GPU Package Substrates Manufacturer.”GPU Package Substrates Manufacturer” refers to a company specializing in the production of substrates specifically designed for GPU (Graphics Processing Unit) packages. These substrates are engineered to meet high-performance demands, offering efficient thermal management and reliable electrical connectivity essential for modern graphics applications.
In today’s digital world, GPU packaging substrates play a key role in modern electronic devices. This article aims to provide an in-depth introduction to the definition, design, manufacturing process, application fields and advantages of GPU packaging substrates, to provide professionals in the electronics and technology fields with a comprehensive understanding, from basic concepts to advanced applications, and to help readers gain an in-depth grasp of this important technology. component.
What are GPU Package Substrates?
GPU packaging substrates are an integral and critical component of modern electronic devices. It is a flat substrate, usually made of insulating materials such as FR4 (fiberglass reinforced epoxy laminate), with various electronic components such as integrated circuits, capacitors, resistors, etc. mounted on its surface. These components are interconnected through conductive paths, pads, and other features on the substrate to form complex circuit structures.
The design and manufacturing of GPU packaging substrates is a highly precise process that requires strict manufacturing and assembly technology. The conductive layer of the substrate is usually covered with a thin copper foil on the surface of the substrate, and a precise circuit path is formed through photolithography, etching and other processes. These paths not only connect various electronic components, but also allow electrical signals to be quickly transmitted between various components to ensure the normal operation of the device.
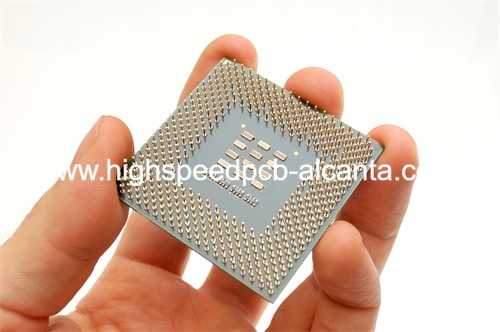
GPU Package Substrates Manufacturer
In practical applications, GPU packaging substrates are widely used in various devices that require high-performance computing and graphics processing capabilities, such as graphics processing units (GPUs), high-performance computers, game consoles, and data center servers. They not only support the functional operation of the device, but also provide it with a stable electrical connection and signal transmission channel.
In short, as a core component of electronic equipment, GPU packaging substrate not only provides structural support and a platform for component installation, but is also the key to achieving coordinated operation among various functional modules of the equipment. As technology advances and demand continues to grow, the design and manufacturing of GPU packaging substrates will continue to evolve to meet the needs of increasingly complex electronic devices.
GPU Package Substrates design Reference Guide.
The GPU Packaging Substrate Design Reference Guide is an essential manual for engineers and designers designing GPU layouts. In modern electronic devices, GPU packaging substrates play a key role, and their design quality directly affects device performance and reliability. Here are the main things covered in the design guide:
Best practices: Best practices for designing GPU packaging substrates include circuit layout optimization, signal integrity assurance and thermal management strategies. Through reasonable layout design, signal interference and electromagnetic interference can be minimized and the stability and anti-interference ability of the circuit can be improved. At the same time, effective thermal management design can ensure stable operation of the GPU under high load and extend the service life of the device.
Design rules: Design rules are key to ensuring that the GPU packaging substrate design meets technical requirements and manufacturing capabilities. These rules cover key parameters such as minimum line width/line spacing, aperture diameter, and inter-layer distance, ensuring that good process control and reliability can be maintained during the manufacturing process. Following design rules can effectively reduce manufacturing defects and costs, and improve first-time success rates.
Software Tools: Modern GPU packaging substrate design relies on powerful software tools such as CAD software, layout software, and simulation tools. These tools not only enable precise layout and design of complex circuits, but also perform signal integrity analysis, thermal simulation and three-dimensional modeling to help designers optimize design solutions and predict possible problems.
Design technology: With the advancement of technology, GPU packaging substrate design technology continues to evolve. New materials, new manufacturing processes, and advanced packaging technologies are constantly emerging, and designers need to continue to learn and apply these technologies to meet growing performance demands and compact equipment space requirements.
In summary, the GPU packaging substrate design reference guide is not only an important tool for technicians, but also the key to ensuring efficient and reliable GPU design. By following best practices, design rules, and utilizing advanced software tools and design techniques, engineers and designers can more effectively optimize complex GPU layouts, driving improvements in electronic device performance and innovation.
What material is used in GPU Package Substrates?
GPU packaging substrates are critical components in modern electronic devices, supporting the stable operation and efficient performance of graphics processing units. These substrates often come in a variety of materials to meet different application needs and design requirements.
One of the most common substrate materials for GPU packaging is FR4, or fiberglass reinforced epoxy laminate. FR4 material is known for its excellent electrical insulation properties and mechanical strength, making it the substrate of choice for most conventional GPU packaging. It can effectively support circuit wiring and installation of electronic components while providing good mechanical support and stability, making it suitable for a variety of consumer electronics and industrial applications.
Another important material is polyimide, which is mainly used for flexible GPU packaging substrates. Unlike rigid FR4, polyimide substrates have excellent flexibility and high temperature resistance, making them suitable for applications that require bending and curved surface installation. The use of this material allows GPU packaging substrates to function in devices with limited space or requiring highly flexible designs, such as portable electronics and flexible displays.
In summary, the choice of GPU packaging substrate depends on specific application requirements and design considerations. As a conventional rigid material, FR4 excels in its stability and reliability; while polyimide provides flexible design options to adapt to the emerging market demand for flexible electronic devices. As technology continues to advance and application scenarios expand, material selection for GPU packaging substrates will continue to evolve to support more diverse and complex electronic product design and manufacturing needs.
What size are GPU Package Substrates?
The size of the GPU packaging substrate varies depending on the specific application. They play a key role in a variety of electronic devices, ranging in size from tiny GPU packaging substrates in smartphones and wearable devices to large GPU packaging substrates in industrial equipment or power electronics. Variations in these dimensions are primarily determined by the following factors:
First, smartphones and wearable devices require compact and lightweight GPU packaging substrates to adapt to the miniaturization trend of devices. These devices often need to accommodate the GPU and other surrounding components in a limited space, so the GPU packaging substrate is usually very small and can be accurately installed inside the device to ensure the performance and battery life of the device.
Secondly, industrial equipment and power electronics often require larger GPU packaging substrates. These devices may need to handle higher power and current, so the GPU packaging substrate requires a larger surface area to accommodate more electronic components and thermal solutions. In addition, industrial equipment often requires higher reliability and durability, so the design and size of substrates will also increase accordingly to meet the requirements for long-term stable operation.
In summary, the size of the GPU packaging substrate is not only determined by the size of the electronic components, but also affected by the space constraints within the device. The size of the GPU packaging substrate required for different application scenarios may vary greatly, from tiny to large, each with its own unique design requirements and functional requirements. Therefore, when designing a GPU packaging substrate, the actual needs of a specific application must be carefully considered to ensure optimal performance, reliability and adaptability.
The Manufacturer Process of GPU Package Substrates.
The manufacturing process of GPU packaging substrates involves multiple critical steps, each of which has a significant impact on the quality and performance of the final product. Here’s a detailed look at the main steps:
The first is the substrate preparation stage. At this stage, selecting the appropriate substrate material is critical. Common materials include FR4 (fiberglass reinforced epoxy laminate) and other application-specific high-performance materials. Substrate preparation includes cleaning and surface preparation to ensure subsequent material deposition and adhesion can proceed smoothly.
Next comes the copper layer deposition. Copper is one of the most conductive materials on circuit boards, and the copper layer is deposited by chemical methods or electroplating processes to create the required conductive paths and connection areas.
The third step is the application and exposure of photoresist. In this step, photoresist is first coated on the substrate surface and then exposed through a template or mask. After exposure, the uncured photoresist is removed by chemical etching, leaving the desired conductive patterns and structures.
Etching is one of the key steps in the manufacturing process. The etching process uses chemical solutions or ion beams to remove unprotected portions of the copper layer, creating precise areas for conductors and connections on the substrate.
Then comes drilling. Drill holes at specific locations using mechanical drills or laser technology to facilitate subsequent installation and connection of components. Accuracy and precision in drilling are critical to ensuring the functionality and reliability of the circuit board.
Next is the installation of the components. Depending on the design requirements, electronic components are precisely mounted on the circuit board via surface mount technology (SMT) or through-hole mounting technology. SMT technology is suitable for small and high-density electronic components, while through-hole mounting is suitable for larger components and components requiring higher mechanical strength.
Finally comes the welding and testing phase. During the soldering process, hot fusion soldering or reflow soldering is used to securely secure electronic components to the circuit board and ensure a good electrical connection. After soldering is complete, functional testing and performance verification of the boards is performed to ensure each board is working as expected.
In summary, the manufacturing process of GPU packaging substrates covers multiple key steps from substrate preparation to final testing. Each step requires precise process control and a high degree of process technology to ensure the production of high-quality and reliable electronic products. .
The Application area of GPU Package Substrates.
As a core component of modern electronic equipment, GPU packaging substrate has a wide range of applications, covering many important industries such as consumer electronics, communications, automobiles, aerospace, medical equipment, and industrial automation.
In the field of consumer electronics, GPU packaging substrates are widely used in products such as smartphones, tablets, home appliances, and gaming devices. They not only support the high-performance computing and graphics processing capabilities of the device, but also enable device miniaturization and diversification of functions.
In the communications industry, GPU packaging substrates play a key role and are used in network equipment, base stations and communications infrastructure. They are capable of handling large data streams and complex signal processing tasks, ensuring efficient operation and stability of communication equipment.
In the automotive industry, GPU packaging substrates are used in high-end electronic equipment such as vehicle infotainment systems, vehicle navigation, and driver assistance systems. They not only improve the intelligence level of vehicles, but also support the data processing and analysis functions of on-board cameras and sensors.
In the aerospace sector, GPU packaging substrates play a key role in avionics, satellite communications and navigation systems. They can withstand the challenges of extreme environmental conditions and ensure the reliability and performance stability of aerospace equipment.
In the field of medical equipment, GPU packaging substrates are used in medical imaging equipment, health monitoring systems and medical information technology. They support high-definition image processing, real-time data analysis and telemedicine services, improving the accuracy and efficiency of medical diagnosis and treatment.
In the field of industrial automation, GPU packaging substrates are used in industrial robots, automated production lines and intelligent monitoring systems. They help achieve efficient interconnection and data exchange between devices, improving production efficiency and manufacturing quality.
In short, GPU packaging substrate is not only an indispensable core component in modern electronic equipment, but also an important driving force for technological progress and innovation in various industries. Their wide application ensures high performance, efficiency and reliability of equipment, helping to build an intelligent, connected and digital future.
What are the advantages of GPU Package Substrates?
GPU packaging substrate has obvious advantages compared to other wiring methods, which are mainly reflected in the following aspects:
First, GPU packaging substrates effectively enable the miniaturization of electronic devices by allowing compact layouts. Because its design can highly integrate electronic components and complex circuits, the size of the device can be significantly reduced, especially in mobile devices and portable electronic products. This advantage is particularly prominent.
Second, the GPU packaging substrate uses a standardized manufacturing process, ensuring consistent quality and reliability. Strict quality control and testing processes during the manufacturing process enable each GPU packaging substrate to meet high standard performance requirements, thereby ensuring product reliability and stability.
Third, the assembly process of GPU packaging substrate is simpler and more efficient than traditional wiring methods. The automated assembly process not only greatly reduces the need for manual operations, but also improves production efficiency, shortens product time to market, and reduces overall manufacturing costs.
Secondly, GPU packaging substrates are highly customizable. Design engineers can flexibly layout circuits and integrated components according to specific application needs and performance requirements to meet the individual needs of different markets and customers, including handling complex circuit designs and the integration of multiple functions.
Finally, because the GPU packaging substrate is suitable for mass production, its unit price cost is low, giving it obvious economic advantages in mass manufacturing. This makes GPU packaging substrates economical and affordable in the production of electronic products, and can be more widely used in various consumer electronics, communication equipment, industrial control systems and other fields.
In summary, GPU packaging substrates have become an indispensable and key component in modern electronic equipment manufacturing due to their compact design, high reliability, simple assembly process, flexible customization and economical production costs, promoting the electronics industry. Rapid development and innovative applications of technology.
FAQ
How is a GPU packaging substrate different from a traditional circuit board?
GPU packaging substrates generally need to handle higher power density and thermal management requirements than traditional circuit boards. They are designed for high-performance computing devices with integrated graphics processing units (GPUs) and therefore differ in electrical characteristics, thermal solutions and physical dimensions.
What are the main materials for GPU packaging substrates?
Primary materials typically include fiberglass-reinforced epoxy laminates such as FR4, used for conventional GPU packaging substrates, and flexible materials such as polyimide for specific applications requiring bending properties.
How to choose a suitable GPU packaging substrate manufacturer?
When selecting a GPU packaging substrate manufacturer, key factors include its experience in high-performance computing and electronic devices, manufacturing capabilities, quality control standards, and service support capabilities. It is recommended to evaluate its advanced manufacturing technology and reliable delivery lead time.
What are the design considerations for GPU packaging substrates?
When designing a GPU packaging substrate, optimization of circuit layout, thermal management solutions, EMI/EMC compatibility, component layout, and power consumption distribution need to be considered. These factors directly affect the performance and stability of the GPU packaging substrate.