Micro cavity PCB Supplier, Specializing in the production of various types of Cavity PCBs, Embedded Slot PCBs, and Open multi- Cavity on the PCBs/BGA/IC substrates. We offer Cavity PCBs from 4 layer to 30 layers.
Micro Cavity PCB manufacturing is a critical technology that provides precision circuit boards for electronic devices for a variety of high-tech applications. With the continuous development of electronic products and the increasing demand for intelligence, the demand for miniaturized, high-performance Micro Cavity PCB is also increasing. This article will delve into the design, manufacturing, and cost aspects of Micro Cavity PCBs, providing readers with a comprehensive guide to better understanding and applying this important manufacturing technology.
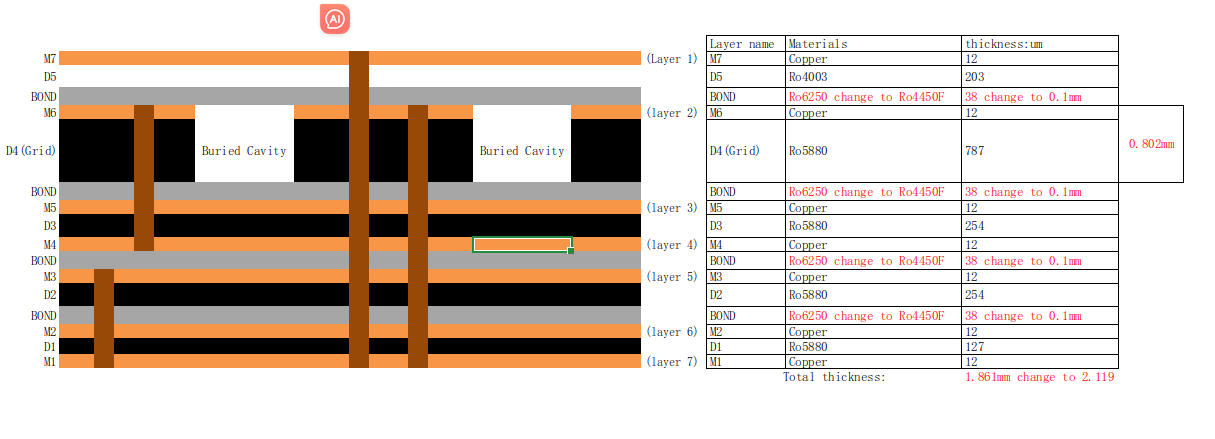
Buried cavity(slot) PCBs
What is Micro Cavity PCB?
Micro Cavity PCB (Micro Cavity Printed Circuit Board) is a specially designed printed circuit board whose main feature is the formation of micro grooves or protruding structures on the surface to accommodate electronic components, chips or other components. These micro-grooves are typically made by etching or other machining processes and can be custom designed to meet specific application needs.
In electronic devices, Micro Cavity PCB plays an important role. They provide an efficient way to arrange various electronic components into a compact space and provide higher integration and performance. By embedding components into the surface microstructure of PCBs, higher circuit density and lower signal delays can be achieved, thereby improving the overall performance and reliability of electronic devices.
Micro Cavity PCB has wide applications in many fields, especially in portable electronic equipment, medical equipment, automotive electronics, aerospace and communication equipment, etc. For example, in portable smartphones, Micro Cavity PCB can help achieve thinner and lighter designs and provide better heat dissipation. In medical devices, Micro Cavity PCBs can help achieve greater integration and more precise control, thereby improving device diagnostics and treatment. In terms of automotive electronics, Micro Cavity PCB can help achieve more complex functions and more reliable performance, improving vehicle safety and comfort. In general, Micro Cavity PCB plays an irreplaceable role in modern electronic equipment and provides important technical support for various application scenarios.
Through the design and manufacturing of Micro Cavity PCB, electronic devices can be enhanced in function, miniaturized in size, and optimized in performance to meet the growing market demand and consumer expectations.
How to design a Micro Cavity PCB?
Designing a Micro Cavity PCB is a complex and critical process that requires a combination of electronic principles, CAD software skills, and an understanding of microstructure. The following are the basic principles and steps for designing Micro Cavity PCB:
Micro Cavity PCB is a special type that creates tiny cavities on or within the PCB, often used to house sensitive electronics, sensors, or other components. The basic principle of designing Micro Cavity PCB is to rationally plan the circuit layout and chamber structure to ensure the performance and stability of the circuit and provide accurate guidance for the manufacturing of the chamber.
Determine needs and specifications: First, clarify the purpose of the design and the required specifications. This includes circuit layout, chamber size and shape, and the type and number of electronic components.
Choose the right CAD software: Choose a CAD software suitable for PCB design, such as Altium Designer, Eagle or KiCad, etc. Ensure that the software supports the design and simulation of microstructures.
Draw a circuit diagram: Use CAD software to draw a circuit diagram, including the location, connections, and routing of electronic components. Consider the location and shape of the chamber in the design, and arrange it appropriately to ensure the stability and performance of the circuit.
Add a chamber structure: Add a chamber structure to the PCB according to design requirements. The 3D module of the CAD software can be used to simulate and design the microchamber, ensuring that it matches the circuit layout and provides enough space to accommodate the target components.
Optimized Layout: Circuit layout and chamber structure are optimized to minimize interference and cross-talk. Ensure adequate spacing between electronic components and chamber to avoid heat build-up and signal interference.
Simulate and test: Simulate and test in CAD software to verify the performance and stability of your design. Conduct circuit simulation and thermal analysis through simulation software to evaluate the working status of the circuit and the heat dissipation effect of the chamber.
Adjustments and modifications: Make adjustments and modifications to the design based on simulation and test results. Circuitry may need to be rearranged or the size and shape of the chamber adjusted to meet design needs and performance requirements.
Generate manufacturing files: Finally, generate the Gerber files and BOM tables required for PCB manufacturing, and communicate with the PCB manufacturer to ensure design accuracy and manufacturability.
Through the above steps, designing Micro Cavity PCB will be more systematic and efficient. Combined with reasonable circuit design and microstructure optimization, Micro Cavity PCBs with higher performance and reliability can be achieved.
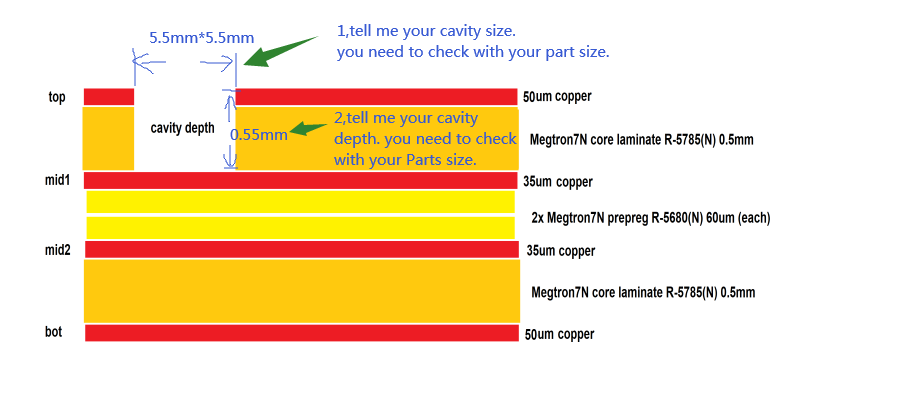
Buried cavity(slot) PCBs
What is the manufacturing process of Micro Cavity PCB?
The manufacturing process for Micro Cavity PCBs is a complex and precise process consisting of multiple critical steps that ensure the quality and performance of the final product. Let’s walk through the process together.
The manufacturing process of Micro Cavity PCB begins with the preparation of materials. The commonly used substrate is fiberglass reinforced resin board (FR-4), the surface of which is coated with a layer of copper foil. First, the original sheets are cut into substrates of appropriate size according to the design requirements for subsequent processing and handling.
Next is the production of the printed circuit layer. In this step, a layer of photosensitive material is coated on the surface of the substrate through chemical processing or mechanical engraving. Then, using the design pattern generated by CAD software, the pattern is transferred to the photosensitive layer through exposure.
After exposure, the photosensitive layer in the unexposed area is removed by chemical etching to expose the copper foil. After etching, the plate needs to be thoroughly cleaned to remove residual photosensitive substances and etchants to ensure that the surface of the plate is clean and free of contamination.
Drilling is an integral step in the manufacturing of Micro Cavity PCBs. According to the design requirements, use a drill press to drill holes in the board to provide channels for the connection and assembly of the circuits. After drilling is completed, electroplating is performed to strengthen the circuit connection, improve conductivity, and protect the circuit from oxidation and corrosion by electroplating a layer of metal on the copper foil.
Finally, the circuit board is assembled and tested. Install various electronic components on the PCB according to design requirements and solder them. The PCB is then functionally tested and performance verified using automated or manual test equipment to ensure it meets design specifications and quality standards.
Overall, the Micro Cavity PCB manufacturing process includes key steps such as material preparation, printed circuit layering, chemical etching and cleaning, drilling and plating, and final assembly and testing. Every step is critical and has a direct impact on the quality and performance of the final product.
What are the specific steps for manufacturing Micro Cavity PCB?
Micro Cavity PCB manufacturing is a complex and precise process that involves multiple critical steps, from material preparation to final assembly and testing, each step is critical. Below we will introduce in detail the specific steps of Micro Cavity PCB manufacturing:
Material Preparation: The first step in making a Micro Cavity PCB is to prepare the required materials. This includes PCB substrates, copper foil, insulation layer materials, heat-resistant adhesives, etc. The selection and quality of materials directly affects the performance and reliability of the final product.
Printing the circuit layer: The next step is to print the circuit layer on the surface of the PCB substrate. This is usually done by covering a layer of copper foil on the substrate and using chemical methods to remove the unwanted copper foil to create the desired circuit pattern.
Micro Cavity manufacturing: After the circuit layer is completed, Micro Cavity manufacturing is performed. This step involves using a laser or CNC machine to cut tiny grooves or holes into the PCB for mounting micro components or making specific circuit connections.
Chemical Etching and Cleaning: Next, the PCB is chemically etched to remove unnecessary copper foil to form circuit connections. Afterwards, a cleaning step removes any remaining chemicals and ensures a clean PCB surface.
Drilling and Plating: Drilling holes in a PCB to mount electronic components and plating to enhance the conductivity of the hole walls. These holes will be used to mount components and connect circuits.
Assembly and soldering: Mounting electronic components onto a PCB, either manually or automatically, and using soldering techniques to hold them in place. This step involves using a variety of equipment and tools to ensure that each component is installed correctly and connected to the circuit.
Testing: The last step is to test the manufactured Micro Cavity PCB. This includes electrical testing, functional testing and reliability testing to ensure the PCB meets design requirements and works properly.
Through the above steps, Micro Cavity PCB has completed the entire process from material preparation to final testing. Each step requires a high degree of technology and precision operations to ensure the quality and performance of the final product reaches the expected level.
How much does Micro Cavity PCB cost?
The cost of Micro Cavity PCBs is an important factor to consider during the manufacturing process. Understanding these cost factors and being able to accurately estimate costs is one of the keys to ensuring a successful project.
First, one of the factors that affects the cost of Micro Cavity PCB is the type and quality of materials chosen. Different materials have different prices, and differences in quality will also have an impact on costs. High-performance materials tend to be more expensive but may offer better performance and reliability.
Secondly, PCB design complexity also directly affects cost. If the PCB needs to contain complex circuits, multi-layer designs, or special requirements such as micro-apertures, manufacturing costs will increase accordingly. In addition, special process requirements or customized requirements may also increase costs.
Manufacturing scale is another important factor. Large-scale production often reduces unit costs because fixed costs can be spread over more products. In contrast, the costs of small-scale production may be higher because fixed costs are allocated at a lower rate.
Finally, supply chain management also has an impact on costs. Proper supply chain management can optimize material procurement, production processes and logistics management, thereby reducing overall costs. Improper supply chain management may lead to material waste, production delays or increased transportation costs, thereby increasing costs.
To accurately estimate the cost of a Micro Cavity PCB, you first need to consider the various factors mentioned above. Secondly, you need to communicate with suppliers and manufacturers to obtain relevant quotes and estimates. When considering quotes from different suppliers, price, quality, delivery time and after-sales service need to be considered comprehensively.
Additionally, you can take the help of some online cost estimating tools to get a preliminary estimate. These tools typically generate estimated cost ranges based on parameters such as the PCB’s design specifications, material selection, and production quantities. While these tools cannot completely replace actual quotes from suppliers, they can help you quickly understand the ballpark range of costs and make an initial decision.
In summary, understanding the factors that influence Micro Cavity PCB cost and adopting appropriate estimating methods can help you develop a reasonable budget and ensure that the project goes smoothly.
What materials are Micro Cavity PCBs made of?
Micro Cavity PCB is a high-performance circuit board widely used in electronic devices, and its material selection is critical to its performance and reliability. Commonly used Micro Cavity PCB materials include FR-4, FR-4 High Tg, aluminum substrate, ceramic substrate, etc.
FR-4: FR-4 is a glass fiber reinforced epoxy resin substrate with good mechanical and electrical properties and is widely used in PCB manufacturing of general electronic products. Its advantages include low cost, good processability, high temperature resistance, chemical corrosion resistance, etc., making it suitable for most application scenarios.
FR-4 High Tg: FR-4 High Tg is an improved version of FR-4 with a higher glass transition temperature (Tg), usually above 170°C. This makes it have better performance stability and heat resistance in high temperature environments, and is suitable for applications with higher high temperature requirements, such as automotive electronics, aerospace and other fields.
Aluminum substrate: Aluminum substrate is a PCB board based on an aluminum substrate and formed with a thermal conductive layer and circuit layer through chemical corrosion or mechanical processing. It has excellent heat dissipation performance and is suitable for electronic equipment with high heat dissipation requirements, such as LED lamps, power modules, etc.
Ceramic substrate: Ceramic substrate is a PCB made of ceramic materials such as alumina and silicon nitride. It has excellent high-frequency performance, high-temperature resistance and chemical corrosion resistance. It is suitable for radio frequencies in high-frequency communications, radar, microwave and other fields. Circuit design.
Material selection has a direct impact on the performance of Micro Cavity PCBs. For example, FR-4 plates have low cost and good processability, and are suitable for applications with general performance requirements; and for applications that require high-temperature stability and heat dissipation performance, FR-4 High Tg or aluminum substrates can be selected. In addition, ceramic substrates have excellent high-frequency performance and are suitable for high-frequency signal transmission situations.
When selecting Micro Cavity PCB materials, comprehensive considerations need to be made based on specific application scenarios and performance requirements to ensure optimal PCB performance and reliability.
Who makes Micro Cavity PCBs?
The manufacturing process of Micro Cavity PCB requires highly specialized equipment and technology, and choosing the right supplier is a key part of ensuring product quality and performance. In this field, our company has become the leader in the industry with its excellent manufacturing capabilities and rich experience.
Our company has the most advanced manufacturing equipment and technology to meet the various needs of our customers for high-precision Micro Cavity PCBs. From design to production, we are committed to ensuring the highest standards are met every step of the way to ensure the quality and performance of the final product.
To ensure the quality of each Micro Cavity PCB, we have implemented a strict quality control system. From the procurement of raw materials to the shipment of final products, we conduct multiple quality inspections to ensure that the products meet customer requirements and standards.
Our company not only offers standard Micro Cavity PCB products but also provides customized solutions as per the needs of our clients. Whether it is special size requirements or complex technical needs, we are able to provide customers with satisfactory solutions.
As a leader in Micro Cavity PCB manufacturing, our company is always committed to continuous improvement and innovation. We continuously invest in R&D and technological innovation to meet changing market needs and provide customers with better products and services.
In our company, customers always come first. We take customer satisfaction as our highest pursuit, always consider issues from the customer’s perspective, actively listen to customer needs and feedback, and make timely adjustments and improvements to ensure that customers receive the best experience and service.
As a leader in the field of Micro Cavity PCB manufacturing, our company has won widespread praise and trust for its professional manufacturing capabilities, strict quality control and customer-first service concept. We will continue to work hard to provide customers with better products and services, grow together with customers, and create a better future together.
What are the five characteristics of great customer service?
Quality customer service refers to the services provided by a business or organization to meet customer needs and provide a good experience. It goes beyond simple product sales or service delivery and focuses on building long-term customer relationships that meet and exceed customer expectations. Excellent customer service is not only the solution to customer problems, but also the understanding and care of customer needs to ensure the improvement of customer satisfaction and loyalty.
Prompt response: The first element of great customer service is prompt response to customer needs and questions. Whether it’s a phone call, email, or online chat, timely responses can make customers feel valued and enhance customer trust and satisfaction with your business.
Expertise: Excellent customer service requires specialized knowledge and skills. Service personnel should know the details of a product or service and be able to provide customers with accurate, useful information and advice. Professional services can enhance customers’ trust in the company and increase customer satisfaction with products or services.
Customized Solutions: Every customer’s needs are unique, so providing customized solutions is key to excellent customer service. Understanding customers’ needs and preferences and tailoring products or services can improve customer satisfaction and loyalty and promote the establishment of long-term cooperative relationships.
Good Communication: Good communication is the foundation of great customer service. Service personnel should listen to customers’ needs and opinions, express information clearly, and ensure smooth communication between both parties. Good communication can avoid misunderstandings and dissatisfaction and build good customer relationships.
After-sales support: Excellent customer service is not only about service during the sales process, but also includes after-sales support. Handling customer complaints and problems in a timely manner and providing after-sales service and technical support can enhance customer trust and satisfaction in the company, improve customer loyalty, and win reputation and market competitiveness for the company.
Excellent customer service is one of the keys to a successful business. Through key features such as timely response, professional knowledge, customized solutions, good communication and after-sales support, enterprises can win the trust and support of customers, improve customer satisfaction and loyalty, and achieve sustainable development and competitive advantage.
FAQS
What are the main advantages of using Micro Cavity PCBs?
Micro Cavity PCBs offer several advantages, including reduced size and weight of electronic devices, improved thermal management, enhanced signal integrity, and increased design flexibility for complex circuitry.
What factors affect the cost of manufacturing Micro Cavity PCBs?
The cost of manufacturing Micro Cavity PCBs depends on various factors such as board size, complexity of the design, choice of materials, surface finish, and production volume. Larger boards with intricate designs and specialized materials typically incur higher costs.
What materials are commonly used in Micro Cavity PCBs?
Common materials used in Micro Cavity PCBs include FR-4, high-frequency laminates, ceramic substrates, and metal-core laminates. The choice of material depends on the specific application requirements such as thermal conductivity, dielectric properties, and signal integrity.
How does Micro Cavity PCB manufacturing differ from traditional PCB manufacturing?
Micro Cavity PCB manufacturing involves additional steps such as creating cavities or recesses within the board to accommodate components or provide thermal management. These cavities require precise machining or laser processing, which adds complexity to the manufacturing process compared to traditional PCBs.