IPC Class III Boards Manufacturer.An IPC Class III Boards Manufacturer specializes in producing circuit boards built to the highest industry standards, ensuring durability and reliability in the most demanding environments. With meticulous attention to detail, cutting-edge technology, and rigorous quality control measures, they craft boards capable of withstanding extreme conditions, including high temperatures, vibrations, and corrosive elements. These manufacturers cater to sectors where precision and resilience are paramount, such as aerospace, defense, medical devices, and automotive industries, providing essential components for critical systems where failure is not an option.
In today’s electronics industry, IPC Class III PCB boards play a vital role, especially in application scenarios that require extremely high reliability and stability. The IPC Class III standard covers strict design, manufacturing and assembly requirements, ensuring PCB board performance reaches the highest level while operating reliably in extreme environments. The strict implementation of these standards makes IPC Class III PCB boards the first choice in fields such as medical equipment, aerospace vehicles, and defense systems, providing reliable basic support for critical applications.
What are IPC Class III Boards?
IPC Class III is a standard in the electronics industry that is used to guide and evaluate the design, manufacturing and assembly of printed circuit boards (PCBs), especially those used in environments that require extremely high reliability and stability. The IPC Class III standard contains strict requirements to ensure that PCB boards can operate reliably under extreme conditions, such as high temperature, high humidity, strong vibration or harsh chemical environments.
IPC Class III Boards require higher quality control and more stringent manufacturing processes than other classes of PCB boards. They are often used in critical applications in the military, aerospace, medical and industrial fields, which have extremely high requirements for the reliability and stability of electronic equipment.
The IPC Class III standard covers all aspects, starting from the design of the PCB board, which needs to take into account various environmental conditions and working requirements to ensure that the performance and stability of the PCB board reach the highest level. During the manufacturing process, each step must be strictly controlled to ensure that each PCB board meets the requirements of the IPC Class III standard. This includes appropriate material selection, precise layer alignment, copper etching, high-precision drilling and soldering, and more.
The application range of IPC Class III Boards is very wide, and they are widely used in various critical applications, such as spacecraft, medical diagnostic equipment, military communication systems and industrial automation equipment. These fields have extremely high requirements on the reliability and stability of PCB boards, so IPC Class III Boards have become one of the indispensable electronic components.
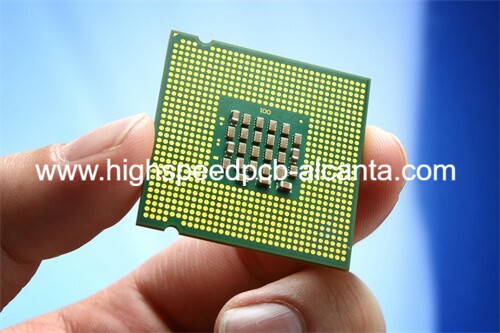
IPC Class III Boards Manufacturer
In short, IPC Class III Boards represent the highest level of PCB board manufacturing. They have excellent performance, stability and reliability, can meet application requirements under various extreme conditions, and provide reliable support and support for electronic equipment in key areas. Assure.
IPC Class III Boards design Reference Guide.
The Design Reference Guide for IPC Class III Boards is designed to help engineers and designers effectively design high-quality PCB boards while meeting the requirements of the IPC Class III standard. This guide covers every aspect, from wiring layout to material selection, from electrical characteristics to thermal management, and aims to provide comprehensive design guidance to ensure that PCB boards can operate reliably in extreme environments.
First of all, in the design of IPC Class III Boards, wiring layout is crucial. A good wiring layout can minimize signal interference and electromagnetic interference and ensure the stability and reliability of signal transmission. Designers need to consider factors such as various signal path lengths, routing patterns, and distributed capacitance and inductance to minimize signal attenuation and latency.
Secondly, material selection is critical to the design of IPC Class III Boards. Designers need to choose high-quality materials that meet the requirements of IPC Class III standards, such as substrate materials with excellent insulation properties and thermal stability, and high-purity copper foil for wires. Correct material selection can ensure that the PCB board has good electrical properties, mechanical strength and high temperature resistance.
In addition, electrical characteristics and thermal management are also key considerations in the design of IPC Class III Boards. Designers need to conduct in-depth analysis of signal integrity to ensure the accuracy and stability of signal transmission. At the same time, the heat of the PCB board must be effectively managed to avoid the impact of local hot spots and thermal stress on electronic components to ensure that the PCB board can maintain stability during long-term high-load operation.
Finally, the IPC Class III Boards Design Reference Guide also includes manufacturing and assembly considerations. Designers need to work closely with manufacturers to ensure that the PCB board manufacturing process meets the requirements of the IPC Class III standard, as well as taking appropriate measures during the assembly process to ensure that each component is installed correctly and soldered well.
In summary, the IPC Class III Boards Design Reference Guide provides comprehensive design guidance to help designers effectively meet the requirements of the IPC Class III standard and design high-quality, high-reliability PCB boards for various critical applications. Reliable electronic support.
What material is used in IPC Class III Boards?
IPC Class III Boards require the use of high-quality, reliable materials to ensure they can maintain stability and reliability under extreme conditions. Here are some key materials commonly used in IPC Class III Boards:
IPC Class III Boards typically use substrate materials with excellent insulation properties and mechanical strength. FR-4 (fiberglass reinforced epoxy) is one of the most commonly used substrate materials. It has good insulation properties, high temperature resistance and chemical resistance, and is suitable for applications in various environmental conditions.
The wires on the circuit board are usually made of copper foil because copper has good electrical conductivity and mechanical strength. For IPC Class III Boards, high-purity copper foil needs to be selected to ensure good electrical conductivity and reliability, especially in high-frequency and high-current applications.
The pad is a key component for connecting components and wires, and is usually made of gold- or silver-plated materials to provide good soldering performance and corrosion resistance. In IPC Class III Boards, the quality and durability of the solder pads are critical as they carry the connections of the components.
Surface coating is used to protect the pads and wires of the PCB board from oxidation and corrosion. Common surface coating materials include organic tin (HASL), nickel gold (ENIG) and gold-tin alloy (ENEPIG). For IPC Class III Boards, high-quality surface coating materials are typically selected to ensure good soldering performance and long-term stability.
Encapsulation materials are used to protect electronic components and provide mechanical support. Common encapsulation materials include epoxy resin, polyimide (PI) and polytetrafluoroethylene (PTFE). In IPC Class III Boards, packaging materials must have excellent high temperature resistance and chemical resistance to ensure component reliability and stability under extreme conditions.
In short, the materials used in IPC Class III Boards must be of high quality, high reliability and durability to meet the strict IPC Class III standard requirements and ensure reliable operation of PCB boards under various extreme conditions. Proper selection and use of these materials is one of the key factors in designing and manufacturing high-quality IPC Class III Boards.
What size are IPC Class III Boards?
IPC Class III Boards can vary in size depending on specific application needs and design requirements. They can cover a wide range of sizes from tiny electronic devices to large industrial systems. Here are some common considerations regarding IPC Class III Boards sizing:
The size of IPC Class III Boards is usually affected by their application areas and functional requirements. For example, IPC Class III Boards used in portable electronic devices may be very small and lightweight to fit the compact size of the device, while IPC Class III Boards used in industrial automation systems or aerospace vehicles may be larger.
The size of IPC Class III Boards is also affected by device density. High-density electronic devices require more space for layout and connections, so a larger PCB board size may be required to accommodate these devices and ensure good thermal and electrical performance.
The dimensions of IPC Class III Boards may be affected by assembly and repair requirements. Designers may choose a larger PCB board size to make it easier to handle and install components during assembly, as well as to facilitate later repairs and upgrades.
The size of IPC Class III Boards is also limited by mechanical constraints such as installation space, connector size, and housing size. Designers need to ensure that the PCB board is sized to accommodate the required mechanical constraints and to integrate and fit effectively with other components.
In summary, the size of IPC Class III Boards is a flexible parameter that can be determined based on specific application needs and design considerations. Whether it is a small micro PCB board or a large industrial-grade PCB board, designers must consider various factors to ensure that the final PCB board size can meet the performance, reliability and assembly requirements to achieve optimized design and manufacturing.
The Manufacturer Process of IPC Class III Boards.
The manufacturing process of IPC Class III PCB boards is a strictly controlled and complex process, designed to ensure that each step meets the requirements of the IPC Class III standard to ensure the reliability and stability of PCB boards in various extreme environments. The following are the key steps in the IPC Class III PCB board manufacturing process:
The first step in the manufacturing process is substrate preparation. This includes inspecting and cleaning the substrate to remove surface contaminants and ensuring that the substrate meets specified size and flatness requirements. The quality and flatness of the substrate are critical to the subsequent manufacturing process.
Layer alignment is the process of accurately aligning graphics and circuit lines on different levels. Layer alignment is critical during the manufacturing process of IPC Class III PCB boards, as any slight deviation may affect the performance and reliability of the board.
Copper etching is the process of removing unwanted copper foil from the surface of a substrate. This is achieved by immersing the substrate in a chemical solution or using mechanical processing methods. During the IPC Class III PCB board manufacturing process, the accuracy and consistency of copper etching must be ensured to ensure the accuracy and stability of the circuit traces.
Drilling is used to create holes in the PCB board for mounting components and wires between connecting layers. During the manufacturing process of IPC Class III PCB boards, drilling must be performed with high precision and consistency to ensure accurate installation and connection of components.
Pad coating is the application of a protective coating on the PCB board to prevent copper corrosion and improve soldering quality. For IPC Class III PCB boards, pad coating must meet strict quality control standards to ensure soldering quality and reliability.
Component mounting is the process of accurately mounting electronic components onto a PCB board. During the manufacturing process of IPC Class III PCB boards, the accurate location and correct positioning of components must be ensured to ensure the performance and reliability of the circuit board.
Soldering is the process of connecting electronic components to a PCB board. During the manufacturing process of IPC Class III PCB boards, high-quality welding processes and materials must be used to ensure the firmness and stability of the welding connections.
In general, the manufacturing process of IPC Class III PCB boards requires strict quality control and high-precision operations to ensure that each PCB board meets the requirements of the IPC Class III standard. Manufacturers must strictly follow standard operating procedures and conduct effective quality management to ensure the highest level of performance and reliability of the final product.
The Application area of IPC Class III Boards.
IPC Class III PCB boards play an important role in various critical fields, and their high reliability and stability make them the preferred electronic components in military, aerospace, medical and industrial fields. The following are the applications of IPC Class III PCB boards in various fields:
In the military field, IPC Class III PCB boards are widely used in various key systems and equipment, such as military communication equipment, radar systems, navigation equipment, and weapon systems. These systems have extremely high requirements for performance stability and reliability, so IPC Class III PCB boards are required to ensure reliable operation in harsh environments and extreme conditions.
In the aerospace field, IPC Class III PCB boards are used in aerospace equipment such as spacecraft, satellites, aircraft and drones. These devices need to work under extreme conditions such as high altitude, high speed and high temperature, so the reliability and stability requirements of PCB boards are particularly strict.
In the medical field, IPC Class III PCB boards are used in critical medical equipment such as medical diagnostic equipment, medical monitoring equipment, and treatment equipment. These devices have extremely high requirements for accuracy and reliability, because they directly affect the results of medical diagnosis and treatment, so IPC Class III PCB boards are needed to ensure the stability and accuracy of the equipment.
In the industrial field, IPC Class III PCB boards are used in key industrial equipment such as industrial automation equipment, control systems, power systems, and mechanical equipment. These devices have extremely high requirements for stability and reliability, because they directly affect the efficiency and safety of industrial production, so IPC Class III PCB boards are needed to ensure reliable operation of the equipment.
To sum up, IPC Class III PCB boards are widely used in military, aerospace, medical and industrial fields, and their high reliability and stability make them the preferred electronic component for various critical applications. By adopting IPC Class III PCB boards, equipment in these fields can operate stably under extreme conditions and ensure the reliability and stability of their performance and functionality.
What are the advantages of IPC Class III Boards?
IPC Class III PCB boards offer numerous advantages that make them the preferred electronic component for a variety of critical applications. The following are the main advantages of IPC Class III PCB boards:
IPC Class III PCB boards have been rigorously designed, manufactured and tested to ensure excellent reliability. Each manufacturing step follows strict quality control standards to ensure that the final product meets the requirements of IPC Class III standards and can maintain stability during long-term use and harsh environments.
IPC Class III PCB boards have good stability and can maintain consistent performance under various environmental conditions. Whether it is high temperature, low temperature, high humidity or low humidity environment, IPC Class III PCB board can operate stably without affecting its performance and functions due to environmental changes.
IPC Class III PCB board has excellent anti-interference ability and can resist the influence of external interference and noise. Through careful design and appropriate shielding measures, IPC Class III PCB boards can ensure the stability and reliability of signal transmission, maintaining good performance even in noisy environments.
IPC Class III PCB boards have a long service life and are able to maintain stability and reliability over a long period of time. Using high-quality materials and strict manufacturing processes, IPC Class III PCB boards can withstand the test of long-term operation and repeated use, providing long-lasting support for critical applications.
IPC Class III PCB boards can operate reliably in harsh conditions such as extreme temperatures, humidity, and vibration. Whether in high-temperature desert areas, cold polar environments or high-altitude mountain areas, IPC Class III PCB boards can work stably and provide reliable support for critical applications.
To sum up, IPC Class III PCB board has many advantages such as high reliability, stability, anti-interference ability and long service life, making it an ideal choice for various critical applications. By using IPC Class III PCB boards, users can ensure that their equipment operates stably under various harsh conditions, providing reliable support and protection for critical applications.
FAQ
What is the difference between IPC Class III PCB boards and other classes of PCB boards?
IPC Class III PCB boards require higher quality control and stricter manufacturing standards than other classes of PCB boards. They are designed for critical applications in extreme environments, such as military, aerospace and medical fields. Compared with other classes of PCB boards, IPC Class III PCB boards have higher reliability, stability and anti-interference capabilities.
What are the characteristics of the manufacturing process of IPC Class III PCB boards?
The manufacturing process of IPC Class III PCB boards requires strict control of every step, including substrate preparation, layer alignment, copper etching, drilling, pad coating, component mounting and soldering, etc. Manufacturers must follow strict quality control standards to ensure that each PCB board meets the requirements of the IPC Class III standard.
What are the applicable fields of IPC Class III PCB boards?
IPC Class III PCB boards are widely used in military, aerospace, medical and industrial fields. These fields have extremely high requirements on the reliability and stability of electronic equipment. For example, in spacecraft, medical diagnostic equipment, and military communications systems, IPC Class III PCB boards carry critical functions and must provide excellent performance and reliability.
What are the advantages of IPC Class III PCB boards?
IPC Class III PCB boards offer many advantages, including high reliability, stability, interference immunity, and long service life. They are able to operate reliably in harsh conditions such as extreme temperatures, humidity and vibration, providing reliable support for critical applications.