High Speed Mixed Dielectric PCB Manufacturing.High Speed Mixed Dielectric PCB Manufacturing involves the production of printed circuit boards using multiple dielectric materials to optimize electrical performance. This process is crucial for high-frequency applications, ensuring signal integrity and minimizing losses. Advanced techniques and materials are utilized to achieve superior speed and reliability, making it essential for cutting-edge technologies in telecommunications, aerospace, and computing.
In today’s world of electronic engineering, high-speed mixed media PCB manufacturing plays a vital role, becoming the fundamental backbone of almost all electronic devices. High-speed mixed media PCBs not only provide connections between electronic components, but also carry key functions such as signal transmission and power distribution. Understanding its design, manufacturing and cost is crucial for engineers and electronics enthusiasts, not only to help improve circuit performance but also to optimize manufacturing processes and reduce costs.
What is a high-speed mixed media PCB?
As a key component in the field of electronic engineering, high-speed mixed media PCB (Printed Circuit Board) plays an indispensable role. It is a sophisticated electronic device designed and manufactured to meet high-speed signal transmission and mixed media requirements.
First, let’s explain the basic concepts of high-speed mixed media PCB. High-speed mixed media PCB is a circuit board that provides mechanical support and electrical connections for electronic components by etching or “printing” conductive paths on the board. Compared with traditional single-layer or double-layer PCB, high-speed mixed media PCB has higher signal transmission speed and better anti-interference performance. This performance is due to the use of special materials and processes that allow it to perform well in high-frequency environments.
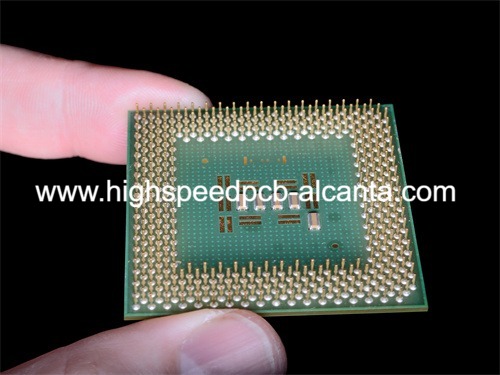
High Speed Mixed Dielectric PCB Manufacturing
In high-speed mixed media PCB, common materials include a mixture of high-frequency media and ordinary media. This hybrid media design can reduce manufacturing costs while ensuring signal transmission speed. In addition, high-speed mixed media PCBs often use fine line widths and spacing, as well as special layer stacking designs to ensure that the circuit board maintains stability and reliability during high-speed signal transmission.
The manufacturing process of high-speed mixed-media PCBs involves several key steps, including material selection, design layout, layer stacking, circuit pattern design, copper foil etching, drilling, etc. These steps require highly sophisticated equipment and process control to ensure the final product meets design requirements.
Overall, high-speed mixed media PCBs are an integral part of modern electronic equipment, and their design and manufacturing require highly specialized knowledge and technology. By understanding the basic concepts and manufacturing process of high-speed mixed media PCB, we can better understand its importance in electronic engineering and how to design and manufacture high-quality electronic products.
How to design high-speed mixed media PCB?
Designing high-speed mixed-media PCBs is a delicate and complex task that requires engineers to make careful considerations and decisions in multiple key areas. The main steps of this process are detailed below.
First, the starting point for design is schematic capture. At this stage, engineers convert the circuit design into a digital schematic diagram to clarify the connection relationships and signal transmission paths between various components. The accuracy and completeness of this step is critical to the subsequent design process, as any errors or omissions can lead to instability or performance issues in the final product.
Next is component placement. Engineers place various electronic components, including processors, memories, sensors, etc., in the PCB layout software based on the circuit schematic diagram. At this stage, the interaction between components and their connection to other components and external interfaces need to be considered to maximize signal transmission and circuit performance.
Routing is another critical step in the design process. At this stage, engineers connect the designed components to form a complete circuit path. This involves not only path selection and length matching of signal lines, but also considerations such as power consumption and thermal management, signal integrity, and electromagnetic compatibility. Through reasonable wiring design, signal interference and timing problems can be minimized and the stability and reliability of the circuit can be improved.
Finally, there’s the layout. At this stage, engineers place the routed circuits on the PCB board and perform final physical layout optimization. This involves considering factors such as PCB board size and shape, power supply and ground trace distribution, thermal design, and the location of external interfaces. Through reasonable layout design, the stability, manufacturability and maintainability of the PCB board can be ensured, and electromagnetic interference and signal loss can be minimized.
To sum up, designing a high-speed mixed-media PCB is a complex and meticulous task that requires engineers to make careful considerations and decisions in many aspects such as schematic capture, component placement, wiring, and layout. Only through rigorous processes and professional technology can high-speed mixed-media PCBs with excellent performance, stability and reliability be designed.
What does the high-speed mixed media PCB manufacturing process look like?
The high-speed mixed-media PCB manufacturing process is a sophisticated and complex process consisting of multiple critical steps, each of which is critical and directly affects the performance and reliability of the final product.
First, the first step in manufacturing high-speed mixed-media PCBs is substrate selection. Substrate selection is critical to PCB performance. Common substrate materials include FR-4, Rogers, and other high-frequency materials. Different applications require different types of substrates to meet their performance requirements.
Next comes layering. During the lamination process, it is important to select the appropriate layer thickness and sequence to ensure the signal integrity and electromagnetic compatibility of the PCB. In high-speed circuit design, stacking also requires consideration of impedance control and signal transmission matching.
Copper patterning is the next critical step in the manufacturing process. This involves transferring a designed conductor pattern to a substrate surface and using chemical etching or mechanical cutting to remove unwanted copper to create conductive paths.
Drilling is done to create connection holes in the PCB for mounting components and wires between connection layers. In the high-speed mixed-media PCB manufacturing process, the location, diameter and quality of drill holes must be strictly controlled to ensure the accuracy and flatness of the hole diameter.
This is followed by copper plating. In this step, copper is deposited on the wire patterns and connection holes through chemical methods or electroplating, increasing their conductive properties and improving the reliability and corrosion resistance of the PCB.
The last critical step is etching. In this step, chemical methods are used to remove the copper covering the copper pattern, leaving the designed conductor pattern and connection holes. This ensures that there are only required conductive paths on the PCB, reducing unnecessary electromagnetic interference.
Through these key steps, the high-speed mixed-media PCB manufacturing process transforms the substrate into a fully functional, assembly-ready PCB that meets the high-speed signal transmission and stability requirements of modern electronic devices.
How to make high-speed mixed-media PCBs?
Manufacturing high-speed mixed-media PCBs requires a series of precise and meticulous operations to ensure the quality and reliability of the final product are up to par. The following are the main stages of the manufacturing process:
The first step in manufacturing a high-speed mixed-media PCB is design. Based on circuit needs and performance requirements, the design team uses professional software to draw circuit schematics and convert them into physical layouts. During the design phase, key factors such as signal integrity, electromagnetic compatibility, and thermal management need to be considered to ensure that the final PCB performs as expected.
Once the design is complete, the substrate needs to be prepared. Normally, substrate selection mainly considers characteristics such as dielectric constant, dielectric loss, and mechanical strength. In the preparation stage, the substrate undergoes cleaning, cutting and surface treatment to ensure adhesion and flatness of the copper layer.
Copper deposition is one of the critical steps in the process of manufacturing high-speed mixed-media PCBs. A conductive copper layer is formed on the surface of the substrate through chemical methods or electroplating techniques to form the wires and connections of the circuit. The deposited copper layer must have a certain thickness and uniformity to ensure the conductivity and stability of the circuit.
After the copper layer is formed, next comes routing and layout. This stage involves placing circuit components on the PCB surface and connecting them using wires to establish the circuit path. The wiring process needs to consider factors such as signal transmission speed, signal integrity, and electromagnetic interference to ensure reliable transmission of high-speed signals.
The final stage of manufacturing high-speed mixed-media PCBs is final inspection. At this stage, the PCB undergoes strict quality control and inspection, including visual inspection, dimensional measurement, electrical testing, etc. Through these inspections, it is ensured that the PCB complies with the design specifications and meets the customer’s requirements.
Each manufacturing stage has a significant impact on the quality and reliability of the finished product. Only through careful design and precise operation can high-quality, high-speed mixed-media PCBs be produced that meet the performance and reliability requirements of modern electronic equipment.
What does the high-speed mixed media PCB manufacturing process look like?
The manufacturing process of high-speed mixed-media PCBs is a sophisticated and complex process involving multiple critical steps, each of which has a significant impact on the quality and performance of the final product.
First, the manufacturing process begins with substrate selection. Choosing the right substrate material for a specific application is critical. Common substrate materials include fiberglass reinforced epoxy (FR-4) and polytetrafluoroethylene (PTFE). The physical properties, dielectric constant and thermal properties of the substrate directly affect the performance of the final PCB.
Next comes layering. For multi-layer PCBs, the lamination process is essential. This involves stacking multiple single-layer boards on top of each other, with pre-riveted perforations ensuring inter-layer connections. The correct layup is crucial for subsequent process steps.
Copper pattern making is the next critical step. This involves the process of forming conductive paths on the surface of a substrate. This is usually done by coating a layer of copper on the surface of the substrate and then using photolithography techniques and chemical etching to define the desired conductive pattern.
Next comes drilling. This step is used to drill holes in the PCB for subsequent component installation and interconnection. High-speed mixed-media PCBs often require very precise hole locations and sizes, so the drilling process requires a high degree of control and precision.
Copper plating is another important step in the manufacturing process. This involves electroplating a thin layer of copper over the copper pattern to enhance conductivity and protect the conductive pattern from corrosion.
Finally comes the etching. This step removes unwanted copper material through chemical etching, leaving only the desired conductive pattern. The accuracy and control of etching directly affects the quality and performance of the final PCB.
To sum up, the manufacturing process of high-speed mixed media PCB is a precise and complex process that requires strict control and high technical requirements. Through the precise execution of the above key steps, a fully functional and highly reliable PCB product can finally be obtained to meet the needs of various high-performance electronic devices.
How to make high-speed mixed-media PCBs?
Manufacturing high-speed mixed-media PCBs is a complex process that requires precise and meticulous operations. From the design phase to final inspection, every step is critical to the quality and reliability of the final product.
First, during the design phase, engineers need to convert the circuit schematic into a PCB layout. This needs to take into account the functional requirements of the circuit, the signal transmission rate, and the requirement for high-speed hybrid media. Through professional PCB design software, engineers can perform component placement, routing and stack-up design to maximize circuit performance.
Once the design is complete, the next step is substrate preparation. This involves selecting an appropriate substrate material and coating its surface with a thin film for copper deposition in a subsequent step.
Copper deposition is one of the key steps in the manufacturing process. At this stage, the substrate is immersed in a solution containing copper ions, and then through an electrochemical process, copper ions are deposited on the surface of the substrate to form conductive paths and connections.
Next comes patterning, which uses photolithography to transfer designed conductive paths and connections to the copper-covered substrate surface. This process involves applying a photosensitive adhesive to the surface of a substrate and then exposing the adhesive layer to specific areas by exposing a light source so that unwanted copper can be removed during a subsequent etching process.
Etching is the process of removing unwanted copper from the surface of a substrate. By immersing the substrate in an etching solution, the solution dissolves the copper exposed to the photosensitive adhesive, creating designed conductive paths and connections.
Finally, a final inspection is performed. This includes using microscopes and test equipment to check that the traces, apertures and other key features on the PCB meet design requirements. Only after passing strict inspection can the PCB be considered a qualified product and can enter the subsequent assembly and testing stages.
Overall, manufacturing high-speed mixed-media PCBs requires deep expertise and extensive experience. Each step must be executed precisely to ensure the final product has excellent performance and reliability to meet the high-speed data transmission and complex functionality requirements of modern electronic devices.
How much does a high speed mixed media PCB cost?
The cost of high-speed mixed-media PCBs is a complex and dynamic topic, affected by many factors. First of all, size is one of the important factors that determine the cost. Larger PCB boards require more materials and processing time, and therefore are generally more expensive. In contrast, small PCBs usually cost less.
Secondly, PCB complexity also has a significant impact on cost. Complex circuit designs, high-density wiring, and multi-layer board construction all increase manufacturing costs. In high-speed mixed media PCB manufacturing, special materials and processes are required to meet the requirements of high-speed signal transmission, which will also increase costs.
Material selection is another key factor. High-speed mixed-media PCBs typically require the use of high-quality substrate materials, premium copper foil, and advanced surface treatment techniques to ensure signal integrity and reliability. The cost of these materials is higher than the standard materials used in ordinary PCB manufacturing, thus increasing the overall cost.
Finally, production quantity also affects costs. Generally speaking, high-volume production can reduce the cost per PCB because the production line setup costs can be spread over more boards. On the contrary, the cost of small batch production is higher because the cost of setting up the production line accounts for a larger proportion.
Therefore, understanding these cost drivers is critical to budgeting and optimizing production costs. During the design phase, engineers need to weigh a variety of factors, including performance needs, budget constraints, and timelines. By optimizing design, material selection, and production strategies, the cost of high-speed mixed-media PCBs can be minimized while ensuring that project requirements and standards are met.
What material is PCB made of?
PCB is an indispensable key component in modern electronic engineering, and its constituent materials are crucial to circuit performance and reliability. Typically, PCBs are composed of several key materials, including substrate materials, conductive path materials, and insulation protection materials.
First, substrate material plays an important role in PCB manufacturing. One of the most common substrate materials is fiberglass reinforced epoxy (FR-4). This material has excellent mechanical properties and heat resistance, making it suitable for most applications. FR-4 substrates generally have higher electrical properties and chemical stability, making them one of the preferred choices for manufacturers.
Second, conductive paths form the connections between electronic components on the PCB. Copper is the most commonly used conductive material, favored for its excellent conductive properties and cost-effectiveness. During the PCB manufacturing process, the copper layer forms a conductive path through processes such as etching or copper plating to achieve circuit connection and conduction.
Finally, the insulating protective material plays the role of insulating and protecting the circuit on the PCB. Solder film is one of the most common insulating protective materials. Its function is to cover the PCB surface to prevent poor contact or short circuit between the conductive path and the external environment. Solder film usually has excellent heat resistance and chemical corrosion resistance, ensuring the stability and reliability of PCB under various working conditions.
In addition to traditional materials, advanced materials such as flexible substrates and metal substrates also play an important role in specific applications. Flexible substrates are made of flexible materials and are suitable for applications that require bending or folding, such as portable and wearable devices. Metal substrates have excellent heat dissipation properties and are suitable for high-power and high-temperature applications such as automotive electronics and industrial control systems.
In summary, PCB material selection is critical to circuit performance and reliability. By rationally selecting substrate materials, conductive path materials, and insulation protection materials, PCBs can be ensured to have excellent performance and stability in various application scenarios.
Who makes PCBs?
In modern electronic engineering, suppliers that manufacture high-speed mixed-media PCBs are crucial. These suppliers not only provide critical manufacturing services, but also assume responsibility for ensuring product quality and reliability. In this area, our company plays an important role and is committed to becoming a trusted partner for our customers.
As a leading PCB manufacturer, we have advanced manufacturing equipment and technology, as well as an experienced engineering team, to meet our customers’ various needs. Whether it is a simple single-layer PCB or a complex multi-layer PCB, we can provide high-quality, high-performance solutions.
Our manufacturing process strictly follows international standards and undergoes strict quality control and inspection from raw material procurement to final product delivery. We use advanced automation equipment and precise processes to achieve high efficiency and fast delivery while ensuring product quality.
In addition to technical strength, we also focus on customer service and communication. Our team always focuses on customer needs, provides personalized solutions, and responds to customer feedback and requirements in a timely manner. Our goal is to establish a long-term and stable cooperative relationship and achieve a win-win situation together.
Overall, as a supplier of manufacturing high-speed mixed media PCBs, we are committed to providing customers with quality products and services, constantly innovating and improving, and growing together with our customers. We look forward to cooperating with you to create a better future together.
What are the 5 qualities of great customer service?
Excellent customer service is a core component of any successful business, it is more than just a service, it is an expression of attitude and values. Here are five key attributes of great customer service, which together form the foundation for satisfying customers and maintaining long-term relationships.
The first is responsiveness. In a highly competitive market environment, it is crucial to respond promptly and effectively to customer needs and issues. A responsive customer service team can promptly handle customer inquiries, complaints or suggestions, thereby enhancing customer trust and satisfaction.
Second is the ability to empathize. The customer service team should have a certain amount of empathy and be able to understand their needs and feelings from the customer’s perspective. By listening carefully to your customers’ opinions and feedback and doing your best to meet their expectations, you can build closer customer relationships and increase customer loyalty.
Reliability is another important trait. Customers want to be able to trust the partners they choose, and they expect them to consistently deliver on their promises and ensure the quality and effectiveness of their services. Therefore, a trustworthy customer service team must treat customers with a reliable attitude and strictly abide by their commitments to ensure that customers receive stable support and assistance during the cooperation process.
Clear and transparent communication is the cornerstone of good customer relationships. Customers hope to obtain clear and concise information during communication with suppliers or service providers, and understand key information such as service content, price, and delivery time. Therefore, customer service teams need to maintain communication transparency and convey important information in a timely manner to avoid misunderstandings or dissatisfaction.
Finally, problem-solving ability is one of the important criteria for judging customer service quality. Customers may encounter various problems or difficulties when using products or services, and an excellent customer service team should be able to solve these problems quickly and proactively to ensure customer satisfaction and experience. By proactively resolving issues, customer service teams can build a positive corporate image, enhance brand reputation, and foster the development of long-term customer relationships.
To sum up, high-quality customer service is not only a service standard, but also a reflection of corporate culture and core competitiveness. By maintaining good responsiveness, empathy, reliability, communication and problem-solving skills, companies can win the trust and loyalty of customers and achieve sustained and healthy development.
Frequently Asked Questions
What measures can be taken to ensure the quality and reliability of high-speed mixed dielectric PCBs?
Ensuring the quality and reliability of high-speed mixed dielectric PCBs involves comprehensive testing, stringent quality control processes, and adherence to industry standards. Key measures include thorough design verification, in-process inspections, electrical testing (such as continuity, impedance, and signal integrity testing), reliability testing (e.g., thermal cycling, vibration testing), and ongoing monitoring of manufacturing processes to detect and address any deviations or defects promptly. Collaborating with experienced PCB manufacturers and utilizing certified materials further enhances product quality and reliability.
How does the choice of substrate material impact the performance of high-speed mixed dielectric PCBs?
The choice of substrate material significantly influences the performance and characteristics of high-speed mixed dielectric PCBs. Factors such as dielectric constant, dissipation factor, thermal conductivity, and mechanical properties directly affect signal integrity, thermal management, and overall reliability. Selecting an appropriate substrate material, such as high-frequency laminates optimized for signal integrity or thermally conductive substrates for heat dissipation, is crucial for meeting the requirements of specific high-speed applications.
What are the advantages of using high-speed mixed dielectric PCBs?
High-speed mixed dielectric PCBs offer several advantages, including reduced signal loss, improved signal integrity, and better impedance control. These characteristics are crucial for applications requiring high-frequency operation and reliable data transmission.
How do I choose the right materials for high-speed mixed dielectric PCBs?
Selecting the appropriate materials for high-speed mixed dielectric PCBs involves considering factors such as dielectric constant, dissipation factor, and thermal properties. Materials with low dielectric constants and low loss tangents are preferred for high-speed applications to minimize signal distortion and maintain signal integrity.