Low CET PCB manufacturing, We use BT series low shrinkage material or other types high speed and high frequency low shrinkage material production the PCBs.The precision of trace distance is better, and the finished PCB board surface is more flat, which is convenient for component assembly.
Printed Circuit Boards (PCBs) play a vital role in the manufacturing of modern electronic devices. They not only provide support and connections for electronic components, but also implement various functions of the device. With the increasing awareness of environmental protection, Low CET (low odor, low corrosion, low pollution) technology has become an important trend in the field of PCB manufacturing. This article aims to introduce the key contents of Low CET PCB manufacturing and help readers gain a deeper understanding of this environmentally friendly PCB manufacturing technology.
What is low volatility PCB?
Low-volatility PCB is a printed circuit board manufactured using low-volatility materials and processes to reduce the impact on the environment and human health. In traditional PCB manufacturing, some volatile organic compounds (VOCs) and harmful gases may be released into the environment, causing potential risks to the ecosystem and human health. The emergence of low-volatility PCB is to deal with this problem. By using environmentally friendly materials and processes, low-volatile PCBs can effectively reduce the release of volatile organic compounds, thereby reducing adverse effects on the environment and human health.
The manufacturing process of low-volatility PCB pays attention to environmental protection and health and safety. In terms of material selection, materials such as low-volatile resin, environmentally friendly copper foil, and lead-free solder are usually used. These materials not only have good electrical and mechanical properties, but also reduce environmental pollution. In addition, during the manufacturing process, pollutants in the production environment are strictly controlled and effective emission control measures are taken to ensure that the PCBs produced meet environmental standards and customer requirements.
The introduction of low-volatility PCB has brought new development opportunities to the electronics manufacturing industry. Against the backdrop of increasing environmental awareness, more and more manufacturers and customers are paying attention to and choosing low-volatility PCB products. Not only can it meet the environmental protection and health and safety requirements of modern electronic equipment, but it also excels in performance and reliability, providing customers with higher-quality solutions.
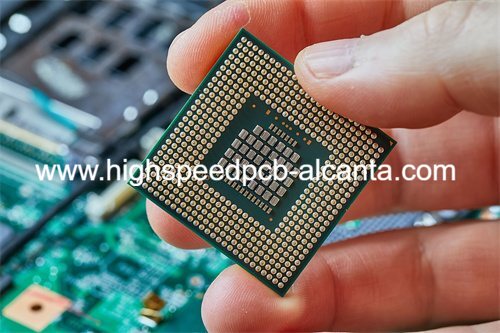
Low CET PCB Manufacturing
In short, the emergence of low-volatility PCB is an important step towards a more environmentally friendly and sustainable development of the electronics manufacturing industry. By using low-volatility PCBs, we can reduce environmental pollution, protect the ecological environment, and make positive contributions to human health and future sustainable development.
How to design low volatility PCB?
Designing a low-volatility PCB is a complex task that requires consideration of multiple factors to ensure it meets environmental and health and safety standards. The following are the main factors to consider when designing a low-volatility PCB:
First, material selection is crucial. The use of low-volatility substrate materials, covering layers, and soldering materials is a primary consideration in designing low-volatility PCBs. These materials should have low volatility, low corrosivity and low toxicity to reduce the impact on the environment and human health.
Secondly, laminate design requires special attention. Reasonable lamination design can reduce the release of volatiles inside the PCB and reduce the emission of volatile organic compounds (VOCs). By selecting appropriate laminate structures and materials, volatile emissions can be effectively reduced.
In addition, wiring and layout are also one of the key factors to consider when designing low-volatility PCBs. Proper routing and layout can reduce heat build-up on the circuit board and reduce the release of volatiles. Try to avoid concentrated layout of high-temperature areas, which can effectively reduce environmental pollution and human health risks.
Using professional PCB design software can bring many benefits. These software often have advanced features and tools that help engineers conduct simulation analysis, optimize designs, and provide detailed manufacturing documentation. Through these software, designers can better control PCB routing, layout and lamination design, thereby minimizing environmental pollution and human health risks.
Minimizing environmental pollution and human health risks is the ultimate goal of designing low-volatility PCBs. In order to achieve this goal, designers should pay close attention to the requirements of environmental standards and regulations, select appropriate materials and processes, use professional PCB design software, and strictly control volatile emissions during the production process. Only in this way can we produce high-quality PCB products that meet environmental protection requirements and health and safety standards.
What is the manufacturing process of low volatility PCB?
The manufacturing process of low-volatility PCBs involves a series of special materials and processes that are significantly different from traditional PCB manufacturing. During the manufacturing process, the focus is on ensuring that the PCB produced not only meets environmental standards, but also meets customer requirements and expectations.
Traditional PCB manufacturing usually uses volatile organic compounds (VOCs), which may release harmful gases during manufacturing and use, posing potential threats to the environment and human health. In contrast, low-volatile PCB manufacturing processes use more environmentally friendly materials and processes to reduce the use and emissions of volatile organic compounds.
When manufacturing these PCBs, special materials such as low-volatile resins, environmentally friendly copper foil, and lead-free solder are required. These materials not only have good electrical and mechanical properties, but also can effectively reduce the release of volatile organic compounds, thereby reducing environmental pollution and human health risks.
In terms of process, low-volatility PCB manufacturing usually adopts strict production control measures, including reducing chemical processing steps, optimizing production processes and equipment, and controlling temperature and humidity in the production environment. These measures help reduce the emission of harmful substances and ensure that the PCB produced meets environmental standards and customer requirements.
In order to ensure the quality and environmental performance of the PCBs produced, manufacturers usually conduct strict quality control and testing. This includes the use of advanced testing equipment and technology to conduct comprehensive inspection and analysis of raw materials and finished products to ensure they comply with relevant environmental standards and customer requirements. At the same time, manufacturers also work closely with customers to understand their needs and expectations, and adjust production processes based on actual conditions to meet customers’ specific requirements.
In general, the manufacturing process of low-volatile PCB pays more attention to environmental protection and health and safety than traditional PCB manufacturing, using more environmentally friendly materials and processes, and ensuring product quality and performance through strict quality control and testing. Through continuous innovation and improvement, low-volatility PCB manufacturing will make an important contribution to the sustainable development of the electronics manufacturing industry.
How much does a low volatility PCB cost?
The manufacturing cost of low-volatility PCBs may be slightly higher than the cost of traditional PCBs, mainly due to the use of more environmentally friendly and high-performance materials and processes in material selection and manufacturing. These materials are typically more expensive and require stricter environmental controls during the manufacturing process, increasing manufacturing costs. However, with the continuous development and maturity of technology and the increasing awareness of environmental protection, the cost of low-volatile PCBs is gradually declining.
First, with the advancement of technology, the special materials and processes required to manufacture low-volatility PCBs are constantly being improved and optimized. The application of new production technologies and processes has improved production efficiency, thus reducing manufacturing costs. For example, the development and application of new environmentally friendly materials and the application of intelligent manufacturing technology will help reduce the cost of low-volatile PCBs.
Secondly, as market competition intensifies, more and more PCB manufacturers are paying attention to low-volatility technology and increasing investment and research and development in related technologies. This has led to the upgrading of production equipment and improvements in manufacturing processes, reducing production costs. At the same time, mass production can also reduce the manufacturing cost of unit products, thereby reducing the overall cost of low-volatile PCBs.
In addition, manufacturers can take a series of cost-saving measures to reduce the cost of low-volatile PCBs. For example, optimize production processes and improve production efficiency; streamline production lines and reduce unnecessary waste of resources; strengthen supply chain management and reduce raw material procurement costs, etc. In addition, working with customers to jointly develop customized solutions suitable for their specific application scenarios can also reduce product costs and improve market competitiveness.
In general, with the continuous advancement of technology and the continuous development of the market, the cost of low-volatility PCBs is gradually decreasing. By continuously optimizing production processes, improving production efficiency and strengthening supply chain management, manufacturers can further reduce the cost of low-volatile PCBs and provide customers with higher-quality, environmentally friendly products and services.

Low CET PCB manufacturing
What are the materials for low-volatility PCBs?
Low-volatility PCB materials are a key factor in ensuring that PCBs reduce volatile organic compounds (VOCs) and harmful gas emissions as much as possible during manufacturing and use. These materials not only need to meet PCB performance and reliability requirements, but also meet environmental standards and customer health and safety needs. Here are some commonly used low-volatility PCB materials:
Environmentally friendly resin
Low-volatility PCBs often use environmentally friendly resins as substrate materials, such as epoxy resin (EP) and polyimide resin (PI). These resins have low volatility and high thermal resistance, making them suitable for applications in a variety of environmental conditions.
Environmentally friendly copper foil
Copper foil commonly used in traditional PCB manufacturing may contain volatile organic compounds, while low-volatile PCB uses environmentally friendly copper foil. This copper foil is usually specially treated to reduce the emission of volatile substances and ensure the stability and reliability of the circuit board.
Lead-free solder
Low-volatility PCBs are often soldered with lead-free solder to avoid harmful substances that may be contained in traditional solder. Lead-free solder not only meets environmental requirements, but also provides good soldering performance and reliability.
Low volatility coating
The material of PCB surface coating is also an important component of low-volatility PCB. These coatings typically use low-volatile resins or environmentally friendly polymer materials to provide protection and insulation and ensure PCB stability and reliability.
Environmentally friendly filling materials
In multi-layer PCB manufacturing, the volatility of filler materials also needs to be considered. Low-volatility PCBs usually use environmentally friendly filling materials, such as environmentally friendly resin or silicone, to ensure the stability and reliability of the entire PCB structure.
The selection and application of these materials enable low-volatility PCBs to meet the environmental protection and health and safety requirements in modern electronic equipment manufacturing, providing users with more reliable and safer products. With the continuous advancement of technology and the improvement of environmental awareness, it is believed that more new low-volatile PCB materials will appear in the future, contributing to the sustainable development of the electronics industry.
Who is making low-volatility PCBs?
In today’s context of increasing emphasis on environmental protection and health and safety, more and more manufacturers are beginning to pay attention to low-volatility PCB technology and actively invest in its manufacturing and research and development. Among them, our company, as a leading company focusing on high-quality, environmentally friendly PCB manufacturing, has rich experience and technology accumulation in the field of low-volatility PCBs.
Advantages of our company
We have a highly skilled and experienced R&D team that constantly pursues innovation and breakthroughs, and continues to lead the trend of technological development in the field of low-volatility PCB manufacturing.
Environmental awareness: As a socially responsible company, we always regard environmental protection as one of our core values. We are committed to finding and using low-volatility, low-corrosive materials and processes to ensure that our products have minimal impact on the environment during production and use.
Quality Assurance: Our company strictly follows international standards and industry norms and has established a complete quality management system. From raw material procurement to production and manufacturing to final product delivery, we have conducted strict inspection and control to ensure that each Low CET PCB has excellent performance and reliability.
Customer customization: We know that each customer’s needs are unique, so we provide flexible customization services and can customize Low CET PCB products according to customers’ specific requirements to meet their personalized needs.
Service system: Customer first is our purpose. We have established a comprehensive customer service system, including professional technical support, timely after-sales service, and continuous communication and feedback mechanisms to ensure that customers are satisfied throughout the entire cooperation process. experience and service.
As a leader in the field of low-volatility PCB manufacturing, our company will continue to work tirelessly to provide customers with more environmentally friendly and reliable PCB solutions, and jointly promote the development of the electronic manufacturing industry in a more sustainable and healthy direction.
What are the 5 qualities of great customer service?
To ensure customer satisfaction and build long-term relationships, providing excellent customer service is crucial. Here are five key qualities:
Communication: Communication plays a vital role in customer service. Clear, timely communication helps customers understand order progress, product features and solutions. By establishing good communication channels with customers, customers’ trust in products and services can be enhanced and the occurrence of misunderstandings and dissatisfaction can be reduced.
Responsiveness: Responding quickly to customer needs and questions is key to maintaining customer satisfaction. Customers expect timely responses and solutions when they encounter problems or have questions. Through timely responses, customer satisfaction and loyalty can be improved while enhancing the company’s competitiveness.
Empathy: It is very important to show empathy during the customer service process. Great customer relationships are built by understanding your customers’ needs, concerns, and pain points, and meeting their expectations with genuine care and support. Empathy can also help customers feel respected and valued, thereby increasing customer loyalty to the company.
Professionalism: Providing professional technical support and advice is an important part of excellent customer service. Customers expect professional guidance and solutions to meet their specific needs and requirements. Through a customer service team with professional knowledge and skills, we can provide customers with high-quality services and enhance customer satisfaction and brand image.
Reliability: Customers want to be able to rely on and trust their suppliers or service providers. Therefore, ensuring product quality and on-time delivery is one of the key attributes of good customer service. By establishing reliable supply chains and production processes, as well as strict quality control and management systems, we can ensure that customers receive consistent high-quality products and services.
Frequently Asked Questions
What measures can be taken to optimize the performance of Low CET PCBs?
To optimize the performance of Low CET PCBs, designers and manufacturers can focus on factors such as material selection, thermal management, and signal integrity. By choosing appropriate materials and implementing efficient design practices, the reliability and functionality of Low CET PCBs can be enhanced.
Are there any limitations or challenges associated with Low CET PCB manufacturing?
While Low CET PCBs offer numerous benefits, there may be challenges related to material availability, compatibility with certain manufacturing processes, and initial investment costs. However, advancements in technology and increased market demand are driving solutions to overcome these challenges.
How can customers ensure the quality of Low CET PCBs from a manufacturer?
Customers can ensure the quality of Low CET PCBs by thoroughly evaluating the manufacturer’s credentials, certifications, and track record. It is important to engage in open communication, request samples or prototypes for testing, and conduct site visits if possible to assess the manufacturing facilities and processes. Additionally, feedback from other customers and reviews can provide valuable insights into the manufacturer’s reputation and reliability.
Can Low CET PCBs meet industry standards and regulations?
Yes, reputable manufacturers of Low CET PCBs ensure that their products comply with industry standards and regulations regarding environmental protection, safety, and quality. These standards may include RoHS (Restriction of Hazardous Substances), REACH (Registration, Evaluation, Authorization and Restriction of Chemicals), and others.