Glass Package Substrates Manufacturer.A leading Glass Package Substrates Manufacturer, our expertise lies in crafting precision-engineered substrates for diverse electronic applications. Merging cutting-edge technology with meticulous craftsmanship, we produce substrates that meet stringent industry standards. Our state-of-the-art facilities ensure seamless production processes, guaranteeing consistency and reliability in every batch. With a commitment to innovation and quality, we cater to the evolving needs of the semiconductor industry, providing tailor-made solutions for advanced packaging requirements. Partner with us for unparalleled expertise and exceptional products, driving efficiency and performance in your electronic devices.
In modern electronic equipment, printed circuit boards (PCBs) play a vital role, running through the design and manufacturing of almost every electronic product. However, with the continuous development of technology, the requirements for performance and reliability of electronic equipment are also constantly increasing. Under this circumstance, glass packaging substrates have gradually attracted widespread attention. As an important type of PCB, glass packaging substrates have excellent electrical and thermal properties and are suitable for many high-performance applications. For PCB engineers, an in-depth understanding of the process processes of glass packaging substrate manufacturers will help to better understand and apply this advanced technology.
What is a glass packaging substrate?
When it comes to the manufacturing and design of electronic devices, glass packaging substrates are a critical component that cannot be ignored. Glass package substrate, referred to as GPG (Glass Package Substrates), is a high-performance electronic substrate based on glass substrate, which plays an important role in high-frequency, high-speed and high-density applications. This substrate not only provides excellent electrical performance, but also has excellent thermal performance and reliability, making it widely used in various fields such as communications, medical, aerospace, etc.
First, let’s take a closer look at the composition and characteristics of glass packaging substrates. The core of the glass packaging substrate is the glass substrate, whose advantages include a high degree of flatness, excellent dimensional stability and excellent chemical inertness. These properties make glass substrates ideal carriers for high-performance electronic devices. Compared with traditional organic substrates, glass packaging substrates have lower dielectric loss, higher frequency response and better mechanical stability, and can meet the requirements for high-frequency signal transmission and high-speed data processing.
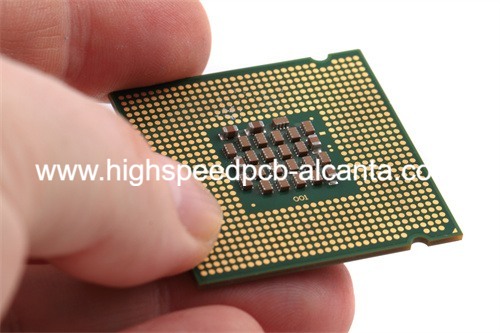
Glass Package Substrates Manufacturer
Secondly, the applications of glass packaging substrates in different fields are also diverse. In the field of communications, glass packaging substrates are widely used in wireless base stations, optical fiber communication equipment and satellite communication systems. Its high frequency response and low loss characteristics can ensure stable transmission of signals. In the medical field, glass packaging substrates are used in medical imaging equipment, medical diagnostic instruments and implantable medical devices. Their reliability and durability can ensure the long-term stable operation of medical equipment. In the aerospace field, glass packaging substrates are widely used in spacecraft, navigation systems and flight control equipment. Their lightweight, high strength and high temperature resistance can meet the working requirements of spacecraft in extreme environments.
In general, as a high-performance electronic substrate, glass packaging substrate not only has excellent electrical performance, thermal performance and reliability, but can also meet the requirements for high-frequency, high-speed and high-density applications in various fields. With the continuous development of electronic technology and the continuous expansion of application fields, glass packaging substrates will play an increasingly important role in the future.
How to design glass packaging substrate?
Designing glass packaging substrates is a complex and critical task that involves considerations and trade-offs of many factors. Below are detailed instructions for designing glass packaging substrates:
Circuit layout is one of the primary considerations when designing glass packaging substrates. Good circuit layout can ensure the stability and reliability of signal transmission. Engineers need to consider factors such as component placement, signal path length and routing. Reasonable layout can reduce the length of the signal path, reduce signal transmission delay and loss, thereby improving system performance.
Glass packaging substrates usually have a multi-layer structure, and effective connections between different layers are required. During the design process, engineers need to reasonably plan the inter-layer connection methods, including through-hole connections, blind via connections, and buried via connections. Proper inter-layer connections can ensure the reliability and stability of signal transmission while reducing electromagnetic interference and crosstalk in the system.
When designing glass packaging substrates, engineers also need to consider power consumption management. High-power components may cause the system temperature to rise, affecting circuit performance and reliability. Therefore, engineers need to take effective measures to manage power consumption, including optimizing the power supply network, using low-power components and designing effective heat dissipation structures. These measures can help reduce system power consumption and improve system stability and reliability.
Electromagnetic interference (EMI) and radio frequency interference (RFI) are issues that need to be paid attention to when designing glass packaging substrates. These interferences may affect the normal operation of the system or even cause system performance degradation or failure. In order to suppress EMI/RFI interference, engineers can take a series of measures, including using shielding structures, reducing loop areas, adopting appropriate wiring methods, and selecting appropriate filters. These measures can effectively reduce the impact of interference and improve the anti-interference ability of the system.
Using advanced design software and simulation tools, engineers can conduct comprehensive simulation and optimization of glass packaging substrates. Through reasonable layout design, inter-layer connections, power management and EMI/RFI suppression, engineers can ensure that the designed glass packaging substrate has excellent performance, stability and reliability to meet the needs of different application scenarios.
What is the manufacturing process of glass packaging substrates?
The glass packaging substrate manufacturing process is highly complex and sophisticated, involving multiple critical steps. Below is a detailed description of each step:
Before manufacturing a glass packaging substrate, you first need to prepare a high-quality glass substrate and other necessary materials. The choice of glass substrates is critical as they will form the basis of the circuit. These substrates must have consistent thickness and surface flatness to ensure circuit stability and reliability.
Before actual manufacturing can proceed, the design of the circuit must be converted into a CAD (computer-aided design) file. This step involves using professional design software to convert circuit layout, connections, power management, etc. into digital graphical representations. Designers must consider factors such as signal transmission, circuit routing, power distribution, and EMI/RFI suppression.
Once the CAD files are complete, the next step is to transfer these graphics to the glass substrate surface. Typically, this is achieved using photolithography techniques. In this process, a photosensitive material is used to cover the entire substrate surface, and a CAD file is used as a template to transfer the pattern to the photosensitive material using a photolithography machine.
After the pattern transfer is completed, metal or other materials need to be deposited on the surface of the substrate to form the actual circuit pattern. This is usually achieved through techniques such as chemical vapor deposition (CVD) or physical vapor deposition (PVD). The deposited material will fill the empty areas in the pattern and form conductive paths.
Once deposition is complete, the next step is to use chemical or mechanical methods to remove unwanted material to form the final circuit pattern. This process is called etching, and typically uses an acidic or alkaline solution, or mechanical etching equipment. After etching, the desired circuit pattern will be obtained.
Finally, the manufactured substrates undergo rigorous inspection and testing to ensure they meet specifications and quality requirements. This includes using optical microscopes to check the accuracy and integrity of circuit graphics, and using high-frequency test equipment to test circuit performance and stability. Only after passing all inspections and tests will the manufactured substrate be considered qualified and can be used in actual applications.
Through the above steps, glass packaging substrate manufacturers can produce high-quality, high-performance electronic substrates to meet the needs of different industries and fields. The precision and complexity of this process requires manufacturers to have advanced equipment and technology, as well as a strict quality control system to ensure product quality and reliability.
How much does a glass packaging substrate cost?
The cost of glass packaging substrates is an important issue of great concern to both manufacturers and customers. It is affected by many factors, including manufacturing process, material selection, specification requirements and order quantity. Only by understanding these factors can the cost of glass packaging substrates be more accurately evaluated and controlled.
First of all, the manufacturing process is one of the key factors affecting the cost of glass packaging substrates. High-end manufacturing processes usually require more advanced equipment and technology, so the cost is relatively high. For example, using high-precision photolithography technology and micro-machining technology can achieve more complex and finer circuit patterns, but it will also increase production costs. In contrast, traditional manufacturing processes, although lower cost, often fail to meet the requirements of high-performance electronic products.
Secondly, material selection has a huge impact on the cost of glass packaging substrates. Different substrate materials and copper thicknesses will directly affect the cost level. For example, using high-quality glass substrates and copper foil can improve the performance and reliability of circuit boards, but it also increases material costs. In addition, the selection of special dielectric materials and solder will also have an impact on costs.
In addition, specification requirements are another important factor that affects costs. Customers may have different specifications for glass packaging substrates, including size, number of layers, line width and line spacing, aperture, etc. Customized and special-request products often increase manufacturing costs because they require more process steps and more complex production processes.
Finally, order quantity will also have an impact on the cost of glass packaging substrates. Generally speaking, mass production can achieve cost advantages of scale, so the unit product cost is relatively low. On the contrary, in small batch production, due to the smaller production scale and relatively high equipment debugging and preparation costs, the unit product cost will be relatively high.
Overall, customized and high-performance glass packaging substrates cost more because they require more advanced manufacturing processes and high-quality materials. The cost of mass-produced products with standard specifications is relatively low because they can enjoy the cost advantage of scale. Therefore, when selecting glass packaging substrates, manufacturers and customers should comprehensively consider the above factors and make reasonable choices based on actual needs.
What is the material of the glass packaging substrate?
Glass packaging substrate is an important type of high-performance electronic substrate, and its material composition is crucial. In the manufacturing process of glass packaging substrates, the selection of various materials directly affects its electrical performance, thermal performance and overall reliability. The following are the main materials of glass packaging substrates and their characteristics:
Glass substrate is the basic material of glass packaging substrate and is usually made of high-purity glass material. These glass substrates offer excellent flatness and surface flatness, ensuring accurate circuit routing and stable performance.
Metallized materials are mainly used to form circuit patterns and connect conductive paths between different layers. Commonly used metallization materials include copper and silver, which have good electrical conductivity and solderability, ensuring efficient transmission and reliable connection of circuits.
Dielectric materials are used to fill the gaps between circuit patterns and serve as insulation and support. Among them, polyimide film is a commonly used dielectric material with excellent insulation properties, heat resistance and chemical stability, and can effectively reduce signal crosstalk and circuit noise.
Solder is used to weld electronic components and connect circuit patterns. It is one of the most important materials in the manufacturing of glass packaging substrates. High-quality solder should have good welding performance and reliable connectivity, ensuring a solid connection and good electrical conductivity between electronic components and substrates.
The excellent properties of these materials make glass packaging substrates suitable for various complex application environments, such as communication equipment, medical equipment, aerospace and other fields. By properly selecting and combining these materials, manufacturers can produce glass packaging substrates with stable performance and reliable quality that meet customer needs and expectations. In the increasingly competitive electronics market, precise selection of materials and continuous innovation in application technology will become key competitive advantages for glass packaging substrate manufacturers.
Who manufactures glass packaging substrates?
In the production process of glass packaging substrates, manufacturers play a vital role. They must have advanced production equipment, a professional technical team and a strict quality management system to ensure the production of high-quality products that meet customer requirements and standards. In this field, supplier selection is crucial, and our company is your reliable partner.
As a professional glass packaging substrate manufacturer, our company is committed to providing customers with high-quality products and services. We have advanced production equipment and technology to meet the needs of various complex applications. Our production process strictly follows industry standards and quality management systems to ensure that every substrate produced has stable and reliable performance.
The company not only provides standard specifications of glass packaging substrates, but also provides customized solutions according to customers’ specific needs. Our technical team has rich industry experience and professional knowledge and can provide customers with personalized design and technical support to ensure that products can fully meet customer requirements and expectations.
In addition to high-quality products, our company also focuses on communication and cooperation with customers. We always adhere to the principle of “customer first” and are committed to providing customers with the most satisfactory service and support. Our sales team and customer service team have good professionalism and communication skills, and can respond to customer needs and problems in a timely manner and provide effective solutions.
In short, our company is a trustworthy glass packaging substrate manufacturer, and we are committed to providing customers with high-quality products and excellent services. No matter what your needs are, we will be happy to provide you with the most satisfactory solution. Look forward to working with you!
What are the 5 qualities of great customer service?
For PCB manufacturers, quality customer service is a key factor in maintaining customer relationships and improving market competitiveness. Here are five qualities of great customer service:
Responsiveness: In a competitive market, time is money. An excellent customer service team should be able to respond to customer inquiries and questions in a timely manner, ensuring that customers receive prompt support and solutions. Fast response time not only demonstrates the efficiency of the enterprise, but also enhances customer trust and satisfaction in the enterprise.
Professional knowledge: PCB manufacturing involves complex processes and technologies, and customers often require professional guidance and advice. Therefore, a customer service team with rich industry experience and professional knowledge is particularly important. They should be able to accurately understand the client’s needs and provide effective solutions to help the client achieve the success of their project.
Customized services: Every customer has unique needs and requirements, so providing customized solutions is crucial to meet customer expectations. An excellent customer service team should be able to flexibly provide personalized products and services based on customers’ specific needs, thereby ensuring that the product perfectly matches the customer’s requirements.
Quality Assurance: As a PCB manufacturer, providing high-quality products is a basic responsibility. Therefore, strict implementation of the quality management system is an important guarantee to ensure customer satisfaction and trust. The customer service team should always pay attention to product quality to ensure that product quality is stable and reliable and meets customer requirements and standards.
After-Sales Support: Excellent customer service doesn’t just end with transaction completion, it also includes after-sales support and service. Customers may encounter various problems during the use of products, and good after-sales support can help customers solve problems in a timely manner and improve customer satisfaction and loyalty. Providing comprehensive after-sales services such as technical training, maintenance and problem solving will help establish solid customer relationships and gain long-term competitive advantages for enterprises.
Overall, excellent customer service is a key factor for PCB manufacturers to stand out in a highly competitive market. Through timely response, professional knowledge, customized services, quality assurance and comprehensive after-sales support, PCB manufacturers can establish good cooperative relationships with customers and achieve a win-win situation.
FAQs
What application areas are glass packaging substrates suitable for?
Glass packaging substrate is a multi-functional electronic substrate suitable for various demanding applications. They are widely used in communications, medical, aerospace, military and industrial control fields. Because glass packaging substrates have excellent electrical, thermal and mechanical properties, they perform well in high-frequency, high-speed, high-density circuit designs.
What is the maximum size of a glass packaging substrate?
The size of glass packaging substrates is usually limited by manufacturing processes and equipment. Most glass packaging substrate manufacturers can provide customized solutions, manufacturing substrates in different sizes according to customers’ specific needs. Generally speaking, the size of the glass packaging substrate can reach tens of centimeters, but it can also be customized according to needs.
How long is the production cycle of glass packaging substrates?
The production cycle of glass packaging substrates depends on multiple factors, including order volume, complexity, material supply, and manufacturing processes. Generally speaking, the production cycle of customized glass packaging substrates may be longer, usually between weeks and months. The production cycle of standard specifications of glass packaging substrates may be shorter, generally between days and weeks. In order to ensure timely delivery and meet customer needs, manufacturers usually work closely with customers and adjust production plans based on actual conditions.
How reliable are glass packaging substrates?
Glass packaging substrates have excellent reliability and can operate stably under various harsh environmental conditions. Because glass substrates have good thermal stability and mechanical strength, glass packaging substrates perform well under conditions such as high temperature, high humidity, high vibration, and high pressure. In addition, manufacturers usually conduct strict quality control and testing of glass packaging substrates to ensure that they comply with international standards and customer requirements.
What is the cost of glass packaging substrates?
The cost of glass packaging substrates depends on several factors, including size, material, complexity, order quantity and delivery time. Customized and high-performance glass packaging substrates typically cost more because they require the use of high-quality materials and advanced manufacturing processes. The cost of mass-produced standard specification products is relatively low because costs can be reduced through bulk purchasing and optimization of the production process. Manufacturers usually provide detailed quotations and price plans based on customer needs to ensure that customers receive the most competitive prices and highest quality products.