Micro PCB Substrate Manufacturer.A Micro PCB Substrate Manufacturer specializes in crafting intricate circuitry foundations on a miniature scale. Employing cutting-edge technologies and precision engineering, they produce substrates tailored to the demands of modern electronics. These substrates serve as the backbone for microelectronic devices, ensuring optimal performance in compact designs. With a focus on quality and innovation, this manufacturer caters to industries requiring miniaturized components, from consumer electronics to medical devices and beyond. Their expertise lies in translating intricate designs into tangible substrates, enabling the seamless integration of technology into our increasingly interconnected world.
In the rapid development of modern electronic technology, micro PCB (printed circuit board) substrates play a vital role. As a core component of many electronic devices and systems, micro PCB substrates not only improve the performance of the devices, but also promote the miniaturization and efficiency of electronic products. This article will discuss in detail the design, materials, manufacturing process, application areas and advantages of micro PCB substrates to help you better understand the application and development trends of this key technology in today’s electronic products. Whether it is consumer electronics, medical equipment, or industrial automation, micro PCB substrates have shown irreplaceable importance.
What is Micro PCB Substrate?
A micro PCB substrate is a flat plate made of non-conductive material with conductive paths (i.e. wires) etched or printed on it. These wires provide the electrical connections between electronic components, allowing the entire circuit system to function properly. Compared with traditional PCB, micro PCB substrate pays more attention to size reduction and performance optimization, and is suitable for the high density and high integration requirements of modern electronic equipment.
Micro PCB substrates are usually made of high-performance non-conductive materials, such as fiberglass reinforced epoxy (FR4), polyimide and ceramics. These materials have excellent electrical insulation and thermal stability and can withstand high temperatures and mechanical stress. In addition, micro PCB substrates may also contain multi-layer structures to increase the density and complexity of circuits to meet the needs of high-performance electronic devices.
When designing a micro PCB substrate, component placement, signal integrity, thermal management and manufacturability need to be considered. The component layout should be compact and reasonable to maximize the use of limited space while ensuring the reliability of signal transmission. High-density interconnect (HDI) technology and micro via (via) technology are often used in the design of micro PCB substrates to increase the number of wires and reduce electrical interference.
The manufacturing process of micro PCB substrates includes steps such as material preparation, image transfer, etching, drilling, electroplating, pad application and surface treatment. Each step requires high-precision workmanship to ensure the quality and reliability of the final product. Modern manufacturing techniques, such as laser drilling and direct imaging (DI), make the production of micro PCB substrates more efficient and precise.
Micro PCB substrates are widely used in various modern electronic devices, such as smartphones, tablets, wearable devices, medical equipment, automotive electronics, and high-end computers. With the trend of miniaturization and high performance of electronic equipment, the importance of micro PCB substrates has become increasingly prominent.
Compared with traditional PCB, micro PCB substrate has significant advantages. First, its compact size makes electronic devices more lightweight and portable. Secondly, the optimized design and manufacturing process improve the reliability and durability of the circuit. Thirdly, the high density and high integration of micro PCB substrates can meet the needs of complex circuits and improve the performance of the equipment. In addition, standardized production processes and automated assembly technology reduce manufacturing costs and assembly errors, and improve production efficiency and product consistency.
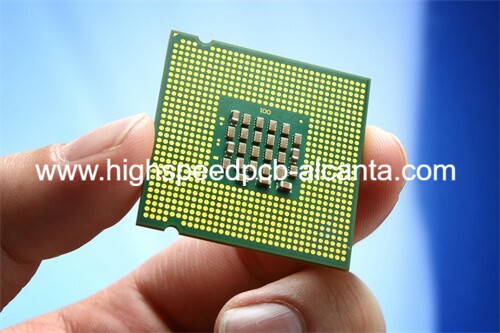
Micro PCB Substrate Manufacturer
With the continuous advancement of science and technology, the technology of micro PCB substrates is also constantly developing. The application of new materials, new processes and new design methods will further improve the performance and reliability of micro PCB substrates. For example, the emergence of flexible PCB and rigid-flexible PCB provides new possibilities for micro PCB substrates in more application fields.
Micro PCB Substrate design Reference Guide.
The design of micro PCB substrate is an important link in modern electronic engineering, which directly affects the performance, reliability and cost of the final product. This guide will introduce the key points and best practices of micro PCB substrate design to help engineers better understand and apply micro PCB substrate design.
Size and layout
The size and layout of the micro PCB substrate are critical to overall circuit performance. Reasonable size design can minimize the space occupied by the circuit board while ensuring sufficient component layout space and wire path arrangement. Engineers need to consider the actual installation environment and usage requirements of the circuit board and reasonably determine the size and layout.
Laminated structure
The stack-up structure of the micro PCB substrate is critical for signal integrity and power management. Through reasonable stacking design, signal crosstalk can be reduced, signal quality improved, and power consumption and heat dissipation effectively managed. Engineers need to select an appropriate stack-up structure based on circuit complexity and performance requirements to ensure the stability and reliability of the circuit board.
Signal integrity
The design of micro PCB substrate needs to fully consider signal integrity, including signal transmission speed, waveform quality and anti-interference ability. Reasonable signal wiring and circuit board stacking design can reduce signal distortion and crosstalk, and improve signal stability and reliability. Engineers need to verify the signal integrity of the circuit through simulation analysis and actual testing to ensure that the design meets the requirements.
Thermal management
Micro PCB substrates often face higher heat output in high-performance and high-density electronic devices. Therefore, effective thermal management is crucial to ensure the stable operation of electronic devices. Engineers need to consider appropriate thermal design and material selection to ensure that the temperature of electronic components is within safe limits.
Manufacturing feasibility
Micro PCB substrate design should take into account the feasibility and cost-effectiveness of the manufacturing process. Proper selection of materials, processes, and manufacturers ensures that the design can be successfully put into mass production and meet expected quality and performance requirements.
Through reasonable micro PCB substrate design, engineers can achieve high performance, miniaturization and high reliability of electronic products, and promote the development and application of modern electronic technology. This guide provides key points and best practices for micro PCB substrate design to help engineers better apply micro PCB substrate technology and create better electronic products.
What material is used in Micro PCB Substrate?
As an indispensable part of modern electronics, the performance and reliability of micro PCB substrates often depend on the materials used. In different application scenarios, choosing the right material is crucial to ensure the stability and functionality of the micro PCB substrate. The following are some commonly used micro PCB substrate materials and their characteristics:
Glass fiber reinforced epoxy resin (FR4)
FR4 is one of the most common PCB substrate materials, which has good mechanical strength, heat resistance and electrical insulation. It consists of fiberglass cloth and epoxy resin and is suitable for most general applications such as consumer electronics and communications equipment.
Polyimide
Polyimide is a high-performance engineering plastic with excellent high temperature resistance, chemical stability and mechanical strength. Micro PCB substrates using polyimide materials can meet the requirements of electronic equipment in high-temperature environments and harsh working conditions, such as aerospace and automotive electronics.
Ceramics
Ceramic substrates have excellent thermal conductivity and insulation and are suitable for high-frequency and high-power circuit applications. They are commonly used in fields such as radio frequency (RF) modules, power amplifiers, and microwave devices because their stability and performance advantages ensure stable operation of circuits at high frequencies.
Metal core substrate
The metal core substrate is based on aluminum or copper and has good heat dissipation performance and mechanical strength. This type of substrate is usually used in circuits that require high power density and heat dissipation, such as LED lighting, power modules, and electric vehicle controllers.
These micro PCB substrate materials each have their own characteristics and can be selected according to specific application requirements. During the design process, the physical properties, thermal properties, cost and feasibility of the manufacturing process of the material need to be taken into consideration to ensure that the final product has good performance and reliability. With the continuous advancement and innovation of technology, the selection of micro PCB substrate materials is also constantly expanding, providing more possibilities for various application scenarios.
What size are Micro PCB Substrate?
Micro PCB substrate sizes vary depending on the specific application, demonstrating adaptability and flexibility. In micro electronic devices such as smartphones and wearable devices, micro PCB substrates often exhibit extremely small sizes. Since these devices require highly integrated circuits and components, the size of the micro PCB substrate must be small enough to fit into the limited space and ensure the lightness and portability of the device. Therefore, these micro PCB substrates are often smaller than a fingernail, but can still achieve complex circuit connections and functional implementations.
At the same time, in fields such as industrial equipment and communication infrastructure, micro PCB substrates also play an important role, but their sizes are usually larger. These application scenarios require micro PCB substrates with higher power handling capabilities and more complex circuit designs. Therefore, micro PCB substrates in these areas often require larger sizes to accommodate more electronic components and connection lines, and to ensure the stability and reliability of the circuit.
Overall, the size of the micro PCB substrate can be customized according to the needs of the specific application. Whether in micro electronic equipment or industrial equipment, micro PCB substrates can be flexibly designed according to space and performance requirements to meet circuit connections and function implementation in different scenarios. This size flexibility not only demonstrates the engineering technology level of the micro PCB substrate, but also reflects its important position and application prospects in the field of modern electronics.
The Manufacturer Process of Micro PCB Substrate.
The manufacturing process of micro PCB substrates is a precise and complex process designed to ensure high quality and high reliability of the final product. The typical steps for manufacturing micro PCB substrates are detailed below:
Substrate material preparation
The first step in manufacturing a micro PCB substrate is to prepare the substrate material. Commonly used materials include fiberglass reinforced epoxy (FR4) or other high-performance materials. Substrates are typically supplied in large sheets that need to be cut into individual substrates of appropriate size based on design requirements.
Layer alignment
Micro PCB substrates are usually multi-layer structures, with each layer containing a conductive layer or an insulating layer. During the manufacturing process, layers need to be precisely aligned to ensure proper connections between wires and components. This is usually accomplished with optical or mechanical alignment devices.
Etching or printing of conductive paths
Once the layer alignment is complete, the next step is to fabricate the conductive paths. This can be achieved by chemical etching or printing. For chemical etching, a layer of photosensitive adhesive is first coated on the conductive layer, and then exposed and etched to form wires. Printing, on the other hand, creates conductive lines by printing conductive ink.
Drilling component holes
After the conductive paths are formed, holes need to be drilled in place to accommodate the electronic components. These holes are typically drilled with a CNC drill machine to ensure accuracy of hole diameter and location.
Pad application
After drilling is complete, the next step is to apply the pads in place. The pad is a layer of metal coated on the surface of the substrate to facilitate soldering of electronic components. Pads can be applied to the substrate thermally or chemically.
Assembly of components
Once the pad application is complete, the electronic components can be mounted to the substrate. This is usually done through automated surface assembly (SMT) or manual plug-in assembly (PTH). During the SMT process, components are precisely placed on pads and connected to wires by melting the pads with heat. PTH inserts the component pins into pre-drilled holes and fixes them by soldering.
Final test
The final stage of the manufacturing process is testing of the micro PCB substrate. This includes testing wire continuity, component functionality, and overall circuit performance. Through rigorous testing, the quality and reliability of micro PCB substrates are ensured.
Through the above steps, the process of manufacturing the micro PCB substrate is completed. This process requires a high degree of precision and expertise to ensure that the final product meets design requirements and has excellent performance and reliability.
The Application area of Micro PCB Substrate.
Micro PCB substrate is an important technological innovation in today’s electronics industry. Its miniaturization and high performance make it widely used in various industries.
The consumer electronics field is one of the most widely used fields for micro PCB substrates. From smartphones and tablets to smart watches and headphones, almost all modern consumer electronics products are inseparable from the support of micro PCB substrates. The small size and high degree of integration of micro PCB substrates make consumer electronics not only thinner and more portable, but also capable of achieving more functions and higher performance.
In the automotive industry, micro PCB substrates also play a vital role. Modern cars have become mobile smart terminals, covering many functions such as engine control, in-car entertainment, and driving assistance systems. The high performance and stability of micro PCB substrates ensure the reliable operation of automotive electronic systems, and also provide the possibility for continuous innovation of automotive electronic products.
The aerospace field has more stringent requirements for electronic equipment, and micro PCB substrates are ideal for meeting this demand. Electronic systems in aerospace devices such as aircraft, satellites, and missiles need to be lightweight, highly reliable, and resistant to high temperatures, and micro PCB substrates are an outstanding solution in these aspects.
In the field of medical equipment, micro PCB substrates are also widely used. From portable medical diagnostic equipment to high-end medical imaging equipment, micro PCB substrates play an important role. Its high precision, stability and reliability provide reliable support for precise diagnosis and treatment of medical equipment.
The communication field is another important application field of micro PCB substrates. Micro PCB substrates are widely used in various communication equipment such as wireless communication equipment, base stations, and optical fiber communication equipment, providing necessary support for information transmission and data processing.
Industrial automation is one of the key areas of modern industrial production, and the application of micro PCB substrates has also been widely reflected here. Sensors, controllers, data acquisition equipment, etc. in industrial automation equipment are all inseparable from the support of micro PCB substrates. Its stability and high performance ensure the efficient operation of industrial production.
To sum up, micro PCB substrates not only perform well in the field of consumer electronics, but also play an important role in various industries such as automobiles, aerospace, medical equipment, communications, and industrial automation, making important contributions to the development and progress of modern technology.
What are the advantages of Micro PCB Substrate?
The advantages of micro PCB substrates are becoming more and more prominent in the field of modern electronics. Compared with traditional wiring methods, they present a series of eye-catching characteristics:
First, micro PCB substrates are known for their compact size. Since electronic components are arranged directly on the PCB surface without the need for additional connections, micro PCB substrates can greatly save space and make electronic devices more compact and portable. This feature is particularly suitable for modern portable devices such as smartphones, tablets and wearables, providing greater freedom in their design.
Secondly, the micro PCB substrate has high reliability. Through optimized design and strict manufacturing processes, micro PCB substrates can ensure the stability and durability of the circuit. A stable and reliable circuit is the foundation of any electronic equipment, and the micro PCB substrate excels at this point, ensuring the long-term stable operation of the equipment.
Third, micro PCB substrates are easy to mass produce. The standardized manufacturing process allows micro PCB substrates to achieve high efficiency and low cost in mass production. This allows manufacturers to respond to market demand faster while reducing production costs and bringing more competitive products to consumers.
In addition, micro PCB substrates can reduce assembly errors. Automated production processes reduce the possibility of human error and improve product consistency and quality stability. This is particularly important for electronic equipment manufacturers that require mass production, and can greatly improve production efficiency and product quality.
Another advantage of micro PCB substrates is improved signal integrity. Reasonable wire layout and lamination structure can reduce interference and loss in signal transmission, and improve circuit performance and stability. This is particularly important for applications that require high-speed data transmission or frequent signal processing, such as communications equipment and computer systems.
Finally, micro PCB substrates can also enhance heat dissipation performance. Special materials and designs help dissipate heat from electronic components, effectively extending the service life of the device. In high-performance and high-power-density electronic equipment, good heat dissipation design is a key factor to ensure stable operation of the equipment, and the excellent heat dissipation performance of the micro PCB substrate provides strong support for this.
In summary, micro PCB substrates have become an indispensable component in the design and manufacturing of modern electronic equipment due to their compact size, high reliability, ease of mass production, reduced assembly errors, improved signal integrity, and enhanced heat dissipation performance. part. With the continuous advancement of technology and the continuous expansion of application fields, micro PCB substrates will continue to play an important role and bring more innovation and development to the electronics industry.
FAQ
What are the materials of micro PCB substrate?
Commonly used materials for micro PCB substrates include fiberglass reinforced epoxy resin (FR4), polyimide (PI), ceramics and metal core substrates, etc., which have good electrical properties and mechanical strength.
What is the size range of micro PCB substrates?
Micro PCB substrates come in a wide range of sizes, from a few millimeters to tens of centimeters, and can be customized to meet specific application needs.
What is the manufacturing process of micro PCB substrate?
The process of manufacturing micro PCB substrates includes steps such as substrate preparation, layer alignment, circuit pattern etching, drilling, pad covering, component mounting and testing. Each step requires strict control to ensure product quality.
In what fields are micro PCB substrates mainly used?
Micro PCB substrates are widely used in consumer electronics, communications, medical, automotive, aerospace and other fields, such as smartphones, drones, medical diagnostic equipment, etc.
What is the difference between micro PCB substrate and traditional PCB?
Compared with traditional PCBs, micro PCB substrates pay more attention to size reduction and high integration, and can meet the needs of modern electronic equipment for miniaturization and high performance.