Integrated Circuit Substrate Manufacturer.An Integrated Circuit Substrate Manufacturer specializes in producing high-quality substrates essential for semiconductor devices. These substrates provide critical electrical connections, thermal management, and mechanical support for integrated circuits. Utilizing advanced materials and precision manufacturing processes, the manufacturer ensures reliable performance and durability of electronic components across various applications, from consumer electronics to industrial equipment. Their expertise in substrate design and production is vital for the ongoing innovation and advancement in the electronics industry.
Integrated circuit (IC) substrates are fundamental components in semiconductor technology, providing the platform for mounting and interconnecting integrated circuits within electronic devices. These substrates are crucial for ensuring reliable electrical performance and efficient heat dissipation in various applications. This article explores the properties, structure, materials, manufacturing processes, applications, advantages, and frequently asked questions (FAQs) related to integrated circuit substrates.
Structure of Integrated Circuit Substrates
Integrated circuit substrates are meticulously engineered to provide optimal performance:
The substrate is typically made from high-performance materials such as silicon, ceramic (e.g., alumina or aluminum nitride), or organic substrates (e.g., FR-4). The choice depends on thermal conductivity, electrical properties, and mechanical strength.
Metal layers, usually copper, are patterned into interconnects and wiring to establish electrical pathways between components.
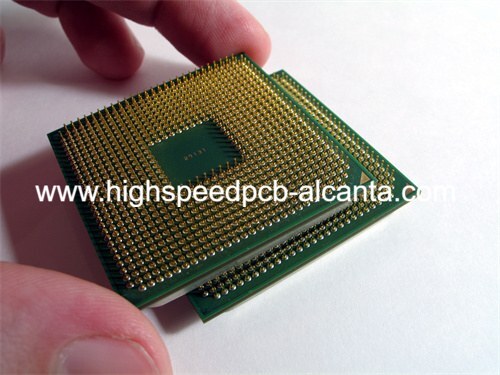
Integrated Circuit Substrate Manufacturer
Insulating materials, such as silicon dioxide or polyimide, are placed between conductive layers to prevent short circuits and ensure signal integrity.
Vertical interconnects that pass through the substrate to connect front and backside layers, enabling three-dimensional (3D) integration and compact designs.
Areas on the substrate surface for attaching ICs using wire bonding or flip chip technology, facilitating electrical connections.
A protective layer over conductive traces to prevent solder bridges during assembly and ensure reliability.
Materials Used in Integrated Circuit Substrates
Key materials used in integrated circuit substrates include:
Silicon, ceramic (alumina or aluminum nitride), or organic materials (FR-4) with tailored properties for thermal management and electrical performance.
Copper or other metals for wiring and interconnects due to their high conductivity and reliability.
Insulating layers like silicon dioxide or polyimide with low dielectric constants to minimize signal loss.
Protective coatings (e.g., silicon nitride or silicon oxide) to shield the IC and substrate from external contaminants and moisture.
Coatings such as gold plating (ENIG) or solder mask (OSP) to enhance solderability and protect exposed metal surfaces.
Manufacturing Process of Integrated Circuit Substrates
The manufacturing process of integrated circuit substrates involves several precise steps:
Starting with a base material, typically silicon or ceramic, prepared through cutting, polishing, and cleaning.
Thin film deposition techniques (e.g., chemical vapor deposition or physical vapor deposition) are used to apply conductive and dielectric layers onto the substrate.
Photolithography and etching processes are used to define the circuit patterns and interconnects on the substrate.
Drilling or etching processes are employed to create vias and TSVs for vertical interconnects between layers.
Deposition of metal layers (e.g., copper) onto the substrate surface and into vias to establish electrical connections.
Attachment of ICs using wire bonding or flip chip technology, followed by encapsulation with molding compounds or protective coatings.
Comprehensive testing for electrical functionality, reliability, and adherence to specifications.
Applications of Integrated Circuit Substrates
Integrated circuit substrates are integral to various applications, including:
Found in microprocessors, memory chips, and logic devices for computing and digital electronics.
Used in smartphones, tablets, and wearables for compact, high-performance electronic devices.
Deployed in vehicle control systems, infotainment, and advanced driver-assistance systems (ADAS).
Essential for network equipment, routers, and communication devices requiring high-speed data processing.
Utilized in industrial automation, robotics, and control systems for manufacturing and process control.
Advantages of Integrated Circuit Substrates
Integrated circuit substrates offer numerous advantages:
Enable compact designs and high-density integration of components.
Provide reliable electrical connectivity and signal integrity for complex electronic functions.
Effective heat dissipation through substrate materials and design features.
Robust construction and testing ensure long-term performance in demanding environments.
Support for various IC types, configurations, and application requirements.
FAQ
How do integrated circuit substrates facilitate miniaturization in electronic devices?
Integrated circuit substrates enable compact designs by integrating multiple ICs and components into a single substrate, reducing overall size and enhancing functionality.
What are the key differences between ceramic and silicon-based integrated circuit substrates?
Ceramic substrates (e.g., alumina or aluminum nitride) offer superior thermal conductivity and mechanical strength, while silicon substrates are advantageous for their compatibility with semiconductor processes and integrated circuit integration.
In which industries are integrated circuit substrates most commonly used?
Integrated circuit substrates are widely used in microelectronics, consumer electronics, automotive electronics, telecommunications, and industrial automation industries for their critical role in electronic device functionality and performance.
How are integrated circuit substrates tested to ensure reliability?
Integrated circuit substrates undergo rigorous testing processes, including electrical testing, thermal cycling, and reliability testing, to verify functionality, performance under stress conditions, and adherence to industry standards.