Microvias | Blind Vias PCB Manufacturing.Microvias and blind vias are crucial elements in modern PCB manufacturing, revolutionizing miniaturization and enhancing circuit density. Microvias, minute holes drilled with precision, facilitate intricate interconnections in multilayer boards, enabling higher signal speeds and reducing signal loss. Meanwhile, blind vias, terminating on one side of the board, connect inner layers, conserving space and enhancing design flexibility. Together, they epitomize the advancement in PCB technology, offering unparalleled efficiency in compact electronic devices. With meticulous fabrication techniques, manufacturers ensure seamless integration of these vias, elevating the performance and reliability of electronic systems.
Microvias PCB (Printed Circuit Board) is an indispensable and key component of modern electronic equipment. By providing high-density connections and optimized layout, Microvias PCBs make electronic products more compact and performant. This article will take an in-depth look at the Microvias PCB manufacturing process to provide you with a comprehensive guide to help you better understand this important technology.
What is Microvias PCB?
Microvias PCB (Printed Circuit Board) is a special type of printed circuit board whose main feature is the use of microvias (Microvias) connection technology. These tiny holes pass through different layers of the PCB and are used to connect various electronic components such as chips, resistors, and capacitors. Compared with traditional through-hole (Through-Hole) technology, Microvias PCB has smaller aperture and higher density, so it can achieve more compact layout and higher connection density.
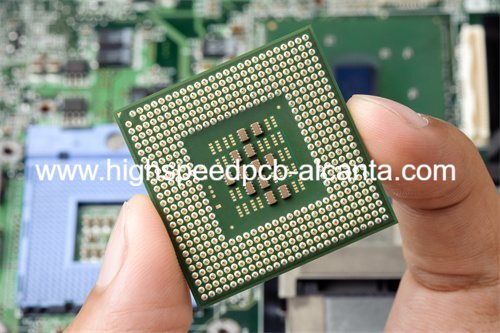
Microvias | Blind Vias PCB manufacturing
In modern electronic equipment, Microvias PCB plays a vital role. As electronic equipment becomes increasingly miniaturized, lightweight and high-performance, the requirements for PCBs are becoming more and more stringent. The emergence of Microvias PCBs meets this need. They can provide higher connection density and faster signal transmission speeds, making electronic products more compact, lightweight and high-performance. At the same time, Microvias PCB can also reduce the length of signal transmission paths, reduce signal transmission delays, and improve signal quality and stability. Therefore, it is widely used in high-frequency, high-speed, and high-density electronic equipment, such as communication equipment and computer equipment. , medical equipment and consumer electronics, etc.
In general, Microvias PCB plays a key connection and support role in modern electronic equipment. Its high-density connection, optimized layout and high-performance characteristics enable electronic products to have better functions and performance, and promote the continuous advancement of electronic technology. development and innovation.
How to design Microvias PCB?
Designing Microvias PCBs is a complex and critical process that requires careful planning and precise execution to ensure the final product is high-performance and reliable. The main steps of designing Microvias PCB will be introduced in detail below:
Before designing Microvias PCB, you first need to clarify the customer’s needs and product specifications. This includes determining parameters such as the number of plies, plate type, aperture size, plate thickness, etc. Based on these needs and specifications, determine the direction and goals of the design.
After determining the requirements and specifications, circuit layout planning is the first step in design. At this stage, factors such as the location of circuit components, their connection methods, and signal transmission paths need to be considered. Especially for Microvias PCB, the location and layout of micro-holes need to be reasonably arranged to minimize signal transmission paths and reduce signal loss.
PCB design using CAD (Computer-Aided Design) software is the core part of design. In CAD software, designers can convert circuit diagrams into PCB layouts and arrange and optimize micro-holes. During the design process, attention needs to be paid to maintaining the integrity and stability of the circuit and avoiding signal interference and electromagnetic interference.
Microvias are a key component of Microvias PCB and directly affect the performance and reliability of the circuit. During the design process, the location, size and layout of micro-holes need to be determined based on signal transmission requirements and the number of board layers. Additionally, the spacing and arrangement of microvias and other components need to be considered to ensure good connectivity and signal transmission quality.
In Microvias PCB design, in addition to circuit performance, factors such as thermal management and mechanical strength also need to be considered. Reasonably arrange micro-holes and circuit components to ensure uniform temperature distribution on the board and improve the mechanical strength and stability of the PCB.
After the design is completed, simulation and verification are essential steps. Use simulation software to perform signal integrity analysis and thermal analysis on Microvias PCB to verify the rationality and reliability of the design. Additionally, prototyping and testing can be used to verify that the design meets expected performance requirements.
Optimizing and improving the design based on simulation and test results is the final step of the design. This may involve the rearrangement of microvias, adjustments to circuit paths, or replacement of materials. Through continuous optimization and improvement, ensure the best performance and reliability of the design.
To summarize, designing a Microvias PCB requires careful planning and execution through multiple steps, including determining requirements and specifications, circuit layout planning, CAD software design, microvia design and optimization, thermal management and mechanical strength considerations, simulation and verification, and Optimization and improvement. Only by executing each step rigorously and meticulously, and continuously optimizing and improving it, can we ensure that the final designed Microvias PCB has high performance and reliability.
What is the manufacturing process of Microvias PCB?
The manufacturing process of Microvias PCB is a complex and precise process involving multiple critical steps, each step is crucial to ensure that the quality and performance of the final product meet the expected requirements.
Before manufacturing Microvias PCB, detailed design and planning first need to be carried out. This stage includes determining the number of layers of the circuit board, selection of board materials, layout and wiring, location and size of microvias, etc. Designers must consider the board’s end use and specific performance requirements to ensure the design is achievable and manufacturable.
The first step in manufacturing Microvias PCB is to convert the design into a graphical circuit board image and make a pattern making mold for the circuit board. This step usually uses photolithography technology to transfer the design pattern to the surface of the copper-clad substrate to form the required circuit pattern and microhole locations.
Next, the unnecessary copper is removed through etching technology, exposing the metal traces and microvia locations on the circuit board. After etching, microhole drilling is performed to penetrate the circuit board. This step requires a high degree of precision to ensure that the size and position of the micropores are exactly as designed.
After drilling the micropores, copper is plated inside the micropores through chemical methods to form a good conductive connection. Subsequently, the micropores are filled, usually using special filling materials or by adding metal into the micropores through electroplating methods. This step is critical to ensure the conductivity and reliability of the micropores.
During the final stages of manufacturing Microvias PCBs, surface treatments are performed to improve the board’s corrosion resistance and soldering properties. Common surface treatment methods include tin spraying, gold spraying, silver spraying, etc. After completing the surface treatment, strict inspection and testing are carried out to ensure that the circuit board meets the design requirements and quality standards, including visual inspection, electrical testing, solder joint inspection, etc.
Through the above key steps, Microvias PCB manufacturing process has completed the precise control of key processes such as circuit board design, processing, filling and surface treatment, ensuring that the quality and performance of the final product meet customer requirements and expectations.
What are the specific steps for Microvias PCB manufacturing?
The manufacturing process of Microvias PCB is a precise and complex project that involves multiple steps and processes to ensure the high quality and reliability of the final product. The specific steps for manufacturing Microvias PCB will be introduced in detail below:
Before you start manufacturing Microvias PCB, you first need to do the design and preparation work. This includes determining the layout and size of the PCB, selecting appropriate substrate materials (such as FR-4 or high-frequency materials), and designing the location and size of microvias, etc. During the design phase, it is important to ensure that microvias are properly laid out to achieve high-density connections and meet circuit design requirements.
Patterning is the process of transferring a design onto a PCB substrate. Through photolithography technology, the designed PCB pattern is transferred to the photoresist layer covering the surface of the substrate. Then, chemical etching or mechanical removal methods are used to remove the copper foil that is not covered with the photoresist layer to form a circuit pattern.
After patterning, the PCB surface needs to be copper plated. The purpose of this step is to form a uniform layer of copper on the PCB surface to provide good conductivity and connectivity. Through techniques such as electroless copper plating or electrolytic copper plating, copper is deposited on the surface of the exposed copper foil and within the micro-holes, filling the micro-holes and ensuring good connections.
Punching is the process of drilling holes in a PCB. In Microvias PCB manufacturing, these holes are usually very small, typically less than 150 microns in diameter. Using laser drilling or mechanical drilling techniques, micro-vias and other regular holes are drilled through for subsequent plating and filling.
Etching is the process of removing copper foil that is not covered by the photoresist layer to form the final PCB circuit pattern. By immersing in an acidic or alkaline solution, the portion of the copper foil that is not protected by the photoresist layer is removed, leaving the desired circuit pattern.
Electroplating is one of the key steps in Microvias PCB manufacturing, and it involves applying a layer of metal (usually copper) to the surface of the PCB and within the microvias to increase conductivity and corrosion resistance. Through chemical or electrolytic methods, metal is deposited on the PCB surface and within the micropores, filling the micropores and forming good connections.
At the final stage of the manufacturing process, final inspection is performed to ensure the quality and performance of the PCB. This includes checking the integrity of the circuit pattern, the filling and connectivity of micro-holes, the surface quality and flatness of the PCB, etc. Through visual inspection, X-ray inspection and electrical testing, the PCB is comprehensively inspected and verified to ensure that it meets the design requirements and customer needs.
Microvias PCB manufacturing process requires sophisticated technology and equipment support to ensure the quality and performance of the final product. By following the above steps, manufacturers can produce high-quality, reliable Microvias PCBs that meet the needs of a variety of electronic applications.
Strict execution and quality control of these steps are key factors in ensuring the success of Microvias PCB manufacturing, and are also an important guarantee for customer satisfaction and product reliability.
How much does Microvias PCB cost?
When we consider the cost of Microvias PCBs, there are several factors that need to be considered as they have a significant impact on the final cost. Here are some key factors:
The base material of the PCB has a significant impact on the overall cost. Different types of substrate materials, such as FR-4, PTFE, etc., may have significantly different costs. High frequency materials are generally more expensive than regular FR-4 substrates.
The number of layers and complexity of Microvias PCBs is also an important factor in cost. The more layers there are, the more difficult and expensive it is to manufacture. In addition, if the PCB requires special interlayer connection technology, such as blind holes or buried holes, the cost will increase accordingly.
The number and size of microvias in Microvias PCB directly affects the manufacturing cost. More or smaller micropores mean a more complex manufacturing process and higher costs. Therefore, it is important to properly optimize the number and size of micropores during the design stage.
If Microvias PCB requires special processes, such as controlled impedance, special surface treatment, metal filling, etc., these processes usually increase manufacturing costs. These special process requirements may require additional equipment and materials, thereby increasing costs.
Production batch size is also an important factor affecting costs. Typically, high-volume production reduces the cost per PCB because fixed costs can be spread out. In comparison, the cost of small batch production is usually higher.
Finally, the technology and equipment used to manufacture Microvias PCBs also affects costs. Advanced technology and equipment may improve manufacturing efficiency, but they will also increase investment costs, thus affecting costs to a certain extent.
Therefore, to calculate the cost of Microvias PCB, you need to comprehensively consider the above factors and develop a suitable manufacturing plan based on specific needs and budget. Proper design and production planning can help minimize costs while ensuring product quality and performance.
What materials are Microvias PCBs made of?
Microvias PCB is a printed circuit board widely used in modern electronic equipment, which features microvias (Microvias) connection technology to achieve high-density layout and high-performance requirements. To meet these requirements, Microvias PCBs typically use a range of high-performance substrate materials with excellent electrical, thermal and mechanical properties to ensure stable and reliable electronic performance. Here are some common Microvias PCB materials:
FR-4 is one of the most common substrate materials and is characterized by affordable price, high mechanical strength, and good heat resistance. FR-4 substrates are usually used in applications with lower general performance requirements, such as communication equipment, industrial control, etc.
PTFE is a high-frequency material with excellent electrical properties and high temperature resistance, and is suitable for high-frequency and high-speed electronic applications. Microvias PCB uses PTFE substrate to achieve lower signal attenuation and better high-frequency performance.
RO4003C is a special high-frequency material with low loss, low dielectric constant and stable mechanical properties. It is often used in applications such as high-frequency antennas and radio frequency modules.
In addition to the common materials mentioned above, there are also some boards specially used for high-speed digital signal transmission, such as Isola I-Tera MT, Nelco N4000-13, etc. These high-speed boards offer excellent signal integrity and crosstalk immunity for applications requiring extremely high data transfer rates.
For applications that require excellent heat dissipation performance, such as LED lighting, power amplifiers, etc., metal substrates can also be used as the substrate material of Microvias PCB. Metal substrates have excellent heat dissipation characteristics, which can effectively reduce the operating temperature of electronic components and improve product reliability and stability.
Microvias PCB is made of a variety of high-performance substrate materials to meet high-performance requirements in different application scenarios. Choosing the right materials is critical to achieving good electronic performance and reliability, so material selection and characteristics need to be fully considered when designing and manufacturing Microvias PCBs.
Who makes Microvias PCBs?
The process of manufacturing Microvias PCB requires precision technology and professional equipment, so choosing the right supplier is crucial. Let’s take a look at who manufactures Microvias PCBs, and their expertise and experience in this field.
Our company is a professional supplier of Microvias PCB manufacturing with many years of experience and expertise. Our manufacturing plants are equipped with advanced equipment and technology to meet the various needs of our customers.
Our company has a team with strong technical strength, including engineers, technicians and quality management experts. They have extensive PCB manufacturing experience and are able to provide high-quality Microvias PCB products.
Our manufacturing factory is equipped with the latest PCB production equipment, including high-precision photolithography machines, chemical processing equipment, etching machines and electroplating equipment, etc. These advanced equipment ensure that the Microvias PCBs we produce are highly precise and reliable.
Our company focuses on product quality and customer satisfaction. We strictly implement the ISO quality management system to ensure that each batch of products undergoes strict quality control and inspection. From raw material procurement to manufacturing to final delivery, we are always committed to providing high-quality Microvias PCB products.
Our company values communication and cooperation with customers. Our sales team and customer service team are always ready to provide customers with technical support and solutions. We are committed to establishing long-term and stable cooperative relationships and providing customers with the best Microvias PCB solutions.
In the world of Microvias PCB manufacturing, choosing the right supplier is crucial. As an experienced and technologically advanced supplier, our company is committed to providing customers with high-quality, reliable Microvias PCB products and excellent customer service. We look forward to cooperating with you to jointly promote the development and progress of the electronics industry.
What are the five characteristics of great customer service?
Providing excellent customer service is key to ensuring customer satisfaction and maintaining long-term business relationships. Listed below are five key features to ensure customers receive the best possible service experience:
Prompt Response: Responding quickly to customer questions, concerns or needs is critical. Whether by phone, email or online chat, respond to customer inquiries in a timely manner and demonstrate customer care. Quick response can effectively reduce customer waiting time, enhance customer confidence in service, and improve customer satisfaction.
Expertise: Customers want to deal with professionals who know their stuff, can solve their problems and provide valuable advice. Provide training and ongoing learning opportunities to ensure the customer service team remains up-to-date on product knowledge and industry trends. By providing professional technical support and consulting services, we build customer trust in the company, thereby enhancing customer loyalty.
Customized Solutions: Every customer has unique needs and challenges, so providing customized solutions is key to increasing customer satisfaction. Through in-depth understanding of customers’ business and needs, we tailor products and services to meet their specific requirements. Customized solutions can improve product adaptability and performance, enhance customer experience, and promote the establishment of long-term partnerships.
Good communication: Establishing good communication channels is the basis for maintaining a good relationship with customers. Maintain close communication with customers, communicate important information and progress in a timely manner, and ensure customers understand the status of their projects or orders. Listen to customer feedback and suggestions, promptly solve problems and improve services to improve customer satisfaction and loyalty.
After-sales support: Good after-sales support is key to improving customer satisfaction and maintaining customer relationships. Solve customer problems and complaints in a timely manner, provide technical support and maintenance services, and ensure customer satisfaction with products and services. Establish a complete after-sales service system to provide customers with continuous support and assistance, and enhance customers’ trust and loyalty to the company.
To sum up, timely response, expertise, customized solutions, good communication and after-sales support are the five key characteristics of providing excellent customer service. By focusing on these aspects, companies can build good customer relationships, improve customer satisfaction, and achieve continued business growth and development.
FAQS
What are Microvias PCBs, and what advantages do they offer?
Microvias PCBs are printed circuit boards featuring small diameter holes, typically less than 150 micrometers in diameter, used for connecting layers in high-density circuit designs. They offer advantages such as increased routing density, improved signal integrity, and enhanced thermal management, making them ideal for high-speed and high-frequency applications.
How do you design Microvias PCBs to optimize performance?
Designing Microvias PCBs involves careful consideration of factors such as via size, pad size, and trace routing to ensure signal integrity and reliability. High-frequency designs may require controlled impedance traces and careful placement of vias to minimize signal distortion.
What is the manufacturing process for Microvias PCBs?
The manufacturing process for Microvias PCBs includes several key steps such as substrate preparation, laser drilling of microvias, metallization, electroplating, and final inspection. Each step is critical to ensure the quality and reliability of the finished PCB.
What materials are commonly used in Microvias PCB manufacturing?
Common materials used in Microvias PCB manufacturing include FR-4, high-frequency laminates such as Rogers and Taconic materials, and specialized materials for specific applications such as high-temperature or high-reliability environments.