Microvia Substrates Manufacturing,Microvia substrates manufacturing involves the intricate process of creating printed circuit boards (PCBs) with tiny, precise vias that enable high-density interconnections. This advanced manufacturing technique utilizes cutting-edge technology to fabricate PCBs with microscale features, enhancing performance and reliability in electronic devices. The process entails precise material deposition, laser drilling, and plating to create microvias, which enable the transmission of signals across multiple layers within a compact PCB design. Microvia substrates manufacturing revolutionizes electronics production, enabling the development of smaller, lighter, and more efficient devices for various applications, from smartphones to medical devices.
Microvia Substrates play a key role in the modern electronics industry, and their design and manufacturing processes are critical to the performance and reliability of electronic devices. As the basic component that connects and supports electronic components, the quality of Microvia Substrates directly affects the performance of the entire circuit board. This article will delve into the manufacturing process of Microvia Substrates, providing readers with a comprehensive guide to help them understand Microvia Substrates design principles, manufacturing processes, cost factors, and how to choose a quality manufacturer.
What are Microvia Substrates?
Microvia Substrates are a special type of printed circuit board (PCB) technology that plays a vital role in modern electronic devices. Compared with traditional multi-layer printed circuit boards, Microvia Substrates have higher density, smaller size and better performance, making it widely used in many high-end electronic products.
In electronic equipment, the main role of Microvia Substrates is to connect and support various electronic components, such as chips, capacitors, and resistors. Through Microvia technology, designers can implement more complex circuit layouts on PCBs, and can reduce the size and weight of circuit boards and improve the performance and reliability of electronic devices.
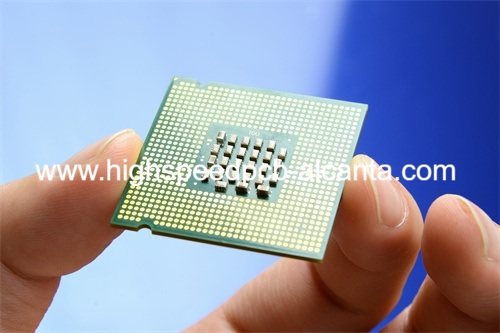
Microvia Substrates manufacturing
Microvia Substrates are widely used in the modern electronics industry, covering almost all fields of electronic equipment. From smartphones, tablets and laptops to aerospace, medical devices and military equipment, Microvia Substrates play a vital role. It can not only meet the needs of modern electronic equipment for miniaturization, lightweight and high performance, but also improve the stability and reliability of the circuit, providing users with a better user experience.
The emergence and development of Microvia Substrates not only promotes the technological progress of electronic equipment, but also promotes the development of the entire electronics industry. It provides designers with more space for innovation, provides manufacturers with more competitive advantages, and brings more advanced and reliable electronic products to users. Therefore, it can be said that Microvia Substrates has become an indispensable part of the modern electronics industry, and its application and importance will be further expanded and deepened with the continuous development of technology.
What is the design process for Microvia Substrates?
Microvia Substrates’ design process is a vital part of the entire electronic device manufacturing process. When designing Microvia Substrates, there are a number of key points to consider to ensure the final product meets performance and reliability requirements.
First of all, when designing Microvia Substrates, designers need to consider the function and purpose of the circuit board. This includes determining the types of electronic components carried by Microvia Substrates, connection requirements, and operating environmental conditions. By understanding the actual purpose of the board, designers can better determine design parameters and layout.
Secondly, designers need to consider the hierarchy and layout of Microvia Substrates. This involves determining the number of layers on the circuit board, the location of Microvia holes, and routing. During the design process, factors such as signal transmission paths, power distribution, ground wire layout, and EMI/EMC need to be fully considered to ensure the stability and performance of the circuit board.
In addition, designers also need to pay attention to the thermal management and protection measures of Microvia Substrates. In high-performance electronic devices, heat generation and dissipation is an important issue. Therefore, when designing Microvia Substrates, components such as radiators, fans, and heat sinks need to be properly arranged to ensure that the board maintains a stable temperature during long-term operation.
When using CAD software to design Microvia Substrates, designers can adopt a series of techniques and methods to improve design efficiency and quality. First, designers can use the advanced layout tools provided by CAD software to quickly generate the initial layout of the circuit board. Secondly, designers can use the simulation function provided by CAD software to verify the performance and reliability of the design. Through simulation analysis, designers can detect potential problems early and make timely adjustments and optimizations.
In addition, designers can also use the automatic routing function provided by CAD software to simplify the wiring process. Automatic wiring tools can automatically generate optimal wiring solutions based on design requirements and constraints, improving design efficiency and wiring quality.
To sum up, the design process of Microvia Substrates needs to comprehensively consider factors such as the function, hierarchy, thermal management and protective measures of the circuit board. By rationally utilizing the tools and methods provided by CAD software, designers can efficiently complete the design of Microvia Substrates and ensure that the final product meets performance and reliability requirements.
What is the manufacturing process for Microvia Substrates?
Microvia Substrates’ manufacturing process is complex and sophisticated, involving a series of critical steps and special processes to ensure the quality and reliability of the final product. The manufacturing process of Microvia Substrates will be analyzed in detail below, let us understand it in depth.
The first step in manufacturing Microvia Substrates is to prepare the substrate. Glass fiber reinforced epoxy resin is usually used as the base material, and its surface requires special treatment to improve adhesion. Next, the surface of the substrate is coated with copper foil to form a conductive layer for subsequent circuit layer printing.
One of the features of Microvia Substrates is its microvias, which are used to connect circuits at different levels. In this step, Microvia holes are drilled into the substrate using laser drilling technology and a special filling material, usually copper or polyimide resin (PI), is coated inside the hole to ensure good connection and insulation.
After the Microvia holes are filled, the circuit layer will be printed. The desired circuit layout is formed by covering the printed circuit pattern on the surface of the copper foil and using chemical etching to remove the uncovered copper foil. This step requires precise control and processing to ensure the accuracy and clarity of the circuit pattern.
The final step is to metallize and surface coat the manufactured Microvia Substrates. Metallization usually uses electroplating technology to deposit a metal layer on the surface of the circuit layer and Microvia hole to enhance its conductivity and corrosion resistance. Next, a protective coating is applied to the surface of Microvia Substrates to protect it from environmental influences and physical damage.
Drilling of Microvia holes is one of the key steps in the manufacturing of Microvia Substrates. Using laser drilling technology can achieve tiny hole diameters and high precision, ensuring the quality and reliability of Microvia.
The chemical etching process requires precise control and monitoring to ensure correct circuit patterning and avoid unnecessary etching errors. Precise process parameters and real-time monitoring equipment are the key to ensuring the quality of chemical etching.
The electroplating process is used to enhance the conductivity and corrosion resistance of the Microvia Substrates surface and requires strict control of the composition and temperature of the plating solution to ensure uniform metal deposition and good coating quality.
Microvia Substrates’ manufacturing process requires a high degree of expertise and technology to ensure the quality and performance of the final product meet requirements. Through the introduction of the above steps and special processes, I believe readers will have a deeper understanding of the manufacturing process of Microvia Substrates.
What are the specific manufacturing steps for Microvia Substrates?
During the manufacturing process of Microvia Substrates, a series of precise steps are required to ensure the quality and performance of the final product. The following are the specific manufacturing steps of Microvia Substrates:
First, the process of manufacturing Microvia Substrates begins with the substrate preparation phase. At this stage, a suitable substrate needs to be selected and surface treated to ensure good adhesion.
Next comes the drilling and filling of the Microvia holes. Microvia holes are a key component in Microvia Substrates, they allow connections between electronic components. In this step, laser drilling technology is used to drill tiny holes in the substrate, which are then filled with conductive material, such as copper, to create connections.
Printing circuit layers is the next important step in manufacturing Microvia Substrates. In this process, a circuit pattern is printed on the substrate and photolithography is used to precisely define the location of the Microvia holes.
Next comes chemical etching, a key step in the process of manufacturing Microvia Substrates. Chemical etching forms the structure of circuit patterns and Microvia holes by removing unwanted metal in predefined areas. This process ensures the accuracy and precision of the circuit.
After completing the preparation of circuit layers and Microvia holes, metallization and surface coating are essential steps. The metallization process covers the surface with a layer of metal, usually copper, to provide electrical conductivity to the circuit. Surface coatings are used to protect Microvia Substrates from environmental influences and mechanical damage.
In summary, manufacturing Microvia Substrates is a complex and precise process that requires multiple critical steps to ensure the quality and performance of the final product. From substrate preparation to final metallization and surface coating, each step is critical and requires a high degree of expertise and technology. Through careful design and precise control of each step, high-quality, reliable Microvia Substrates can be produced to meet the requirements of various electronic devices.
How much do Microvia Substrates cost?
The cost of Microvia Substrates is affected by a variety of factors, here are some of the main ones:
Board Materials: The cost of Microvia Substrates is affected by the type and quality of board materials selected. Common board materials include FR-4, polyimide (PI), polytetrafluoroethylene (PTFE), etc. The prices of different materials vary greatly.
Number of layers and layer thickness: The cost of Microvia Substrates is closely related to its number of layers and layer thickness. Multilayer boards generally cost more to manufacture than double-sided or single-sided boards, and thicker layer thicknesses also increase manufacturing costs.
Line width/line spacing: The line width and line spacing of Microvia Substrates determine the conductor spacing and conductor width on the circuit board. The smaller the line width/line spacing, the higher the production process requirements and the manufacturing cost will increase accordingly.
Pore size: The size of the pores in Microvia Substrates affects manufacturing costs. Smaller hole diameters typically require higher-precision machining equipment and processes, thus increasing manufacturing costs.
Special process requirements: If Microvia Substrates has special process requirements, such as blind vias, buried vias, impedance control, etc., the manufacturing cost will increase. These special process requirements require more complex processing and higher-level equipment.
Production Volume: Mass production of Microvia Substrates is generally less expensive than small-scale production. Because large-scale production enables more efficient processes and better resource utilization, thereby reducing the cost per unit of product.
Supply chain factors: Supply chain stability and supplier selection will also have an impact on Microvia Substrates’ costs. A stable supply chain and suitable suppliers can provide more competitive prices and better services.
Design complexity: The design complexity of Microvia Substrates will affect manufacturing costs. Complex designs may require more processing steps and more materials, increasing costs.
Therefore, the cost of Microvia Substrates is determined by multiple factors, and manufacturers and designers need to consider these factors to ensure that costs are kept as low as possible while meeting performance and quality requirements.
What materials are Microvia Substrates made of?
Microvia Substrates are key components in modern electronic devices, and their performance and reliability are directly affected by material selection. Below we will introduce the types of materials commonly used in Microvia Substrates as well as their characteristics, properties and impact on the performance of Microvia Substrates.
Commonly used material types for Microvia Substrates include:
FR-4 (fiberglass reinforced epoxy resin): FR-4 is a common substrate material with excellent mechanical strength and heat resistance, and is suitable for a variety of applications. Its dielectric constant and dielectric loss are low, providing good signal transmission performance.
PTFE (polytetrafluoroethylene): PTFE has excellent high-frequency performance and chemical stability and is suitable for high-frequency applications. Its dielectric constant is very low, which can reduce losses in signal transmission and improve system performance.
BT (bisphenol A-type epoxy resin): BT material has high thermal stability and high temperature resistance, and is suitable for the manufacture of high-density circuit boards. Its thermal expansion coefficient is low, which can reduce component spacing changes caused by thermal expansion and improve system reliability.
Rogers: Rogers material is a specialized high-performance substrate material with excellent high-frequency performance and dimensional stability. Its dielectric constant and dielectric loss are very low and can meet the needs of high-speed digital signal and radio frequency signal transmission.
Each of these materials has its own characteristics, and choosing the right material has an important impact on the performance of Microvia Substrates. For example, for high-frequency applications, choosing materials with low dielectric constant and dielectric loss can reduce losses in signal transmission and improve system performance. For high-density circuit boards, choosing materials with lower thermal expansion coefficients can reduce component spacing changes caused by thermal expansion and improve system reliability.
To sum up, the material selection of Microvia Substrates is crucial. Different material types have different characteristics and properties. Choosing the right materials can effectively improve the performance and reliability of Microvia Substrates and meet the needs of different applications.
Who makes Microvia Substrates?
The manufacturing of Microvia Substrates is a complex and precise process that requires highly specialized equipment and technology. In the current electronics industry, many companies are dedicated to the manufacturing of Microvia Substrates, but choosing the right manufacturer is crucial to ensuring product quality and reliability.
In the process of manufacturing Microvia Substrates, the main manufacturers are usually specialized electronic manufacturing companies with advanced production equipment, rich experience and high-level technical teams. These manufacturers are often able to provide comprehensive services, including turnkey solutions from design to production, to meet the various needs of their customers.
As a well-known electronics manufacturer, our company has many years of Microvia Substrates manufacturing experience and rich technology accumulation. We are committed to providing customers with high-quality, reliable Microvia Substrates products to meet the needs of different industries and application fields.
Our manufacturing process uses the most advanced technology and equipment to ensure product quality reaches industry-leading levels. Our technical team has rich experience and professional knowledge and is able to provide customized solutions according to customers’ specific requirements and provide customers with professional technical support and consulting services.
In addition to high-quality products and professional technical support, our company also focuses on cooperation and communication with customers to ensure that we can fully understand customer needs and respond to and solve customer problems and concerns in a timely manner. We are committed to establishing long-term and stable cooperative relationships and growing and developing together with our customers.
In short, by choosing our company as the manufacturer of Microvia Substrates, you will receive high-quality products, professional technical support and excellent customer service. We will wholeheartedly provide you with the most satisfactory solutions to help you achieve your business goals and achieve success.
What are the five characteristics of great customer service?
Excellent customer service is paramount in Microvia Substrates design and manufacturing. Here are five key features and suggestions on how to get Microvia Substrates design and manufacturing services that meet your expectations.
Prompt response: Excellent customer service means a manufacturer is responsive to customer needs and questions in a timely manner. Regarding the design and manufacturing process of Microvia Substrates, manufacturers should respond quickly to customer inquiries, provide professional advice, and resolve any issues promptly. What customers need is high efficiency and quick feedback to ensure the project progresses smoothly.
Professional knowledge: Manufacturers need to have deep professional knowledge and experience and be able to provide customers with comprehensive technical support. They should understand the design principles, manufacturing processes and material properties of Microvia Substrates, as well as the latest development trends in the industry. By continually updating their knowledge and sharing it with their customers, manufacturers can build relationships of trust and collaboration.
Customized solutions: Every customer’s needs may be different, so manufacturers should be able to provide customized solutions that meet the customer’s specific needs. They should be able to flexibly adjust their manufacturing processes, fine-tune them according to customer requirements, and provide personalized service. This ensures that customers receive the most appropriate Microvia Substrates design and manufacturing solutions.
Good communication: Establishing good communication channels is crucial to ensuring a smooth project. Manufacturers should maintain close contact with customers, promptly update project progress, share important information, and promptly resolve any misunderstandings or issues in communication. By establishing open and transparent communication mechanisms, manufacturers can enhance collaborative relationships with customers and increase project success rates.
After-Sales Support: Excellent customer service includes not only the project execution phase, but also after-sales support after the project is completed. Manufacturers should provide ongoing technical support and service to customers to ensure smooth operation when using Microvia Substrates. This may include support with training, maintenance services, troubleshooting, etc. to ensure customer satisfaction and confidence in the product.
In order to obtain Microvia Substrates design and manufacturing services that meet their expectations, customers should actively choose to cooperate with manufacturers that possess the above characteristics. When choosing a manufacturer, they should conduct full investigation and evaluation to understand the manufacturer’s professionalism, service quality and customer reputation. Communicate deeply with manufacturers and ensure both parties have a clear understanding of project goals and expectations. Most importantly, a strong long-term relationship is established to ensure the success and sustainability of future projects.
FAQS
How can one ensure effective communication with Microvia Substrates manufacturers?
Effective communication with Microvia Substrates manufacturers is essential for ensuring that design specifications, quality standards, and delivery timelines are met satisfactorily. It involves clearly articulating project requirements, providing detailed technical documentation, establishing regular channels for feedback and updates, and fostering open dialogue to address any issues or concerns promptly. Maintaining transparency and collaboration throughout the manufacturing process enhances the likelihood of achieving successful outcomes.
What are Microvia Substrates?
Microvia Substrates are a type of printed circuit board (PCB) technology characterized by small diameter holes known as microvias. These boards are used extensively in modern electronics for their high-density interconnect capabilities and improved signal integrity.
What are the advantages of using Microvia Substrates?
Microvia Substrates offer several advantages, including increased routing density, improved signal integrity, reduced signal loss at high frequencies, and enhanced reliability due to reduced susceptibility to via failures.
How are Microvia Substrates manufactured?
The manufacturing process for Microvia Substrates involves several key steps, including material preparation, layer buildup, laser drilling of microvias, electroplating, and surface finishing. Specialized equipment and techniques are employed to ensure precise alignment and high-quality microvia formation.