IPC Class III PCB Manufacturer.An IPC Class III PCB Manufacturer specializes in crafting circuit boards that meet the stringent standards set by the IPC (Association Connecting Electronics Industries) for Class III, denoting the highest level of reliability and performance. These manufacturers employ advanced techniques and technologies to ensure their PCBs withstand harsh environments, extreme temperatures, and demanding applications, such as aerospace, medical devices, and military systems. With a meticulous focus on quality assurance and precision engineering, IPC Class III PCB Manufacturers deliver products that exceed industry expectations, guaranteeing optimal functionality and durability for mission-critical electronic systems.
In modern electronic equipment, IPC Class III PCB (Printed Circuit Board) plays a vital role. They are not only the foundation of electronic equipment, but also one of the key factors in ensuring equipment performance, reliability and durability. As a standard for high reliability, IPC Class III PCB design and manufacturing processes strictly follow industry standards to ensure reliable operation in extreme environments. Whether it is aerospace, medical equipment or military equipment, IPC Class III PCBs bear the important responsibility of maintaining stable operation of equipment.
What is IPC Class III PCB?
IPC Class III PCB is a high-reliability printed circuit board that complies with IPC (Electronic Industries Consortium) standards. In the electronics industry, IPC Class III PCB is considered the highest level of PCB with stringent design and manufacturing requirements to ensure its reliability and durability in extreme environments.
These PCBs are designed for a variety of applications that require extremely high reliability, including aerospace, medical equipment, and military equipment. In these fields, equipment often needs to run for a long time and work in harsh environments such as high temperature, low temperature, high humidity, high pressure and strong vibration. Therefore, IPC Class III PCB must be able to maintain stable performance under these extreme conditions to ensure safe operation of equipment and accurate transmission of data.
The IPC Class III standard has detailed requirements for all aspects of PCB. For example, it requires that the design of PCB must take into account environmental factors and take measures to improve anti-interference and corrosion resistance. In addition, the material selection, process flow and quality control of IPC Class III PCBs must also meet strict standards to ensure the reliability and durability of the final product.
In conclusion, IPC Class III PCB is a high-end circuit board that is well designed and manufactured, and they play a vital role in critical application areas. By complying with IPC Class III standards, manufacturers can ensure that their products can perform well under the most demanding conditions, providing users with stable and reliable electronic equipment.
IPC Class III PCB design Reference Guide.
The IPC Class III PCB Design Reference Guide is one of the key resources for designing high-reliability PCBs. Following this guideline ensures products meet the highest standards in the industry while striving for superior performance and long-term stability. The following are key takeaways from the IPC Class III PCB Design Reference Guide:
Place And Route
In IPC Class III PCB design, reasonable layout and routing is crucial. Good layout and wiring can minimize signal interference and electromagnetic interference and improve the stability and reliability of the circuit. To achieve optimal layout and routing, designers should consider factors such as board hierarchy, signal paths, component placement, and wiring methods.
Material Selection
Choosing the appropriate materials is critical for IPC Class III PCBs. High-quality materials provide excellent performance and long-term stability. For example, the use of high-temperature-resistant FR-4 fiberglass composite materials and high-purity copper foil can ensure the reliability of PCBs in extreme environments. In addition, choosing environmentally friendly materials that comply with RoHS standards is also one of the factors that needs to be considered during the design process.
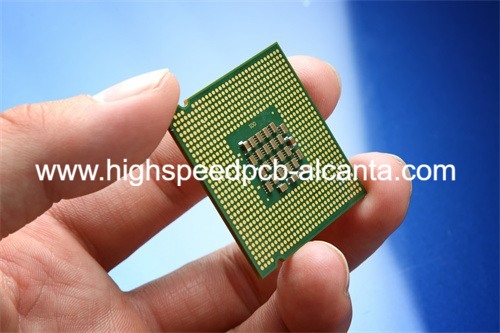
IPC Class III PCB Manufacturer
Electrical Characteristics
The design of IPC Class III PCB requires special attention to electrical characteristics. Including signal integrity, power distribution, ground and power plane design, etc. Through reasonable electrical design, signal distortion and power loss can be minimized and the performance and stability of the circuit can be improved.
Environmental Adaptability
Considering that IPC Class III PCBs are often used in applications in extreme environments, designers need to pay special attention to their environmental adaptability. This includes considerations such as resistance to high temperatures, humidity, corrosion and vibration. By selecting appropriate materials and taking effective protective measures, the long-term stability and reliability of PCBs in harsh environments can be ensured.
In summary, the IPC Class III PCB Design Reference Guide provides key advice and guidance needed to design high-reliability PCBs. Following these guidelines ensures products meet the highest industry standards and deliver stable and reliable performance in extreme environments.
What material is used in IPC Class III PCB?
IPC Class III PCBs typically feature a range of high-quality, carefully selected materials to ensure their stability and reliability in extreme environments. The most common materials include FR-4 fiberglass composite and high-purity copper foil.
First, FR-4 fiberglass composite is a common substrate material with excellent insulation properties and mechanical strength. Made of fiberglass cloth impregnated with epoxy resin, this material has excellent high temperature resistance and chemical stability. The use of FR-4 materials in IPC Class III PCB ensures that the circuit board remains stable in high temperature and humid environments and is not susceptible to environmental factors.
Secondly, high-purity copper foil is one of the preferred materials for making IPC Class III PCB circuit layers. High-purity copper foil has excellent electrical and thermal conductivity, which can ensure stable transmission of circuit signals and good heat dissipation performance. By selecting high-purity copper foil materials, the resistance can be reduced, the signal transmission speed can be increased, and the heat accumulation on the circuit board surface can be reduced, thus enhancing the reliability of IPC Class III PCB in high-voltage, high-frequency and high-power environments.
In addition to these main materials, IPC Class III PCB may also use other auxiliary materials, such as solder paste, solder resist, and surface treatment agents, to meet the needs of specific applications. The selection and application of these materials are subject to strict quality control and standard specifications to ensure that the final PCB product meets the requirements of the IPC Class III standard.
To sum up, the materials used in IPC Class III PCBs have been carefully selected and tested to ensure their stability, reliability and durability in extreme environments. By using high-quality materials, IPC Class III PCB can meet the needs of various high-reliability applications, including aerospace, medical equipment, and military equipment, providing users with reliable electronic solutions.
What size are IPC Class III PCB?
IPC Class III PCBs are sized according to the needs of specific applications, which makes them widely used in a variety of devices. In some cases, IPC Class III PCBs may need to be very small in size to fit into tight equipment spaces. For example, for some portable medical devices or portable communication devices, their PCBs usually need to be as small as possible in order to accommodate more functions and components in a limited space.
On the other hand, IPC Class III PCBs can also have large and complex designs to meet the needs of high-performance and high-reliability equipment. For example, flight control systems or military radar systems in the aerospace field may require larger PCB sizes to accommodate more circuits and components to ensure stable operation and efficient performance of the system.
Whether it is a small and compact design or a large and complex design, IPC Class III PCBs must strictly comply with design specifications and quality standards. During the design process, engineers need to consider size constraints, circuit layout, heat dissipation requirements, and other factors to ensure PCB reliability and stability in extreme environments.
Overall, IPC Class III PCBs come in a wide range of sizes and can be customized according to the requirements of specific applications. Whether small and compact or large and complex, they need to be precision designed and manufactured to ensure their reliability and performance in a variety of environmental and application conditions.
The Manufacturer Process of IPC Class III PCB.
The manufacturing process of IPC Class III PCB is a complex and precise engineering, covering multiple critical steps to ensure high reliability and quality performance of the final product. Below is a detailed description of the manufacturing process:
Design Verification
The first step in manufacturing an IPC Class III PCB is design verification. During this phase, engineers utilize advanced software tools to design board layout, routing, and component mounting. Design verification includes evaluation of electrical simulations, design rule checks, and prototyping to ensure that the design meets specifications and application-specific requirements.
Prototyping
Once the design verification is completed, a prototype of the IPC Class III PCB is made. The key to this stage is to ensure that the prototype accurately reflects the design specifications and can pass rigorous testing. Prototyping often involves rapid prototyping technologies such as rapid prototyping (RP) and rapid circuit board manufacturing (PCB) technology.
Circuit Board Molding
Once the prototype passes testing and is approved, formal prototyping of the board proceeds. This involves selecting an appropriate substrate material (such as FR-4 fiberglass composite) and copper foil, and then using chemical etching or machining methods to form the circuit pattern on the board.
Component Installation
The formed circuit board will enter the component installation stage. At this stage, electronic components (such as chips, resistors, capacitors, etc.) will be precisely mounted onto the circuit board, usually using surface mount technology (SMT) or plug-in assembly technology.
Test
After completing the component installation, the IPC Class III PCB will enter the testing phase. This includes functional testing, electrical testing, temperature cycle testing and environmental suitability testing, etc. The purpose of testing is to ensure that the circuit board can work stably and reliably under various conditions.
Strict quality control is crucial throughout the entire manufacturing process. Every step is strictly monitored and inspected to ensure that IPC Class III PCBs meet the highest standards and can meet customer needs and expectations. Through these carefully designed and strictly executed manufacturing processes, IPC Class III PCB can become a core component of high-reliability electronic equipment.
The Application area of IPC Class III PCB.
IPC Class III PCBs are widely used in industries with extremely high reliability requirements, including aerospace, medical equipment, defense and industrial control systems. In the aerospace field, IPC Class III PCBs undertake the important task of connecting critical avionics equipment. Avionics equipment needs to operate stably in extreme environments (such as high temperature, low temperature, high humidity, high pressure, etc.), and the high reliability and durability of IPC Class III PCB ensures the normal operation of these equipment and provides a solid foundation for flight safety. protection.
In the field of medical equipment, IPC Class III PCB is widely used in various medical diagnostic and treatment equipment. For example, devices such as pacemakers, medical imaging equipment, and surgical robots all rely on high-quality PCBs to ensure their stable performance and reliable operation. The normal operation of medical equipment is directly related to the life safety and health of patients, so the reliability requirements for IPC Class III PCBs are more stringent.
In the field of national defense, IPC Class III PCB is used to manufacture various military electronic equipment, such as communication systems, navigation systems, radars and fire control systems. These devices need to operate reliably in harsh battlefield environments, so the high reliability and durability of IPC Class III PCBs are indispensable. The normal operation of defense equipment is crucial to the success of military operations, so the quality and reliability of PCBs are extremely high.
In the field of industrial control systems, IPC Class III PCB is used to manufacture various industrial automation equipment and control systems, such as PLC (programmable logic controller), sensors, actuators, and monitoring systems. These devices need to operate stably for a long time to ensure normal production of factories and production lines, so the reliability and stability of IPC Class III PCBs are extremely high.
Overall, IPC Class III PCB plays a vital role in these key areas, ensuring the safe operation and stable performance of the equipment. Its high reliability, durability and stability make it the first choice in these industries, providing solid support and guarantee for various critical applications.
What are the advantages of IPC Class III PCB?
High reliability
IPC Class III PCB design follows strict standards and quality control processes, ensuring its high reliability. In critical applications such as aerospace and medical equipment, stable performance is critical. IPC Class III PCBs ensure reliability and durability in a variety of environmental conditions through rigorous testing during their design, material selection, and manufacturing processes.
High Temperature Resistance
IPC Class III PCB uses high-quality materials and workmanship and has excellent high-temperature resistance. In high-temperature environments, ordinary PCBs may experience problems such as looseness, open circuits, or short circuits, while IPC Class III PCBs can operate stably and are not affected by temperature fluctuations. This makes them more suitable for use in high-temperature environments, such as aerospace devices and industrial high-temperature equipment.
Shock And Vibration Resistant
IPC Class III PCB design takes into account the shock and vibration that the equipment may suffer during use, so it has excellent shock and vibration resistance. In fields such as automotive electronics, military equipment, and industrial control systems, equipment is usually subject to severe vibration and impact. IPC Class III PCB can operate stably without being affected by external interference, ensuring the reliability and safety of the equipment.
Suitable For Critical Applications
IPC Class III PCB is widely used in many key areas due to its high reliability, high temperature resistance, impact resistance and vibration resistance. Whether it is aerospace, medical equipment, defense or industrial control systems, IPC Class III PCBs can meet stringent performance requirements and ensure stable operation and long-term reliability of equipment.
FAQ
What is the environmental impact of IPC Class III PCBs?
Manufacturing IPC Class III PCBs involves a series of chemicals and processes that have certain impacts on the environment. However, many manufacturers have taken measures to reduce their impact on the environment, such as using environmentally friendly materials and implementing waste recovery and recycling. In addition, the high reliability and durability of IPC Class III PCB can reduce the scrap rate and energy consumption of equipment, which has a positive impact on reducing resource waste and environmental burden.
How do IPC Class III PCBs differ from other classes of PCBs?
IPC Class III PCBs focus more on high reliability and durability than other classes of PCBs such as Class I and Class II. They are designed for use in applications in extreme environments, such as aerospace and medical equipment, and therefore need to meet more stringent standards during design, manufacturing and testing.
How much does an IPC Class III PCB cost?
Because IPC Class III PCBs require the use of high-quality materials, rigorous manufacturing processes, and complex testing procedures, their manufacturing costs are typically higher. However, given its importance and reliability requirements in critical applications, this additional cost is worth it.
How to perform reliability testing on IPC Class III PCB?
Reliability testing of IPC Class III PCB includes environmental suitability testing, high temperature and high humidity testing, vibration testing and impact testing. These tests are designed to simulate various extreme conditions that a PCB may encounter in actual use to ensure its performance is stable and reliable.
What are the quality standards for IPC Class III PCBs?
IPC Class III PCB quality standards are set by the IPC (Electronic Industries Confederation) and generally cover all aspects of the design, manufacturing, assembly and testing process. These standards are designed to ensure that PCBs meet the highest reliability and durability requirements.