minimum clearance PCB technology can reduce the size of the PCB board, thereby reducing the required materials and manufacturing costs. In addition, the more compact design can also reduce the complexity of the welding and assembly processes, further reducing production costs.
Improve anti-interference ability
Since minimum gap PCB technology can reduce crosstalk and interference in the circuit, it can improve the anti-interference ability of the circuit. This is particularly important for electronic products that need to work in complex electromagnetic environments, such as industrial control equipment and communication equipment.
Enable innovative design
Minimum clearance PCB technology provides electronic designers with greater flexibility and freedom, allowing them to implement more complex and innovative designs. By implementing more functions and components in a limited space, designers can create more competitive products that meet changing market demands.
To sum up, minimum gap PCB technology can not only improve circuit performance and stability, but also optimize space utilization, reduce manufacturing costs, improve anti-interference capabilities, and provide the possibility for innovative designs. Therefore, for electronic product manufacturers who pursue high performance, high efficiency and innovation, adopting minimum gap PCB technology is a wise choice.
FAQ
How does minimum clearance PCB technology differ from traditional PCB design?
Traditional PCB designs often leave some clearance to ensure that signals do not interfere with each other or cause short circuits. Minimum gap PCB technology, on the other hand, aims to minimize the spacing between conductors to enable higher density layouts and more compact designs.
Do minimum clearance PCBs increase the risk of failure?
While minimum clearance PCB technology allows for more compact circuits, with careful design and appropriate manufacturing processes, it does not actually increase the risk of failure. Conversely, by minimizing signal transmission paths and lowering resistance, minimum clearance PCB technology can actually improve circuit stability and reliability.
How does a minimum clearance PCB affect the thermal performance of a circuit?
Minimum clearance PCB technology can make circuits more compact, but it can also increase heat build-up between components. Therefore, when designing a minimum clearance PCB, special consideration needs to be given to heat dissipation solutions to ensure the stability and long-term reliability of the circuit.
What types of electronics is minimum clearance PCB technology suitable for?
Minimum clearance PCB technology is suitable for almost all types of electronic products, especially those with high requirements on performance, size and power consumption. For example, smartphones, tablets, networking equipment, automotive electronics, and more can benefit from minimum clearance PCB technology.
Designing a minimum clearance PCB requires consideration of many factors, including signal integrity, thermal management, electromagnetic compatibility (EMC), manufacturing cost, and more. In particular, it is necessary to ensure that the minimum spacing between wires does not cause signal interference or short circuits, and the heat dissipation scheme needs to be properly planned to ensure stable operation of the circuit.