Global Packaging Substrate Supplier, BT core, Rogers Core, High TG FR4 core, ABF core, and other types materials substrates manufacture. we offer small gap/ trace BGA substrates from 2 layer to 20 layrs.
In today’s electronics industry, the packaging substrate holds immense importance as a crucial electronic component. Its primary function lies in connecting and supporting chips, facilitating essential electrical and mechanical connections within electronic devices to ensure their normal operation and stability.
Essentially, the packaging substrate serves as the foundational element of an electronic device. It offers a stable support platform for the chip while establishing connections with other components such as power supplies and sensors through its embedded circuitry. This connectivity encompasses both physical links and the transmission of signals and power, enabling seamless communication and collaboration among the device’s various components.
Chips in electronic devices are typically housed within chip packages, which in turn require mounting onto a support structure. This is precisely where the packaging substrate comes into play. It must bear the weight and pressure of the chip while facilitating reliable electrical connections to facilitate proper communication between the chip and external systems.
Beyond its primary functions of providing support and connectivity, packaging substrates also serve roles in heat dissipation and dust protection. As electronic equipment evolves and functionalities expand, the demands placed on packaging substrates grow increasingly stringent. They must exhibit high density, reliability, and effective heat dissipation capabilities to ensure prolonged and stable operation of the equipment.
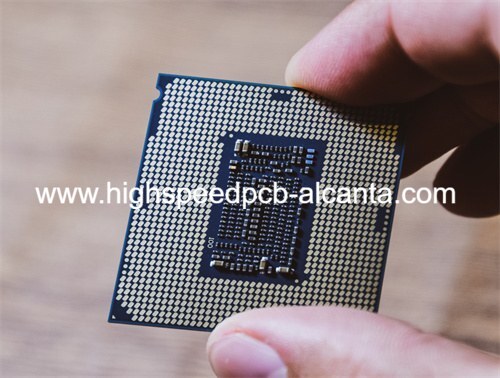
Global Packaging Substrate Manufacturer
Therefore, the packaging substrate stands out as a core component in electronic equipment, with its quality and performance directly impacting the overall quality and functionality of the device. In the modern electronics industry, research, development, and production of packaging substrates constitute a vital field, continually driving innovation and progress in electronic equipment.
What types of packaging substrates are there?
Packaging substrates are essential components in modern electronic equipment manufacturing, offering a variety of types with unique characteristics and applications worldwide. Each type serves specific electronic products and fields, catering to diverse needs.
High-frequency substrates are specialized for processing high-frequency signals, offering low signal loss and high transmission rates. They excel in applications like wireless communication and radar systems, ensuring consistent signal transmission in high-frequency environments.
Carrier boards are designed to support and secure chips, boasting high load capacity and effective heat dissipation. They find utility in chip testing and packaging scenarios, enhancing stability and reliability during production processes, thus improving efficiency and product quality.
Multilayer boards, composed of multiple substrates and copper foil layers, feature high wiring density and robust electrical performance, suitable for large and complex circuit designs. They enable sophisticated wiring layouts within confined spaces while ensuring stable electrical connections and signal transmission.
Choosing the appropriate packaging substrate type requires comprehensive considerations based on specific product requirements and application contexts to guarantee optimal performance and reliability of electronic products.
Why choose packaging substrates?
In the realm of modern electronic device manufacturing, the selection of suitable substrate materials holds paramount importance. Among these, packaging substrates emerge as a crucial electronic component, offering a host of advantages over other boards. Let’s delve into these advantages together.
Packaging substrates offer increased density and smaller footprints compared to conventional boards, allowing for the incorporation of more components and connections in limited spaces. This facilitates the creation of electronic devices that are more compact and lightweight.
In the domain of high-speed data transmission and processing, maintaining signal integrity is paramount. Packaging substrates employ advanced materials and techniques to effectively minimize signal degradation and interference during transmission, guaranteeing the transmission of high-quality signals.
As electronic device performance continues to advance, effective thermal management emerges as a pressing issue. Packaging substrates excel in dissipating and dispersing heat, thereby upholding equipment performance stability through optimized heat dissipation structures and materials.
While the manufacturing cost of packaging substrates may be relatively high, they pave the way for long-term cost savings by enhancing production efficiency and reducing maintenance expenses. Furthermore, their integration and performance advantages contribute to overall electronic device cost reduction.
Packaging substrates find applicability not only in traditional electronic equipment manufacturing but also in supporting various advanced technologies and applications, including high-speed communications, artificial intelligence, and the Internet of Things. They serve as a dependable foundation for innovation across diverse industries.
In summary, the preference for packaging substrates over other boards in modern electronic equipment manufacturing stems from their multitude of advantages. Their high density, optimized signal integrity, efficient thermal management, cost-effectiveness, and support for various technologies render packaging substrates a favored material in the electronics industry.
What is the manufacturing process for packaging substrates?
The manufacturing process of packaging substrates is a multifaceted procedure involving a series of sequential steps and specialized equipment. Let’s explore each phase of manufacturing packaging substrates and clarify how they are carried out.
Before commencing the manufacturing process of a packaging substrate, meticulous planning and design are essential. This stage involves defining parameters such as size, layout, hierarchy, and critical aspects like circuit wiring design.
These materials typically include fiberglass cloth, epoxy resin, copper foil, and others. Among these, fiberglass cloth serves as the insulating material, epoxy resin functions as the substrate’s base material, while copper foil is utilized as the conductive layer.
Initially, fiberglass cloth is positioned on a level surface, followed by the uniform application of epoxy resin onto the cloth surface. Subsequently, the epoxy resin undergoes curing, either through pressing or baking, culminating in the formation of the substrate’s fundamental structure.
Throughout the manufacturing process, the creation of a conductive layer on the substrate, in accordance with design prerequisites, is imperative to achieve circuit connectivity functionality. This stage commonly entails etching technology, wherein the substrate’s surface is coated with a layer of copper foil. Chemical etching methods are then employed to eliminate surplus portions of the copper foil, thereby crafting the requisite circuit layer.
For multi-layer substrates, an additional step of multi-layer stacking and lamination is requisite. During this phase, manufactured circuit boards are stacked as per design specifications, and the various layers of circuit boards are securely bonded together through a high-temperature and high-pressure lamination process, culminating in the formation of a comprehensive multi-layer substrate structure.
During the substrate manufacturing process, drilling and guide holes are also required to achieve penetration of circuit connections. This step usually uses CNC drilling machines or laser drilling technology to drill or guide holes where connections are needed to provide access for subsequent welding and assembly.
Following the manufacturing of the substrate, surface treatment and application of a protective cover layer are typically necessary. This stage aims to safeguard the substrate surface, enhance corrosion resistance and mechanical durability, and streamline welding and assembly procedures. Through these steps, the production process for the packaging substrate concludes. Achieving desired quality and performance mandates advanced technology and precise equipment to meet specified standards.
In what areas are packaging substrates used?
Packaging substrates serve as crucial components in various electronic devices across different sectors. In the realm of communications, they find extensive application in devices like mobile phones, routers, and base stations. These substrates facilitate the integration of chips and components, enabling complex wiring connections for signal transmission and processing.
Meticulous design and manufacturing are essential to ensure the reliable operation of medical equipment across different environments, providing dependable technical support for medical diagnostics and treatments.
Similarly, in the automotive sector, packaging substrates are extensively utilized in electronic systems such as in-car entertainment, body control, and driver assistance systems. With the increasing number and complexity of electronic devices in modern vehicles, packaging substrates serve as vital components that connect and support various electronic elements. High-performance packaging substrates contribute significantly to achieving greater functional integration and faster signal processing speeds in automotive electronic systems, thereby enhancing the intelligence, safety, and comfort of vehicles.
They not only facilitate the connection and support of diverse electronic components but also ensure stable signal transmission and processing, providing crucial support for technological innovation and development in related sectors. With ongoing advancements in science and technology and growing application demands, packaging substrates will continue to be integral in promoting development and progress across various fields.
How to find global packaging substrate manufacturers?
When searching for global packaging substrate manufacturers, there are several common methods and channels you can utilize to gather relevant information and select the most suitable partner.
Firstly, leveraging your company’s existing network of suppliers can be fruitful. Reach out to current suppliers to inquire about their capabilities in packaging substrate manufacturing, including quality levels and production capacity. This approach can help identify reliable partners quickly while minimizing collaboration risks.
Another effective approach is leveraging the internet to search for global packaging substrate manufacturers. Utilizing search engines with relevant keywords like “global packaging substrate manufacturers” and “packaging substrate suppliers” enables thorough exploration and comparison of various vendors, providing insights into their products and services.
Moreover, participating in industry trade shows and exhibitions provides an excellent opportunity to explore packaging substrate manufacturers. These gatherings enable direct interaction with numerous manufacturers, offering insights into their products, technologies, and credibility. Furthermore, conducting on-site inspections allows for a thorough assessment of each manufacturer’s capabilities.
Joining relevant industry associations and forums can also help you find packaging substrate manufacturers. On these platforms, you can exchange experience and information with professionals in the same industry, and obtain more industry trends and manufacturer recommendations.
Regularly reading professional media and magazines is also a way to learn about packaging substrate manufacturers. These media usually report on industry news and vendor dynamics, helping you track industry trends and find potential partners.
By utilizing the aforementioned approaches, you can attain a thorough comprehension of global packaging substrate manufacturers and select the most suitable partner for your requirements. When opting for a partner, besides evaluating price and quality, it’s essential to also focus on factors such as production capacity, technical expertise, and level of service to guarantee seamless collaboration and shared success.
What factors affect the quotations of global packaging substrate manufacturers?
When selecting a global packaging substrate manufacturer, it’s crucial to grasp the factors influencing their quotes. These factors not only shape the final quotation but also directly impact project costs and benefits. Below, I’ll delve into the primary factors affecting quotes from global packaging substrate manufacturers and how to procure the most suitable ones.
Material costs stand out as a major expense in packaging substrates. Prices vary significantly across different substrate materials, and fluctuations in market supply, demand, and raw material prices constantly alter material costs.
The complexity of substrate designs directly impacts the manufacturing process, necessitating specific processes and technologies. More intricate designs entail greater investments in processes and equipment, prompting manufacturers to base their quotes on design complexity.
Different manufacturing processes have different cost impacts on substrates. Some advanced manufacturing processes may require higher investment and technical support, thus resulting in higher quotations.
The quantity and batch size of an order play significant roles in determining the quotation. Typically, larger-volume orders benefit from reduced unit prices, whereas smaller-volume orders tend to have comparatively higher prices. Additionally, the level of technical support and after-sales service provided by the manufacturer impacts the quotation. Some manufacturers may offer extensive technical assistance and customization services, albeit at a higher cost reflected in the quote.
Frequently Asked Questions (FAQs)
Can global packaging substrate manufacturers provide customized solutions for unique project requirements?
Many global manufacturers offer customization services to tailor packaging substrates to specific project needs. Discuss your requirements with manufacturers to explore available options.
How do packaging substrates differ from traditional board materials?
Packaging substrates offer advantages such as higher density, improved signal integrity, and lower costs compared to traditional board materials. These benefits make them preferable for modern electronic device manufacturing.
What are the main types of packaging substrates available?
Global packaging substrate manufacturers offer various types, including HDI boards, rigid-flex boards, and more. Each type has distinct characteristics suited for different applications.
How do packaging substrates differ from traditional boards?
Packaging substrates offer advantages such as higher density, improved signal integrity, and reduced costs compared to traditional boards. They are designed specifically to support and connect chips in electronic devices.
How do packaging substrate manufacturers handle customization requests?
Many manufacturers offer customization options to tailor packaging substrates according to specific project needs. This may include adjustments in size, material, and design features. Communication with the manufacturer is key to ensuring precise customization.