Micro cavity substrates manufacturing, Open multi-cavity on the Substrates PCBs. Or open multi-step cavity on the substrates. We use advanced control processes to produce Micro cavity substrates from 4 layer to 30 layers.
Microcavity substrates (MCS) are at the heart of leading-edge electronic devices, achieving the perfect combination of compact design and superior performance. In this comprehensive guide, we’ll dive into the complexities of microcavity substrate manufacturing, exploring the processes, materials, and considerations that drive this critical aspect of PCB production.
What is a microcavity substrate?
Micro Cavity Substrates (MCS) are special printed circuit boards designed to accurately accommodate microscopic electronic components. Compared with traditional printed circuit boards, microcavity substrates have higher density and precision, providing the possibility for compact design of modern electronic devices. The core feature of a microcavity substrate is its internal precision structure, including tiny grooves (i.e., microcavities) that are used to accommodate components such as microchips, sensors, and transistors.
In electronic devices, microcavity substrates play a vital role. First, microcavity substrates allow the integration of a large number of electronic components in a limited space, making the device more compact and lightweight. This is critical for portable devices and embedded systems. Secondly, the design of the microcavity substrate makes the connection between electronic components more stable and reliable, improving the stability and performance of the circuit. In addition, the microcavity substrate also has excellent thermal conductivity properties, which helps to effectively manage the heat generated by electronic components and ensure stable operation of the equipment for a long time.
Microcavity substrates play an important role in many application fields. In the field of communications, microcavity substrates are widely used in wireless communication equipment, base stations and radio frequency modules to ensure the stability and reliability of signal transmission. In the field of medical electronics, microcavity substrates are used in high-precision applications such as medical diagnostic equipment and implantable medical devices to support innovation in the medical industry. In the field of automotive electronics, microcavity substrates can be used in vehicle control units, vehicle entertainment systems and other aspects to improve the intelligence and safety performance of vehicles.
In general, the emergence of microcavity substrates has brought electronic devices to new heights in terms of size, performance, and reliability. By fully understanding the design, manufacturing and application of microcavity substrates, the electronics industry can continue to promote technological progress, meet growing market demands, and make greater contributions to the development of human society.
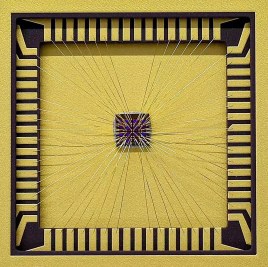
Micro cavity substrates
What is the manufacturing process of microcavity substrates?
The manufacturing process of microcavity substrates is a precise and complex project involving multiple key steps, each of which is critical to ensure the quality and performance of the final product. Next, we will delve into the manufacturing process of microcavity substrates and how to use advanced technology to ensure micron-level precision.
First, the process of fabricating microcavity substrates begins with the preparation of raw materials. This involves selecting the appropriate substrate material, such as ceramic, FR-4 or polyimide. The choice of materials directly affects the performance and scope of application of the final product. At this stage, quality control is particularly critical to ensure that raw materials meet specifications, thereby laying a solid foundation for subsequent processes.
Next, is the formation of microcavities. The accurate fabrication of microcavities is crucial to ensure the performance of microcavity substrates. Using advanced technologies such as laser drilling, chemical etching and micron-scale milling, engineers are able to precisely create micron-scale cavity structures. These technologies not only ensure that the size and shape of the microcavity are accurate, but also enable high-efficiency production and improve production efficiency.
After the microcavities are formed, the next steps are surface treatment and coating. Through chemical treatment and coating technology, the surface of the microcavity can be smoothed and protected to ensure its stability and reliability during subsequent assembly and use. These surface treatment processes are not only for aesthetics, but more importantly, to improve the durability and performance of the microcavity substrate.
Subsequently, there is the production of circuit graphics. Using photolithography and thin-film deposition techniques, engineers can precisely print circuit patterns onto microcavity substrates. This requires highly precise operations and strict quality control to ensure the accuracy and stability of circuit graphics.
Finally, there is quality inspection and testing. After the microcavity substrate is manufactured, strict quality inspection and testing are required to ensure that it meets the design requirements and performance indicators. This includes visual inspection, dimensional measurement, electrical performance testing and many other aspects. Only after passing all inspections and tests can the microcavity substrate be considered a qualified product and enter the subsequent production and application stages.
In general, the manufacturing process of microcavity substrates is a highly complex and technology-intensive project that requires multi-faceted expertise and rich experience. By utilizing advanced manufacturing technology and strict quality control, it is possible to ensure that microcavity substrates have micron-level precision and stability, thereby meeting the performance and reliability requirements of modern electronic equipment.
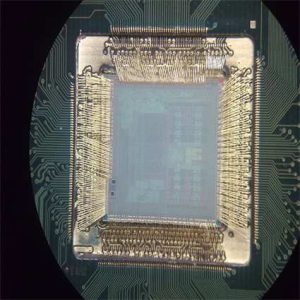
Micro cavity substrates
How is the production of microcavity substrates performed?
The production of microcavity substrates is a precise and complex process involving a variety of technologies and engineering to ensure consistency and reliability of production. The following will introduce the key steps and related technologies for microcavity substrate production.
First, the production of microcavity substrates begins with the preparation of materials. Selecting the appropriate substrate material is critical to the performance of the final product. Common substrate materials include ceramics, FR-4, etc. Each material has different characteristics and application range. Choose appropriate materials based on design requirements and application scenarios.
Next is process selection and optimization. Microcavity substrates are usually manufactured using a variety of processes, including laser drilling, chemical etching, micro-milling, etc. The choice of these processes depends on design requirements, material properties and production efficiency. By optimizing process parameters and precise control, the accuracy and consistency of each step is ensured.
In the formation process of microcavities, precision machining is crucial. The dimensions of microcavities are typically in the micron range, so high-precision equipment and tools are required to ensure accuracy. Laser technology plays an important role in the processing of microcavities, enabling precise apertures and shapes.
This is followed by surface treatment and coating. Surface treatment can improve the corrosion resistance, electrical conductivity and welding performance of the microcavity substrate. The selection and application of coatings is critical to the quality and performance of the final product, taking into account material compatibility and process controllability.
Finally comes quality control and inspection. Throughout the production process, strict quality control measures are essential. By implementing a traceable quality management system, we monitor the quality indicators of each production link to ensure that products meet design requirements and industry standards.
In summary, the production of microcavity substrates involves multiple critical steps and complex processes, requiring a high degree of technical and engineering skills. Through precise process control and strict quality management, the consistency and reliability of microcavity substrate production can be ensured to meet the needs of different application fields.
What are the cost considerations for microcavity substrates?
The cost of the microcavity substrate is one of the key factors to be considered in the manufacturing process. It directly affects the competitiveness and market positioning of the product. Understanding the factors that influence microcavity substrate cost and how to optimize cost in terms of materials and design is one of the challenges that manufacturers must face.
First, the cost of microcavity substrates is affected by many factors. Among them, material selection is one of the most important factors. Different substrate materials have different physical properties and manufacturing difficulties, so their costs will also vary. High-performance specialty materials may result in higher costs, while general-purpose materials are relatively cheaper.
Secondly, design complexity and manufacturing process are also important factors affecting the cost of microcavity substrates. Complex designs and special manufacturing processes often increase production costs because they require more time and resources to complete. For example, the design of microcavities may require more advanced processes and more sophisticated equipment to achieve, thereby increasing the difficulty and cost of manufacturing.
Considering the cost of microcavity substrates, manufacturers can adopt a variety of strategies to optimize costs. First, they can choose the right materials to balance performance and cost based on the product’s requirements and budget. Secondly, optimized design is the key to reducing costs. By simplifying the design, reducing the number of layers and optimizing the layout, manufacturing costs can be reduced and production efficiency improved. In addition, the use of standardized processes and automated production lines can also help reduce production costs and improve production efficiency.
In summary, the cost consideration of microcavity substrates involves multiple factors, including material selection, design complexity, and manufacturing processes. Through reasonable material selection and design optimization, manufacturers can reduce production costs and improve product competitiveness and market share.
What materials are used for microcavity substrates?
The material selection of the microcavity substrate is crucial, as it directly affects the performance, stability and application range of the microcavity substrate. Common microcavity substrate materials include ceramics, FR-4, and flexible materials such as polyimide. Each material has unique characteristics and is suitable for different application scenarios.
First, ceramic is a common microcavity substrate material with excellent thermal conductivity and high temperature resistance. Ceramic substrates can effectively dissipate heat and therefore perform well in high power density and high temperature environments. In addition, ceramic substrates have good mechanical strength and chemical stability, making them suitable for harsh industrial and military applications.
Secondly, FR-4 is a commonly used substrate material with good mechanical and electrical properties. FR-4 substrate is cheap and easy to process, and is widely used in consumer electronics and general electronic equipment. However, the thermal conductivity of FR-4 substrate is relatively poor and is not suitable for applications in high-power or high-temperature environments.
In addition, flexible materials such as polyimide (PI) substrates have excellent flexibility and bending properties and are suitable for curved displays, flexible electronic products and other fields. PI substrate has excellent high temperature resistance and chemical stability, but its cost is higher compared to ceramics and FR-4.
In addition to the common materials mentioned above, there are other special materials, such as metal substrates, aluminum substrates, etc., which have specific characteristics and are suitable for specific application scenarios. Metal substrates have excellent thermal conductivity and are suitable for applications that require efficient heat dissipation, while aluminum substrates have the advantages of being lightweight and low-cost, and are suitable for applications that are sensitive to weight and cost requirements.
In general, selecting an appropriate microcavity substrate material requires comprehensive consideration of application needs, performance requirements, cost constraints and other factors. Different materials have different characteristics and application ranges. Reasonable selection of materials can improve product performance and competitiveness.
Who are the major microcavity substrate manufacturers?
In the field of microcavity substrate manufacturing, there are many companies that stand out for their technical strength and product quality. The company is proud to be one of the leading manufacturers in this field and is committed to providing customers with high-quality microcavity substrate solutions.
As one of the major microcavity substrate manufacturers, the company has extensive experience and expertise to meet various customer needs. We use advanced manufacturing processes and technologies to ensure that the microcavity substrates we produce have excellent performance and reliability.
The company’s manufacturing process strictly follows international standards and quality management systems to ensure product quality reaches the highest level. We have advanced equipment and facilities, staffed with highly qualified staff, to meet our customers’ needs for high-quality microcavity substrates.
In addition to offering standardized products, the company also provides customized solutions to meet customer-specific needs and requirements. We work closely with our customers to understand their needs and provide the best solutions to ensure their satisfaction.
As a major microcavity substrate manufacturer, we are committed to continuous innovation and improvement to meet changing market demands. We will continue to work on technology research and development and product improvement to ensure that our products remain at the forefront and provide customers with excellent service and support.
In the field of microcavity substrate manufacturing, the company will continue to play a leading role, provide customers with high-quality products and solutions, and achieve common development and success.
What are the characteristics of great customer service?
High-quality customer service is crucial in microcavity substrate manufacturing. Its characteristics cover many aspects and directly affect customer satisfaction and the stability of cooperative relationships. Here are these features and how they apply to microcavity substrate manufacturing:
Technical Professionalism: Excellent customer service begins with a deep understanding of technology and the application of expertise. For microcavity substrate manufacturers, technical expertise manifests itself in a comprehensive understanding of microcavity substrate design, material selection, and manufacturing processes. The customer service team must be able to provide accurate answers to technical questions and provide customers with professional advice to meet their specific needs.
Rapid response: In microcavity substrate manufacturing, time is often a critical factor. Excellent customer service requires maintaining a high degree of responsiveness, promptly responding to customer inquiries and needs, and ensuring that production plans and delivery deadlines are adhered to. Timely communication and feedback can enhance customers’ trust in manufacturers and strengthen the cooperative relationship between the two parties.
Customization options: The customer service team should be able to understand the specific needs of the customers and provide them with customized solutions. In microcavity substrate manufacturing, customers may require microcavity substrates with specific dimensions, materials, or special process requirements. Manufacturers enhance customer satisfaction and loyalty by offering customization options to meet customers’ individual needs.
Reliability: Excellent customer service is reflected in strict adherence to product quality and delivery commitments. Microcavity substrate manufacturers must ensure that the quality of their products meets customer expectations and orders are delivered on time. By establishing a sound quality management system and supply chain management, manufacturers can provide reliable products and services and win the trust and respect of customers.
Professional Attitude: In customer service, a professional attitude is crucial. The Customer Service team must communicate with customers, resolve issues, and provide support in a friendly, courteous, and professional manner. In microcavity substrate manufacturing, professional attitude is reflected in accurate understanding of customer needs and timely and effective response, as well as the establishment of good cooperative relationships with customers.
In the microcavity substrate manufacturing industry, excellent customer service is not just an added value, it is a key factor in ensuring business success and long-term development. Through characteristics such as technical expertise, responsiveness, customization options, reliability and professional attitude, manufacturers can establish good cooperative relationships with customers and jointly promote the development and innovation of the industry.
Frequently Asked Questions
What are the key benefits of using micro cavity substrates?
Micro cavity substrates offer several key benefits, including compact design, improved thermal management, and enhanced signal integrity. By housing components within precisely engineered cavities, MCS allows for higher component density, reduced electromagnetic interference, and efficient heat dissipation, making it ideal for space-constrained and high-performance applications.
How do micro cavity substrates differ from traditional PCBs?
Unlike traditional PCBs, micro cavity substrates feature recessed cavities that house electronic components, enabling a more compact and efficient design. Traditional PCBs rely on surface-mounted components, whereas MCS offers the advantage of integrated component placement within the substrate itself, resulting in reduced footprint and improved performance.
What factors should I consider when selecting a micro cavity substrate material?
When selecting a micro cavity substrate material, several factors should be considered, including thermal conductivity, electrical properties, mechanical strength, and compatibility with manufacturing processes. Materials such as ceramics offer high thermal conductivity, while flexible materials like polyimide provide versatility for bendable and foldable applications.
Can micro cavity substrates be used in high-frequency applications?
Yes, micro cavity substrates are well-suited for high-frequency applications due to their excellent signal integrity and minimal signal loss characteristics. By minimizing electromagnetic interference and optimizing signal propagation, MCS enables reliable operation in high-frequency environments, making it ideal for RF and microwave applications.
How can I optimize the design of micro cavity substrates for thermal management?
Optimizing the design of micro cavity substrates for thermal management involves several considerations, including cavity placement, heat sink integration, and selection of thermally conductive materials. By strategically positioning cavities and incorporating heat dissipation mechanisms such as thermal vias and metal layers, designers can effectively manage heat within the substrate, ensuring optimal performance and reliability.