Military Circuit Board Manufacturer.A leading military circuit board manufacturer, boasting cutting-edge technology and rigorous quality control measures, ensures reliability in the most demanding environments. With a specialized focus on defense applications, they engineer intricate circuitry tailored to withstand extreme conditions, from battlefield operations to aerospace missions. Their expertise encompasses advanced materials and precision assembly techniques, adhering to strict military standards for performance and durability. Collaborating closely with defense agencies, they deliver bespoke solutions vital for modern warfare, reinforcing communication systems, weaponry, and surveillance infrastructure with the resilience necessary for mission success.
In modern warfare and defense systems, the role of military circuit boards is crucial. These complex electronic components are the basis of advanced weapons, communications systems and surveillance equipment and are used by militaries around the world. In this comprehensive guide, we delve into the complexities of military circuit board manufacturing, revealing the processes, materials, and important considerations that shape key aspects of this military technology.
What is a military circuit board?
In modern warfare and defense systems, the role of military circuit boards is crucial. These sophisticated electronic components are at the heart of military equipment and provide critical support for advanced weapons, communications systems and surveillance equipment. But what exactly is a military circuit board?
In short, Military Printed Circuit Boards are circuit boards designed and manufactured specifically for military applications. They offer higher reliability, durability and immunity to interference than commercial circuit boards to meet the stringent requirements of military environments.
Military circuit boards play a key role in modern military equipment. In advanced weapons systems, such as missiles, fighter aircraft, and tanks, military circuit boards are responsible for controlling and coordinating various functions such as navigation, communications, weapons control, and target identification. In addition, in military communication systems, military circuit boards carry the important task of confidential communication and data transmission, ensuring safe and reliable information exchange between armies. In surveillance equipment and reconnaissance equipment, military circuit boards help achieve high-resolution image processing, target tracking and intelligence collection, providing necessary intelligence support for battlefield decision-making.
The design and manufacturing of military circuit boards requires strict compliance with military standards and specifications. They must be able to withstand harsh environmental conditions such as heat, humidity, vibration and electromagnetic interference. At the same time, military circuit boards must also have a high degree of reliability and stability to ensure long-term operation under extreme conditions. To meet these requirements, military circuit boards often use special materials and processes, such as high-temperature tolerant substrates, metallization, and overlay protection.
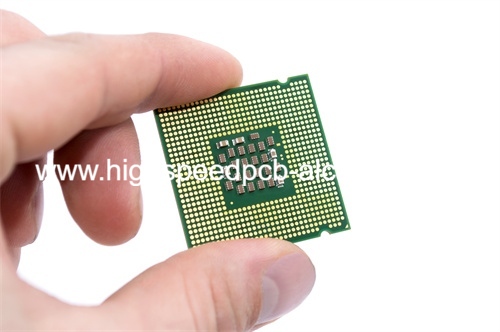
Military circuit board Manufacturer
Overall, military circuit boards are a key component of modern military technology, providing the military with advanced weapons, communications, and surveillance capabilities. Their design and manufacture require a high degree of expertise and technology to ensure reliability and performance on the battlefield.
What is the design of military circuit boards?
The design of military circuit boards is a complex and critical task that requires rigorous steps and the use of advanced technologies to ensure that the final product meets the strict requirements of military applications.
First, designing a military circuit board requires a detailed requirements analysis. Design teams must work closely with military customers to fully understand their needs and specifications. This includes considering the circuit board’s operating conditions in extreme environments, such as high and low temperatures, humidity, and electromagnetic interference.
Second, perform circuit design and layout. Designers use professional circuit design software to draw circuit schematics and layout drawings based on customer specifications and functional requirements. During the design process, attention must be paid to aspects such as signal integrity, circuit stability, and power consumption optimization to ensure that the board can operate reliably under various operating conditions.
Next comes prototyping and validation. Once the design is completed, the design team will make prototype samples of the circuit board and conduct various tests and verifications to ensure that its performance and reliability meet the requirements. These tests include circuit functional testing, signal integrity analysis, thermal analysis and reliability testing.
Throughout the design process, the design team must strictly follow military standards and specifications. They must ensure that the circuit board design complies with relevant military standards, such as MIL-STD-810 and MIL-PRF-55110, etc. At the same time, they also need to consider the security and protection of the circuit board to prevent unauthorized access and malicious attacks.
Additionally, the design team needs to work closely with suppliers and manufacturers. They must select high-quality materials and components and ensure supply chain reliability and stability. At the same time, they need to coordinate all aspects of the manufacturing process to ensure that the final product meets the design specifications and is delivered on time.
In short, designing military circuit boards is a complex and critical task that requires the design team to have extensive experience and expertise to ensure that the final product can operate reliably and perform optimally in military applications.
What is the manufacturing process of military circuit boards?
The manufacturing process of military circuit boards is a complex and precise process that covers multiple key steps. From the selection of raw materials to the inspection of the final product, every step is crucial. These steps and their special techniques and requirements are detailed below:
Raw material selection: The process of manufacturing military circuit boards begins with the selection of raw materials. High-quality substrate materials are key, usually materials with strong high temperature resistance and low dielectric constant, such as FR-4 or PTFE. Selecting the appropriate substrate material can ensure the stability and reliability of the circuit board in harsh environments.
Drawing design and layout planning: During the design stage, circuit board layout planning is a crucial step. By optimizing the layout, signal interference and circuit noise can be minimized, improving the performance and reliability of the circuit board. Special techniques, such as impedance matching and length matching of signal transmission lines, are widely used in layout design.
Printed circuit board (PCB) manufacturing: Printed circuit board is the process of printing circuit patterns onto a substrate. This step typically uses screen printing or photolithography techniques to create conductive layers and circuit patterns on the substrate. At this stage, precise control and high-quality printing equipment are essential.
Chemical etching and cleaning: The printed circuit board needs to be chemically etched to remove unnecessary metal parts and retain the required conductive pattern. The board then goes through a rigorous cleaning process to remove any impurities or chemicals that may remain on the surface.
Drilling and Metallization: Drilling holes in circuit boards are used to mount components and connect circuits. This step requires high-precision drilling equipment to ensure the accuracy and consistency of hole locations. Afterwards, the hole walls are metallized through techniques such as chemical deposition or gold plating to enhance the reliability and conductive properties of the connection.
Soldering and Assembly: Soldering electronic components onto a circuit board is one of the critical steps in the manufacturing process. This is usually done via surface mount technology (SMT) or plug-in assembly. The quality of welding directly affects the performance and reliability of the circuit board.
Cover coating: In order to protect the circuit board from environmental factors, its surface is usually covered with a cover coating, such as spraying or dipping a covering agent. This helps prevent damage to the board from moisture, chemicals, and other contaminants and improves its long-term stability.
Final Inspection and Testing: At the final stage of the manufacturing process, each circuit board undergoes rigorous final inspection and testing. This includes visual inspection, functional testing, electrical testing and high/low temperature testing to ensure the product meets military specifications and performance requirements.
Through the above key steps, military circuit boards can be precisely manufactured to ensure their reliability under extreme conditions.
and performance. Each step relies on advanced technology and strict quality control to meet the stringent requirements of military applications.
How are military circuit boards made?
The manufacturing of military circuit boards is a precise and complex process involving advanced equipment and technology as well as strict quality control measures. When manufacturers produce high-quality military circuit boards, they usually use the following advanced equipment and technologies:
First, manufacturers use advanced circuit board design software to design the circuit board layout and perform simulation and verification. These software accurately calculate signal transmission and electrical characteristics to ensure designs meet military specifications and performance requirements.
Second, manufacturers utilize advanced automated equipment for printing and making circuit boards. Automated production lines enable efficient production and ensure production consistency and accuracy. For example, automated printers can precisely print conductive ink onto substrates to form circuit patterns.
In the chemical etching and electroplating stages, manufacturers use advanced chemical processing equipment and technology. These devices can precisely control the process and parameters of chemical reactions, ensuring the quality and flatness of the board surface, as well as the thickness and uniformity of the copper layer.
During the drilling and metallization stages, manufacturers often use advanced technologies such as laser drilling and vacuum metallization. Laser drilling can achieve high-precision hole position and hole diameter control, while vacuum metallization can uniformly deposit metal on the hole wall, improving the conductivity and reliability of the circuit board.
Finally, during the final inspection and testing stage, manufacturers use advanced inspection equipment and technology to conduct comprehensive inspection and testing of the circuit boards. These devices can detect various performance indicators of circuit boards, such as continuity, insulation, reliability, etc., to ensure that products meet military standards and customer requirements.
In addition to advanced equipment and technology, manufacturers have also adopted strict quality control measures to ensure product reliability and performance. They have implemented a comprehensive quality management system, including strict screening of raw materials and supplier management, real-time monitoring and control of the production process, and comprehensive inspection and testing of finished products. Through these measures, manufacturers can ensure that each military circuit board meets customer needs and expectations and operates reliably in the harsh military application environment.
How much do military circuit boards cost?
The cost of military circuit boards is a complex issue that is affected by many factors. First, the cost of military circuit boards is affected by the complexity of their design and manufacturing. Because military circuit boards need to meet higher reliability and performance requirements, their design and manufacturing processes are typically more complex and rigorous than commercial circuit boards. This means more manpower, technology and resources are required to develop and produce these boards, leading to higher costs.
Secondly, the cost of military circuit boards is also affected by material selection. Military circuit boards typically use high-quality, high-durability materials to ensure their reliability and stability in extreme environments. These materials are more expensive than commercial circuit board materials, thus increasing the cost.
In addition, the scale of production will also affect the cost of military circuit boards. Since the demand for military circuit boards is usually smaller, it is not possible to achieve the significant cost reductions that can be achieved by mass-producing commercial circuit boards. Moreover, the production of military circuit boards often requires strict quality control and review processes, which also increases production costs.
Military circuit boards typically cost more than commercial circuit boards. This is because military circuit boards need to meet more stringent performance and reliability requirements, as well as higher quality standards. In addition, the manufacturing process of military circuit boards may require more special equipment and technology, as well as more manpower input, which will increase manufacturing costs. So while in some ways the cost of military circuit boards may be decreasing as technology advances, they are generally still more expensive than commercial circuit boards.
What materials are used in military circuit boards?
The materials selected for military circuit board manufacturing are critical to ensuring their durability and reliability. Here are some common military circuit board materials and their characteristics:
Substrate material: Common substrate materials include FR-4 fiberglass reinforced epoxy resin and polyimide (PI). FR-4 has excellent mechanical strength and heat resistance, making it suitable for most applications. Polyimide has higher thermal and chemical stability and is suitable for high temperature and high frequency applications.
Conductive layer: The conductive layer usually uses copper as the conductive material. Its excellent conductivity and processability make it the first choice material. In military circuit boards, thick copper foil is often used to increase current carrying capacity.
Insulation layer: The insulation layer material is usually made of fiberglass cloth covered with epoxy resin (Prepreg) or polytetrafluoroethylene (PTFE). These materials have excellent insulation properties and high temperature resistance, which can effectively prevent short circuits and leakage between circuit boards.
Overlay: The overlay usually uses epoxy or polyurethane as a protective layer to protect the circuit board from chemical corrosion and mechanical damage in the environment.
Special Materials: Some military circuit boards may require the use of special materials to meet specific application needs. For example, high-density interconnect boards (HDI) may use polyimide film as an insulating layer to achieve higher line density and better signal integrity.
The properties of these materials allow military circuit boards to operate stably in harsh environmental conditions. They have excellent thermal resistance, chemical stability, mechanical strength and electrical properties to ensure the reliability and performance of electronic systems under extreme conditions. Therefore, when selecting materials, military circuit board manufacturers often base their selection on specific application needs and performance
Who can make military circuit boards?
In the world of military circuit board manufacturing, finding the right supplier is critical. Excellent suppliers not only have advanced technology and equipment, but also have a deep understanding of and strict compliance with military standards. When selecting suppliers, the company needs to consider the following factors:
Technical strength and experience: The manufacturing of military circuit boards requires highly specialized technology and extensive experience. Suppliers must have advanced manufacturing equipment and technical teams that can meet the company’s high requirements for performance, reliability and quality.
Quality management system: Suppliers must establish a complete quality management system to ensure that products meet military standards and customer requirements. This includes comprehensive monitoring and control from raw material procurement to production processes, as well as strict inspection and testing processes.
Comply with military standards: Military circuit boards must comply with a series of strict military standards and specifications, such as MIL-PRF-31032, MIL-PRF-55110, etc. Suppliers must be familiar with these standards and be able to ensure that products are designed and manufactured to meet the requirements.
Innovation capability: With the continuous development of technology, the design and manufacturing of military circuit boards are also constantly innovating. Suppliers must have continuous R&D capabilities and innovation awareness, and be able to provide the company with the latest technologies and solutions.
Supply stability: Military projects usually have strict requirements on supply stability. Suppliers must be able to guarantee timely delivery and have flexible production capabilities to adapt to changes in market demand.
As an enterprise with rich experience in the military field, our company needs to choose a reliable supplier that meets the above conditions. We are committed to establishing long-term and stable cooperative relationships with our partners, jointly promoting the development of military electronics technology, and contributing to the national defense industry.
What are 5 qualities of a good customer service?
Excellent customer service is a key component of any successful business. Whether in the military circuit board manufacturing industry or elsewhere, providing excellent customer service is an important factor in ensuring customer satisfaction and business growth. Here are five hallmarks of great customer service:
Excellent customer service starts with a professional attitude and expert knowledge. Employees providing services should have the necessary skills and experience to effectively address customer problems and needs. No matter what challenges customers face, a professional customer service team is expected to support and assist them with courtesy, patience, and professionalism.
Responding quickly to customer needs and questions is the key to excellent customer service. Customers want their issues to be resolved promptly, not ignored or delayed. By establishing efficient communication channels and response mechanisms, companies can ensure that customers receive timely feedback and support, thereby increasing customer satisfaction and loyalty.
Understanding your customers’ needs and preferences and providing a personalized service experience is the key to excellent customer service. By building good customer relationships and positive interactions, companies can better understand their customers’ needs and provide them with customized solutions and services. Personalized care not only improves customer satisfaction, but also enhances customer loyalty and word-of-mouth.
In the customer service process, it is crucial to solve the customer’s problems and challenges. A quality customer service team should have good problem-solving skills and be able to quickly identify and resolve various issues faced by customers. By working closely with customers and adopting proactive solutions, companies can build trust and partnership, increasing customer satisfaction and loyalty.
Great customer service is not just a one-time transaction, but a process of continuous improvement. Businesses should continually seek customer feedback and suggestions and view them as motivation and opportunities for improvement. By continuously optimizing service processes, upgrading employee skills and improving product quality, companies can continuously improve customer service levels, maintain competitive advantages and achieve business growth.
In conclusion, excellent customer service is one of the key factors for a successful business. Through professionalism, timely responses, personalized care, problem solving and continuous improvement, businesses can build strong customer relationships and achieve long-term business success
FAQS
What certifications should a military circuit board manufacturer have?
Military circuit board manufacturers should have a series of certifications and qualifications to ensure that their products meet military standards and specifications and meet customer needs. These certifications include ISO 9001 quality management system certification, AS9100 aerospace quality management system certification, and ITAR international exchange weapons regulations certification.
How to choose the right military circuit board manufacturer?
There are several factors to consider when choosing the right military circuit board manufacturer. First, manufacturers must have extensive experience and expertise to meet the special needs of military applications. Secondly, manufacturers should have advanced production equipment and technology to ensure product quality and performance. Finally, manufacturers should also provide excellent customer service and technical support to meet customer needs and requirements.
What is the future development trend of military circuit boards?
With the continuous development and upgrading of military technology, military circuit board manufacturing technology is also constantly progressing and evolving. In the future, we can foresee that military circuit boards will increasingly tend to be multi-layer, high-density, high-speed, low-power consumption and high-reliability to meet the needs of increasingly complex and diverse military applications.
What are the main challenges in military circuit board design?
Key challenges in military circuit board design include ensuring signal integrity, effective thermal management, and meeting military standards within strict size and weight constraints. Because military electronic equipment often operates in harsh environmental conditions, such as high temperatures, high humidity, and is subject to electromagnetic interference, the design process requires special consideration of these factors.
What is the difference between military circuit boards and commercial circuit boards?
Military circuit boards have higher durability, stability and anti-interference capabilities than commercial circuit boards. They typically feature higher quality materials and workmanship to meet military standards and specifications. In addition, military circuit boards often undergo more rigorous testing and certification to ensure their reliability under extreme conditions