Millimeter Wave Antenna Board Manufacturer.Millimeter Wave Antenna Board Manufacturer specializes in producing high-frequency antenna boards for advanced communication systems. Utilizing cutting-edge technology and precision engineering, they deliver top-quality, reliable solutions for 5G, satellite, and radar applications. Their expertise ensures optimal performance and innovation, meeting the demands of the rapidly evolving millimeter wave industry.
Millimeter Wave (mmWave) technology is rapidly gaining prominence in various high-frequency applications, including telecommunications, automotive radar, and imaging systems. The core of mmWave technology is the mmWave antenna board, a specialized printed circuit board (PCB) designed to operate at frequencies typically ranging from 30 GHz to 300 GHz. In this article, we will explore the characteristics, design considerations, materials, manufacturing processes, applications, and advantages of mmWave antenna boards, highlighting their significance in advancing high-frequency communications and sensing technologies.
What is a Millimeter Wave Antenna Board?
A Millimeter Wave Antenna Board is a type of PCB specifically engineered to support the transmission and reception of mmWave signals. These boards are designed to handle the unique challenges associated with mmWave frequencies, such as higher signal attenuation, increased signal loss, and precise signal routing requirements. The design and fabrication of mmWave antenna boards require meticulous attention to detail to ensure optimal performance and reliability.
Characteristics of Millimeter Wave Antenna Boards
Millimeter Wave Antenna Boards possess several critical characteristics that make them suitable for high-frequency applications:
mmWave antenna boards are designed to operate efficiently at frequencies between 30 GHz and 300 GHz, enabling high-speed data transmission and precise sensing capabilities.
The boards are constructed using low-loss materials to minimize signal attenuation and ensure efficient transmission and reception of mmWave signals.
The layout of mmWave antenna boards is meticulously designed to maintain signal integrity and red
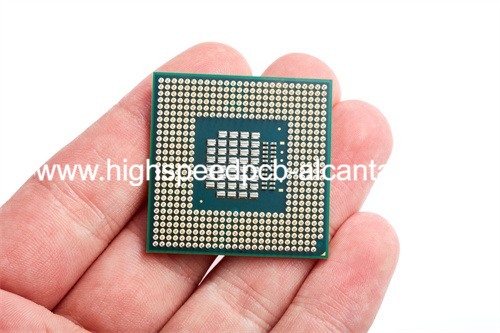
Millimeter Wave Antenna Board Manufacturer
uce losses. This includes precise trace geometries, controlled impedance, and minimal parasitic elements.
Due to the high frequencies involved, mmWave antenna boards are typically compact in size, allowing for integration into small and lightweight devices.
Effective thermal management is crucial in mmWave applications to prevent overheating and ensure reliable performance. The boards often incorporate thermal vias, heat sinks, and other cooling mechanisms.
Design Considerations for Millimeter Wave Antenna Boards
Designing mmWave antenna boards involves several key considerations to achieve optimal performance:
Choosing the right materials is critical for mmWave antenna boards. High-frequency laminates such as Rogers, Taconic, and PTFE-based materials are commonly used due to their low dielectric constant and low loss characteristics.
The design of the antenna elements, including their shape, size, and arrangement, plays a crucial role in determining the board’s performance. Common antenna designs for mmWave applications include patch antennas, dipole antennas, and array antennas.
Ensuring proper impedance matching is essential to minimize signal reflections and maximize power transfer. This involves designing transmission lines with controlled impedance and using matching networks if necessary.
Maintaining signal integrity at mmWave frequencies requires careful consideration of trace widths, spacing, and routing. Signal integrity simulations and testing are often performed to optimize the design.
Efficient thermal management is essential to prevent performance degradation due to overheating. This includes incorporating thermal vias, heat sinks, and other cooling mechanisms into the board design.
Proper shielding and grounding techniques are employed to minimize electromagnetic interference (EMI) and crosstalk, ensuring reliable signal transmission.
Materials Used in Millimeter Wave Antenna Boards
The choice of materials for mmWave antenna boards is crucial to achieving the desired performance:
Materials such as Rogers RT/duroid, Taconic TLY, and PTFE-based laminates are commonly used due to their low dielectric constant and low loss characteristics. These materials ensure minimal signal attenuation and distortion.
Copper is the primary conductive material used for traces and pads due to its excellent electrical conductivity. Surface finishes such as gold or silver are often applied to enhance performance and reliability.
Advanced dielectric materials with low loss and stable dielectric properties are used to provide insulation between conductive layers while maintaining signal integrity.
Materials with high thermal conductivity, such as thermal vias and heat sinks, are incorporated to dissipate heat effectively and prevent overheating.
Manufacturing Process of Millimeter Wave Antenna Boards
The manufacturing process of mmWave antenna boards involves several precise steps to ensure high quality and performance:
The design phase involves creating detailed schematics and layouts using computer-aided design (CAD) software. Signal integrity and thermal simulations are performed to optimize the board design.
Appropriate substrate and conductive materials are selected based on the design requirements and performance specifications.
Multiple layers of substrate and conductive materials are laminated together to form a multilayer structure. Precise alignment and control are essential to ensure the layers are properly bonded and aligned.
The circuit patterns are created using photolithographic processes. A photosensitive film (photoresist) is applied to the copper surface, exposed to ultraviolet (UV) light through a mask, and developed to reveal the desired circuit patterns. The PCB is then etched to remove the unwanted copper, leaving behind the traces and pads.
Vias are drilled into the PCB to create vertical electrical connections between different layers. These holes are then plated with copper to establish conductive pathways.
Surface finishes such as ENIG (Electroless Nickel Immersion Gold) or immersion silver are applied to the contact pads to enhance solderability and protect the conductive traces from oxidation and corrosion.
The final PCBs undergo assembly, where antenna elements, connectors, and other components are added. Rigorous testing, including signal integrity tests, impedance matching tests, and environmental stress tests, are conducted to ensure the PCBs meet the required performance standards.
Applications of Millimeter Wave Antenna Boards
Millimeter Wave Antenna Boards are used in a wide range of high-frequency applications:
mmWave technology is essential for the deployment of 5G networks, enabling high-speed data transmission and low latency. mmWave antenna boards are used in base stations, user devices, and backhaul links.
mmWave radar systems are used in advanced driver assistance systems (ADAS) for collision avoidance, lane departure warning, and adaptive cruise control. The high resolution and accuracy of mmWave radar make it ideal for automotive applications.
mmWave technology is used in imaging systems for security screening, medical imaging, and industrial inspection. The high-frequency signals can penetrate materials and provide detailed images with high resolution.
mmWave antenna boards are used in satellite communication systems and aerospace applications, where high-frequency signals are required for data transmission and remote sensing.
mmWave technology is used in military and defense applications for radar systems, communication systems, and electronic warfare. The high-frequency signals provide enhanced detection and communication capabilities.
Advantages of Millimeter Wave Antenna Boards
Millimeter Wave Antenna Boards offer several advantages that make them indispensable in high-frequency applications:
The ability to operate at high frequencies enables mmWave antenna boards to support extremely high data rates, making them ideal for applications requiring fast and reliable data transmission.
The high-frequency operation allows for the design of compact and lightweight antenna boards, enabling integration into small and portable devices.
The precise design and low-loss materials used in mmWave antenna boards ensure accurate and reliable signal transmission, essential for high-performance applications.
mmWave antenna boards can be customized to accommodate a wide range of applications, from telecommunications to automotive radar and imaging systems.
The robust construction and advanced materials used in mmWave antenna boards ensure long-term reliability and durability, even in demanding environments.
FAQ
What materials are commonly used in mmWave antenna boards?
Common materials used in mmWave antenna boards include high-frequency laminates such as Rogers RT/duroid, Taconic TLY, and PTFE-based materials. Copper is used for conductive traces, often with surface finishes like gold or silver to enhance performance and reliability.
How do mmWave antenna boards improve telecommunications?
mmWave antenna boards improve telecommunications by enabling high-speed data transmission and low latency, essential for 5G networks. The high-frequency operation allows for increased bandwidth and capacity, supporting more users and higher data rates.
Can mmWave antenna boards be used in automotive applications?
Yes, mmWave antenna boards are used in automotive radar systems for advanced driver assistance systems (ADAS). The high-frequency signals provide high resolution and accuracy, essential for collision avoidance, lane departure warning, and adaptive cruise control.
What are the common applications of mmWave antenna boards in imaging systems?
In imaging systems, mmWave antenna boards are used for security screening, medical imaging, and industrial inspection. The high-frequency signals can penetrate materials and provide detailed images with high resolution, enabling accurate and reliable imaging in various applications.