What is MEGTRON 7 PCB?
MEGTRON 7 PCB Manufacturer.MEGTRON 7 PCB Manufacturer, renowned for its cutting-edge technology and precision engineering, stands as a beacon of excellence in the electronics industry. With unparalleled expertise in producing high-performance printed circuit boards (PCBs), they redefine industry standards. MEGTRON 7’s commitment to innovation ensures products that excel in reliability, efficiency, and durability. Their state-of-the-art facilities, coupled with a dedicated team of experts, guarantee flawless execution from design to production. Trusted by leading tech firms worldwide, MEGTRON 7 PCBs epitomize quality, driving the advancement of electronic devices across diverse sectors.
MEGTRON 7 PCB, as an innovative technology in the electronic field, is gradually becoming the focus of the industry. This packaging substrate not only represents a technological leap, but also plays a key role in the design and manufacturing of high-performance electronic devices. In this article, we will delve into what makes MEGTRON 7 PCB unique and its exceptional performance in today’s electronics industry.
MEGTRON 7 PCB is a high-performance material designed to meet the demanding signal transmission, thermal management and reliability requirements of advanced electronic equipment. Its unique material combination and manufacturing process make it stand out in the electronics industry and become the packaging substrate of choice for many engineers and manufacturers.
As electronic devices become increasingly complex and diverse, traditional packaging substrates often find it difficult to meet the requirements for high frequency, low loss and thermal performance. The emergence of MEGTRON 7 PCB fills this technological gap and provides designers with a broader space for innovation. This article will deeply explore the technical characteristics of MEGTRON 7 PCB and show you a full picture of how this packaging substrate surpasses tradition in all aspects and leads the innovation trend in the electronics industry. With our in-depth discussion, I believe you will have a deeper understanding of the unique features of MEGTRON 7 PCB, and then realize its core position in the electronic field.
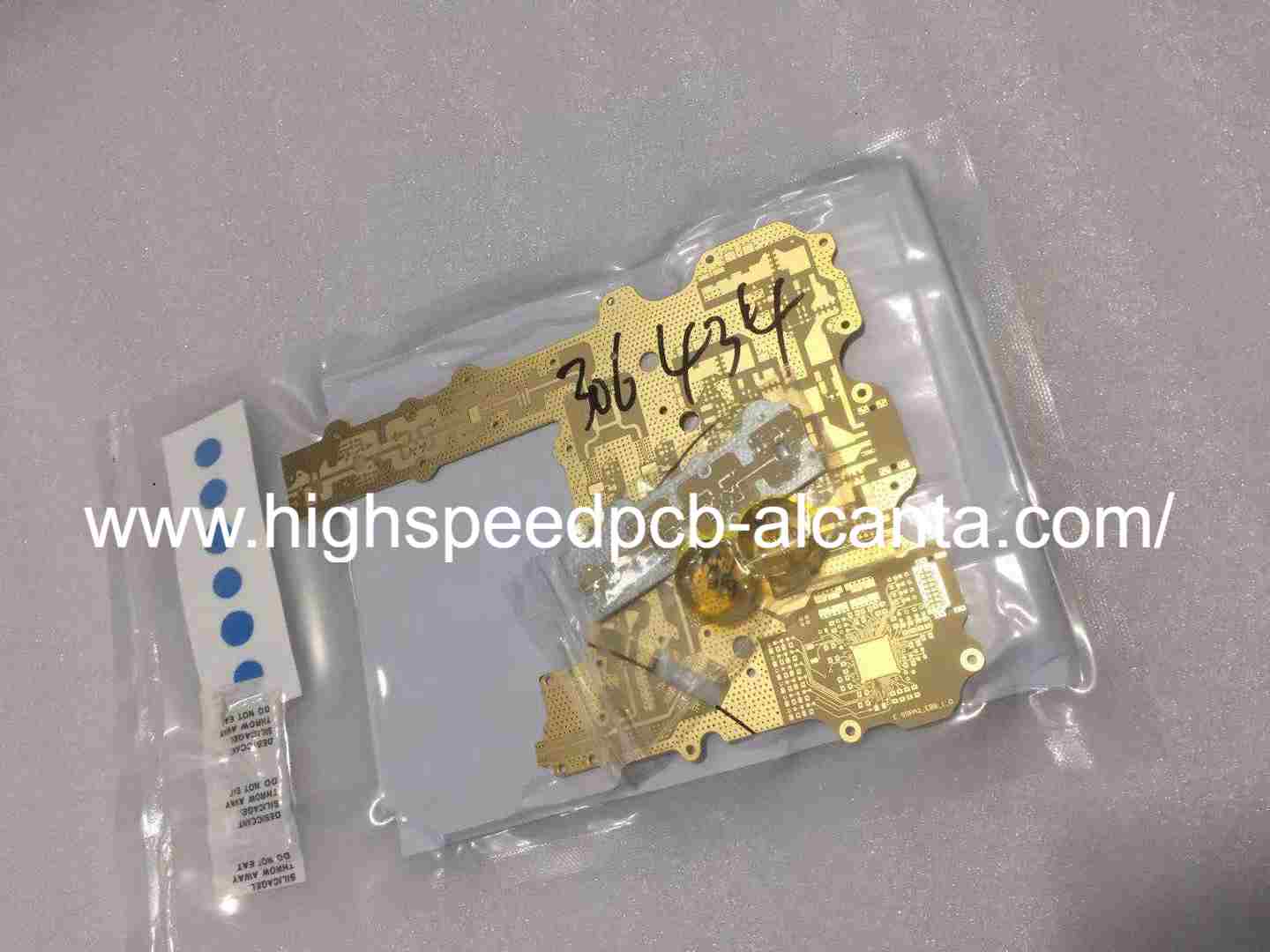
MEGTRON 7 PCB Manufacturer
Ultra-low Loss, Highly Heat Resistant Circuit Board Materials
Ultra-low transmission loss and highly heat-resistant circuit board materials are an important innovation in today’s electronic manufacturing field, providing key support for the development of modern high-performance electronic devices. This advanced circuit board material is widely used in communications, computers, radio frequency electronics and other fields with its unique performance characteristics.
Primarily, the circuit board material under consideration exhibits outstanding properties with ultra-low transmission loss. Transmission loss, quantified in decibels (dB), represents the energy dissipated during signal transmission through a circuit. The material, distinguished by an optimized conductive and insulating layer structure, effectively curtails energy loss during signal transmission. This feature is pivotal for preserving signal strength, minimizing distortion, and elevating overall system performance, ensuring the circuit operates with efficiency.
Furthermore, the material boasts remarkable heat resistance, enabling it to sustain optimal performance even in extreme temperature environments. Particularly crucial for high-temperature applications like automotive engine control systems, military electronics, and space detectors, the circuit board material utilizes a high-temperature-resistant base material and a heat-stable conductive layer to guarantee circuit stability and reliability in challenging operating conditions.
Moreover, the material exhibits exceptional mechanical strength and chemical stability owing to its purpose-built multi-layer construction. Engineered to meet the robustness and stability demands across diverse applications, this design empowers the material to withstand mechanical stress and resist chemical corrosion, thus ensuring prolonged reliability and reducing equipment maintenance and replacement costs.
This circuit board material, distinguished by ultra-low transmission loss and high heat resistance, assumes a pivotal role in critical fields such as 5G communications, satellite communications, radar systems, and high-performance computers. Beyond advancing communication technology and enhancing the speed and reliability of wireless communications, it offers innovative solutions for high-performance computing and radio frequency applications.
Overall, ultra-low transmission loss and highly heat-resistant circuit board materials represent cutting-edge technologies in electronics manufacturing. As technology continues to develop, this material will continue to promote the performance improvement of electronic devices and bring more innovation and progress to various application fields.
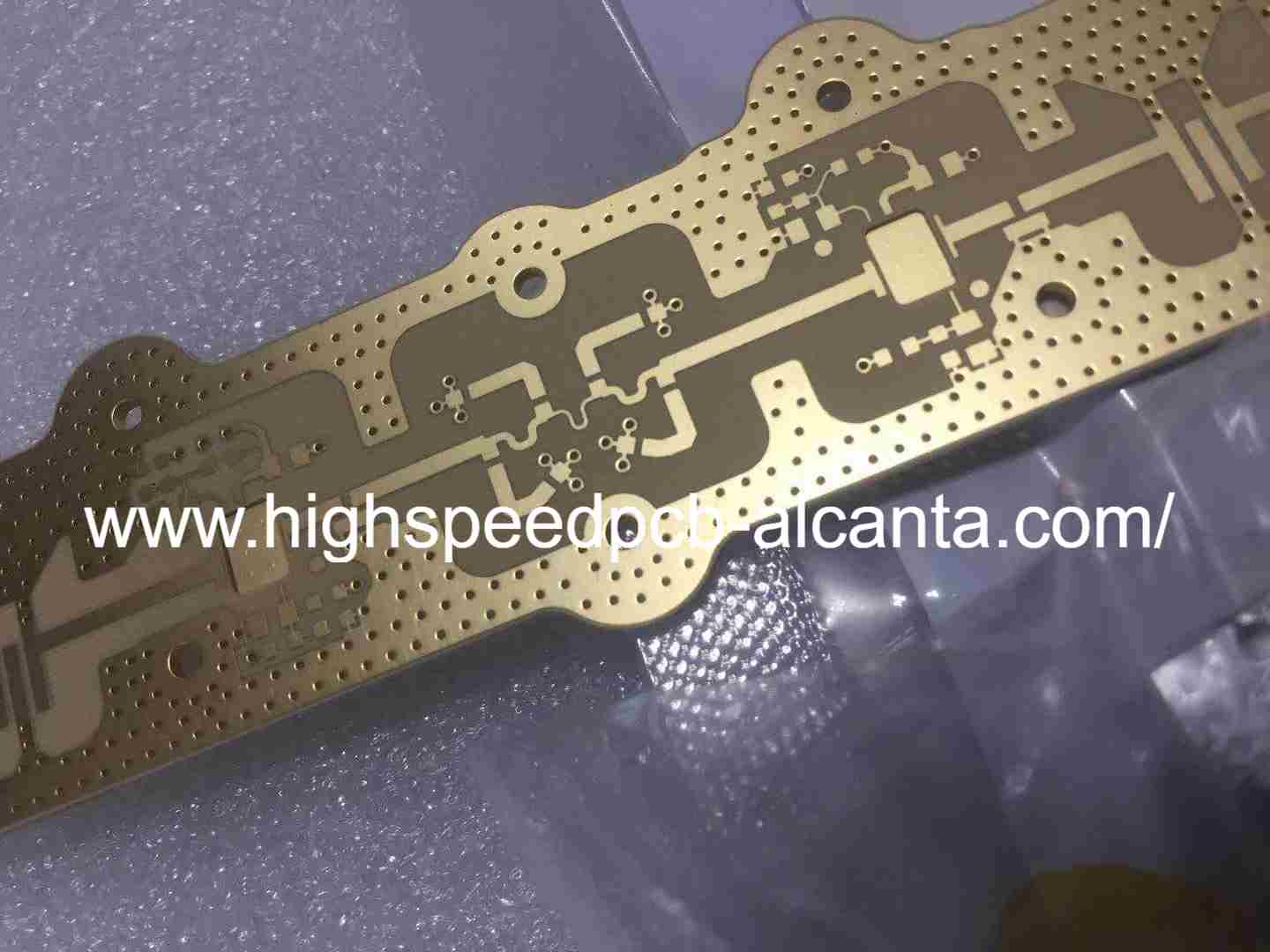
MEGTRON 7 PCB
LaminateR-5785(N)/Prepreg R-5680(N)
Laminate R-5785(N) and Prepreg R-5680(N) are advanced composite materials mainly used to manufacture high-performance multi-layer printed circuit boards (PCBs). These two materials have attracted widespread attention for their superior electrical properties, mechanical strength and heat resistance, and are indispensable materials in the field of modern electronic equipment manufacturing.
Laminate R-5785(N) stands out as a multi-layer circuit board substrate characterized by outstanding electrical properties. Crafted through lamination with high-performance resin and glass fiber, it boasts a low dielectric constant and minimal dielectric loss. These features contribute to the reduction of energy loss during signal transmission, enabling the circuit board to efficiently transmit signals. This, in turn, mitigates signal attenuation and distortion, ultimately enhancing system performance and reliability.
Secondly, Prepreg R-5680(N) is a prepreg material that is often used in combination with Laminate R-5785(N). This prepreg material acts as an adhesive when manufacturing multi-layer circuit boards, holding the layers together. Prepreg R-5680(N) has excellent fluidity and adhesion, ensuring that the various layers of materials can be evenly combined to form a solid circuit board structure under high temperature and pressure.
Both Laminate R-5785(N) and Prepreg R-5680(N) stand out for their exceptional heat-resistant properties, exhibiting stability in high-temperature environments without succumbing to deformation or performance deterioration. This characteristic renders them exceptionally well-suited for applications demanding elevated-temperature operation, including automotive engine control systems, aerospace equipment, and high-performance computers.
Moreover, these materials boast impressive mechanical strength, ensuring structural stability even in intricate manufacturing and usage scenarios. Their robust resistance to chemical corrosion fortifies them against the detrimental effects of various chemicals, thereby enhancing the overall durability of the circuit board.
Their use helps improve the performance of electronic devices and promotes more advanced, compact designs. At the same time, their reliability and durability enable electronic devices to maintain efficient operation in the face of extreme environmental conditions, providing a solid foundation for innovation in various industries. As technology continues to evolve, advanced materials such as Laminate R-5785(N) and Prepreg R-5680(N) will continue to drive advancements in electronics manufacturing.
The ultra-low dielectric constant (Dk) and dissipation factor (Df) make MEGTRON 7 ideal for high speed and large data volumes associated with servers and routers required for 5G.
The MEGTRON 7 family, including MEGTRON 7(N), MEGTRON 7(GE) and MEGTRON 7(GN), is High Density Interconnect (HDI) technology compatible with very high layer count and large format printed Circuit Board (PCB) layouts.
R-5785(GN)/R-5680(GN)
Specification / Laminate R-5785(GE) & R-5785(GN)
Property | Units | Test Method | Condition | Typical Value | |||
THERMAL | Glass Transition Temp ( Tg) | C | DSC | As received | 200 | 200 | |
TMA | As received | 190 | 190 | ||||
DMA | As received | 210 | 210 | ||||
Thermal Decomposition Temp ( Td ) | C | TGA | As received | 400 | 400 | ||
Time to Delam ( T288 ) |
Without Cu | min | IPC TM-650 2.4.24.1 | As received | > 120 | > 120 | |
With Cu | min | IPC TM-650 2.4.24.1 | As received | > 120 | > 120 | ||
CTE :α1 | X- axis | ppm/C | IPC TM-650 2.4.24 | < Tg | 14~16 | 14~16 | |
Y – axis | ppm/C | IPC TM-650 2.4.24 | < Tg | 14~16 | 14~16 | ||
Z – axis | ppm/C | IPC TM-650 2.4.24 | < Tg | 42 | 42 | ||
CTE :α2 | Z – axis | ppm/C | IPC TM-650 2.4.24 | > Tg | 280 | 280 | |
ELECTRICAL | Volume Resistivity | MΩ-cm | IPC TM-650 2.5.17.1 | C-96/35/90 | 1*10⁹ | 1*10⁹ | |
Surface Resistivity | MΩ | IPC TM-650 2.5.17.1 | C-96/35/90 | 1×10⁸ | 1×10⁸ | ||
Dielectric Constant (Dk ) |
@1MHz | ⁻ | IPC TM-650 2.5.5.9 | C-24/23/50 | 3.37 | 3.37 | |
@1GHz | ⁻ | *Note 1 | C-24/23/50 | 3.60@13GHZ | 3.31@13GHZ | ||
Dissipation Factor (Df) |
@1MHz | ⁻ | IPC TM-650 2.5.5.9 | C-24/23/50 | 0.002 | 0.001 | |
@1GHz | ⁻ | *Note 1 | C-24/23/50 | 0.0034@13GHZ | 0.0023@13GHZ | ||
PHYSICAL | Water Absorption | % | IPC TM-650 2.6.2.1 | D-24/23 | 0.06 | 0.06 | |
Peel Strength | 1oz(H-VLP2) | kN/m | IPC TM-650 2.4.8 | As Received | 0.8 | 0.8 | |
Flammability | ⁻ | UL | C-48/23/50 | 94V-0 | 94V-0 | ||
Sample thickness ;29.5 mil=0.750mm(Core Type 30) | |||||||
The data in the above table are not guaranteed values. |
R-5785(N)/R-5680(N)
Specification / Laminate R-5785(N)
Property | Units | Test Method | Condition | Typical Value | ||
R-5785(N) Low-Dk glass |
||||||
THERMAL | Glass Transition Temp ( Tg) | C | DSC | As received | 200 | |
DMA | As received | 210 | ||||
Thermal Decomposition Temp ( Td ) | C | TGA | As received | 400 | ||
Time to Delam ( T288 ) |
Without Cu | min | IPC TM-650 2.4.24.1 | As received | > 120 | |
With Cu | min | IPC TM-650 2.4.24.1 | As received | > 120 | ||
CTE :α1 | X- axis | ppm/C | IPC TM-650 2.4.24 | < Tg | 14~16 | |
Y – axis | ppm/C | IPC TM-650 2.4.24 | < Tg | 14~16 | ||
Z – axis | ppm/C | IPC TM-650 2.4.24 | < Tg | 42 | ||
CTE :α2 | Z – axis | ppm/C | IPC TM-650 2.4.24 | > Tg | 280 | |
ELECTRICAL | Volume Resistivity | MΩ-cm | IPC TM-650 2.5.17.1 | C-96/35/90 | 1*10⁹ | |
Surface Resistivity | MΩ | IPC TM-650 2.5.17.1 | C-96/35/90 | 1×10⁸ | ||
Dielectric Constant (Dk ) |
@1MHz | ⁻ | IPC TM-650 2.5.5.9 | C-24/23/50 | 3.37 | |
@14GHz | ⁻ | *Note 1 | C-24/23/50 | 3.31 | ||
Dissipation Factor (Df) |
@1MHz | ⁻ | IPC TM-650 2.5.5.9 | C-24/23/50 | 0.001 | |
@14GHz | ⁻ | *Note 1 | C-24/23/50 | 0.0023 | ||
PHYSICAL | Water Absorption | % | IPC TM-650 2.6.2.1 | D-24/23 | 0.06 | |
Peel Strength | 1oz(H-VLP2) | kN/m | IPC TM-650 2.4.8 | As Received | 0.8 | |
Flammability | ⁻ | UL | C-48/23/50 | 94V-0 | ||
Sample thickness ;29.5 mil=0.750mm(Core Type 30) | ||||||
The data in the above table are not guaranteed values. |
R-5785(GE)/R-5680(GE)
Specification / Laminate R-5785(GE) & R-5785(GN)
Property | Units | Test Method | Condition | Typical Value | |||
R-5785(GE) E glass |
R-5785(GN) Low-Dk glass |
||||||
THERMAL | Glass Transition Temp ( Tg) | C | DSC | As received | 200 | 200 | |
TMA | As received | 190 | 190 | ||||
DMA | As received | 210 | 210 | ||||
Thermal Decomposition Temp (Td ) | C | TGA | As received | 400 | 400 | ||
Time to Delam( T288 ) | Without Cu | min | IPC TM-650 2.4.24.1 | As received | > 120 | > 120 | |
With Cu | min | IPC TM-650 2.4.24.1 | As received | > 120 | > 120 | ||
CTE :α1 | X- axis | ppm/C | IPC TM-650 2.4.24 | < Tg | 14~16 | 14~16 | |
Y – axis | ppm/C | IPC TM-650 2.4.24 | < Tg | 14~16 | 14~16 | ||
Z – axis | ppm/C | IPC TM-650 2.4.24 | < Tg | 42 | 42 | ||
CTE :α2 | Z – axis | ppm/C | IPC TM-650 2.4.24 | > Tg | 280 | 280 | |
ELECTRICAL | Volume Resistivity | MΩ-cm | IPC TM-650 2.5.17.1 | C-96/35/90 | 1*10⁹ | 1*10⁹ | |
Surface Resistivity | MΩ | IPC TM-650 2.5.17.1 | C-96/35/90 | 1×10⁸ | 1×10⁸ | ||
Dielectric Constant (Dk ) |
@1MHz | ⁻ | IPC TM-650 2.5.5.9 | C-24/23/50 | 3.63 | 3.37 | |
@13,14GHz | ⁻ | *Note 1 | C-24/23/50 | 3.60@13GHZ | 3.31@14GHZ | ||
Dissipation Factor (Df) |
@1MHz | ⁻ | IPC TM-650 2.5.5.9 | C-24/23/50 | 0.002 | 0.001 | |
@13,14GHz | ⁻ | *Note 1 | C-24/23/50 | 0.0034@13GHZ | 0.0023@14GHZ | ||
PHYSICAL | Water Absorption | % | IPC TM-650 2.6.2.1 | D-24/23 | 0.06 | 0.06 | |
Peel Strength | 1oz(H-VLP2) | kN/m | IPC TM-650 2.4.8 | As Received | 0.8 | 0.8 | |
Flammability | ⁻ | UL | C-48/23/50 | 94V-0 | 94V-0 | ||
Sample thickness ;29.5 mil=0.750mm(Core Type 30) | |||||||
The data in the above table are not guaranteed values. |
What are the structure and functions of MEGTRON 7 PCB?
MEGTRON 7 PCB, a prominent player in the realm of printed circuit board (PCB) materials, has asserted itself in the electronics industry due to its distinctive structure and exceptional performance. A closer examination of its composition not only enhances our comprehension of its merits but also unveils its extensive utility across demanding applications.
Firstly, let’s delve into the honeycomb structure integrated into MEGTRON 7 PCB. This innovative design imbues the entire board with a lightweight and slim profile, all while exhibiting remarkable mechanical strength and impact resistance. The introduction of this honeycomb structure successfully addresses limitations found in traditional substrates, presenting an optimal solution for the weight-reduction and high-strength requisites of equipment. Its unique architecture facilitates outstanding performance across diverse environments, establishing it as one of the most sought-after PCB materials in contemporary electronic devices.
Turning our attention to the electrical and thermal performance of MEGTRON 7 PCB, it excels under high-frequency and high-speed operational conditions, meeting the stringent requirements of advanced electronic equipment for transmission rate and frequency response. Simultaneously, its commendable heat dissipation capabilities position it favorably for applications demanding robust performance, such as communication equipment and computer hardware. This not only enhances equipment stability and reliability but also provides robust support for maintaining peak performance during high-load operations.
These superior properties of MEGTRON 7 PCB make it highly respected in the electronics manufacturing industry. By using a honeycomb structure, it successfully balances the contradiction between thinness and strength, and its performance in electrical and thermal properties is even more impressive. This enables MEGTRON 7 PCB to not only meet the needs of current electronic equipment for high performance and high reliability, but also lay a solid foundation for the development of future electronic technology.
What are the electrical and thermal properties of MEGTRON 7 PCB?
As an advanced printed circuit board (PCB) material, MEGTRON 7 PCB has become the first choice for many demanding applications due to its excellent electrical and thermal properties. MEGTRON 7 PCB exhibits excellent performance in high-frequency and high-speed environments, making it an ideal choice in fields such as communication equipment and computer hardware.
First of all, MEGTRON 7 PCB uses a unique honeycomb structure, which provides it with excellent electrical performance. At high frequencies, this structure effectively reduces losses in signal transmission and ensures signal stability and accuracy. This enables MEGTRON 7 PCB to cope with complex circuit designs and is suitable for advanced electronic equipment requiring high-frequency transmission.
Furthermore, the MEGTRON 7 PCB exhibits excellent performance in high-speed environments. The incorporation of a honeycomb structure not only contributes to a lighter and thinner board but also enhances its mechanical strength, effectively minimizing the time delay in signal transmission. This attribute proves particularly crucial in applications demanding high-speed data transfer, such as computer hardware.
At the same time, MEGTRON 7 PCB also exhibits excellent heat dissipation performance. In various applications, especially in communication equipment and computer hardware, heat dissipation issues have always been of great concern. MEGTRON 7 PCB effectively dissipates the heat generated by electronic equipment through its excellent heat dissipation performance, ensuring that the equipment can maintain stable working conditions under long-term high-load operation. This provides reliable guarantee for high-performance applications and extends the service life of equipment.
Therefore, the excellent electrical and thermal properties of MEGTRON 7 PCB make it stand out in many fields. Whether it is communication equipment used for high-frequency transmission or computer hardware requiring high-speed data processing, MEGTRON 7 PCB exhibits excellent performance and has become an ideal choice for electronic engineers and designers pursuing excellent performance and reliability.
What are the manufacturing technologies for MEGTRON 7 PCB?
MEGTRON 7 PCB’s manufacturing technology is a compelling aspect of this advanced printed circuit board material. By delving deeper into its manufacturing process, we can better understand how this material can meet the high performance and reliability needs of advanced electronic devices.
First, the manufacturing process of MEGTRON 7 PCB adopts improved high-density interconnect (HDI) technology. This technology enables higher circuit density by adding more layers to the surface of the board. This is crucial for accommodating more circuit components in a limited space, especially with the increasing demand for small, lightweight devices in modern electronic devices. By improving HDI technology, MEGTRON 7 PCB effectively improves the performance and functionality of the circuit board.
Secondly, MEGTRON 7 PCB adopts an innovative manufacturing process, namely the improved semi-additive method. This approach introduces more precision and control into the manufacturing process, thereby increasing production efficiency. The advantage of the improved semi-additive method is the ability to achieve higher production speeds without compromising quality, while also reducing scrap rates in the manufacturing process. This is crucial to ensure the stability and consistency of MEGTRON 7 PCBs.
In this process, the manufacturer also took into account the honeycomb structure of the MEGTRON 7 PCB. The introduction of this structure makes the board lighter and thinner, while improving mechanical strength and impact resistance. This is critical for the reliability of electronic devices in various environments, especially in applications requiring high durability and long life.
In general, the manufacturing technology of MEGTRON 7 PCB integrates improved HDI technology, innovative semi-additive method and unique honeycomb structure design. Together, these advanced manufacturing technologies ensure MEGTRON 7 PCB’s excellent electrical, thermal and mechanical performance, making it an indispensable part of today’s high-performance electronic equipment.
What is the manufacturing process of MEGTRON 7 PCB?
MEGTRON 7 PCB is an excellent printed circuit board (PCB) material and its manufacturing technology has attracted much attention. We will take an in-depth look at the manufacturing process of MEGTRON 7 PCB, which includes its improved high-density interconnect (HDI) manufacturing technology and a new manufacturing process using a semi-additive method.
First, the manufacturing process of MEGTRON 7 PCB relies on improved high-density interconnect (HDI) technology. By introducing improved HDI manufacturing technology, MEGTRON 7 PCB can achieve a more compact circuit layout and effectively increase the circuit density on the circuit board.
Secondly, the semi-additive method in the new manufacturing process provides an innovative solution for the manufacturing of MEGTRON 7 PCB. The semi-additive method is a manufacturing method that gradually adds copper foil to the surface of the substrate to form a circuit pattern. In the manufacturing of MEGTRON 7 PCB, this new process is applied, which not only improves manufacturing efficiency, but also ensures high-quality products. Through the semi-additive method, the manufacturing process of MEGTRON 7 PCB is more flexible and can better adapt to the requirements of complex circuit design.
Taken together, the manufacturing process of MEGTRON 7 PCB has achieved a more advanced and efficient production method with the introduction of high-density interconnection technology and semi-additive method. These innovative manufacturing techniques not only improve the performance of MEGTRON 7 PCBs, but also make them ideal in the electronics field. Through continuous innovation and optimization of manufacturing processes, MEGTRON 7 PCB will continue to play a key role in future electronic devices, providing reliable support for high-performance applications.
How is MEGTRON 7 PCB different from other PCBs?
MEGTRON 7 PCB, as an advanced printed circuit board (PCB) material, exhibits a series of significant differences compared with traditional substrates and conventional printed wiring boards (PWBs). In this regard, we will delve into these differences to better understand the outstanding features of MEGTRON 7 PCB in the field of electronics.
The difference between MEGTRON 7 PCBs and PWBs
There are differences in structure and performance between PWBs (Printed Wire Boards) and conventional printed circuit boards (PCBs), and MEGTRON 7 PCB further enhances these differences. First of all, PWBs usually use more traditional materials, while MEGTRON 7 uses a high-performance glass fiber reinforced honeycomb structure, making the board lighter and thinner while improving mechanical strength and impact resistance.
In different applications, MEGTRON 7 PCB reflects more excellent performance. For example, in high-frequency and high-speed applications, MEGTRON 7 PCB performs well and has lower transmission losses, making it the first choice in fields such as communication equipment and computer hardware. This highlights the significant advantages of MEGTRON 7 in electrical performance, providing reliable support for various advanced applications.
Significant differences between MEGTRON 7 PCB and traditional substrates
Compared with traditional substrates, MEGTRON 7 PCB shows significant differences in electrical properties, thermal properties and structure. First, it uses improved high-density interconnect (HDI) manufacturing technology to increase line density and adapt to more complex circuit designs. This makes MEGTRON 7 PCB more flexible and adaptable in demanding electronic equipment.
In terms of electrical performance, MEGTRON 7 PCB performs well and is suitable for high frequency and high speed applications. Compared with traditional substrates, MEGTRON 7 PCB is more stable when transmitting signals, reducing signal distortion and transmission loss, thus improving overall performance.
In terms of thermal performance, MEGTRON 7 PCB has excellent heat dissipation performance through its honeycomb structure and improved semi-additive manufacturing technology. This allows it to maintain stable performance under high-load operation and high-temperature environments, providing longer service life for electronic equipment.
Overall, MEGTRON 7 PCB demonstrates significant advantages in all aspects compared with traditional substrates and conventional PCBs by introducing advanced structure and manufacturing technology. Its high performance and high reliability make it a key component in today’s advanced electronic applications.
What are some frequently asked questions about MEGTRON 7 PCB?
In the process of in-depth understanding of MEGTRON 7 PCB, many readers may have some common questions. Here are some common questions and their answers to help readers better understand this advanced PCB material.
How does MEGTRON 7 PCB improve electrical performance?
MEGTRON 7 PCB excels in electrical performance through its unique high-performance glass fiber reinforced honeycomb structure. This structure reduces signal transmission losses and improves performance in high-frequency and high-speed applications. MEGTRON 7’s electrical performance advantages make it the first choice for many communications equipment and computer hardware.
What are the thermal properties of MEGTRON 7 PCBs?
MEGTRON 7 PCB not only excels in electrical performance, but also in thermal performance. Its design takes the heat dissipation effect into consideration to ensure that in high-load and high-frequency applications, it can effectively cool electronic components and maintain system stability and reliability.
What are the advantages of MEGTRON 7 PCB compared to traditional substrates?
Compared with traditional substrates, the structural honeycomb design of MEGTRON 7 PCB not only reduces weight, but also improves mechanical strength and impact resistance. This makes it more suitable for use in harsh environmental conditions, providing a significant improvement in the reliability and stability of electronic equipment.
What kind of manufacturing process does MEGTRON 7 PCB use?
MEGTRON 7 PCB adopts improved high-density interconnect (HDI) manufacturing technology and semi-additive method to increase circuit density and manufacturing efficiency. These advanced manufacturing techniques ensure the reliability of complex circuits on the board, providing designers with more flexibility.
How is MEGTRON 7 PCB different from regular PCBs and PWBs?
Compared with conventional PCB and PWB, MEGTRON 7 PCB has significant differences in electrical performance, thermal performance and structure.
By answering these frequently asked questions, we hope readers can gain a more comprehensive understanding of MEGTRON 7 PCB and better utilize this advanced technology in practical applications.
What is the comprehensive understanding of the structure, function and manufacturing technology of MEGTRON 7 PCB?
Through in-depth research on MEGTRON 7 PCB, we can fully understand its unique structure, excellent functions and advanced manufacturing technology. MEGTRON 7 PCB uses a high-performance glass fiber reinforced honeycomb structure, allowing it to play a vital role in electronic devices.
From a structural standpoint, the honeycomb configuration of MEGTRON 7 PCB not only imparts a lighter and more slender profile to the board but also substantially enhances its mechanical strength and resilience against impacts. This distinctive design not only facilitates outstanding performance at elevated frequencies and speeds but also ensures the board’s reliability across diverse environmental conditions.
Its excellent electrical and thermal properties further highlight the importance of MEGTRON 7 PCB. It performs well in high-frequency and high-speed application scenarios, providing reliable support for high-performance applications such as communication equipment and computer hardware. The excellent heat dissipation performance ensures effective cooling during operation and maintains the stability of the equipment.
The manufacturing prowess of MEGTRON 7 PCB stands as a point of pride, exemplified by its advanced high-density interconnect (HDI) technology. This innovation enables the accommodation of more lines within the same area, allowing for intricate and sophisticated circuit designs. Simultaneously, the implementation of an enhanced semi-additive method not only elevates manufacturing efficiency but also guarantees the superior quality of the end product.
As the demand for high performance in the electronics industry continues to increase, MEGTRON 7 PCB will become a key factor in promoting technological progress with its unique advantages. Its wide application in communications, computers, medical equipment and other fields will provide strong support for innovation and development in these fields.
In general, MEGTRON 7 PCB not only shows excellence in structure, function and manufacturing technology, but also has broad application prospects in the electronic field. Its advanced performance will provide reliable support for current and future electronic devices and promote the continuous development of science and technology.