Manufacturer of The CPU Package Substrates.The manufacturer specializes in crafting intricate CPU package substrates, finely engineered to meet the demands of cutting-edge technology. Their production line hums with precision as skilled hands meticulously assemble each component, ensuring optimal performance and reliability. From intricate circuitry to durable materials, every substrate embodies innovation and quality. With a commitment to excellence, they push the boundaries of possibility, delivering substrates that power the next generation of computing devices. In the heart of their facility, a fusion of expertise and state-of-the-art machinery drives forward the evolution of CPU technology.
CPU packaging substrate plays a key role in modern electronic technology. It not only carries the functions of the CPU, but also connects various necessary electronic components. This article comprehensively introduces the design, materials, manufacturing processes, application areas, advantages and FAQs of CPU packaging substrates, aiming to provide readers with the opportunity to gain an in-depth understanding of this important technology. The careful design and high-quality materials of the CPU packaging substrate enable it to play an irreplaceable role in various electronic devices, providing a solid foundation for the development of modern technology.
What are CPU Package Substrates?
CPU packaging substrate is one of the indispensable key components in modern electronic equipment. It is a flat substrate usually made of non-conductive material such as fiberglass, epoxy or composite. What is special about this substrate is that it has conductive paths laid or printed on its surface. These paths are called lines. These lines play an extremely important role. They are like a precise electronic map, electrically connecting various electronic components connected to the substrate.
Imagine that a CPU packaging substrate is like the skeleton of an electronic device. It provides a stable support platform for the CPU and other key electronic components, and connects them together through precision-designed lines. These lines can be extremely thin metal foils or copper wires printed on the surface of the substrate through printing technology. They form a complex and precise network on the substrate, ensuring the smooth transmission of electronic signals and the normal operation of the circuit. run.
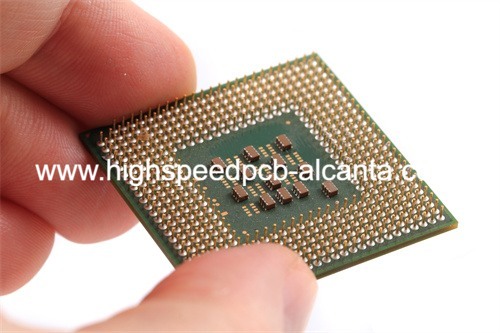
Manufacturer of The CPU Package Substrates
In addition, the CPU packaging substrate not only provides electrical connections, but also provides mechanical support and thermal management functions. By mounting the CPU and other heat-sensitive components directly on the substrate, the CPU packaging substrate can effectively conduct and dissipate heat, maintaining the stability and reliability of electronic equipment.
In general, CPU packaging substrates play a vital role in modern electronic technology. They are not only the core components of electronic devices, but also a key bridge that connects and supports various electronic components. Through careful design and manufacturing, CPU packaging substrates provide a stable and reliable foundation for our electronic devices and promote the development and progress of modern technology.
CPU Package Substrates design Reference Guide.
The design of the CPU packaging substrate is a key link in ensuring the functionality and performance of the entire system. The design process involves the placement of electronic components and routing of circuits to achieve optimal circuit connectivity and performance. When designing a CPU packaging substrate, several factors need to be considered to ensure that the final product meets expected quality standards and performance requirements.
First, designers need to properly arrange the layout of electronic components. This involves choosing the best component locations to achieve the shortest circuit path and minimum signal delay. Through precise component placement, signal transmission efficiency can be optimized and interference and noise in the circuit can be reduced.
Second, design considerations include signal integrity. During the design process, attention needs to be paid to issues such as impedance matching, signal stacking and crossing of signal transmission lines to ensure the stability and reliability of signal transmission. By optimizing signal integrity, signal distortion and interference can be minimized and the system’s anti-interference capability improved.
In addition, thermal management is also one of the factors that need to be considered during the design process. The CPU packaging substrate will generate a large amount of heat during operation. If the heat cannot be effectively removed, the stability and reliability of the system will be affected. Therefore, designers need to properly design the heat dissipation structure and ventilation system to ensure that the CPU packaging substrate can maintain a suitable operating temperature under high load.
Finally, manufacturability needs to be considered during the design process. This includes taking into account process limitations and cost factors in the manufacturing process, as well as design maintainability and repairability. By properly considering the feasibility of manufacturing, you can ensure that the design plan can be successfully transformed into actual products and remain efficient and economical during the manufacturing process.
To sum up, the design of CPU packaging substrate is a complex process that takes into account multiple factors and requires designers to have rich experience and professional knowledge. Through reasonable component layout, signal integrity optimization, thermal management design and manufacturability considerations, the best design solution can be achieved to ensure that the final product has excellent functionality and performance.
What material is used in CPU Package Substrates?
CPU packaging substrate is a vital part of modern electronic equipment, and the materials used play a vital role in its performance and stability. Typically, the CPU packaging substrate is made of materials such as fiberglass reinforced epoxy resin (FR4). FR4 is a common substrate material with good insulation properties, mechanical strength and heat resistance, and is suitable for most application scenarios.
However, as technology develops and application requirements continue to change, CPU packaging substrates are gradually using other materials to meet specific requirements. For example, for some applications that require high mechanical strength and high temperature resistance, such as automotive electronic systems or aerospace equipment, ceramic materials may be selected. Ceramic substrates have excellent high temperature resistance and mechanical strength and can work stably in extreme environments.
In addition, for some scenarios that have strict requirements on size and weight, polyimide materials may become the first choice. Polyimide substrates are lightweight, high-strength and have excellent electrical properties, making them suitable for high-density circuit design and miniaturization application scenarios.
In addition, some applications with special requirements may choose metal core substrates as the material of the CPU packaging substrate. Metal core substrates have excellent heat dissipation properties and can effectively conduct heat to the external environment, making them suitable for high-power and high-performance electronic equipment.
To sum up, the materials used in CPU packaging substrates vary depending on application requirements. Choosing appropriate materials can ensure that the CPU packaging substrate has stable performance and reliability under various environments and working conditions. With the continuous advancement of technology, more new materials may emerge for CPU packaging substrates in the future to meet the increasingly complex electronic device design needs.
What size are CPU Package Substrates?
The size of the CPU packaging substrate varies depending on the specific application and the size of the electronic device or system. In different application scenarios, CPU packaging substrates come in a wide range of sizes, from small substrates used in tiny mobile phones and wearable devices to large substrates required for huge industrial equipment and telecommunications infrastructure.
For small electronics such as mobile phones and wearable devices, the size of the CPU packaging substrate is often very delicate. Due to the high volume and weight requirements of these devices, the substrates are often very compact and small in size to accommodate the miniaturized design of the device. For example, the CPU packaging substrate of a smartphone may be only a few square centimeters in size, while the substrate size of wearable devices such as smart watches is even smaller.
In contrast, CPU packaging substrates used in large systems such as industrial equipment and telecommunications infrastructure require larger dimensions. These devices often need to process more data and complex tasks, so the substrate requires more space to accommodate more electronic components and complex circuit layouts. For example, a CPU packaging substrate for a factory automation control system may be several times larger than that of a smartphone, or even larger.
Not only that, but some specific applications may require very specific substrate dimensions. For example, some specially shaped substrates may be used in specifically shaped electronic devices or systems to maximize the use of available space. In some cases, the substrate may require custom design to meet specific size and performance requirements.
Therefore, the size of the CPU packaging substrate varies, depending on the specific scenario and device type in which it is used. Whether it is a small portable device or a large industrial system, the CPU packaging substrate plays a vital role in supporting and guaranteeing the performance and functionality of the device.
The Manufacturer Process of CPU Package Substrates.
The manufacturing process of CPU packaging substrate is a precise and complex process involving multiple key steps, each of which is crucial and affects the quality and performance of the final product. The manufacturing process of the CPU packaging substrate will be introduced in detail below:
The first is the substrate preparation stage. At this stage, the manufacturer selects a suitable substrate material, typically fiberglass-reinforced epoxy (FR4). The substrate then goes through pre-treatment processes such as cleaning, drying and cutting to ensure that the surface is smooth and free of impurities so that subsequent processes can proceed smoothly.
Next is layer alignment. In this step, multiple layers of substrates are stacked together, and precision alignment equipment is used to ensure the exact position between the layers for subsequent circuit layout and connections.
Then comes the etching or printing of the lines. In this critical step, the required conductive circuit pattern is formed on the surface of the substrate through photolithography or printing technology. These lines will be the channels connecting the CPU and other electronic components, so their accuracy and quality are critical to the performance of the entire system.
Next comes the drilling of component holes. At this stage, high-precision drilling equipment is used to drill holes into the substrate for mounting electronic components. These holes will be used to solder connecting components and make electrical connections.
This is followed by pad application. In this step, pads are coated on the substrate by printing or spraying methods, which are used to connect electronic components and provide a stable soldering surface. The quality of the pad directly affects the reliability and performance of the welding.
Finally comes component assembly and testing. At this stage, electronic components are precisely mounted onto the substrate and undergo rigorous testing and quality control. This includes functional testing, signal integrity testing, thermal testing, etc. to ensure the normal operation and stable performance of the CPU packaging substrate.
In general, the manufacturing process of CPU packaging substrates involves multiple complex steps and sophisticated technologies, requiring highly specialized equipment and experienced operators. Through careful design and strict control of every link, we can ensure that the final product has excellent quality and reliable performance.
The Application area of CPU Package Substrates.
As a key technology, CPU packaging substrate is widely used in various industries. Its versatility and customizability make it an important component in fields such as consumer electronics, automotive, aerospace, medical devices, telecommunications, and industrial automation.
In the field of consumer electronics, CPU packaging substrates are widely used in various devices, such as smartphones, tablets, smart home devices, and personal computers. They not only provide support and connections for electronic components, but also provide stable power and efficient data transmission for these devices.
In the automotive industry, CPU packaging substrates play a vital role in vehicle electronic systems. They are used in car control systems, in-car entertainment systems, driving assistance systems, etc., to provide support for the intelligence, safety and comfort of cars.
In the aerospace field, CPU packaging substrates are widely used in avionics equipment, spacecraft control systems, communication systems, etc. Their high reliability and radiation resistance enable them to operate stably in extreme environments and ensure the normal operation of aerospace vehicles.
In the field of medical equipment, CPU packaging substrates are used in medical imaging equipment, medical monitoring equipment, surgical auxiliary equipment, etc. They provide high-precision control and data processing capabilities for medical equipment, helping to improve the efficiency and accuracy of medical diagnosis and treatment.
In the field of telecommunications, CPU packaging substrates are used in communication base stations, network equipment, optical fiber transmission equipment, etc. They provide key support for the construction and operation of communication networks and ensure the stability and efficiency of communication services.
In the field of industrial automation, CPU packaging substrates are widely used in factory automation equipment, robotic systems, sensor networks, etc. They provide intelligent and efficient solutions for industrial production and promote the continuous improvement of industrial automation levels.
In general, CPU packaging substrates have a wide range of applications. They play an important role in various industries and promote the continuous development and progress of modern technology.
What are the advantages of CPU Package Substrates?
CPU packaging substrates play an integral role in modern electronic technology and one of their advantages is that they have many advantages over other wiring methods.
First of all, the compact size of the CPU packaging substrate allows a large number of electronic components to be placed in a limited space, making the overall size of the electronic device more compact, thereby satisfying the design trend of modern electronic products for being thin, light and short.
Secondly, the CPU packaging substrate has extremely high reliability. Due to its use of advanced manufacturing processes and high-quality materials, the CPU packaging substrate can withstand work under various environmental conditions, including high temperature, high humidity, vibration, etc., ensuring the long-term stable operation of electronic equipment.
In addition, mass production of CPU packaging substrates is relatively easy, which can significantly reduce production costs and cycles, meeting the needs of mass production, thereby accelerating the launch of electronic products and improving market competitiveness.
CPU packaging substrates can also effectively reduce errors during assembly. Through precise design and automated manufacturing processes, the impact of human factors on assembly quality is reduced, and production efficiency and product quality are improved.
In terms of signal transmission, the CPU packaging substrate can achieve precise layout and optimization of circuits, reducing the possibility of signal interference and improving signal integrity, thereby ensuring the stability and reliability of data transmission.
Finally, the CPU packaging substrate has good thermal properties, which can effectively disperse and conduct the heat generated by the device, maintain a stable operating temperature of the electronic device, extend the service life of the device, and improve performance.
To sum up, CPU packaging substrate has become one of the indispensable key technologies in modern electronic products due to its many advantages such as small size, high reliability, easy mass production, reduced assembly errors, improved signal integrity and enhanced thermal performance. , promoting the continuous development and progress of electronic technology.
FAQ
What is the design software for CPU package substrate?
The design of CPU packaging substrates usually uses professional electronic design automation (EDA) software, such as Altium Designer, Cadence Allegro PCB Designer and Mentor Graphics PADS. These software provide a wealth of functions, including component library management, layout design, circuit routing, signal simulation and design verification, etc.
How to choose a suitable CPU packaging substrate material?
Material selection often depends on application requirements, including factors such as operating temperature range, mechanical strength, dielectric constant, flame retardant properties and cost. Common material options include FR4, polyimide (PI), and metal substrates, each with its own specific pros and cons.
What is the manufacturing process of CPU packaging substrate?
The manufacturing process of CPU packaging substrates involves multiple steps, including substrate preparation, layer alignment, line etching or printing, hole drilling, pad application, component placement and final testing. These steps require a high degree of precision and specialized equipment.
How to conduct reliability testing of CPU packaging substrates?
Reliability testing includes environmental testing, electrical performance testing and reliability life testing. Environmental testing involves temperature cycling, humidity testing and vibration testing to simulate actual operating conditions. Electrical performance testing includes testing parameters such as circuit connectivity, resistance and capacitance. Reliability life testing evaluates the service life of the substrate through accelerated aging testing.
What is the environmental impact of CPU packaging substrates?
Environmental influences on the CPU packaging substrate include factors such as temperature, humidity, vibration, and chemicals. These environmental factors may affect the performance and reliability of the substrate, so these effects need to be taken into account during the design and manufacturing process, and corresponding measures need to be taken for protection and testing.