What is Aluminum Oxide PCB|AL203 PCB?
Aluminum Oxide PCB|AL203 PCB Manufacturer.As a leading manufacturer of Aluminum Oxide PCBs (Al2O3 PCBs), we specialize in producing high-quality substrates that offer excellent thermal conductivity and electrical insulation. Our Al2O3 PCBs are ideal for high-power and high-frequency applications, providing superior performance and reliability. With advanced manufacturing techniques and strict quality control, we ensure that our Aluminum Oxide PCBs meet the highest industry standards.
Aluminum Oxide PCB, also known as alumina PCB or Al2O3 PCB, is a high-performance printed circuit board based on alumina ceramic substrate. Compared with traditional fiberglass reinforced epoxy resin (FR4) PCB, Aluminum Oxide PCB has excellent thermal management and mechanical properties, and is especially suitable for electronic equipment in high-power and high-temperature environments.
Aluminum Oxide PCB|AL203 PCB design Reference Guide.
Aluminum Oxide PCB (AL203 PCB), as a printed circuit board based on alumina ceramic substrate, has unique characteristics and wide range of applications. This guide will introduce the key points of AL203 PCB design to help engineers and designers better understand and apply this technology.
AL203 PCB uses high-purity alumina ceramic as the substrate material, which has excellent thermal conductivity and electrical insulation properties. It is commonly used in high-power and high-frequency electronic equipment to effectively manage heat and provide stable circuit performance.
One of the main advantages of the AL203 PCB is its excellent thermal management capabilities. When designing, consideration should be given to maximizing the use of the high thermal conductivity of aluminum oxide, rational layout of heat dissipation components, and optimization of circuit layout to ensure stable operation of electronic components in high-temperature environments.
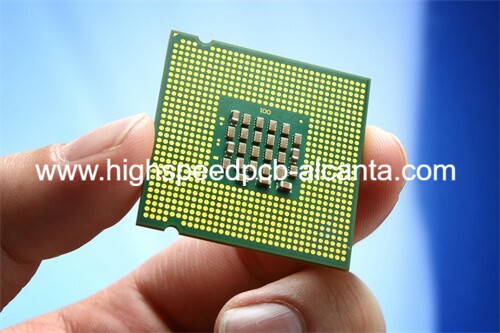
Aluminum Oxide PCB|AL203 PCB Manufacturer
In order to minimize signal interference and electromagnetic interference, the circuit layout of the AL203 PCB needs to follow strict design specifications. The use of multi-layer design can effectively isolate different signal layers and power layers, improving the anti-interference ability and overall performance of the circuit.
When selecting components and welding materials, their compatibility with alumina must be considered. In particular, the welding process should use materials that can bond well with the ceramic substrate and maintain stable performance to ensure reliability and consistency during the manufacturing process.
AL203 PCB performs well in high frequency applications and is able to effectively transmit and process high frequency signals. During the design process, special attention needs to be paid to the impedance matching and loss control of signal transmission lines to ensure circuit stability and signal integrity.
Through this guide, you can understand the design points of AL203 PCB and its importance and application in the electronic field. Effectively utilizing the advantages of AL203 PCB can bring greater reliability, performance and innovation to your projects.
What material is used in Aluminum Oxide PCB|AL203 PCB?
Aluminum Oxide PCB, namely aluminum oxide PCB (Al2O3 PCB), is a high-performance printed circuit board based on alumina ceramic substrate. It uses aluminum oxide as the main material, which has excellent electrical insulation properties and excellent thermal conductivity properties, and is suitable for electronic applications requiring high temperature and high power environments.
Alumina ceramic substrate is the core material of Aluminum Oxide PCB. It has a high degree of thermal conductivity, typically between 20-30 W/m·K, which is significantly higher than common FR4 glass fiber reinforced epoxy PCB (approximately 0.3 W/m·K). This high thermal conductivity enables Aluminum Oxide PCB to effectively manage the heat generated by electronic components and maintain circuit stability and reliability.
Aluminum oxide has excellent electrical insulation properties and can effectively prevent short circuits and leakage between electronic components. This makes Aluminum Oxide PCB particularly suitable for high-frequency and high-voltage electronic equipment, such as power electronics and radio frequency (RF) applications.
Aluminum Oxide PCBs are capable of withstanding higher operating temperatures, often reaching 150°C or higher. This allows it to maintain stable electrical properties in high-temperature environments, making it suitable for fields that require high-temperature resistance, such as automotive electronics, aerospace, and industrial control.
Aluminum oxide has good chemical stability and corrosion resistance, and can resist the erosion of chemicals and humidity, extending the service life of PCB and improving the reliability of equipment.
The manufacturing process of Aluminum Oxide PCB includes substrate processing, copper foil deposition, photolithography and etching, drilling, assembly and welding. Each step in the manufacturing process needs to be strictly controlled to ensure the accuracy and reliability of PCB to meet complex circuit design and high-performance requirements.
To sum up, Aluminum Oxide PCB plays an important role in many high-performance electronic devices due to its excellent thermal management capabilities, electrical insulation properties and high temperature resistance. With the advancement of technology and the expansion of application fields, Aluminum Oxide PCB will continue to demonstrate its irreplaceable advantages in fields such as power electronics, automotive electronics, and aerospace.
What size are Aluminum Oxide PCB|AL203 PCB?
Aluminum Oxide PCB, also known as AL203 PCB, is a printed circuit board based on an alumina ceramic substrate with unique dimensional characteristics suitable for a variety of high-performance electronic equipment and industrial applications. This article will explore the size range of Aluminum Oxide PCB and its importance in electronic engineering.
Aluminum Oxide PCB is widely used in fields that require high thermal conductivity and high temperature resistance, such as power electronics, automotive electronics and industrial control systems. Different application scenarios have different requirements for PCB size. From small smart devices to large industrial control devices, Aluminum Oxide PCB can provide suitable size options.
The size of the PCB directly affects the circuit layout and component mounting density. The design of Aluminum Oxide PCB usually takes into account the layout and heat dissipation requirements of electronic components, and the size can optimize the performance and reliability of the circuit.
The manufacturing process of Aluminum Oxide PCB involves precise material cutting, drilling and metallization steps. Accurate dimensional control is one of the key factors to ensure product quality and stable performance.
Specifically, the size of Aluminum Oxide PCB can be flexibly adjusted according to specific applications and design needs. Common size ranges include but are not limited to:
Small size PCB: used in consumer electronics such as mobile phones and smart wearable devices, usually smaller in size to accommodate the compact design of the device.
Medium size PCB: widely used in industrial control systems, power converters and other equipment, the size is moderate, taking into account the heat dissipation effect and meeting assembly requirements.
Large-size PCB: Used for high-power equipment such as electric vehicles and energy management systems. It is larger in size and can accommodate complex circuit layouts and large electronic components.
Generally speaking, Aluminum Oxide PCB has a wide range of sizes and is flexible, able to meet the design needs and technical challenges in different application scenarios. Through reasonable size design and manufacturing process control, Aluminum Oxide PCB can operate stably and reliably in high temperature, high frequency and high power environments, providing a solid foundation and support for the development of modern electronic technology.
The Manufacturer Process of Aluminum Oxide PCB|AL203 PCB.
Aluminum Oxide PCB, also known as AL203 PCB, is a printed circuit board based on a high thermal conductivity alumina ceramic substrate, suitable for electronic applications requiring high thermal management and high temperature resistance. The manufacturing process of Aluminum Oxide PCB will be introduced in detail below.
The manufacturing of Aluminum Oxide PCB starts with substrate preparation. First, high-purity alumina ceramic is selected as the substrate material, which has excellent electrical insulation and thermal conductivity properties. The surface of the substrate needs to undergo strict cleaning and surface treatment to ensure the accuracy and reliability of subsequent processes.
On the prepared alumina ceramic substrate, a thin layer of copper foil is coated by chemical deposition or mechanical bonding. Copper foil not only serves as a conductive layer for circuit connections, but also enhances the structural strength and thermal conductivity of the PCB, forming a good combination with the alumina substrate.
Next comes the photolithography and etching process, which are key steps in making Aluminum Oxide PCB circuit patterns. First, a light-sensitive photoresist layer is coated on the surface of the copper foil, and then the circuit design pattern is projected onto the photoresist layer using photomask technology. Subsequently, in a chemical etching solution, the unexposed photoresist is removed, thereby exposing the portion of the copper foil that needs to form a conductive path.
After the circuit pattern is completed, a high-precision CNC drilling machine is used to drill holes at the designated locations according to the design requirements. These holes will be used to install and connect electronic components, ensuring that the PCB can effectively interconnect with other system components.
After drilling is complete, assembly and welding are performed. Pre-selected electronic components are accurately mounted on the PCB through automated equipment, and the components are permanently connected to the copper foil using hot melt soldering technology or surface mount technology (SMT).
Finally, conduct testing and quality control. Verify the performance and reliability of Aluminum Oxide PCB through various methods such as electrical testing, functional testing and reliability testing. Only through strict quality control processes can we ensure that each manufactured PCB meets design requirements and industry standards.
Through the above-mentioned fine manufacturing process, Aluminum Oxide PCB can not only meet the needs of various high-temperature and high-power applications, but also provide stable electrical performance and long-term reliability, providing important support and guarantee for the development of modern electronic technology.
The Application area of Aluminum Oxide PCB|AL203 PCB.
Aluminum Oxide PCB, also known as AL203 PCB, is a printed circuit board based on an alumina ceramic substrate. It has excellent thermal management and mechanical strength and is suitable for a variety of demanding applications. The following are its main application scenarios:
In the field of power electronics, Aluminum Oxide PCB is widely used due to its excellent thermal conductivity and high temperature stability. It is commonly used in key components such as power converters, inverters, DC power supplies and electric vehicle charging equipment. AL203 PCB can effectively reduce the operating temperature of electronic components, improve the energy efficiency and reliability of the system, and adapt to the requirements of high power density and long-term stable operation.
In automotive electronic systems, Aluminum Oxide PCB plays an important role. With the popularity of electric vehicles and hybrid vehicles, the requirements for electronic systems are becoming increasingly stringent. AL203 PCB plays a key role in the drive control, battery management system (BMS), on-board charger and electric power converter of electric vehicles, ensuring efficient operation and safety of the system.
In the field of industrial control, Aluminum Oxide PCB is widely used in automation systems, robot control and efficient energy management systems. Its high temperature resistance, vibration resistance and corrosion resistance enable it to operate stably in harsh industrial environments. AL203 PCB supports complex circuit design and high-density component layout, meeting the high requirements for stability and reliability of industrial automation and data acquisition systems.
In addition to industrial and automotive applications, Aluminum Oxide PCBs are also widely used in high-end consumer electronics products, such as communication equipment, wireless network equipment, and high-performance computers. AL203 PCB can provide excellent electrothermal performance and stable electrical signal transmission, adapting to the needs of complex circuit boards, such as high-frequency signal processing and low-noise design.
To sum up, Aluminum Oxide PCB has become an indispensable and important part of modern electronic technology with its unique material advantages and diversified application capabilities. With the advancement of technology and the growth of market demand, it is expected that AL203 PCB will play a wider role in more fields and promote the continuous improvement of the performance and reliability of electronic products.
What are the advantages of Aluminum Oxide PCB|AL203 PCB?
Aluminum Oxide PCB, or AL203 PCB, is a printed circuit board based on an alumina ceramic substrate. It has many superior properties and is suitable for a variety of demanding electronic applications. Here are its main advantages:
One of the main advantages of Aluminum Oxide PCB is its excellent thermal conductivity. Alumina ceramic substrates can effectively conduct heat, help electronic equipment effectively dissipate heat during high-power operation, reduce component temperatures, and improve system stability and reliability.
Compared with traditional fiberglass reinforced epoxy resin (FR4) PCB, Aluminum Oxide PCB has higher mechanical strength. It resists mechanical vibration and shock while maintaining stability in harsh environmental conditions, making it suitable for demanding industrial and automotive electronics applications.
AL203 PCB has excellent electrical insulation properties, which can effectively prevent electrical short circuits and leakage, ensuring the safe operation of electronic equipment. This makes it particularly suitable for high-frequency circuits and microwave applications, ensuring the stability and accuracy of signal transmission.
Due to its material properties, Aluminum Oxide PCB is able to withstand high-temperature environments, often operating in a temperature range of hundreds of degrees Celsius. This makes it an important choice in power electronics, aerospace and military fields to meet the needs of electronic equipment in complex and high-temperature environments.
As one of the main materials, alumina has high environmental protection and sustainability. The manufacturing process of Aluminum Oxide PCB is relatively low-carbon, in line with the development trend of modern green manufacturing, while reducing the negative impact on the environment.
To sum up, Aluminum Oxide PCB has shown obvious advantages in the electronic field with its high thermal conductivity, superior mechanical strength, good electrical properties, high temperature tolerance and environmental protection characteristics. It can not only meet the requirements of complex circuit design, but also improve the performance and reliability of electronic equipment, promote technological progress and application expansion.
FAQ
What is Aluminum Oxide PCB?
Aluminum Oxide PCB (aluminum oxide PCB) is a printed circuit board whose substrate is made of alumina ceramic material. This material has excellent thermal conductivity and mechanical strength, making it suitable for electronic equipment in high-power and high-temperature environments.
How is Aluminum Oxide PCB different from traditional FR4 PCB?
Alumina PCB has significant advantages in thermal management and mechanical strength compared to traditional fiberglass reinforced epoxy resin (FR4) PCB. It can dissipate heat more effectively and is suitable for applications requiring high thermal conductivity and high temperature resistance.
What application fields is Aluminum Oxide PCB suitable for?
Alumina PCB is widely used in power electronics, automotive electronics, industrial control and other fields. For example, it is used in power converters, electric vehicle control systems and industrial automation equipment, as well as in environments that require high temperature resistance and vibration resistance.
What are the advantages of Aluminum Oxide PCB?
Alumina PCB has excellent thermal management capabilities and mechanical strength, which can effectively reduce the operating temperature of electronic components and improve system reliability and performance. In addition, it also has the characteristics of energy saving and environmental protection, which is in line with the development trend of modern green technology.