What is a Metal Core PCB?
A Metal Core PCB Manufacturer specializes in crafting circuit boards with a metal core, enhancing thermal conductivity and durability. These boards are crucial for applications demanding high heat dissipation, like LED lighting, automotive electronics, and power supplies. With advanced manufacturing processes and expertise, they ensure precise etching, drilling, and soldering of components onto the metal substrate. Their products adhere to stringent quality standards, ensuring reliability and performance in demanding environments. From prototyping to mass production, they cater to diverse industries, driving innovation and powering technological advancements worldwide.
Metal Core PCB is a specialized type of printed circuit board whose core uses a metal substrate, usually aluminum or copper, instead of traditional fiberglass. This metal substrate has superior thermal conductivity properties, making metal substrate printed circuit boards ideal for applications that require efficient heat dissipation.
Compared with traditional fiberglass substrates, the biggest feature of metal substrates is their excellent thermal conductivity. Metal substrates can more effectively transfer and disperse the heat generated by electronic devices, thereby maintaining the stability and reliability of electronic devices. Especially in high power density and high temperature environments, metal substrate printed circuit boards perform well and can ensure the normal operation of electronic equipment.
Typically, the metal core of metal substrate printed circuit boards is mainly made of aluminum or copper. Aluminum-based metal substrates are light and easy to process and are suitable for applications with generally low power density, while copper-based metal substrates have higher thermal conductivity and are suitable for applications in high power density and high temperature environments.
In short, metal substrate printed circuit boards have become the first choice for various high-power density electronic equipment due to their excellent heat dissipation performance, providing reliable guarantee for the stable operation of electronic products.
Metal Core PCB design Reference Guide.
Designing a metal substrate PCB requires careful consideration of thermal management, electrical connections, and mechanical stability. Engineers must optimize the layout to ensure optimal heat transfer while maintaining signal integrity and reliability.
First of all, thermal management is one of the key factors that must be considered when designing Metal Core PCB. The metal substrate has high thermal conductivity and can effectively transfer the heat generated by electronic components to the external environment, preventing the device from overheating and ensuring its stable operation. In order to maximize heat transfer efficiency, engineers need to rationally layout the heat dissipation components on the circuit board and use appropriate heat dissipation designs, such as heat sinks, heat sinks or heat pipes, to ensure that heat is effectively dissipated.
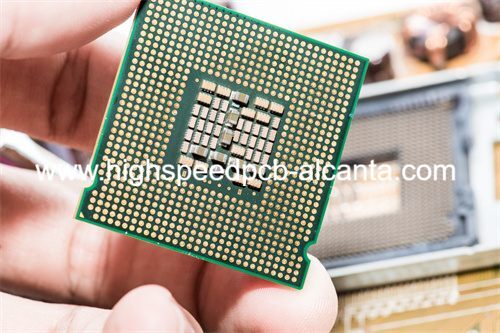
Metal Core PCB Manufacturer
Secondly, electrical connections are another key consideration in the Metal Core PCB design process. During the layout and wiring process, engineers must ensure the stability and reliability of electrical connections to prevent signal interference and electrical failures. To achieve this, they need to precisely design the board’s circuit paths, reduce signal trace lengths and electrical noise, and employ appropriate shielding and filtering techniques to protect critical signals from external interference.
Finally, mechanical stability is another important aspect to focus on during the Metal Core PCB design process. Metal substrates have high stiffness and durability, which can maintain the stability and reliability of electronic devices under harsh environmental conditions. Engineers need to design strong support structures and fixtures to ensure that the PCB will not be deformed or damaged during transportation, installation and use, and can withstand external shock and vibration.
To sum up, designing Metal Core PCB requires comprehensive consideration of multiple aspects such as thermal management, electrical connection, and mechanical stability. By properly optimizing layout and design, engineers can achieve the best performance and reliability of PCBs to meet the needs of various application scenarios.
What material is used in Metal Core PCB?
Metal substrate PCBs (Metal Core PCBs) are made of a variety of materials, with aluminum and copper being the most common core material choices. There is usually a layer of thermally conductive dielectric sandwiched between the metal core board and the copper foil layer. This dielectric material is usually a material with excellent thermal conductivity. The role of this thermally conductive medium is to provide electrical isolation and promote the conduction of heat, thereby effectively dispersing the generated heat throughout the metal core board, maintaining the stability and reliability of the circuit board.
During the manufacturing process of metal core PCBs, selecting the appropriate materials is crucial. Aluminum, one of the commonly used materials for metal cores, has excellent thermal conductivity and good mechanical properties, making it a first choice for many applications. Compared with aluminum, copper core PCB has higher thermal conductivity and electrical conductivity, and is suitable for some occasions that require higher heat dissipation and electrical performance.
The choice of thermally conductive medium is also critical. Thermally conductive dielectric materials commonly used have good thermal conductivity and electrical insulation properties, such as polyimide (PI) or polyamide (PA), to ensure the stability of the circuit board in high-temperature environments. This layer of dielectric material is located between the metal core board and the copper foil layer, which serves as thermal and electrical insulation. It also helps reduce thermal stress and extend the service life of electronic devices.
In general, metal core PCB utilizes different material combinations to achieve excellent thermal management and electrical performance through reasonable design and selection, providing reliable solutions for various application fields.
What size are Metal Core PCB?
Metal Core PCBs come in a variety of sizes, from small and delicate designs for consumer electronics to large, high-power configurations for industrial applications. The selection of these sizes depends on the specific requirements of the electronic device and its intended use.
For consumer electronics, such as smartphones, tablets, and wearable devices, small and delicate metal-based PCBs are often required. These PCBs often have complex layouts to accommodate various components and achieve a high level of integration within limited space. In addition, consumer electronics products often require the weight and thickness of PCBs to be reduced as much as possible to improve portability and comfort.
For industrial applications, such as automotive electronic systems, industrial control equipment, and energy management systems, large and high-power metal-based PCBs are required. These PCBs are often more complex in design to meet higher power density and more stringent environmental requirements. They may require larger sizes to accommodate more power devices and sensors and ensure reliability and stability, even in high-temperature or high-humidity environments.
Whether it is small consumer electronics or large industrial applications, the size of metal-based PCBs is customized according to specific needs and application scenarios. Manufacturers typically work closely with customers to design and produce custom PCBs based on their requirements and technical specifications to ensure optimal performance and reliability. This customized approach enables metal-based PCBs to perform optimally in a variety of applications, driving the continuous advancement and innovation of electronic technology.
The Manufacturer Process of Metal Core PCB.
The manufacturing process of metal-based PCBs involves several key steps, including substrate preparation, copper layer patterning, dielectric layer lamination, solder film coating and surface treatment. During the manufacturing process, advanced technologies such as controlled impedance routing and thermal vias are used to optimize performance.
First, substrate preparation is one of the key steps in metal-based PCB manufacturing. At this stage, the metal-based material (usually aluminum or copper) is prepared and cleaned to ensure the surface is smooth and clean for subsequent processes.
Next is the copper layer pattern making. This step involves placing a conductive pattern on a metal substrate, usually through chemical etching or electroplating. The formation of the copper layer provides conductive paths and connection points for the circuit.
This is followed by dielectric layer lamination. In this process, dielectric materials (usually dielectrics with high thermal conductivity) are stacked layer by layer on top of the copper layers to form a stable structure. This design is designed to improve heat dissipation and ensure the stability and reliability of the circuit board.
Then comes the solder film coating. Solder film is applied on the surface of metal-based PCB to protect the circuit from the external environment and provide a good soldering surface. This helps ensure reliable connection of components and long-term stability of the board.
Finally, there is the surface treatment. At this stage, surface treatment agents are applied to the surface of the metal-based PCB to improve its corrosion resistance and soldering performance. This helps extend the life of metal-based PCBs and ensures their reliability under various environmental conditions.
To summarize, the manufacturing process of metal-based PCBs involves multiple critical steps, each of which plays an important role in the performance and reliability of the final product. By adopting advanced technologies and processes, metal-based PCB manufacturers are able to provide high-quality, high-performance electronic products to meet the needs of different industries.
The Application area of Metal Core PCB.
Metal-based PCBs are widely used in multiple industries, including automotive, aerospace, LED lighting, power electronics, and telecommunications. In these industries, metal-based PCBs play an important role, providing a reliable foundation for various applications.
First, metal-based PCBs are widely used in the automotive industry. They are used in key components such as automotive engine control modules, lighting systems and in-car entertainment systems. Due to the harsh conditions and high temperature environment of the automotive environment, the excellent thermal conductivity and mechanical stability of metal-based PCBs make them the first choice.
Secondly, the aerospace field is also one of the main application fields of metal-based PCBs. Avionics equipment has extremely high requirements for stability and reliability. Metal-based PCBs can meet these requirements and play an important role in aircraft control systems, navigation systems and communication equipment.
In addition, metal-based PCBs are also widely used in the LED lighting industry. LED lighting products require efficient heat dissipation capabilities to ensure long-term stable operation. The excellent thermal conductivity of metal-based PCBs makes them an ideal choice for LED lamps. From street lighting to commercial lighting, metal-based PCBs are playing a key role.
In the field of power electronics, metal-based PCBs are widely used in various power converters and amplifiers. Because metal-based PCBs can effectively disperse and conduct heat, they are particularly suitable for high-power equipment such as power inverters, electric vehicle chargers, etc.
Finally, in the field of telecommunications, metal-based PCBs are used in various communication equipment and base stations. They play an important role in equipment such as radio frequency power amplifiers, microwave signal processors, and antenna control units, providing support for the stable operation of communication networks.
Overall, metal-based PCBs play a key role in multiple industries, providing a reliable circuit foundation for a variety of applications. With the continuous advancement of technology and the growth of industry demand, the application scope of metal-based PCBs will continue to expand, injecting new vitality into future innovation and development.
What are the advantages of Metal Core PCB?
Metal Core PCBs have many advantages over traditional PCBs, including:
Superior thermal management
The metal chips provide efficient heat conduction, allowing electronic components to operate at lower temperatures, thereby increasing overall reliability. In high-power applications, Metal Core PCBs can quickly conduct the generated heat to the surrounding environment to prevent electronic components from overheating and damage.
Excellent mechanical stability
Metal Core PCBs offer increased rigidity and durability compared to standard PCBs, making them suitable for harsh environments and high-vibration applications. This stability makes Metal Core PCBs widely used in industrial fields, such as automotive electronic control units and aerospace equipment.
Higher power handling capabilities
Metal Core PCBs are capable of handling higher current and power densities, making them ideal for high-power electronic devices. This capability makes Metal Core PCBs widely used in fields such as power inverters, motor drives, and solar inverters.
Compact design
Metal Core PCBs have excellent thermal properties, allowing for more compact designs and higher component density, saving space in electronic components. This is critical for space-constrained applications such as embedded systems, LED lighting and mobile devices.
Overall, the many advantages of Metal Core PCBs make it one of the key technologies in today’s electronics industry. With the continuous advancement of technology and the expansion of application fields, Metal Core PCB manufacturers will continue to play an important role in promoting the innovation and development of electronic equipment.
FAQ
Are metal-based PCBs more expensive than traditional PCBs?
Metal-based PCBs can cost more because they use special materials and manufacturing processes. However, this investment can often be justified due to its superior performance and reliability, especially in critical applications.
Can metal-based PCBs be used in consumer electronics?
Yes, metal-based PCBs are increasingly used in consumer electronics, especially in areas such as high-power LED lighting, audio amplifiers, and computer peripherals, where efficient heat conduction is critical.
Are metal-based PCBs suitable for high-frequency electronics?
Yes, metal-based PCBs can play a role in high-frequency electronics. For applications requiring high-speed signal transmission and low signal distortion, specially designed metal-based PCBs can be used to meet high-frequency requirements.
What is the maximum size of a metal-based PCB?
The size of the metal-based PCB depends on the manufacturer’s capabilities and the customer’s needs. Typically, they can be manufactured into small electronic modules or scaled up for large, high-power applications.