Microtrace RF PCB Manufacturer.Microtrace RF PCB Manufacturer specializes in crafting high-quality printed circuit boards (PCBs) tailored for radio frequency (RF) applications. With precision engineering and advanced manufacturing techniques, Microtrace ensures optimal performance and reliability for RF circuits in diverse industries such as telecommunications, aerospace, and medical devices. Their expertise lies in producing PCBs with intricate RF designs, low signal loss, and minimal interference, meeting the stringent demands of modern wireless communication systems. Whether it’s for satellite communication, radar systems, or wireless networking, Microtrace RF PCBs stand out for their superior quality and cutting-edge technology.
In the field of modern wireless communications, RF (radio frequency) PCBs play a vital role. They are key components that support and connect radio frequency electronic components. This article will delve into the RF PCB manufacturing process and focus on how Microtrace, a leading RF PCB manufacturer, provides customers with excellent solutions. Microtrace not only has advanced manufacturing technology and strict quality control processes, but also has a professional engineering team that can provide customers with customized RF PCB design and manufacturing services to meet their specific application needs.
What is RF PCB?
An RF PCB (Radio Frequency Printed Circuit Board) is a critical component specifically designed to handle radio frequency signals. In the development of modern communication technology, the processing of radio frequency signals has become more and more important, and RF PCB is designed to meet this demand. Compared with ordinary printed circuit boards, RF PCBs have a more complex and precise structure, as well as special material selection to ensure stable performance and reliability at high frequencies.
First, the structure of RF PCB has a unique design. In order to reduce signal attenuation and distortion at high frequencies, RF PCB usually adopts a special layer stack structure, including ground layer, power layer and signal layer. This layer stacking design can effectively reduce signal transmission loss and improve signal anti-interference ability.
Secondly, the material selection of RF PCB is crucial. Traditional FR-4 materials produce large losses at high frequencies, so special materials such as PTFE (polytetrafluoroethylene) and Rogers are usually used in the manufacturing of RF PCBs. These materials have lower dielectric losses and higher dielectric constants and can better support the transmission and processing of high-frequency signals.
As a leading company specializing in RF PCB manufacturing, Microtrace is well versed in the technical requirements and market demands of RF PCB manufacturing. We not only have advanced manufacturing equipment and technology, but also an experienced engineering team, able to provide customers with customized RF PCB solutions. Whether in the fields of communications, radar, satellite navigation or radio frequency identification, Microtrace’s RF PCBs can meet customers’ high requirements for performance, reliability and stability.
All in all, RF PCBs play a vital role in the field of modern wireless communications. They are the core components that support and connect radio frequency electronic components. Microtrace is committed to providing customers with high-performance, high-reliability RF PCB solutions to help customers stand out in the highly competitive market and achieve continued business growth and development.
How to design RF PCB?
The design of RF PCB is a complex and critical task that requires comprehensive consideration of multiple factors to ensure stability and reliability in high-frequency environments. As a leading RF PCB manufacturer, Microtrace has an experienced engineering team and is able to provide customers with customized design services to meet their specific application needs.
First, frequency is one of the key considerations in RF PCB design. Different frequency ranges require different design parameters and technical solutions. Microtrace’s engineers have deep expertise in selecting the appropriate frequency range according to customer requirements and optimizing the design to ensure signal transmission and reception quality.
Secondly, transmission line characteristics are critical to RF PCB design. The characteristic parameters of the transmission line, such as impedance matching, transmission speed and propagation delay, directly affect the stability and speed of the signal. Microtrace’s engineering team is familiar with various transmission line technologies and can make appropriate selections and optimizations based on specific application scenarios.
In addition, noise and interference are also one of the key factors to consider in RF PCB design. In high-frequency environments, any small noise and interference may adversely affect signal quality. Microtrace engineers effectively reduce the impact of noise and interference on system performance through precise design and layout, using shielding technology and suppression measures.
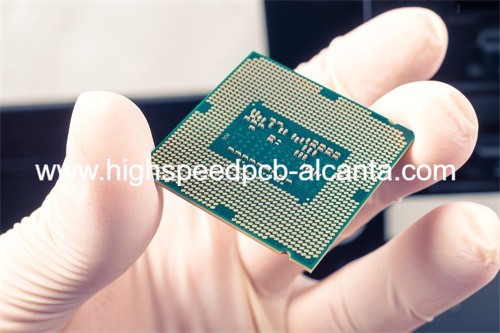
Microtrace RF PCB Manufacturer
Microtrace is committed to providing customers with customized RF PCB design services. We not only focus on technical performance, but also focus on close cooperation with customers. Our engineering team will fully communicate with customers to understand their specific needs and application scenarios, and tailor the optimal design solution for them. Whether in communications, radar, radio or other fields, Microtrace can provide customers with high-performance, high-reliability RF PCB solutions.
During the RF PCB design process, Microtrace’s engineering team will continue to pay attention to technological innovation and industry development, and constantly optimize design solutions to meet the changing needs of customers. We will provide customers with excellent design services in a professional and responsible manner, and jointly promote the development and application of wireless communication technology.
What is the manufacturing process of RF PCB?
The manufacturing process of RF PCB is a complex and precise process that involves multiple key steps, each of which has an important impact on the performance and reliability of the final product. At Microtrace, we are committed to employing state-of-the-art manufacturing technology and strict quality control processes to ensure that each RF PCB meets our customers’ high requirements.
First of all, the first step in manufacturing RF PCB is raw material preparation. This includes selecting appropriate substrate materials, often using materials with high frequency properties such as PTFE (polytetrafluoroethylene) or FR-4, to ensure excellent performance at high frequencies. In addition, the metal foil material for the printed circuit needs to be prepared, usually copper foil.
Next comes the plate processing stage. At this stage, the board is cut to the required size and surface-treated, including chemical treatments, to facilitate subsequent printing and circuit connections.
Then comes the printing stage, which is one of the key steps in the RF PCB manufacturing process. Circuit connections can be formed by printing designed circuit patterns onto the surface of the board. Microtrace uses advanced printing technology to ensure printing quality and accuracy.
Molding is the next important step, this is to ensure that the shape and dimensions of the PCB meet the design requirements. The forming process may include operations such as mechanical cutting, punching and contouring to ultimately form a PCB board that meets the requirements.
Finally comes the assembly stage. At this stage, electronic components are mounted on the PCB board and connected by soldering etc. This process requires a high degree of precision and skill to ensure that each element is positioned and connected correctly.
Microtrace pays attention to detail and quality control in every manufacturing step, and we employ strict inspection and testing processes to ensure that each RF PCB has excellent performance and reliability. We constantly pursue technological innovation and process improvement to meet our customers’ changing needs and provide them with the best RF PCB solutions.
How much does it cost to manufacture an RF PCB?
The manufacturing cost of RF PCB is a crucial consideration in the entire production process. Microtrace understands that this cost is affected by a number of factors, so we employ a range of strategies to ensure our customers receive competitive pricing and are able to provide a quote customized to their needs.
First, the manufacturing cost of RF PCB is affected by the board type. Different types of boards have different properties and prices. For example, PTFE (polytetrafluoroethylene) is a commonly used high-frequency material with excellent dielectric properties, but is relatively expensive. FR-4 is a commonly used general-purpose plate with a relatively low price. Microtrace will recommend the most suitable plate type based on the customer’s needs and budget and provide a corresponding quotation.
Secondly, the manufacturing cost of RF PCB is also affected by the number of layers. The higher the number of layers, the higher the manufacturing cost will usually be. This is because increasing the number of layers increases the complexity and difficulty of manufacturing the board. Microtrace’s engineering team works with customers to assess their project needs, provide the most cost-effective layer options, and ensure cost control without compromising performance.
In addition, the size and quantity of RF PCBs will also have an impact on manufacturing costs. Generally speaking, larger size PCBs require more materials and processing costs, so the cost is relatively higher. And mass production can reduce unit costs because fixed costs can be reduced through economies of scale. Microtrace will flexibly adjust the quotation according to the customer’s order volume and size requirements to ensure that customers get the best price.
To sum up, the manufacturing cost of RF PCB is affected by many factors, but Microtrace is always committed to providing competitive prices and customized quotations according to customer needs. Our goal is to provide customers with high-performance, high-reliability RF PCB solutions while ensuring reasonable prices so that customers can obtain the greatest value for money.
What materials are RRF PCB made of?
RF PCB usually uses special materials to meet the requirements of high-frequency signal transmission. At Microtrace, we understand how important material selection is to RF PCB performance and reliability, so we carefully select each material and work closely with our customers to ensure that the material selection for RF PCBs fully meets their application needs.
First, let’s take a look at two commonly used RF PCB materials: PTFE (polytetrafluoroethylene) and FR-4.
PTFE is a high-performance material with excellent insulation properties and high-frequency signal transmission characteristics. Due to its low dielectric constant and low loss tangent, PTFE is widely used in RF PCBs requiring high frequency performance. It can reduce signal loss at high frequencies, provide more stable signal transmission, and is suitable for wireless communications, radar, satellite communications and other fields.
FR-4 is a common glass fiber reinforced epoxy resin material with good mechanical properties and thermal stability. Although its performance at high frequencies is slightly inferior to PTFE, it is still an affordable and reliable choice in many applications. FR-4 is widely used in general RF PCB applications, such as household electronics, automotive electronics and other fields.
At Microtrace, we are not limited to these two common materials, we can also choose other high-performance materials according to customers’ specific needs, such as RO4350B, RO4003C, etc. Our engineering team has extensive experience and expertise and is able to tailor the most appropriate material selection plan for customers based on their application scenarios and performance requirements.
In addition to material selection, we also focus on material quality and supply chain stability. We have established long-term cooperative relationships with a number of well-known material suppliers to ensure the quality and reliability of the selected materials. In terms of material procurement and supply, we strictly implement quality control and supply chain management processes to ensure that every RF PCB has consistent quality and performance.
To sum up, Microtrace is committed to providing customers with high-quality RF PCB solutions. We not only focus on material selection, but also on material quality and supply chain stability to ensure that customers’ application needs are best met.
Who makes RF PCBs?
With the rapid development of modern communication technology, the demand for RF (radio frequency) PCB is becoming more and more urgent, and the choice of supplier will directly affect the performance and reliability of the product. In this highly competitive market, Microtrace RF PCB Manufacturer has become the industry leader with its professional technical strength and excellent service quality.
As a professional RF PCB manufacturer, Microtrace is committed to providing customers with high-performance, high-reliability RF PCB solutions. We have advanced production equipment and rich industry experience to meet the different needs of customers in various application fields. Whether in the fields of communications, medical, automotive or industrial control, Microtrace can provide customers with customized RF PCB products and ensure that their performance and quality meet industry standards.
As a supplier, Microtrace focuses on cooperation and communication with customers. We not only provide products, but also provide solutions as a partner. Our professional team works closely with clients to understand their needs and requirements, provide customized solutions, and provide technical support and services throughout the project. Whether in the design stage or production stage, Microtrace can provide customers with timely and comprehensive support to ensure the smooth progress of the project.
In addition to providing high-quality products and services, Microtrace also focuses on quality management and after-sales service. We strictly implement the production process in accordance with the ISO9001 quality management system and conduct strict quality inspections to ensure that each RF PCB product meets customer requirements and standards. At the same time, we also provide comprehensive after-sales service to solve any problems and difficulties encountered by customers during use.
To sum up, Microtrace, as a manufacturer and supplier of RF PCB, has won the trust and support of its customers with its professional technical strength, excellent service quality and strict quality management system. If you are looking for a reliable RF PCB supplier, Microtrace will be your best choice.
Five Characteristics of Great Customer Service
Excellent customer service is one of Microtrace’s core values, and we understand the importance of a good customer experience for customer satisfaction and long-term relationships. Here are five features of our services:
Prompt response: We value our customers’ time and therefore always respond quickly. Whether it is for inquiry, technical consultation or after-sales service, we will give customers timely feedback and solutions as soon as possible.
Professional technical support: Microtrace has an experienced and skilled engineering team that can provide customers with professional technical support and consulting services. Regardless of the problems encountered during the RF PCB design stage or during the production process, we can provide effective solutions and suggestions.
Customized solutions: We understand that each customer’s needs are unique, so we provide customized RF PCB solutions to meet customers’ specific needs and application scenarios. Whether it is in terms of material selection, process flow or product characteristics, we are able to tailor the optimal solution for our customers.
Quality Assurance: Microtrace always puts product quality first, we strictly implement the ISO quality management system and use advanced quality testing equipment and technology to ensure that each RF PCB meets the highest standards. We are committed to providing stable and reliable products to protect our customers’ projects.
After-sales service: We pay attention to every need of our customers and are committed to establishing long-term cooperative relationships. After product delivery, we still maintain close contact with customers and provide a full range of after-sales service and technical support to ensure customer smoothness and satisfaction during use.
In short, Microtrace has always been customer-centric and committed to providing customers with high-quality products and services. Whether in terms of technical support, customized solutions or after-sales service, we will do our best to create greater value and better experience for our customers.
FAQs
How long is the design cycle of RF PCB?
The design cycle for RF PCB varies depending on the complexity of the project. Typically, a simple design may only take a few weeks to complete, while a more complex project may take several months. The length of the design cycle also depends on the clarity of the initial design requirements provided by the customer and the frequency of communication with the Microtrace team. During the design process, we work closely with our customers to ensure that the design meets their specific application needs and to minimize the design cycle.
What is the maximum operating frequency of RF PCB?
The maximum operating frequency of an RF PCB depends on several factors, including design, manufacturing, and material selection. Generally speaking, the maximum operating frequency of RF PCB can reach the range of several GHz. However, the actual operating frequency also depends on the specific design and manufacturing quality of the RF PCB. Microtrace’s engineering team has the experience and expertise to provide customers with high-performance RF PCB solutions to meet their specific frequency requirements.
How to calculate the manufacturing cost of RF PCB?
The manufacturing cost of RF PCB is affected by many factors, including board type, number of layers, size, quantity, and special process requirements. Microtrace is committed to providing competitive prices and customizing quotes based on our customers’ specific needs. Our sales team will fully communicate with customers to understand their needs and provide them with the most cost-effective solutions.
Can Microtrace provide sample orders?
Yes, Microtrace can provide sample orders. We understand that customers may need to test and verify products before mass production. Therefore, we offer sample order services so that customers can test the products before deciding to proceed with mass production. Customers only need to provide design documents and related requirements, and we will provide them with samples as soon as possible.
What after-sales service does Microtrace provide?
Microtrace is committed to providing customers with a full range of after-sales services. If customers encounter any problems or require technical support during use, our technical team will respond promptly and provide solutions. In addition, we provide product quality assurance services to ensure that customers receive high-performance, high-reliability products. Customer satisfaction is our ultimate goal.