Mini Led PCB Substrate Manufacturer.A leading innovator in electronic component fabrication, specializing in mini LED PCB substrates, our company blends cutting-edge technology with precision engineering. With a steadfast commitment to quality, we craft substrates that redefine industry standards. Our expertise lies in designing and manufacturing compact PCBs optimized for mini LED applications, ensuring superior performance and durability. Through rigorous testing and meticulous attention to detail, we deliver reliable solutions tailored to meet the evolving demands of the LED market. Trust us as your partner for premium mini LED PCB substrates that elevate your products to new heights of excellence.
In today’s digital world, the rise of Mini LED technology has brought revolutionary changes to the display industry. As one of the core components supporting Mini LED technology, the manufacturing process and material selection of Mini LED PCB substrate are crucial. This article will delve into the role of Mini LED PCB substrate manufacturers and their key role in the production process. The manufacturing of Mini LED PCB substrate is not only a demonstration of technology, but also strict requirements for process and materials, because it is directly related to the performance and reliability of Mini LED display.
What is Mini LED PCB substrate?
Mini LED PCB substrate is an indispensable and important component of current Mini LED display technology. It plays a key role in connecting and supporting the Mini LED chip, providing a solid foundation for the stable operation of the display. This article will take an in-depth look at the definition, functions and materials used in the manufacturing process of Mini LED PCB substrates.
Mini LED PCB substrate is a key component for Mini LED displays. It provides a platform to connect Mini LED chips so that they can operate properly. Compared with traditional LED displays, Mini LED displays use smaller LED chips, so they require higher density connections and stronger support. Mini LED PCB substrate is designed to meet this demand.
Mini LED PCB substrates are usually made of specific materials that have excellent electrical conductivity and heat dissipation properties. Electrical conductivity is necessary to ensure the normal operation of the Mini LED chip, while excellent heat dissipation performance can effectively dissipate the generated heat to maintain the stability and long-term reliability of the Mini LED chip. Common Mini LED PCB substrate materials include FR-4 fiberglass boards and metal substrates, etc., which achieve a good balance between performance and cost.
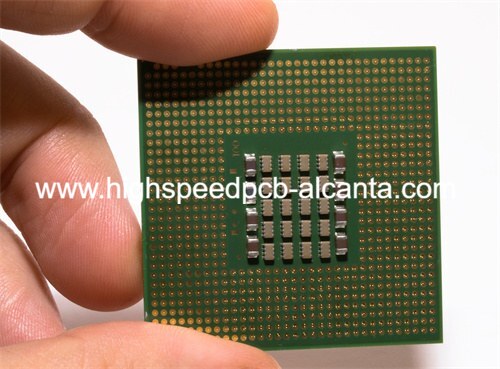
Mini Led PCB Substrate Manufacturer
In addition to material selection, the manufacturing process of Mini LED PCB substrate is also crucial. Manufacturers need to precisely design and manufacture Mini LED PCB substrates to ensure that they meet customer needs and standards. Every aspect of the manufacturing process requires strict control to ensure that the final Mini LED PCB substrate has excellent quality and reliability.
Overall, Mini LED PCB substrate plays a vital role in the development of Mini LED display technology. It not only provides a platform to connect and support Mini LED chips, but also ensures the stable operation and long-term reliability of the display. Through precision design and high-quality manufacturing, Mini LED PCB substrate provides solid support for the promotion and application of Mini LED display technology.
How is Mini LED PCB substrate designed?
The design process of Mini LED PCB substrate is a critical and complex stage, which directly affects the performance and reliability of the final product. Here’s what you need to know about the key steps in Mini LED PCB substrate design and how manufacturers ensure its performance and reliability.
Demand analysis: Manufacturers first need to fully communicate with customers to understand their needs and requirements. This may involve details such as display size, resolution, power consumption, cooling requirements, etc. At this stage, manufacturers need to ensure that the customer’s needs are accurately understood to provide clear direction for subsequent designs.
Circuit layout design: After clarifying customer needs, the manufacturer carries out circuit layout design. This includes placing Mini LED chips, capacitors, resistors and other components on the PCB substrate, and designing the circuit connection method. Designers need to consider layout compactness, signal transmission stability, and circuit optimization to ensure optimal overall performance.
Line width and spacing design: During the design process, manufacturers need to pay attention to the design of line width and spacing. Line width and spacing directly affect the electrical performance and reliability of PCB, so appropriate parameters need to be selected based on design requirements and manufacturing process.
Material selection: During the design stage, manufacturers need to select suitable materials to manufacture PCB substrates. This includes substrate material, copper thickness, solder mask ink, etc. The choice of materials directly affects the conductive performance, heat dissipation performance and durability of the PCB substrate, so it needs to be carefully considered.
Design for electromagnetic compatibility (EMC): During the design process, manufacturers also need to consider electromagnetic compatibility (EMC). Through proper layout and design, interference between circuits can be reduced and system stability and reliability improved.
Simulation and verification: After the design is completed, manufacturers typically perform simulation and verification. The electrical characteristics and signal transmission of the design are simulated and analyzed through simulation software to ensure that the design meets the expected performance requirements. At the same time, manufacturers will also conduct sample verification to test and evaluate the performance of PCB substrates.
Quality Control: Quality control is crucial throughout the design process. Manufacturers need to strictly control the quality of every link to ensure that every detail of the PCB substrate meets the design requirements and standards. This includes the quality of materials, the accuracy of processing techniques, and functional testing of the final product.
Through the above key steps, manufacturers can ensure that the design of Mini LED PCB substrate meets customer needs and has excellent performance and reliability. This not only provides customers with high-quality products, but also provides solid support for the promotion and application of Mini LED technology.
What is the manufacturing process of Mini LED PCB substrate?
The manufacturing process of Mini LED PCB substrate is a precise and complex project, which involves multiple key links from raw material preparation to final testing. Manufacturers need to strictly control every step to ensure that the final Mini LED PCB substrate is of high quality and reliability.
First, the manufacturing process begins with the preparation of raw materials. At this stage, manufacturers must carefully select and purchase materials that meet the requirements, including substrate materials, copper foil, insulation layers, solder paste, etc. The quality of these materials directly affects the performance and reliability of the final product.
Next is the design and fabrication of the circuit board. Manufacturers will design circuit layouts based on customer requirements and application scenarios, and use CAD software for simulation and optimization. Then, the designed circuit pattern is printed on the substrate through the printed circuit board (PCB) process to form the basic circuit structure.
This is followed by chemical processing and electroplating stages. At this stage, the manufacturer chemically treats the printed circuits to remove excess copper and protect the circuit surface. Then, a layer of protective metal is electroplated on the surface of the line to enhance conductivity and corrosion resistance.
After chemical processing and electroplating are completed, the next step is drilling and appearance processing. Manufacturers use drill presses to drill holes into circuit boards for mounting components and connecting wiring. The surface of the board is then given a cosmetic finish, including removing residue, sanding and cleaning to make the surface smooth and flat.
Finally comes the testing phase. At this stage, the manufacturer will conduct strict inspection and testing on each manufacturing link to ensure that the quality of the Mini LED PCB substrate meets standard requirements. Including visual inspection, electrical testing, welding reliability testing, etc. to ensure the stability and reliability of the product.
Manufacturers ensure that every link reaches high standards through strict quality control and inspection processes throughout the manufacturing process. At the same time, they are constantly optimizing manufacturing processes and improving equipment technology to meet the ever-increasing needs and expectations of customers.
In general, the manufacturing process of Mini LED PCB substrate is a complex and precise process, which requires manufacturers to have professional technology and experience, and strictly control the quality of each link to ensure the performance and reliability of the final product. customer’s request.
How much does it cost to manufacture Mini LED PCB substrate?
The cost of manufacturing Mini LED PCB substrate is a complex issue affected by multiple factors. Here are some factors that may affect the cost of Mini LED PCB substrate, as well as thoughts on whether high-quality Mini LED PCB substrate means higher costs.
The material cost of Mini LED PCB substrate is usually an important part of the manufacturing cost. Different types of substrate materials, such as FR-4 fiberglass panels and metal substrates, may have different costs. High-performance materials and special processes may increase material costs.
The processes and technologies required to manufacture Mini LED PCB substrates will also have an impact on costs. Some complex processes, such as multilayer board manufacturing and surface assembly technology, may increase manufacturing costs. At the same time, high-precision and highly automated production lines may increase equipment and labor costs.
The scale of manufacturing Mini LED PCB substrates will also affect the cost. Generally speaking, mass production reduces the production cost per substrate because fixed costs can be spread over more volumes.
High-quality Mini LED PCB substrates often require more stringent quality control and testing processes. This may include more inspection steps, more sophisticated equipment and a higher level of labor, thereby increasing costs.
The final cost is also affected by customer demand. Customized requirements, special design requirements or urgent delivery times may result in additional costs.
For Mini LED PCB substrates, high quality often means higher costs, but it is not absolute. Higher-quality substrates may use more durable, more reliable materials and employ more rigorous production and testing processes, which can increase manufacturing costs. However, high-quality substrates typically have longer life and more consistent performance, which may result in lower overall costs in the long run because repairs and replacements are less frequent.
In general, the cost of Mini LED PCB substrate is affected by many factors, including materials, processes, scale, quality control and customer needs. When balancing cost and quality, manufacturers need to consider a variety of factors to meet customer needs and remain competitive.
What material is Mini LED PCB substrate usually made of?
During the manufacturing process of Mini LED PCB substrate, some specific materials are usually selected, which are designed to ensure the performance and reliability of Mini LED display. The following are some common Mini LED PCB substrate materials and their performance and characteristics:
Performance characteristics: FR-4 fiberglass board is a common substrate material with good insulation properties and mechanical strength. It is resistant to high temperatures and corrosion, and is relatively affordable.
Applicable scenarios: It is suitable for general Mini LED display applications, can meet most needs, and is a common choice for manufacturers and customers.
Performance characteristics: Metal substrates usually use aluminum substrates or copper substrates, which have excellent heat dissipation and conductive properties. They can effectively conduct heat from the LED chip to the surrounding environment, improving the stability and lifespan of the Mini LED display.
Applicable scenarios: Suitable for Mini LED displays that require high heat dissipation performance, such as high-brightness and high-density display applications.
Performance characteristics: Ceramic substrate has excellent insulation performance and high temperature resistance, and can work stably in extreme environments. They also have a low coefficient of linear expansion, which helps keep the connection between the Mini LED chip and the substrate stable.
Applicable scenarios: Mini LED displays are suitable for use in special environments, such as automobiles, aerospace and other fields that have high temperature and environmental requirements.
Performance characteristics: High-frequency circuit board materials have excellent high-frequency performance and signal transmission characteristics, and can meet the needs of Mini LED displays for high-speed signal transmission. They usually have lower dielectric constant and dielectric loss, which helps improve the stability and reliability of signal transmission.
Applicable scenarios: Suitable for Mini LED displays with high signal transmission requirements, such as high-definition and high-refresh rate video display applications.
The above are some common Mini LED PCB substrate materials and their performance characteristics. Manufacturers need to make comprehensive considerations based on customer needs and application scenarios when selecting materials to ensure that the final Mini LED display has excellent performance and stability.
Who manufactures Mini LED PCB substrate?
The rapid development of Mini LED technology has continued to increase the demand for Mini LED PCB substrates. In this area, manufacturer choice is crucial. So, who is making Mini LED PCB substrates? For our company, we play this role as a supplier.
As a professional Mini LED PCB substrate manufacturer, our company is committed to providing high-quality, reliable Mini LED PCB substrates. We have advanced manufacturing equipment and rich experience to meet the customized requirements of customers’ different needs.
Our manufacturing process strictly follows international standards. From raw material procurement to final product delivery, every link undergoes strict quality control and testing. We select high-quality materials and adopt advanced production processes to ensure that Mini LED PCB substrates have excellent performance and reliability.
We have established long-term and stable cooperative relationships with our customers, and have won the trust and praise of our customers by responding to customer needs in a timely manner, providing customized solutions, ensuring product quality and providing excellent after-sales service.
Today, as Mini LED technology continues to develop, we will continue to uphold the spirit of professionalism, integrity, and innovation, provide customers with better quality Mini LED PCB substrates, and jointly promote the development and application of Mini LED technology.
By cooperating with our company, you will receive high-quality Mini LED PCB substrates, as well as professional technical support and excellent customer service. We look forward to working with you to create a better future!
What are the five qualities of great customer service?
When it comes to how Mini LED PCB manufacturers provide excellent customer service, the key lies in how they meet their customers’ needs and provide an experience that exceeds expectations. Here are five traits that define great customer service:
Responsive: Excellent customer service means responding promptly to customer inquiries, questions, and needs. Mini LED PCB manufacturers should ensure that customers’ emails, phone calls or online messages are responded to in a timely manner so that customers can get solutions in the shortest possible time.
Customized service: Every customer has unique needs and challenges, and excellent customer service includes providing customized solutions. Manufacturers should have a deep understanding of customer needs and provide personalized products and services based on their specific requirements and application scenarios.
Quality Assurance: Excellent customer service means not only providing quality products, but also providing reliable quality assurance. Mini LED PCB manufacturers should strictly control product quality to ensure compliance with customer standards and provide appropriate warranty and after-sales service.
Technical support: Mini LED PCB manufacturing involves complex technologies and processes, and customers may need professional technical support and guidance. Excellent customer service includes providing timely and accurate technical support to help customers solve problems and improve production efficiency.
After-sales service: Excellent customer service lies not only in the sales process, but also in after-sales service. Manufacturers should provide timely after-sales support to solve problems encountered by customers during use and ensure customer satisfaction.
To sum up, excellent customer service is one of the keys to success for Mini LED PCB manufacturers. Through responsiveness, customized service, quality assurance, technical support and after-sales service, manufacturers can win the trust and respect of their customers, foster long-term relationships, and stand out in a highly competitive market.
FAQS
How long is the production cycle of Mini LED PCB substrate?
The production cycle of Mini LED PCB substrate varies depending on the manufacturer and order volume. Typically, the production cycle for small batch orders may only take a few days to about a week, while large batch orders may take several weeks. Production cycles are also affected by the specific processes and material supply chains required in the manufacturing process. It is recommended to communicate with the manufacturer before placing an order to understand the specific production cycle.
What is the best material for Mini LED PCB substrate?
The best material for Mini LED PCB substrate depends on application needs and budget constraints. Common materials include FR-4 fiberglass panels and metal substrates. FR-4 fiberglass panels have good insulation properties and mechanical strength, making them suitable for most applications. Metal substrates have excellent thermal conductivity and are suitable for applications that require higher heat dissipation effects, but the cost is also higher. Factors such as thermal conductivity, electrical performance, cost and manufacturing complexity need to be considered when selecting materials.
How to choose Mini LED PCB manufacturer?
When choosing a Mini LED PCB manufacturer, the following factors should be considered: the manufacturer’s manufacturing capabilities and experience, the advanced level of production equipment, quality control system, after-sales service level, and communication efficiency with the manufacturer. It is recommended to conduct market research, find multiple manufacturers to compare, and choose the partner that best matches your needs.
How to ensure the quality of Mini LED PCB substrate?
Manufacturers adopt strict quality control measures during the production process to ensure the quality of Mini LED PCB substrates. This includes strict screening and testing of raw materials, quality control during the production process, and comprehensive testing of finished products. In addition, manufacturers usually follow ISO quality management systems and industry standards to ensure that products meet customer quality requirements and standards.
How about the after-sales service of Mini LED PCB substrate?
Most manufacturers provide comprehensive after-sales services, including technical support, product repair and replacement, etc. Customers can contact the manufacturer’s customer service team at any time for technical consultation and solution support. During the cooperation process, it is recommended to establish a good communication mechanism, promptly feedback problems and seek solutions to ensure ultimate customer satisfaction.