Microtrace PCB Manufacturer.Microtrace PCB Manufacturer specializes in the production of high-quality printed circuit boards (PCBs). With cutting-edge technology and a dedicated team of experts, Microtrace ensures precision and reliability in every PCB they manufacture. Their state-of-the-art facilities allow for efficient production processes, meeting the stringent demands of various industries including aerospace, automotive, and telecommunications. Committed to innovation and customer satisfaction, Microtrace offers customized solutions tailored to meet specific requirements, ensuring optimal performance and durability in every product.
What is a Microtrace PCB?
A micro-trace PCB is a printed circuit board (PCB) with tiny trace lines that is commonly used in high-density electronic equipment and miniature electronics. Micro-trace PCB designs are designed to enable complex circuit layouts and connections within limited space. This type of PCB typically requires precision manufacturing processes and highly optimized wiring designs to ensure good electrical performance and reliability at tiny sizes.
Microtracking PCBs are commonly used in highly integrated electronic devices such as smartphones, tablets, wearables, medical devices, and other portable electronics. Since these devices need to accommodate many functions and components within a limited space, the design of the microtracking PCB must be as compact and efficient as possible.
In order to realize micro-tracking PCB, manufacturers usually use advanced PCB manufacturing technologies, such as laser cutting, photolithography and precision etching. These technologies can achieve fine lines and spacing on small-sized PCBs, allowing more functions to be integrated into smaller spaces.
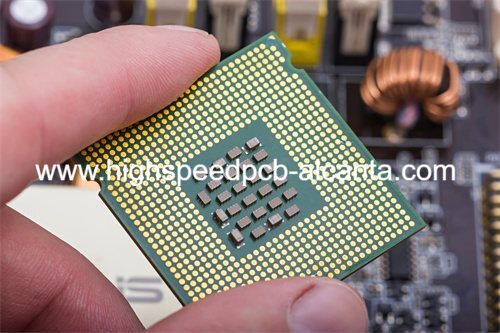
Microtrace PCB Manufacturer
In summary, micro-tracking PCB is a printed circuit board designed for high-density electronic equipment, which is characterized by complex circuit layout and connections in a limited space.
How to Design a Microtrace PCB?
Designing a microtracking PCB requires consideration of many factors, from circuit design to PCB layout and manufacturing process. Here are the general steps:
Determine Requirements: First, identify the specific needs of your microtracking PCB. You need to understand the functional, performance, and size requirements of the circuit you are designing. This may include power requirements, signal transfer rate, packaging type, etc.
Circuit design: Based on your needs, start designing the circuit diagram. Select appropriate components including microcontrollers, sensors, communication modules, etc. Ensure the circuit meets performance specifications and takes into account miniaturization requirements.
PCB Layout: When doing PCB layout, ensure the stability and performance of the circuit. Consider the layout of signal paths, ground and power lines to minimize crosstalk and noise. Minimize the size of the PCB and arrange the location of components appropriately.
Signal integrity: In order to ensure signal integrity, it is necessary to pay attention to the matching impedance and length matching of the signal transmission line. Using technologies such as differential signal transmission and ground plane design can reduce signal distortion and crosstalk.
Power management: Reasonably design the power system to ensure stable and reliable power supply. Taking into account the efficient utilization of power and low power consumption requirements of micro-tracking PCBs.
Thermal Management: Thermal management is particularly important in miniaturized PCB design. Arrange components reasonably and consider heat dissipation design to ensure that the PCB maintains good temperature control under normal operating conditions.
EMI/EMC: Consider electromagnetic interference (EMI) and electromagnetic compatibility (EMC) requirements, and adopt corresponding shielding measures and filtering technology to ensure the stability and reliability of micro-tracking PCBs in the electromagnetic environment.
Manufacturing and Assembly: Select appropriate manufacturing processes and materials to ensure PCB quality and reliability. During assembly, attention to detail is taken to ensure components are soldered and connected correctly.
Testing and Validation: After completion of manufacturing and assembly, the microtracking PCB is fully tested and validated. Including functional testing, performance testing, reliability testing, etc. to ensure that the PCB meets the design requirements.
Optimization and improvement: Continuously optimize and improve the design of micro-tracking PCB based on test results and user feedback. Taking into account the continuous development of technology and changes in market demand, the design is constantly updated and improved.
The above are the general steps for designing micro-tracking PCB. The specific design process will vary according to the actual situation and needs.
What is the Microtrace PCB Fabrication Process?
The micro-tracking PCB manufacturing process is an advanced process for producing printed circuit boards (PCBs) that uses high-precision technology and precise steps to ensure the quality and performance of the final product. Here is a rough description of the manufacturing process:
Design and Layout: The first step in the manufacturing process is the design and layout of the PCB. This involves determining the board’s functionality, size, hierarchy, and placement of components. Designers use specialized software to complete this step and ensure that the design meets specifications and performance requirements.
Material Preparation: Once the design is complete, the manufacturing process requires preparing the materials required for PCB fabrication. These materials include substrates, copper foil, insulation materials, printing inks, etc. The selection and quality of materials directly affects the performance and reliability of the final product.
Graphicalization: PCB manufacturing often uses photolithography to form circuit patterns. In this step, the designed circuit pattern is converted into a graphic image file and then transferred to the substrate surface through photolithography technology.
Lithography and Etching: Lithography uses photosensitizers and masks to transfer graphic images to a photosensitive layer that covers the surface of a substrate. Then, through an etching process, the unnecessary portions of the copper foil are removed from the substrate surface to form the desired circuit pattern.
Adding additional layers: With multilayer PCBs, the steps of repeating photolithography and etching are done multiple times until all necessary layers are formed. Each layer requires proper craftsmanship to ensure accuracy and quality.
Drilling and Adding Components: After the circuit pattern is formed, the PCB needs to be punched in order to add the electronic components. These components are fixed on the PCB surface by methods such as soldering and connected to the circuit pattern.
Testing and Quality Control: The final stage of the manufacturing process is testing and quality control of the PCB. Ensure PCB functionality and performance meet specifications by using various testing methods such as electrical testing, visual inspection, etc.
Final processing and packaging: After completing testing and quality control, the PCB undergoes final processing and packaging. This includes steps such as cleaning, trimming edges, punching holes, marking and packaging for final delivery to the customer.
The micro-tracking PCB manufacturing process uses advanced technology and strict quality control standards to ensure the production of printed circuit board products of high quality, reliability and performance.
How to manufacturing a Microtrace PCB ?
The manufacturing of micro-nano tracking PCB (Printed Circuit Board) is a complex and precise process that requires strict technology and a high degree of professional knowledge. The following are the general steps for manufacturing micro-nano tracking PCB:
Design: First, a detailed PCB design is required, including the requirements for micro-nano tracking technology. Designers use professional PCB design software, such as Altium Designer or Cadence Allegro, to create circuit layouts that ensure accuracy for traceable tiny sizes and high-density layouts.
Material preparation: Select high-quality materials suitable for micro-nano tracking technology, usually special high-frequency materials or materials with specific conductive properties. These materials must have excellent mechanical strength and high temperature resistance to ensure that the PCB is stable and reliable during use.
Graphical image generation: Convert PCB design files into graphical images, which can be achieved through photolithography technology. A laser lithography system is used to transfer the PCB image to a substrate covered with photosensitive material to form the PCB pattern.
Chemical etching: Using chemical etching method, the part of the material not covered by photolithography is etched away from the substrate, leaving the predetermined PCB trace lines. This step requires strict control to ensure tracking accuracy and clarity.
Cleaning and processing: Clean and process the etched PCB substrate to remove residual photoresist and corrosion products to ensure the purity and smoothness of the PCB surface.
Metal Deposition: Depositing a layer of conductive metal (usually copper) on the traces of a PCB through electroplating or other metal deposition techniques to increase conductivity and durability.
Final processing: According to the design requirements, the final processing of the PCB is carried out, such as surface treatment (spraying solder, spraying anti-corrosion layer, etc.) and cutting to obtain the final micro-nano tracking PCB product.
The entire manufacturing process requires strict quality control and testing to ensure that the PCB meets design requirements and standards. Any poor manufacturing process or defects can affect PCB performance and reliability, so quality management is crucial.
How Much Does a Microtrace PCB Cost?
Microtrace PCB prices will vary based on a variety of factors, including board type, number of layers, size, thickness, surface treatment, special process requirements, and more. Generally speaking, Microtrace PCB is slightly more expensive than traditional PCB because Microtrace PCB requires higher precision and more complex processes to achieve micro-circuit tracing.
As a common case, a simple Microtrace PCB might cost in the range of price per square inch (or per square centimeter), plus basic process charges. For more complex and sophisticated Microtrace PCBs, the price will be higher.
In addition, the impact of production volume on price also needs to be considered. Generally speaking, large orders will have lower unit prices, while small batch production costs will be relatively high.
In addition, if special processing or customized services are required, such as special material selection, high temperature tolerance, anti-corrosion treatment, etc., it will have an impact on the price.
Overall, Microtrace PCB prices will vary based on various factors, and it is recommended that you consult the specific PCB manufacturer for an accurate quote.
What materials are Microtrace PCB made of?
Microtrace PCBs are usually composed of a variety of materials that play an important role in the circuit board manufacturing process. Normally, the main components of Microtrace PCB include:
Substrate Material: The body of a Microtrace PCB is typically constructed from the substrate material, which is typically fiberglass-reinforced epoxy (FR-4), which provides the board’s structural support and insulating properties.
Copper foil: Copper foil is a key component of Microtrace PCB. It is plated on the surface of the substrate and used to make circuit paths and connections. Copper foil usually exists in different thicknesses and weights to suit different circuit design needs.
Copper: Copper is a thin layer of copper foil covering a substrate to protect circuit paths from the environment and provide circuit reliability and stability.
Printing inks: Printing inks are commonly used to print marks, logos and graphics, as well as for surface decoration of circuit boards.
Solder Mask: Solder mask is used to cover the surface of a circuit board, protecting areas not covered by circuit connectors, and providing additional insulation protection.
Spray Tin: Spray tin is a thin layer of tin that covers circuit paths and connections to strengthen connections and provide additional protection.
Solder Paste: Solder paste is typically used during circuit board assembly to add solder to the connection areas on the circuit board for soldering electronic components.
Electronic components: Microtrace PCB also includes various electronic components, such as resistors, capacitors, transistors, etc. These components are soldered to the circuit board to form the functional part of the circuit.
In general, Microtrace PCB is usually composed of various materials such as substrate material, copper foil, copper cladding, printing ink, solder resist, tin spray, solder paste and electronic components. These materials together constitute the structural and functional part of the circuit board .
Who manufactures Microtrace PCB ?
Microtrace PCBs are manufactured by a professional electronics manufacturing company. Our company uses advanced technology and equipment and is committed to producing high-quality printed circuit boards (PCBs). We have an experienced engineering team and quality management team to ensure that products meet customer requirements and industry standards.
The manufacturing process of microtrace PCB is subject to strict quality control, and every step from the selection of raw materials to the shipment of the final product is carefully designed and inspected. They use advanced production equipment and advanced processes to ensure PCB precision, performance and reliability.
The company not only produces standard PCBs, but also provides customized solutions to meet the specific needs of different customers. They work closely with customers to understand their needs and provide professional advice and support to ensure the quality and performance of the final product.
Manufacturers of microtrace PCBs focus on technological innovation and continuous improvement to adapt to changing market demands and technology trends. They continuously invest in R&D and technology upgrades to ensure that their products are industry-leading and provide customers with the best solutions.
What are 5 qualities of a good customer service?
Excellent customer service typically has the following five qualities:
Professionalism: A good customer service team has a high level of professional knowledge and skills and can accurately and quickly solve customer problems and needs. They understand all aspects of a product or service and can clearly convey information to customers.
Proactivity: Excellent customer service is not just about passively responding to customer questions, but more importantly, being able to proactively find and solve potential problems. They proactively communicate with customers, providing assistance and advice to ensure customer satisfaction and loyalty.
Reliability: Reliability is one of the cornerstones of customer service. A good customer service team can provide timely and reliable support and assistance when customers need it, consistently maintain a high level of service quality, and build customer trust and dependence on the brand.
Be polite and friendly: Being polite and friendly when communicating with customers is one of the key factors in creating a great customer experience. Excellent customer service representatives always treat customers in a cordial and patient manner, listen to their questions and needs, and respect their opinions and feedback.
Problem-solving skills: Customer service teams need to have problem-solving skills and decisiveness. They should be able to quickly identify and understand customer problems and provide effective solutions to ensure customer satisfaction and loyalty. At the same time, they also need to be flexible and creative to deal with various complex situations and challenges.
FAQS
How long is the manufacturing cycle of Microtrace PCB?
Manufacturing lead time depends on the quantity and complexity of the order. Typically, we can complete rapid prototyping within a few days to a few weeks, and the cycle for mass production will be longer.
What is the quality control system of Microtrace PCB?
We strictly follow the ISO quality management system for production management and implement strict quality control procedures. From raw material procurement to production and manufacturing to final product inspection, we ensure that every process meets quality standards.
How is the customer service for Microtrace PCB?
We value our customers’ needs and feedback and provide timely technical support and after-sales service. Whether it is a problem in product design or production process, we will do our best to meet customer requirements and ensure customer satisfaction.
How to contact Microtrace PCB?
You can contact us through our official website www.microtracepcb.com, or you can contact our customer service team by phone or email, they will be happy to serve you