Micro Via PCB Manufacturing.Micro Via PCB Manufacturing refers to the process of creating printed circuit boards (PCBs) with extremely small vias, which are the pathways that connect different layers of the PCB. This advanced technique enables the construction of intricate electronic circuits in compact devices such as smartphones, tablets, and wearables. By utilizing cutting-edge technology and precise manufacturing processes, micro via PCB manufacturing achieves high-density interconnections while maintaining reliability and performance. It plays a crucial role in the development of miniaturized electronic devices, pushing the boundaries of technology and enabling innovative solutions in various industries.
In the field of modern electronics, Micro Via PCB (printed circuit board) manufacturing technology is attracting increasing attention. Micro Via PCB not only enables higher density wiring, but also enables more powerful performance in small devices. This article will delve into the key steps, materials, and market trends of Micro Via PCB manufacturing, as well as how to ensure customer service quality. The emergence of Micro Via PCB has brought new development opportunities to the electronics industry, and we will unveil the mystery of this eye-catching technology together.
What is Micro Via PCB?
Micro Via PCB, the full name is Micro Vias Printed Circuit Board, is a printed circuit board with micro-hole technology. Compared with traditional printed circuit boards (PCBs), Micro Via PCBs use smaller apertures and higher circuit density, making them widely used in small electronic devices. The core feature of Micro Via PCB is its micro-vias, which typically have a diameter of less than 0.15 mm, which allows more connections and wiring to be accommodated in the same board size, resulting in higher circuit density and more Complex functionality.
The design principles of Micro Via PCB mainly focus on how to minimize the aperture and increase the circuit density, which provides greater flexibility and performance for the design of small electronic products. Compared with traditional electronic products, Micro Via PCB can reduce the size of the circuit board more effectively, thus providing a better solution for increasingly miniaturized devices. In today’s electronics industry, with the continuous development of consumer electronics and portable devices, the demand for Micro Via PCB is also growing.
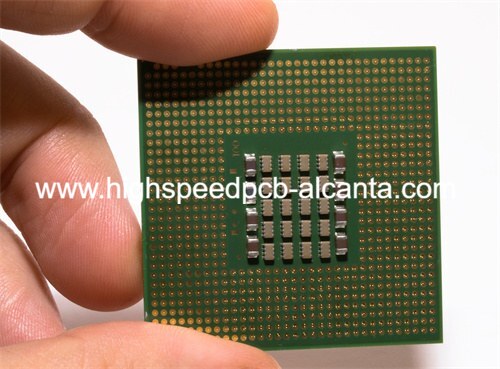
Micro Via PCB Manufacturing
In addition to its application in small devices, Micro Via PCB is also widely used in high-performance and high-density electronic products, such as computer servers, communication equipment, medical equipment, etc. In these areas, Micro Via PCB’s high-density wiring and excellent signal transmission performance make it one of the preferred solutions. For example, in the field of communications, Micro Via PCB can achieve faster and more reliable data transmission, thereby improving the performance and stability of the entire system.
In general, Micro Via PCB is a printed circuit board that uses microvia technology to achieve high-density wiring. Its compact, flexible design and excellent performance make it play an increasingly important role in the design and manufacturing of modern electronic products. With the continuous advancement of technology and the expansion of application scope, Micro Via PCB will continue to contribute to the development and innovation of the electronics industry.
What are the key points in designing Micro Via PCB?
Designing a Micro Via PCB is a complex and critical process that requires careful consideration of multiple factors to ensure the final product meets performance and quality requirements. The following are the main factors to consider when designing Micro Via PCB:
Layout optimization: The first step in Micro Via PCB design is to plan the layout reasonably. During the layout stage, the location and routing paths of individual components need to be considered to minimize signal path length and reduce signal interference. In addition, ensure that the power and ground wires are properly laid out to provide stable power and ground references.
Interlayer stacking: Micro Via PCB usually contains multiple levels of circuits, so the interlayer stacking structure needs to be properly designed. Select the appropriate laminate material and layer arrangement to meet signal transmission and electrical performance requirements and ensure a reliable Micro Via connection.
Micro Via Design: The key features of Micro Via PCB are tiny apertures and high density routing. When designing microvias, you need to consider aperture size, spacing and location, as well as how they are connected to the circuit. At the same time, attention must also be paid to the through-hole quality and reliability of microvias to ensure good electrical connections.
Signal Integrity: Signal integrity is critical in high-speed circuit design. When designing Micro Via PCB, you need to pay attention to issues such as signal transmission timing, power consumption, and electromagnetic compatibility to minimize signal distortion and crosstalk.
Thermal Management: Micro Via PCBs typically have high integration and power density, so thermal management is an important consideration during the design process. Through reasonable layout and heat dissipation design, ensure that the heat on the PCB can be effectively dispersed and discharged to avoid the impact of overheating on circuit performance.
Manufacturing Feasibility: When designing Micro Via PCB, manufacturing feasibility and cost-effectiveness need to be taken into consideration. Select appropriate manufacturing processes and materials to ensure the design can be realized within existing production facilities and meet the customer’s budget and time requirements.
Testing and verification: After the design is completed, testing and verification are required to ensure that the circuit performs as expected. Through simulation, prototype testing and verification, the electrical performance, signal integrity and reliability of Micro Via PCB are checked to ensure product quality and reliability.
In summary, designing Micro Via PCB requires comprehensive consideration of multiple factors such as layout optimization, interlayer stacking, microvia design, signal integrity, thermal management, manufacturing feasibility, and testing and verification to ensure that the final product meets performance and quality Require.
What is the manufacturing process of Micro Via PCB?
Manufacturing Micro Via PCBs is a complex and precise process involving multiple critical steps to ensure the final product meets design requirements and quality standards. Following are the main steps in manufacturing Micro Via PCB:
Before entering the manufacturing stage, the PCB design files need to be prepared first. This includes layout and routing files created by designers using professional PCB design software that incorporate Micro Via’s design specifications and requirements. Design documents need to be carefully reviewed to ensure compatibility with the manufacturing process.
The first step in manufacturing Micro Via PCB is to prepare the substrate. The substrate is typically a fiberglass-reinforced base material such as FR-4 or other high-performance materials. A thin layer of copper foil is applied to the substrate to facilitate the subsequent circuit board manufacturing process.
Next, the designed pattern is transferred to the substrate surface using photolithography technology. This typically involves coating a light-sensitive photoresist on copper foil and then using UV light to expose the pattern through a mask. After exposure, the photoresist in the unexposed areas is chemically removed, leaving areas where circuit patterns are desired.
After photolithography is completed, the surface of the copper foil needs to be electroplated to increase the thickness and conductivity of the circuit lines. This usually involves depositing a thin layer of copper on the surface of the substrate and then chemically removing the photoresist, leaving the desired circuit pattern.
Using laser drilling or mechanical drilling techniques, holes are drilled into the substrate to create Micro Via. These tiny holes are used to connect circuit lines between different layers.
After drilling, the unnecessary copper foil is removed through a chemical etching process, leaving the desired circuit pattern and Micro Via.
The last step is to laminate different PCB layers according to the design requirements to form a complete Micro Via PCB structure. In this process, the Micro Via between each layer plays a connecting role to ensure the connectivity of the circuit.
Through these steps, the manufacturing process of Micro Via PCB is completed. This is a process that requires a high degree of expertise and technology to ensure that the quality and performance of the final product is as expected.
How much does it cost to manufacture a Micro Via PCB?
The cost of manufacturing a Micro Via PCB is the combined result of many factors. Below we will explore how these factors affect the cost and explain why Micro Via PCBs are generally more expensive than traditional PCBs.
The design of Micro Via PCBs typically involves more complex layout and routing to accommodate high-density wiring and tiny aperture requirements. This requires more engineer time and effort, so design complexity is one of the major factors affecting cost.
Micro-apertures in Micro Via PCBs require higher precision drilling and processing techniques. Smaller apertures mean the manufacturing process requires more time and precision equipment, thus increasing costs.
To achieve high performance and reliability, Micro Via PCBs often require high-performance substrate materials such as polyimide (PI) or polytetrafluoroethylene (PTFE). These materials are more expensive than traditional FR-4 materials, which directly affects the cost.
Manufacturing Micro Via PCBs requires more complex processes such as laser drilling and chemical etching. These advanced processes require more equipment and technology and will also increase manufacturing costs.
The production of Micro Via PCBs is usually low-volume or customized, and the smaller scale results in uneven distribution of fixed costs compared with traditional PCBs, thereby increasing unit costs.
The market demand for Micro Via PCB is relatively small, and there are relatively few professional manufacturers, which will also lead to rising costs. In comparison, the traditional PCB market is larger and more competitive, so costs are usually lower.
Overall, the cost of manufacturing Micro Via PCB is affected by multiple factors, including design complexity, material selection, process technology, etc. Although the cost of Micro Via PCB is higher, its application advantages in high-density wiring and small devices make it a high-performance solution worth investing in.
What materials are used in Micro Via PCB?
In the manufacturing process of Micro Via PCB, it is crucial to select appropriate materials. These materials need to have excellent electrical properties, chemical stability and mechanical strength to meet the requirements of high-density wiring and micro-aperture drilling. The following are the main materials commonly used in Micro Via PCB:
FR-4: FR-4 is a fiberglass-reinforced epoxy resin-based material that is one of the most common materials used in PCB manufacturing. It has excellent insulation properties, mechanical strength and heat resistance, and is suitable for general Micro Via PCB applications.
Polyimide (PI): Polyimide is a high-performance engineering plastic with excellent temperature resistance, chemical resistance and mechanical strength. Due to its low dielectric constant and low dielectric loss, PI excels in high frequency and microwave applications and is therefore widely used in Micro Via PCBs where higher performance is required.
Polytetrafluoroethylene (PTFE): PTFE is a polymer with excellent chemical resistance, low coefficient of friction and good dielectric properties. In high frequency and microwave applications, PTFE is widely used as the substrate material of Micro Via PCB to achieve lower signal loss and higher performance.
Copper foil: As the conductive layer of Micro Via PCB, copper foil usually uses high-purity electrolytic copper foil. It has excellent conductivity and processability to provide reliable electrical connections in micro-apertures and high-density wiring.
Filling materials: Microvias in Micro Via PCBs often require filling materials to enhance mechanical support and reduce signal fluctuations. The filling material is usually epoxy resin or polyimide resin, and different filling methods and materials can be selected according to needs.
Metallization layer: The metallization layer of Micro Via PCB is used to form circuit connections, usually using metals such as gold, silver or tin plating. These metallization layers need to have good electrical conductivity and solderability to ensure reliable electrical connections.
When selecting Micro Via PCB materials, comprehensive considerations need to be based on specific application needs and performance requirements to ensure that the final product has excellent performance and reliability.
Who is making Micro Via PCBs?
The manufacturing of Micro Via PCB requires highly professional technology and equipment, and only experienced manufacturers with advanced equipment can do it. In this field, choosing a reliable manufacturer is crucial because their workmanship and quality control directly affect the performance and reliability of the final product.
For many companies, choosing to manufacture Micro Via PCBs within their own production facilities may be the best option. This vertically integrated manufacturing model ensures direct control over the production process, allowing for better management of quality and production schedules. Therefore, some large electronic equipment manufacturers or PCB design companies often produce Micro Via PCBs in their own factories.
First, having its own manufacturing facilities means the company can closely monitor every aspect of the production process, from material procurement to final finished product inspection, to ensure products meet high standards of quality. Second, the company’s in-house manufacturing team usually has extensive experience and expertise and can flexibly respond to various design and production challenges, thereby improving product performance and reliability.
In addition, in-house manufacturing can also bring greater flexibility and customized services. Manufacturers can customize design and production according to customers’ specific needs to meet the needs of different industries and application fields. This kind of customized service can help customers achieve faster time to market and improve competitiveness.
While choosing to manufacture in-house, the company also needs to continuously invest in technology research and development and equipment updates to maintain its competitive advantage in the field of Micro Via PCB manufacturing. This includes introducing advanced manufacturing equipment and production processes, cultivating a professional technical team, and continuously improving the quality management system to ensure product stability and reliability.
To sum up, choosing to manufacture Micro Via PCB in our company can provide customers with higher quality, more flexible and customized products and services, and at the same time, it can also bring the power of sustainable development and innovation to the company. With the continuous development and application expansion of Micro Via PCB technology, the company will continue to be committed to providing the highest quality manufacturing solutions to meet the growing needs and challenges of customers.
What are the qualities of great customer service?
When choosing to work with a PCB manufacturer, excellent customer service is crucial. Here are the key attributes that determine whether a PCB manufacturer has excellent customer service:
Transparency in communication: Great customer service starts with good communication. Manufacturers should be able to communicate with customers promptly and clearly, answer their questions, and provide required information. Transparency in communication means customers are informed about every stage of the manufacturing process, giving them greater control over project progress.
Quick response: Customers expect timely responses and solutions when they encounter problems or have questions. Quality manufacturers respond to customer needs as quickly as possible, ensuring they receive timely support and assistance.
Professional Advice: Customers may not understand the technical details of PCB manufacturing, so great customer service includes providing professional advice and guidance. Manufacturers should be able to provide customers with professional advice on design, material selection, process flow, etc. to help customers make better decisions.
Problem Solving Skills: During the manufacturing process, various issues and challenges may arise. Excellent customer service means the manufacturer is able to resolve these issues quickly and efficiently, ensuring the project runs smoothly. This includes timely adjustments to production plans, resolving quality issues, and handling emergencies.
Customized service: Customers’ needs vary, so good customer service should provide customized solutions. Manufacturers should be able to flexibly adjust production processes and provide personalized services based on customer needs and requirements.
Frequently Asked Questions (FAQs)
Can Micro Via PCBs be used for high-frequency applications?
Yes, Micro Via PCBs can be designed and manufactured to meet the requirements of high-frequency applications. Their ability to support high-density routing and controlled impedance makes them suitable for applications such as telecommunications, RF/microwave systems, and high-speed digital circuits.
Can Micro Via PCBs be manufactured with environmentally friendly materials?
Yes, manufacturers offer options for producing Micro Via PCBs using environmentally friendly materials and processes. This includes using lead-free solder, RoHS-compliant substrates, and implementing green manufacturing practices to minimize environmental impact.
Are Micro Via PCBs more expensive than traditional PCBs?
Due to their specialized manufacturing processes and materials, Micro Via PCBs may be slightly more expensive than traditional PCBs. However, the benefits of higher routing densities, miniaturization, and improved performance often justify the investment, especially for applications demanding compact form factors and advanced functionality.
How long does it take to manufacture Micro Via PCBs?
The manufacturing time for Micro Via PCBs varies depending on factors such as design complexity, production volume, and the capabilities of the manufacturing facility. Generally, the turnaround time can range from a few days to several weeks. For urgent orders or projects with tight deadlines, expedited manufacturing options may be available at additional cost.
Can Micro Via PCBs be used for flexible and rigid-flex designs?
Yes, Micro Via technology is compatible with both flexible and rigid-flex PCB constructions. Flexible PCBs incorporate flexible substrates like polyimide (PI) or polyester (PET), while rigid-flex PCBs combine rigid and flexible layers to accommodate complex form factors and dynamic applications. Micro Via technology enables the creation of fine-pitch vias and intricate circuitry in these flexible and hybrid designs, offering versatility and reliability in demanding environments.