Microwave/Microtrace PCB Manufacturer.Microwave/Microtrace PCB Manufacturer specializes in the precise fabrication of microwave circuitry, catering to industries requiring high-frequency applications. With advanced technology and meticulous attention to detail, we craft PCBs tailored for optimal performance in microwave systems. Our expertise lies in the intricate design and production of circuit boards that ensure minimal signal loss and maximum efficiency, crucial for telecommunications, aerospace, and medical equipment. From prototype to mass production, we deliver reliable solutions meeting stringent quality standards, empowering our clients with cutting-edge technology for their next-generation products.
In today’s digital era, PCB (Printed Circuit Board) has become the core component of almost all electronic devices. In terms of wireless communications, radio frequency technology and high-frequency microwave applications, the development of Microwave/Microtrace PCB manufacturing technology is particularly important. This article will give you an in-depth understanding of PCB definition, design, materials, manufacturing processes, application areas, advantages, and answers to your frequently asked questions.
What is Microwave/Microtrace PCB?
Microwave/Microtrace PCB is a type of printed circuit board specifically designed for use in high frequency microwave applications. It occupies an important position in PCB manufacturing technology, especially in scenarios where high-frequency signals need to be processed. Compared with traditional PCBs, microwave/microtrace PCBs have higher requirements in design and manufacturing to ensure stable transmission and reliability of signals.
A key feature of microwave/microtrace PCBs is their ability to efficiently handle high frequency signals. In the field of high-frequency microwaves, signal transmission is affected by electromagnetic waves, so the design and manufacturing of PCBs need to consider more factors. Microwave/microtrace PCB uses special materials and processes to reduce signal transmission losses, improve impedance matching, and ensure stable frequency response.
Routing and layout become particularly important in the design of microwave/microtrace PCBs. To minimize signal transmission losses, designers must accurately plan the path and layout of wires. In addition, microwave/microtrace PCB also needs to take into account the diffraction and reflection of electromagnetic waves to ensure the stability and reliability of signal transmission.
During the manufacturing process, microwave/microtrace PCB requires the use of high-precision processing equipment and advanced process technology. From chemical processing to imaging technology, each step requires strict control and monitoring to ensure the quality and performance of the final product.
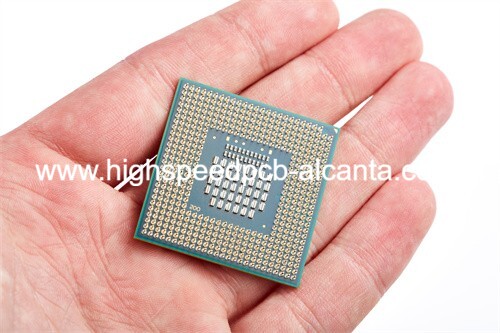
Microwave/Microtrace PCB Manufacturer
In general, a microwave/microtrace PCB is a printed circuit board specifically designed to handle high-frequency microwave signals. It uses special design and manufacturing technology to ensure stable transmission and reliability of signals, and has become an indispensable key component in wireless communications, radar, satellites and other fields.
Microwave/Microtrace PCB design Reference Guide.
The key to Microwave/Microtrace PCB manufacturing is design. For high-frequency microwave applications, a suitable design can ensure stable signal transmission and good impedance matching. During the design process, the particularities of microwave and high-frequency signals need to be taken into account to fully exploit the performance of the PCB. Here are some key design guidelines to help you succeed in Microwave/Microtrace PCB manufacturing:
Material selection
Selecting the appropriate high frequency dielectric material is critical to Microwave/Microtrace PCB design. Commonly used materials include PTFE (polytetrafluoroethylene), FR-4, etc. These materials have low loss and high dielectric constant properties, making them suitable for designs in high-frequency microwave environments.
Layout design
When designing your PCB layout, you need to consider the path and routing of signal transmission. Avoid sharp corners and sudden changes in the signal path to reduce signal reflection and loss. Properly plan the layout of signal, ground, and power layers to ensure good signal integrity and impedance matching.
Signal transmission line design
Transmission line design for high-frequency signals is critical. Microwave/microtrace PCB designs often use high-frequency transmission lines such as microstrip or coaxial lines. Ensure that the width, spacing and plate thickness of the transmission line meet the design requirements to achieve stable signal transmission and impedance matching.
Electromagnetic Compatibility (EMC) Design
During the design process, electromagnetic compatibility (EMC) factors should be taken into consideration. Properly design PCB layout and wiring, and take shielding measures to reduce electromagnetic interference and radiation to ensure system stability and reliability.
Thermal management design
In high-frequency microwave applications, thermal management is an important consideration. Properly design the heat dissipation structure, add heat dissipation holes and other measures to effectively reduce the PCB temperature and ensure stable operation of the system.
Simulation and testing
After the design is completed, simulation and testing are essential steps. Use simulation software to simulate high-frequency signal transmission to verify the feasibility and performance of the design. Verify PCB performance and reliability through actual testing to ensure the design meets expected requirements.
Keep learning and updating
In an ever-changing technological environment, keeping learning and updating are important qualities for designers. Pay close attention to the latest developments and technology trends in the industry, continuously improve design methods and process flows, and improve the level and competitiveness of Microwave/Microtrace PCB manufacturing.
Through the above design guide, you can better understand the key design principles and technical points in Microwave/Microtrace PCB manufacturing. Proper application of these guidelines will help you design a PCB with stable performance and high reliability to meet the needs of high-frequency microwave applications.
What material is used in Microwave/Microtrace PCB?
The materials used in Microwave/Microtrace PCB manufacturing are critical as they directly impact the performance and stability of the board. These materials often include high-frequency dielectric materials such as PTFE (polytetrafluoroethylene), FR-4, and special conductive materials. Let’s take a closer look at the properties and applications of these materials.
First of all, PTFE (polytetrafluoroethylene) is an excellent high-frequency dielectric material that is favored for its low dielectric constant and low dielectric loss. The excellent properties of PTFE make it one of the materials of choice in Microwave/Microtrace PCBs. Its stable dielectric properties and low loss rate enable signals to be transmitted more stably in high-frequency environments, thereby improving the performance and reliability of the circuit board.
Second, FR-4 is a common substrate material that is widely used in conventional PCB manufacturing. However, in Microwave/Microtrace PCB manufacturing where high frequency performance is required, the performance of FR-4 may not be up to par. Therefore, some manufacturers will choose to cover the FR-4 surface with special high-frequency dielectric materials to improve the performance of the circuit board. The use of this hybrid material gives manufacturers the flexibility to choose materials in different application scenarios to meet specific needs.
In addition, Microwave/Microtrace PCB also uses some special conductive materials, such as silver, gold, etc. These conductive materials have excellent conductive properties and stability, which can ensure that the circuit board has good signal transmission performance in high-frequency environments.
Overall, the materials used in Microwave/Microtrace PCB manufacturing perform well in high frequency environments, providing stable performance and low losses. Choosing the right materials is crucial to ensure the performance and reliability of circuit boards in high-frequency microwave applications. Manufacturers need to flexibly select materials based on specific application scenarios and performance requirements to ensure that circuit boards can achieve the best working results.
What size are Microwave/Microtrace PCB?
The size of a Microwave/Microtrace PCB is highly dependent on its specific application requirements. Microwave/Microtrace PCB manufacturing technology has excellent flexibility and can realize diverse designs to meet the requirements of different scenarios. In many high-frequency microwave applications, tiny sized PCBs are often preferred because they can accommodate more functionality and components in a limited space.
Microwave/Microtrace PCB manufacturing technology allows designs with complex circuits and tiny dimensions. Through precision routing and layout, more components can be arranged on the PCB and ensured that they are close enough to minimize the time and loss of signal transmission. This high-density design makes Microwave/Microtrace PCBs widely used in fields such as communications equipment, satellite technology, radar systems, and more.
In the high-frequency microwave world, PCB dimensions are often relatively small. This is because in high-frequency environments, the signal transmission path needs to be shorter to reduce signal attenuation and distortion. Therefore, micro-sized PCBs are more conducive to achieving good signal transmission performance and impedance matching. In addition, the tiny size of PCBs is also more suitable for integration into complex systems, allowing for higher levels of functionality and performance.
Microwave/Microtrace PCB manufacturing technology allows designers to achieve an ideal balance between size and performance. They can flexibly adjust the size of the PCB according to the needs of the specific application for optimal performance and reliability. This customized design approach allows Microwave/Microtrace PCBs to meet a variety of application needs while maintaining a high level of performance and quality.
To sum up, Microwave/Microtrace PCB manufacturing technology can realize the design of complex circuits and tiny sizes to meet high-density and high-performance requirements. In the field of high-frequency microwaves, micro-sized PCBs have more advantages and can achieve more stable signal transmission and higher integration. Therefore, by selecting the right size Microwave/Microtrace PCB, manufacturers can ensure that their products stay ahead of the competition in the competitive market.
The Manufacturer Process of Microwave/Microtrace PCB.
The manufacturing process of Microwave/Microtrace PCB is a complex and precise process involving a variety of key steps, including precision chemical processing, imaging technology and high-precision processing equipment. The manufacturing process of Microwave/Microtrace PCB will be introduced in detail below.
First, the manufacturing process begins with the design phase. At this stage, engineers use professional design software to draw the PCB layout and circuit connections based on the customer’s requirements and application needs. The design of Microwave/Microtrace PCB needs to take into account the transmission characteristics of high-frequency microwave signals, so special attention needs to be paid to impedance matching, signal transmission paths, electromagnetic interference and other factors during the design process.
Once the design is complete, next comes the preparation phase for manufacturing. This stage involves the selection and preparation of materials, including the procurement of high-frequency dielectric materials such as PTFE (polytetrafluoroethylene), and the preparation of special conductive materials. Material selection is crucial as it directly affects the performance and stability of the PCB.
Then comes the application of imaging technology. The manufacturing of Microwave/Microtrace PCB usually uses photolithography technology to transfer the designed graphics to the PCB board. This process involves steps such as photoresist coating, exposure, and development, and requires high-precision equipment and strict process control.
Next comes chemical processing. At this stage, chemical etching is used to remove the metal layer exposed outside the photoresist to form the lines and connections on the PCB. This step requires precise control of the composition and concentration of the etching solution to ensure the quality and accuracy of the circuit.
The last step is processing and inspection. After manufacturing, the PCB needs to be processed and surface treated to improve its corrosion resistance and electrical conductivity. The PCB will then undergo strict quality inspection, including visual inspection, line connectivity testing, and impedance matching testing. Only PCBs that pass all inspections can be delivered to customers.
In general, the manufacturing process of Microwave/Microtrace PCB requires strict process control and professional technical support, and precise operation and strict quality control are required from design to finished product. Each of these steps has an important impact on the performance and reliability of the final product, so every detail in the manufacturing process must be refined.
The Application area of Microwave/Microtrace PCB.
The high-frequency characteristics and stable performance of Microwave/Microtrace PCB manufacturing technology make it widely used in many fields. The following is an introduction to applications in some major areas:
Communication
In the field of communication, Microwave/Microtrace PCB is widely used in wireless base stations, communication network equipment and communication satellites. Its high-frequency characteristics and excellent signal transmission capabilities make it a key component for achieving high-speed data transmission and stable communication. From 5G base stations to satellite communication equipment, Microwave/Microtrace PCB plays an important role in ensuring the stable operation of communication systems.
Radar
Radar systems need to detect targets and obtain information quickly and accurately, and the high-frequency characteristics and stable performance of Microwave/Microtrace PCB make it a core component in the radar system. Whether it is radar systems in military applications or weather radars and traffic monitoring radars in civilian applications, Microwave/Microtrace PCBs provide reliable performance.
Satellite
Satellite systems have extremely high requirements on the stability and high-frequency performance of electronic equipment. Microwave/Microtrace PCB is widely used in satellite communications, remote sensing and navigation systems because of its excellent performance in high-frequency microwave applications. In the fields of earth observation, weather forecasting, satellite navigation and tracking, Microwave/Microtrace PCB applications provide reliable support for satellite systems.
Medical equipment
In medical equipment, Microwave/Microtrace PCBs are used in high-frequency electronic equipment, medical imaging equipment, and vital sign monitoring systems. Its stability and high-frequency characteristics enable it to meet the requirements of medical equipment for signal accuracy and reliability, providing important support for the development of the medical industry. From medical diagnostics to therapeutic devices, Microwave/Microtrace PCBs play a critical role in the medical field.
To sum up, Microwave/Microtrace PCB manufacturing technology is widely used in communications, radar, satellites and medical equipment and other fields. Its high-frequency characteristics and stable performance make it the first choice for many key applications, providing strong support for technological innovation and development in various industries.
What are the advantages of Microwave/Microtrace PCB?
Microwave/Microtrace PCB (Microwave/Microtrace Printed Circuit Board) has many advantages over traditional circuit boards, which make it outstanding in the high-frequency microwave field. The following are the advantages of Microwave/Microtrace PCB:
First, Microwave/Microtrace PCB has lower transmission loss. Transmission loss is the energy lost during signal transmission. Microwave/Microtrace PCB can reduce signal loss by using low-loss high-frequency dielectric materials and optimized design and manufacturing processes to ensure that the signal can be maintained as much as possible during transmission. Stable and strong.
Secondly, Microwave/Microtrace PCB has better impedance matching. Impedance matching refers to the degree of impedance matching between the signal source and the load. Microwave/Microtrace PCB can achieve more precise impedance matching through precise design and manufacturing, improve the efficiency and stability of signal transmission, and reduce reflection and attenuation.
In addition, Microwave/Microtrace PCB has higher frequency response. High-frequency microwave signals need to be transmitted and processed quickly and accurately. Microwave/Microtrace PCB can achieve higher frequency response and is suitable for a wide frequency range, from hundreds of megahertz to tens of gigahertz, to meet the needs of different applications.
Finally, Microwave/Microtrace PCB has higher reliability. In high-frequency microwave applications, extremely high requirements are placed on signal stability and reliability. Any slight error or instability may lead to system performance degradation or even failure. Microwave/Microtrace PCB uses high-quality materials and advanced manufacturing processes to ensure its stability and reliability in high-frequency microwave environments, and can operate stably for a long time.
To sum up, Microwave/Microtrace PCB has many advantages such as lower transmission loss, better impedance matching, higher frequency response and higher reliability, making it the first choice in the high-frequency microwave field. Whether in the fields of communications, radar, satellites or medical equipment, Microwave/Microtrace PCB can exert excellent performance and promote the continuous advancement of technology.
FAQ
What frequency ranges are Microwave/Microtrace PCBs suitable for?
Microwave/Microtrace PCB manufacturing technology is suitable for a wide frequency range, ranging from a few hundred megahertz to tens of gigahertz. This manufacturing technology is particularly suitable for applications requiring high frequency response and stable performance, such as communication systems, radar, satellite communications and other fields. Whether you need to handle high-speed data transmission or microwave signal transmission, Microwave/Microtrace PCBs deliver superior performance and reliability.
What is the manufacturing lead time for Microwave/Microtrace PCB?
Microwave/Microtrace PCB manufacturing lead time depends on specific design requirements and project size. Generally speaking, it takes anywhere from a few days to a few weeks from design to production completion. During the manufacturing process, strict quality control and testing are required to ensure that the final product meets customer requirements and standards. At the same time, the production cycle is also affected by factors such as supply chain and production capacity.
What are the advantages of Microwave/Microtrace PCB over traditional PCB?
Microwave/Microtrace PCBs offer several advantages over traditional PCBs. First, Microwave/Microtrace PCB can achieve lower transmission loss, which means that signal integrity and stability can be more effectively maintained during signal transmission. Secondly, Microwave/Microtrace PCB has better impedance matching capabilities and can provide more stable signal transmission. In addition, due to its specially designed materials and processes, Microwave/Microtrace PCB has higher frequency response and higher reliability, making it suitable for applications with higher performance requirements.
How much does a Microwave/Microtrace PCB cost?
The cost of Microwave/Microtrace PCB manufacturing depends on several factors, including design complexity, materials required, production volumes, and more. Due to their specially designed materials and processes, Microwave/Microtrace PCBs typically cost slightly more to manufacture than traditional PCBs. However, in applications that require high frequency response and stable performance, the performance advantages of Microwave/Microtrace PCBs often offset their higher cost and provide customers with a higher return on investment.