Mini Ceramics PCB Manufacturing.Cross blind/buried vias PCB manufacturing involves the intricate process of creating circuit boards with vias that connect multiple layers while remaining hidden from view. This advanced technique requires precise drilling and plating methods, ensuring optimal conductivity and reliability. Through careful design and fabrication, these vias enable complex interconnections without compromising the integrity of the board. Manufacturers utilize sophisticated equipment and meticulous quality control measures to achieve the desired outcome. The result is a high-density PCB with enhanced functionality, suitable for a wide range of applications demanding compactness and performance.
In the field of modern electronics, PCB (Printed Circuit Board) plays a crucial role. As the basic structure that connects and supports electronic components, the design and manufacturing process of PCB is crucial. Mini Ceramics PCB, with its unique materials and characteristics, shows important application advantages in special environments. This article will delve into the manufacturing process of Mini Ceramics PCB, covering multiple aspects such as design, manufacturing, cost, materials and customer service, and answer related common questions to help readers better understand and apply knowledge in this field.
What is Mini Ceramics PCB?
Mini Ceramics PCB (Mini Ceramics Printed Circuit Board) is a printed circuit board made of tiny ceramic materials used to support and connect electronic components. Compared with traditional fiberglass materials, Mini Ceramics PCB uses special micro ceramic materials, such as alumina (Alumina) or aluminum nitride (AlN). These ceramic materials have excellent thermal conductivity, high temperature resistance, corrosion resistance and mechanical strength, giving Mini Ceramics PCB important advantages in some special application fields.
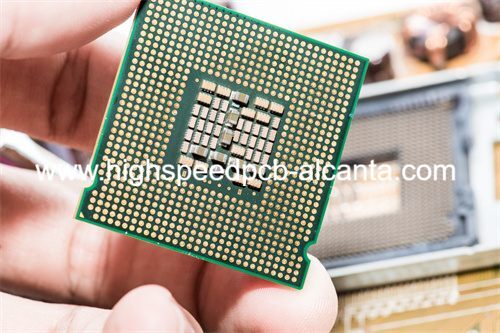
Mini Ceramics PCB manufacturing
First of all, Mini Ceramics PCB uses micro-ceramic materials, which have higher thermal conductivity compared with traditional fiberglass materials. This means that Mini Ceramics PCB can more effectively disperse the heat generated by electronic devices, thereby improving the cooling efficiency of the entire system. This is particularly important for high-performance electronics, radio frequency (RF) applications, and high-power circuits.
Secondly, the high temperature resistance of Mini Ceramics PCB is also one of its unique advantages. In some high-temperature environments, traditional fiberglass PCBs may experience performance degradation or even failure, while Mini Ceramics PCBs can stably work in a higher temperature range, ensuring system stability and reliability.
In addition, Mini Ceramics PCB has excellent corrosion resistance and mechanical strength, making it more reliable for applications in harsh environments. Whether in industrial environments with high chemical exposure or in harsh conditions such as marine or aerospace, Mini Ceramics PCBs can maintain stable performance and extend the life of electronic equipment.
In summary, Mini Ceramics PCB provides a reliable solution for the design and manufacturing of electronic devices by using special micro ceramic materials. Its excellent thermal conductivity, high temperature resistance, corrosion resistance and mechanical strength make it widely used in many fields and has become one of the first choices for many high-performance electronic devices.
How to design Mini Ceramics PCB?
Designing a Mini Ceramics PCB is a complex and critical process that requires the consideration of multiple factors to ensure the performance and reliability of the final product. The following will discuss in detail the factors to consider when designing Mini Ceramics PCB, the tools and software used, and the key points to focus on during the design process.
First of all, when designing Mini Ceramics PCB, engineers need to have an in-depth understanding of the application scenarios and requirements. This includes a thorough understanding of circuit functionality, operating environment, reliability requirements, etc. Considering the special materials and uses of Mini Ceramics PCB, special attention must be paid to its temperature resistance, corrosion resistance and mechanical strength requirements.
Secondly, professional PCB design software needs to be used during the design process to achieve design and layout. Commonly used software includes Altium Designer, Cadence Allegro, etc., which provide a wealth of functions and tools to help engineers implement complex design and wiring. Through these software, engineers can perform circuit layout, signal path planning, heat dissipation design, etc. to ensure the rationality and stability of the design.
When designing Mini Ceramics PCBs, there are several key points that require special attention. The first is circuit layout and signal integrity. Since Mini Ceramics PCB is often used in high-frequency or high-temperature environments, attention must be paid to the stability and reliability of signal transmission. Reasonable layout and routing can minimize signal interference and crosstalk and ensure the stability of circuit performance.
Another focus is thermal design. Mini Ceramics PCBs are usually used in high-temperature environments, so good heat dissipation design is crucial to keep the circuit running stably. Engineers need to design appropriate heat dissipation structures and heat dissipation paths to ensure that Mini Ceramics PCB can work properly and maintain a stable temperature under high temperature conditions.
Additionally, manufacturing feasibility and cost-effectiveness need to be taken into consideration during the design process. Engineers should choose appropriate materials and processes based on actual conditions to ensure the practicality and producibility of the design. While designing, it is also necessary to pay close attention to cost factors to reduce manufacturing costs as much as possible and improve product competitiveness.
To sum up, designing Mini Ceramics PCB is a complex process that takes multiple factors into consideration. Through reasonable design and professional tool support, engineers can achieve high-quality Mini Ceramics PCB design to meet the needs of different application scenarios.
What is the manufacturing process of Mini Ceramics PCB?
The manufacturing process of Mini Ceramics PCB is a complex and precise project involving multiple key steps, each of which is crucial and affects the quality and performance of the final product. The manufacturing process of Mini Ceramics PCB and its importance will be introduced in detail below:
Before manufacturing Mini Ceramics PCB, you first need to prepare the required materials, including ceramic substrate, metallization materials, insulation layers, etc. The selection and quality of materials directly affects the performance and stability of the final product.
Before proceeding with actual manufacturing, the PCB design needs to be verified. This step includes review and verification of design documents to ensure compliance with customer needs and specifications. Through design verification, unnecessary errors and problems can be avoided during the manufacturing process.
Printing is one of the key steps in manufacturing Mini Ceramics PCBs. At this stage, the designed circuit pattern is printed onto the ceramic substrate. The quality of printing directly affects the reliability and stability of circuit connections.
Sintering is an important step in the Mini Ceramics PCB manufacturing process. At high temperatures, the printed circuit pattern and ceramic substrate are bonded together to form a stable structure. The temperature and time need to be strictly controlled during the sintering process to ensure the adhesion and stability between the ceramic substrate and circuit layer.
Metalization is a critical step in imparting conductivity to Mini Ceramics PCBs. After sintering, a metal layer is coated on the surface of the circuit pattern through a metallization process to achieve the conductive function of the circuit. The quality of metallization directly affects the performance and reliability of Mini Ceramics PCB.
After metallization is completed, the Mini Ceramics PCB needs to be surface treated to improve its corrosion resistance and solderability. Surface treatment includes steps such as cleaning and applying a protective layer to ensure that the final product has good surface quality and stability.
Quality inspection is an integral part of the Mini Ceramics PCB manufacturing process. Through strict quality inspection, the size, appearance, electrical properties and other indicators of the products are tested to ensure that each product meets the specifications and customer needs. The results of quality inspection directly determine whether the product is qualified or not, affecting the reliability and quality reputation of the product.
Throughout the entire Mini Ceramics PCB manufacturing process, strictly controlling the quality and stability of each step and taking effective quality management measures are the keys to ensuring the quality and performance of the final product. Only through careful design and precision manufacturing can we produce high-quality, reliable Mini Ceramics PCB products that meet customer needs and expectations.
How much does it cost to manufacture Mini Ceramics PCB?
The cost of manufacturing Mini Ceramics PCBs is a complex issue involving many factors. First, let’s explore how these factors affect cost and compare the cost difference between Mini Ceramics PCBs and traditional PCBs.
Mini Ceramics PCBs use high-performance ceramic materials that are generally more expensive than traditional fiberglass board materials. The price of ceramic materials is affected by supply and demand, which can also have a significant impact on the final cost.
The design of Mini Ceramics PCBs may require more engineer and design time, especially when considering the characteristics of ceramic materials and processes. Complex designs may require more layers and special process steps, which increase manufacturing costs.
Manufacturing Mini Ceramics PCBs may require special processes and equipment to accommodate the characteristics of the ceramic material. These processes may require additional investment and higher operating costs, impacting the final manufacturing cost.
The quantity manufactured also has a significant impact on cost. Generally speaking, high-volume production can reduce the cost per unit, while low-volume production may result in higher unit costs.
Compared with traditional fiberglass PCB, the manufacturing cost of Mini Ceramics PCB is usually slightly higher. This is mainly because ceramic materials cost more and the manufacturing process may require more process steps and specialized equipment. However, it should be noted that Mini Ceramics PCB usually has higher temperature resistance, corrosion resistance and mechanical strength, and is suitable for applications in some special environments. So while the manufacturing cost is higher, the performance and reliability are often worth it.
To sum up, the cost of manufacturing Mini Ceramics PCB is affected by many factors, including material cost, design complexity, manufacturing process and quantity, etc. Mini Ceramics PCBs typically cost slightly more than traditional PCBs, but their performance and features often provide more reliable solutions for demanding applications. Therefore, although the manufacturing cost may be higher, in some specific scenarios, the manufacturing cost of Mini Ceramics PCB is a worthwhile investment.
What materials are Mini Ceramics PCBs made of?
Mini Ceramics PCB usually uses high-performance ceramic materials, mainly including alumina (Alumina) and aluminum nitride (AlN). These materials have unique advantages in electronic applications and are therefore widely used in the manufacture of Mini Ceramics PCBs.
First, alumina is a common ceramic material with excellent thermal conductivity and insulation. Its excellent thermal conductivity allows Mini Ceramics PCB to work stably in high temperature environments, while its insulation ensures the safety and reliability of the circuit. In addition, aluminum oxide has good corrosion resistance and can withstand the attack of chemicals and humidity, thus extending the life of electronic equipment.
In addition, aluminum nitride is a new type of high-performance ceramic material with excellent thermal conductivity and mechanical strength. Compared with aluminum oxide, aluminum nitride has higher thermal conductivity and better wear resistance, allowing Mini Ceramics PCB to perform well in more demanding working environments. In addition, aluminum nitride also has a low dielectric constant and dielectric loss, which is beneficial to improving the quality and speed of signal transmission, thereby improving the performance of electronic equipment.
In general, the ceramic materials such as aluminum oxide and aluminum nitride used in Mini Ceramics PCB have excellent thermal properties, electrical properties and chemical stability, and are suitable for various electronic applications in high temperature, high frequency and corrosive environments. Their wide application provides more possibilities for the design and manufacturing of electronic equipment, and also provides an important guarantee for improving the performance and reliability of electronic equipment.
Who makes Mini Ceramics PCBs?
In the field of Mini Ceramics PCB manufacturing, manufacturer selection is crucial to product quality and performance. In this field, our company is one of the leading manufacturers.
Our company is a leading enterprise specializing in Mini Ceramics PCB manufacturing. With years of experience and expertise, we are committed to providing customers with high-quality, reliable Mini Ceramics PCB solutions.
We have advanced production equipment and technical team to meet Mini Ceramics PCB production needs of various specifications and requirements. Our manufacturing process is carried out in strict accordance with international standards, ensuring that each product has stable performance and reliability.
During the manufacturing process, we strictly control every link, including raw material procurement, production process control and quality inspection. We use advanced testing equipment and technology to ensure that our products meet customer requirements and standards.
As a professional Mini Ceramics PCB manufacturer, we focus on communication and cooperation with customers. We provide a full range of customer services, including technical support, customization needs and after-sales service, to ensure that customers can receive satisfactory solutions and experiences.
We are committed to providing customers with high-quality, reliable Mini Ceramics PCB products that meet their needs and expectations. We will continue to strive to improve and innovate to provide customers with better products and services.
As a leader in the field of Mini Ceramics PCB manufacturing, we will continue to be committed to technological innovation and quality improvement to provide customers with the highest quality products and services. Looking forward to cooperating with you to achieve a win-win situation together!
Five traits of great customer service
Excellent customer service is one of the keys to business success, especially in a highly competitive and technical field like the Mini Ceramics PCB manufacturing industry. Here are five traits of great customer service, along with what they look like in this industry and how to ensure high levels of service:
One of the core components of great customer service is communicating with customers promptly and clearly. In the Mini Ceramics PCB manufacturing industry, the importance of communication is particularly prominent. During the manufacturing process, customers may have specific requirements or needs, and clear communication can help companies better understand and meet these needs. Through timely communication, you can ensure that customers have a clear understanding of the progress of their orders, reducing misunderstandings and unnecessary doubts, thereby enhancing customer satisfaction.
In the Mini Ceramics PCB manufacturing industry, the market is highly competitive and orders usually need to be completed quickly. Therefore, responding quickly to customer inquiries and questions is crucial. Promptly reply to customers’ emails, phone calls or online messages, and provide real-time support and solutions, which can enhance customers’ trust in the company. By maintaining efficient response times, companies can win the trust of customers and maintain a competitive advantage in the market.
Great customer service requires empathy, the ability to understand your customers’ needs and provide solutions accordingly. In the Mini Ceramics PCB manufacturing industry, customers may face various challenges and needs, such as adjustments to product specifications, processing of emergency orders, etc. Listening to customers’ feedback and opinions, paying attention to and solving their problems and concerns, can enhance the mutual trust relationship between customers and enterprises and promote long-term cooperation.
Another important trait of great customer service is reliability. Customers expect to receive high-quality products within the promised timeframe and to be able to rely on businesses to provide ongoing support and service. In the Mini Ceramics PCB manufacturing industry, by establishing a sound production process and quality management system, companies can ensure product quality and on-time delivery. At the same time, establishing a good after-sales service system and handling customer complaints and problems in a timely manner are also key to ensuring reliability.
Excellent customer service requires treating customers with professionalism, courtesy, and efficiency. In the Mini Ceramics PCB manufacturing industry, professionalism is reflected in many aspects, including technical support, engineering design, production process control, etc. Providing professional suggestions and solutions, as well as timely technical support, can enhance customers’ trust in the enterprise and improve customer satisfaction.
Through the implementation of the above measures, Mini Ceramics PCB manufacturing companies can improve customer service levels, establish a good corporate image, and win the trust and support of customers.
Frequently Asked Questions
What are the advantages of Mini Ceramics PCB compared to traditional PCBs?
Mini Ceramics PCBs offer several advantages over traditional PCBs. Firstly, they are made from ceramic materials, which provide higher thermal conductivity and better resistance to corrosion and wear. This makes them ideal for applications requiring high temperature operation or exposure to harsh environments. Additionally, Mini Ceramics PCBs can achieve higher circuit densities and better signal integrity due to their excellent dielectric properties.
What factors influence the cost of manufacturing Mini Ceramics PCBs?
The cost of manufacturing Mini Ceramics PCBs depends on various factors, including the complexity of the design, the type and quality of ceramic materials used, production volume, and the chosen manufacturing processes. Generally, Mini Ceramics PCBs may have slightly higher manufacturing costs compared to traditional PCBs due to the specialized materials and processes involved.
How long does it typically take to manufacture Mini Ceramics PCBs?
The manufacturing lead time for Mini Ceramics PCBs can vary depending on factors such as the complexity of the design, the availability of materials, and the production capacity of the manufacturer. Generally, it can range from a few days to several weeks. It’s essential to work closely with the manufacturer to establish realistic timelines and ensure timely delivery of the PCBs.
What are the key considerations when selecting a Mini Ceramics PCB manufacturer?
When selecting a Mini Ceramics PCB manufacturer, several factors should be considered. These include the manufacturer’s experience and expertise in working with ceramic materials, their production capabilities and quality control processes, their track record of delivering high-quality products on time, and their ability to provide responsive customer support and technical assistance.