High Frequency package Substrate supplier, The package Substrate will be made with Rogers materials or other high frequency materials. we also make the package Substrate with high speed materials.
High-frequency packaging substrates are fundamental and indispensable elements in contemporary high-frequency electronics. They form the foundation for hosting advanced electronic components and ensuring stable support and signal propagation in high-frequency settings. Understanding the definition and importance of high-frequency packaging substrates is crucial for grasping the advancement of modern electronic technology.
This passage delves into the concept of high-frequency packaging substrates in the realm of electronics. These substrates are specifically designed for use in high-frequency environments, employing specialized materials and techniques to ensure optimal signal transmission and electromagnetic compatibility. They provide mechanical support for electronic components, facilitate power and signal conveyance, and act as insulation and shields against external interferences.
The increasing demand for high-frequency packaging substrates is driven by their ability to enhance circuit performance and reliability in various high-frequency electronic devices such as radar systems, communication devices, wireless networks, and medical diagnostic equipment.
In essence, high-frequency packaging substrates represent a pivotal electronic constituent, exerting an indispensable influence on high-frequency electronic devices. Through furnishing steadfast support, facilitating signal propagation, and ensuring electromagnetic shielding, high-frequency packaging substrates form a robust cornerstone for the advancement of contemporary high-frequency electronic technology.
What types of high frequency packaging substrates are there?
This paragraph explores various kinds of high-frequency packaging substrates and their attributes. It divides them into three primary categories: monolayered copper foil substrates, bilayered copper foil substrates, and multilayered copper foil substrates.
Monolayered copper foil substrates represent the most basic choice, comprising a single copper foil layer on one side. While they offer cost efficiency, their capacity for signal transmission is somewhat constrained.
Dual-layered copper foil substrates entail copper foil layers on both sides, providing enhanced signal transmission and electrical connectivity. They are apt for moderately intricate high-frequency circuit designs, albeit with a slightly elevated manufacturing expense.
Multi-layered copper foil substrates are the most intricate, comprising multiple copper foil and dielectric strata. They facilitate heightened integration and more elaborate circuit designs, rendering them well-suited for top-tier high-frequency electronic apparatus. However, their manufacturing outlay and procedural intricacy are greater, necessitating rigorous production oversight and process management.
In essence, the choice of high-frequency packaging substrates hinges on variables such as signal transmission prowess, electrical traits, manufacturing expenditure, and process intricacy. It’s imperative to contemplate specific application requisites and assess these factors to ensure the selected substrate aligns with the demands of high-frequency circuits.
What are the advantages of high-frequency packaging substrates compared to traditional substrates?
The passage discusses the significant advantages of high-frequency packaging substrates over traditional substrates in modern electronic equipment design and manufacturing. This paragraph describes the benefits of high-frequency packaging substrates in enhancing device performance and responsiveness, particularly in applications such as radar and wireless networks. These substrates are optimized for transmitting signals effectively, leading to reduced signal attenuation and improved integrity. Additionally, they exhibit superior high-frequency characteristics, including better impedance matching and lower crosstalk, which make them highly suitable for high-frequency signal processing tasks.Additionally, these substrates address electromagnetic compatibility (EMC) concerns through shielding and suppression methods, ensuring reduced interference and radiation for enhanced equipment reliability. Their use of advanced miniaturization technology and lightweight materials facilitates compact and lightweight device designs, crucial for portable electronics. Furthermore, their high-quality materials and precise manufacturing processes contribute to greater reliability and long-term stability, making them preferred for industrial and military applications where sustained performance is essential. Overall, high-frequency packaging substrates are integral to the development and innovation of the electronics industry due to their optimized performance, excellent characteristics, improved EMC, compact design, and long-term reliability.
Why choose a high frequency packaging substrate manufacturer?
This passage emphasizes the importance of selecting a professional manufacturer for high-frequency packaging substrates in today’s electronics industry. It highlights several key reasons for choosing such manufacturers:
This paragraph highlights the key attributes of professional manufacturers specializing in high-frequency electronic equipment. Firstly, it emphasizes their rich experience and expertise in the design and production of such equipment, underscoring their understanding of various substrate types and application scenarios. This knowledge enables them to precisely meet customer requirements and comply with industry standards.
This paragraph highlights the dedication of manufacturers in the high-frequency electronic equipment industry to employing advanced technology and equipment. They prioritize investing in cutting-edge production machinery and processes to guarantee the quality and reliability of their products. Stringent control over material selection and production processes is upheld to consistently adhere to elevated standards. The overarching focus is on blending experience, expertise, and technological innovation, which sets these professional manufacturers apart in the realm of high-frequency electronic equipment.
Customized Solutions: Professional manufacturers offer tailored solutions to accommodate diverse customer needs. Whether it’s adjusting size, material, or hierarchical structure, they can customize substrates for various applications, such as communication systems or radar equipment.
This passage emphasizes the importance of choosing a professional manufacturer specializing in high-frequency packaging substrates. Such manufacturers prioritize customer service, offering effective communication, collaboration, technical support, and after-sales assistance. They ensure project success and customer satisfaction by delivering quality products and leveraging technological advancements. Moreover, their ability to provide customized solutions meets the diverse needs of high-frequency electronics projects, making them indispensable for success and advancement in this field.
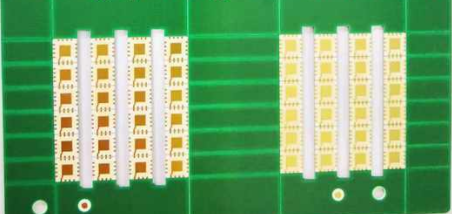
High Frequency package Substrate
What is the process of manufacturing high-frequency packaging substrates?
This passage provides an overview of the meticulous and intricate process involved in manufacturing high-frequency packaging substrates, emphasizing the necessity for precise oversight at each stage to ensure the functionality and reliability of the final product. The key steps outlined include:
Substrate Preparation: This initial stage involves preparing the substrate, typically made of high-frequency dielectric materials such as fiberglass or polyimide. It entails thorough quality checks and pre-treatment to attain smooth surfaces and precise dimensions.
Copper Foil Coating: After substrate preparation, a layer of copper foil is applied onto the substrate surface to establish a conductive layer. Achieving a secure bond between the copper foil and substrate with a flat, even surface requires exacting precision.
Photolithography Patterning: Utilizing photolithography technology, the intended circuit pattern is projected onto the coated copper foil. Through exposure and development processes, the desired circuit pattern is formed. This step is pivotal and necessitates sophisticated equipment and meticulous operation.
Etching: Uncovered portions of the copper foil, as delineated by the photolithography, are etched away to shape the circuit pattern. Precise control over factors such as temperature, pressure, and chemical concentration is essential to ensure accurate etching rates and pattern fidelity.
Chemical Treatment: The etched substrate undergoes chemical treatment to cleanse and eliminate residual photoresist and etchant, while simultaneously enhancing the conductivity and corrosion resistance of the circuit pattern.
Perforation and Copper Pouring: Essential perforations are made in the substrate at designated locations, into which copper is poured to establish connections between circuits at varying levels. This phase requires meticulous control to ensure precise hole placement and uniform copper thickness.
Printing and Marking: Upon completion of the manufacturing process, the high-frequency packaging substrate is printed and marked before being coated with a protective film. This safeguard helps prevent surface damage and corrosion, thus preserving the substrate’s integrity.
Each of these steps demands rigorous process control and the utilization of high-precision equipment to uphold the requisite quality and performance standards for the final product.
In what fields are high-frequency packaging substrates used?
This paragraph highlights the extensive applications of high-frequency packaging substrates across various sectors, primarily in communications, radar technology, medical equipment, and military applications.
In the realm of communications, these substrates are crucial for wireless communication equipment, base stations, and satellite communication systems, facilitating stable and efficient signal transmission and processing to meet the growing demands of communication services.
Radar technology heavily relies on high-frequency packaging substrates for fast and precise signal processing and target detection, ensuring the reliability and stability of radar systems.
In the medical field, these substrates contribute significantly to the development of medical equipment, particularly in high-definition imaging and precise data processing for enhanced medical diagnosis.
Furthermore, high-frequency packaging substrates find extensive use in military applications such as communication equipment, radar systems, and navigation systems, where their anti-interference capabilities and stability are essential for optimal performance in complex combat environments.
This passage highlights the widespread utilization of high-frequency packaging substrates across various domains including communications, radar, medical equipment, and military applications. It emphasizes the role of these substrates in driving technological innovation and societal progress. As technology advances and application areas expand, the prospects for high-frequency packaging substrates are expected to broaden, offering greater convenience and possibilities for both personal and professional endeavors.
How to find a reliable high frequency packaging substrate manufacturer?
When searching for a dependable provider of high-frequency packaging substrates, the selection process plays a pivotal role in securing project success. Here are some strategies and techniques to assist in acquiring precise information and ultimately identifying a supplier aligned with your company’s demands.
Initially, comprehending your requirements is paramount. Prior to engaging a high-frequency packaging substrate manufacturer, delineate your project prerequisites, technical specifications, and budgetary constraints. This will streamline the selection process and enable targeted supplier evaluation.
Reviewing customer feedback and industry standing is an effective means of selecting a trustworthy supplier. Scan industry forums, social media platforms, or professional websites for testimonials and experiences shared by other clients. Scrutinize supplier credibility and reputation to ensure a solid track record.
Assessing the qualifications and accreditations of high-frequency packaging substrate manufacturers serves as pivotal indicators of their technical prowess and quality assurance protocols. Ensuring adherence to pertinent international and industry standards, such as ISO certifications, bolsters confidence in product quality and compliance.
Understanding a supplier’s technical proficiency and research and development (R&D) capabilities is imperative for sourcing products meeting contemporary technical benchmarks. Verify if manufacturers prioritize R&D investments to deliver solutions aligned with evolving technological requirements.
Engaging in direct communication with potential suppliers is fundamental in obtaining accurate insights. Inquire about their operational workflows, production capacities, lead times, and post-sales support via phone, email, or in-person meetings. Timely communication fosters trust and aligns expectations between parties.
Participation in industry-specific trade exhibitions and seminars serves as a valuable avenue for supplier evaluation. These events afford direct interaction with supplier representatives, witnessing product demonstrations, and comprehensive assessment of capabilities.
By leveraging these methodologies and considerations, the selection of a high-frequency packaging substrate manufacturer tailored to your specifications, reliability, and competitiveness is facilitated. Rigorous screening and integration of the aforementioned factors enable the identification of the most suitable supplier, ensuring project success.
What is the price of high frequency packaging substrate?
Understanding the pricing dynamics of high-frequency packaging substrates is crucial for electronic device design and manufacturing. Firstly, price directly impacts project costs, influencing final product pricing and market competitiveness. Thus, manufacturers need to comprehend substrate prices to manage costs effectively and ensure competitive pricing.
Secondly, pricing reflects supply chain stability and reliability. Opting for reasonably priced substrate manufacturers mitigates procurement expenses and secures a stable supply chain, averting production delays or cost escalations due to price fluctuations or supply instability.
Moreover, price awareness aids manufacturers in selecting suitable substrates within budget constraints, striking a balance between performance, quality, and cost to better address customer needs.
Several factors influence substrate prices, including material costs, manufacturing processes, board thickness, layer count, customization requirements, and market supply and demand dynamics.
In essence, comprehending substrate pricing and its influencing factors empowers manufacturers to make informed decisions, enabling effective cost management and enhancing market competitiveness.
Frequently Asked Questions about High Frequency Package Substrates
What advantages do high-frequency package substrates offer over traditional substrates?
High-frequency package substrates provide enhanced stability, interference resistance, and reliability compared to traditional substrates. These advantages make them the preferred choice for applications where consistent signal performance is critical.
How does the manufacturing process of high-frequency package substrates differ from standard substrates?
The manufacturing of high-frequency package substrates involves precise processes to ensure the desired characteristics. This includes intricate steps for both motherboard and substrate production, incorporating advanced technologies to meet the exacting standards of high-frequency applications.
How can one identify reputable high-frequency package substrate manufacturers?
Identifying reliable high-frequency package substrate manufacturers involves considering factors like industry reputation, certifications, and product quality. Online resources, industry exhibitions, and networking with professionals are effective ways to find trustworthy suppliers.
What distinguishes high-frequency package substrates from regular PCBs?
High-frequency package substrates are specifically engineered to handle signals at frequencies beyond those typically handled by standard PCBs. They are designed with materials and structures optimized for minimal signal loss and interference at higher frequencies.
Can high-frequency package substrates be customized to meet specific design requirements?
Yes, many high-frequency package substrate manufacturers offer customization services to meet the unique needs of each application. This may include tailored material formulations, specialized layer stackups, or precise impedance control to ensure optimal performance.