Glass Materials Package Substrates Manufacturer.Ajinomoto GX92 Package Substrate Manufacturer is a leading company specializing in advanced electronic packaging materials. Known for its innovative Ajinomoto Build-up Film (ABF) substrates, the company excels in producing high-performance materials essential for semiconductor packaging. Their GX92 substrates are designed to meet the demands of next-generation electronic devices, ensuring superior reliability and efficiency. With cutting-edge technology and a commitment to quality, Ajinomoto GX92 Package Substrate Manufacturer is at the forefront of the semiconductor industry, driving advancements in electronic packaging solutions worldwide.
In the manufacturing of electronic products, the importance of PCB is self-evident. With the advancement of science and technology, the demand for high-performance and high-reliability substrate materials is increasing. In this context, Glass Materials Package Substrates have become a highly anticipated next-generation option. Its excellent thermal conductivity, low dielectric constant and good mechanical stability make it the first choice for various high-end electronic products. As the industry’s requirements for quality and performance increase, glass material encapsulated substrates will play an increasingly important role in the PCB field.
What are Glass Materials Package Substrates?
Glass Materials Package Substrates are a high-performance printed circuit board (PCB) that uses glass materials as the substrate. Compared with traditional substrate materials such as FR4 (fiberglass reinforced epoxy resin), glass material encapsulated substrates show significant advantages in many aspects and have become the first choice for many high-end electronic products.
First, the glass material encapsulated substrate has excellent thermal conductivity. In electronic devices, as power density increases, heat dissipation issues become increasingly important. Glass materials have high thermal conductivity, which can effectively conduct heat away from components and prevent overheating, thus improving the reliability and lifespan of electronic equipment. This is particularly important for equipment with high power density and high performance requirements, such as servers in data centers, high-performance computing equipment, and communication base stations.
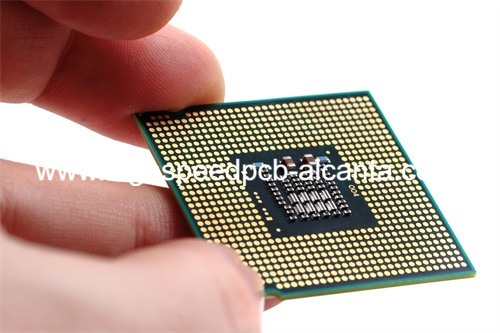
Glass Materials Package Substrates Manufacturer
Secondly, the low dielectric constant of glass materials gives them obvious advantages in high-frequency applications. Low dielectric constant can reduce losses in signal transmission and improve signal transmission speed and integrity. This is critical for high-speed data transmission and high-frequency signal processing. For example, in 5G communication equipment, optical fiber communication and high-frequency radar systems, signal integrity and speed are crucial, and glass material encapsulated substrates can significantly improve the performance of these devices.
In addition, the mechanical stability of the glass material encapsulated substrate is also better than that of traditional materials. Glass materials have high resistance to deformation and dimensional stability, allowing them to maintain their structural integrity in extreme environments. This is important for equipment that needs to operate in harsh conditions, such as sensors and control modules in automotive electronic systems, and aerospace equipment. These devices need to work reliably under high temperatures, vibrations and other harsh conditions, and the stability of the glass material-encapsulated substrate ensures their normal operation.
Finally, glass-encapsulated substrates also support high-density integration. This means that more functions and more complex circuit designs can be implemented in a smaller space, promoting the miniaturization and lightweight of electronic products. This is particularly important in portable electronic devices, smartphones and wearable devices, where the high-density integration capabilities of glass material-encapsulated substrates provide these devices with more design flexibility and room for innovation.
In short, as a high-performance PCB material, glass encapsulated substrate has gradually become an ideal choice for high-end electronic products due to its excellent thermal conductivity, low dielectric constant, excellent mechanical stability and high-density integration functions. In many fields such as communication equipment, high-performance computing, automotive electronics, and medical equipment, glass material-encapsulated substrates have broad application prospects and will play an increasingly important role in future electronic manufacturing.
Glass Materials Package Substrates design Reference Guide.
In modern electronics manufacturing, choosing the right substrate material is critical to achieving high-performance and high-reliability products. Glass Materials Package Substrates have become an ideal choice for many high-end applications due to their excellent performance characteristics. This article will provide a detailed design reference guide to help engineers and designers take full advantage of glass-encapsulated substrates.
Design planning
Before starting the design, you first need to clarify the functional requirements and application environment of the circuit. This includes determining electrical performance requirements, thermal management needs, and mechanical strength requirements. Due to its high thermal conductivity and low dielectric constant, glass material encapsulated substrates are particularly suitable for high-frequency and high thermal load applications, such as 5G communication equipment and high-performance computing systems.
Schematic design
Use advanced electronic design automation (EDA) software, such as Altium Designer or Cadence Allegro, for circuit schematic design. At this stage, special attention should be paid to component selection and interconnection methods to ensure that the performance requirements of the system are met. Glass-encapsulated substrates enable high-density integration, so more functions can be integrated into a limited space.
Component layout
During the PCB layout stage, it is necessary to make full use of the mechanical stability and thermal conductivity properties of the glass substrate. It is recommended to place high-power components where they can effectively dissipate heat, and to minimize the length of high-frequency signal paths to reduce signal loss and interference. Due to the stability of the glass material, a more compact component layout can be used in the design, further reducing the size of the PCB.
Wiring
Routing is one of the key steps in PCB design. The glass material encapsulated substrate has a low dielectric constant, which helps improve the speed and quality of signal transmission. When wiring, bending and crossing of signal lines should be minimized to ensure signal integrity. For high-speed signals, differential pair wiring and controlled impedance techniques are recommended to reduce signal reflections and crosstalk.
Thermal management design
Thermal management is an important part of high-performance electronic product design. The high thermal conductivity of glass material encapsulated substrates gives them significant advantages in thermal management. In the design, heat dissipation efficiency can be further improved by adding heat dissipation holes, heat sinks and heat conduction paths. For components with high power consumption, it is recommended to use thermal vias and heat dissipation copper layers for effective heat dissipation.
Design check and verification
After the design is completed, strict design rule checks (DRC) and electrical rules checks (ERC) are performed to ensure that the design complies with specifications and is error-free. In addition, signal integrity analysis tools can be used to simulate and verify key signals to ensure their reliability in actual operation.
Generate manufacturing files
Finally, Gerber files, drilling files, and assembly files are generated for manufacturing. These documents need to be accurate to ensure the manufacturing process runs smoothly. Maintain good communication with manufacturers to ensure design requirements are correctly implemented in production.
As a new generation of high-performance substrate materials, glass material encapsulated substrates have excellent thermal conductivity, low dielectric constant and good mechanical stability. Through reasonable design and optimization, its advantages can be fully utilized to provide a reliable foundation for high-end electronic products. We hope this design reference guide can help you effectively utilize glass materials to encapsulate substrates in practical applications and promote the continuous improvement of electronic product performance.
What material is used in Glass Materials Package Substrates?
Glass material encapsulated substrate is an emerging high-performance PCB substrate. Its unique feature is the use of glass material as the substrate. In traditional PCB manufacturing, common substrate materials include FR4 (glass fiber reinforced epoxy resin), etc., while glass material encapsulated substrates give PCBs better performance characteristics by using glass materials.
Glass material encapsulated substrates usually use high-purity glass materials, such as glass ceramics (Glass Ceramic) or glass fiber reinforced materials (Glass Fiber Reinforced). These materials have excellent thermal stability and mechanical strength, allowing them to maintain stability in complex environments. Compared with traditional substrate materials, glass materials have lower dielectric constants and higher thermal conductivity, which help improve the efficiency and reliability of electronic components.
In the manufacturing process of glass material encapsulated substrates, special glass material processes are usually used, such as glass sintering technology (Glass Sintering). Through high temperature treatment and pressure processing, the glass material and the metal wire layer are closely combined to form a solid substrate structure. . This manufacturing process not only ensures the stability and reliability of the substrate, but also enables higher integration density and more complex circuit designs.
Overall, the special material selection of the glass-encapsulated substrate gives it excellent performance advantages, making it an ideal choice for the next generation of high-performance PCBs. By combining the excellent properties of glass materials with advanced manufacturing processes, glass material encapsulated substrates are expected to play an important role in the field of electronic manufacturing and promote the continuous improvement of the performance and reliability of electronic products.
What size are Glass Materials Package Substrates?
As a new type of high-performance printed circuit board (PCB) substrate material, Glass Materials Package Substrates are diverse in size and shape and can meet the needs of various applications.
Standard size
The standard sizes of glass encapsulated substrates are usually similar to traditional PCBs, with common sizes ranging from small 10mm x 10mm to large 600mm x 600mm. These standard dimensions are suitable for most electronic products, including consumer electronics, communications equipment, and computer hardware. The selection of standard sizes is mainly based on the maturity and cost-effectiveness of the manufacturing process, which can meet the needs of mass production.
Custom size
In order to meet the needs of specific applications, glass material encapsulated substrates can also be customized according to customer requirements. Custom sizes can range in a very wide range, from a few millimeters to several meters. Custom sizes are often used in areas such as high-performance computing, advanced communications equipment, and specialty industrial equipment. Such applications place extremely high demands on PCB performance, requiring glass materials of specific sizes and shapes to encapsulate the substrate to achieve optimal electrical performance and mechanical stability.
Tiny size
In the fields of microelectronics and nanoelectronics, the size of glass material-encapsulated substrates can reach the micron level. This type of micro-sized substrates are mainly used in high-tech fields such as MEMS (microelectromechanical systems) and NEMS (nanoelectromechanical systems). The micro-sized glass material encapsulated substrate has extremely high precision and stability and can support the integration of tiny components and high-density wiring.
Large size
For applications that require large area circuits, such as large display panels, solar panels, and industrial control equipment, glass material encapsulated substrates can be made into large sizes. The manufacturing process of large-size substrates requires high requirements, and good flatness and consistency must be ensured to ensure circuit performance and reliability. The size of such substrates usually ranges from a few hundred millimeters to several meters and can be designed and manufactured according to specific needs.
Thickness
The thickness of the glass material encapsulating substrate is also an important parameter, usually between 0.1mm and 2mm. Thickness selection depends on application needs and mechanical performance requirements. Thinner substrates are suitable for applications that require flexibility, such as flexible electronics, while thicker substrates are suitable for applications that require high mechanical strength and durability, such as automotive electronics and industrial control equipment.
Different application scenarios have different size requirements for glass material encapsulated substrates. For example, in communication equipment, the substrate size needs to take into account high-frequency signal transmission performance and heat dissipation capabilities; in high-performance computing, the substrate size needs to support complex circuits and high-density integration; in medical equipment, the substrate size needs to comply with miniaturization and High precision requirements.
To sum up, the sizes of glass material encapsulated substrates are diversified and can adapt to the needs of different applications. Whether standard, custom, micro, or large, glass-encapsulated substrates provide excellent electrical performance and mechanical stability, making them ideal for modern electronics. With the continuous advancement of technology, the size and performance of glass material encapsulated substrates will be further improved, and the application range will be wider.
The Manufacturer Process of Glass Materials Package Substrates.
Glass Materials Package Substrates have become an ideal choice for high-end electronic products due to their excellent thermal properties, low dielectric constant and high mechanical stability. To achieve this high-performance substrate, the manufacturing process requires multiple complex and precise steps. The following is the detailed manufacturing process of the glass material encapsulated substrate.
Raw material preparation
The first step in manufacturing a glass material encapsulated substrate is to prepare high-purity glass raw materials. Commonly used glass types include quartz glass, borosilicate glass, etc. These materials have excellent electrical and mechanical properties. The raw materials are washed and dried to ensure their purity and surface-free contamination.
Substrate molding
The glass raw material is heated to a high temperature to melt it into a liquid state, and then formed into a glass sheet of the required thickness through a casting or drawing process. The formed glass sheet is annealed to eliminate internal stress and ensure its mechanical stability and dimensional accuracy.
Surface treatment
The formed glass substrate requires surface treatment to increase its adhesion to conductive materials such as copper foil. Common surface treatment methods include plasma treatment and chemical treatment, which can effectively remove organic and inorganic impurities on the glass surface and form an active layer on the glass surface.
Copper foil lamination
A layer of conductive copper foil is laminated on the surface of the treated glass substrate. The thickness of copper foil is generally 18μm or 35μm, depending on the design requirements. The lamination process is usually performed in a vacuum environment to prevent the generation of air bubbles and ensure a tight bond between the copper foil and the glass substrate.
Image transfer
The circuit pattern is transferred to the copper foil through an exposure and development process. This step requires the use of high-precision photolithography equipment to accurately project the designed circuit pattern onto the copper-clad glass substrate. After exposure, the unprotected copper foil is removed by a developer, leaving the desired circuit pattern.
Etching
Put the developed substrate into the etching solution to remove the unprotected copper foil and retain the circuit pattern. Commonly used etching solutions include ferric chloride, sulfuric acid and hydrogen peroxide. The etching process requires strict control of time and solution concentration to ensure the accuracy and consistency of the circuit pattern.
Hole machining
Drill through holes and blind holes on the glass substrate according to the design requirements. These holes are used for electrical connections and component mounting. Due to the high hardness of glass materials, laser drilling technology is often used to ensure precise apertures and smooth edges.
Plating and surface treatment
The drilled substrate is electroplated to deposit a layer of copper on the hole wall and circuit pattern to improve its conductivity and reliability. Surface treatments such as tin plating, gold plating or other protective coatings are then applied to protect the copper layer from oxidation and corrosion.
Solder Mask and Silk Screen
A layer of solder mask is applied to the circuit pattern, usually a green or other colored coating, to protect the circuit from the external environment and prevent short circuits during soldering. Finally, marks and text information are printed on the substrate through a silk screen process for easy identification and installation.
Testing and Inspection
The manufactured glass material encapsulated substrate needs to undergo strict electrical and optical testing to ensure that it meets the design requirements and quality standards. Common test methods include electrical continuity testing, insulation resistance testing, and visual inspection.
Through the above steps, the manufacturing process of the glass material encapsulated substrate from raw materials to finished products is realized. Every step is critical, ensuring high performance and reliability of the final product. As technology continues to advance, glass material encapsulated substrates will play an important role in more high-end electronic applications.
The Application area of Glass Materials Package Substrates.
Glass Materials Package Substrates (Glass Materials Package Substrate), as an emerging high-performance PCB material, has shown broad application prospects in various fields. It is not only widely used in communications, computing and automotive fields, but also shows great potential in industries such as medical equipment.
First, in the field of communication equipment, the high performance and reliability of glass material-encapsulated substrates make it an ideal choice for base stations and optical fiber communication equipment. In terms of high-speed data transmission and signal processing, glass substrates can provide excellent signal integrity and stability, thereby ensuring the stable operation of communication equipment.
Secondly, in the field of high-performance computing, such as large-scale computing equipment such as data center servers and supercomputers, glass material encapsulated substrates have also shown their unique advantages. These devices usually need to process large amounts of data and complex computing tasks, and have extremely high requirements on the performance and stability of the PCB. The high thermal conductivity and low dielectric constant of the glass substrate can effectively improve the performance and reliability of the device, while supporting more High-density circuit integration.
In the field of automotive electronics, with the development of automobile intelligence and electrification, glass material encapsulated substrates are gradually favored by automobile manufacturers and electronic suppliers. For example, PCBs used in vehicle infotainment systems and autonomous driving controllers need to maintain stability in harsh environments such as high temperature and high humidity. The excellent performance of glass substrates can effectively meet these challenges and ensure the reliable operation of automotive electronic systems.
In addition, glass material encapsulated substrates also have broad application prospects in the field of medical equipment. Medical imaging equipment such as MRI and CT have extremely high performance requirements for PCBs, and the stability and reliability of glass substrates can meet these requirements; at the same time, in medical equipment such as vital sign monitoring instruments, glass substrates can also provide stable signals transmission and reliable electrical connections to ensure the accuracy and reliability of medical equipment.
In summary, glass material encapsulated substrate, as an emerging high-performance PCB material, has broad application prospects and has shown great potential in the fields of communications, computing, automobiles, and medical care. With the continuous advancement of technology and the continuous expansion of applications, it is believed that glass substrates will play an important role in more fields and promote the development and progress of the entire industry.
What are the advantages of Glass Materials Package Substrates?
Glass Materials Package Substrates, as the next generation PCB substrate material, have many advantages, making them very popular in the field of electronic manufacturing. The following are the main advantages of glass material encapsulation substrates:
First, glass materials have excellent thermal conductivity properties. Compared with traditional FR4 substrate materials, glass materials have higher thermal conductivity and can dissipate heat more effectively. This feature is particularly important for high-power density electronic equipment, which can effectively improve the stability and reliability of the equipment and extend its service life.
Secondly, the glass material encapsulating substrate has a lower dielectric constant. A low dielectric constant means less loss when signals are transmitted through the material, helping to improve the quality and speed of signal transmission. This is particularly critical for high-frequency and high-speed data transmission applications, ensuring signal integrity and accuracy.
In addition, the mechanical stability of glass materials is also one of its advantages. The glass material has a stable structure and strong resistance to deformation. It can maintain the shape stability of the PCB under complex environmental conditions and reduce the risk of failure caused by mechanical stress. This makes glass-encapsulated substrates outstanding in applications requiring high reliability and long-term stability.
In addition, the glass material encapsulated substrate also supports high-density integration. Its compact structure enables the integration of more complex circuits and functions, helping to achieve miniaturization and lightweighting of products. This is crucial for the compact design and high performance requirements increasingly pursued by modern electronic products.
To sum up, glass material encapsulated substrates have become a new favorite in the field of electronic manufacturing due to their excellent thermal conductivity, low dielectric constant, good mechanical stability and high-density integration. As the performance and reliability requirements of electronic products continue to increase, glass material encapsulated substrates will have wider application prospects in the future and inject new vitality into the development of the electronics industry.
FAQ
What is the difference between Glass Materials Package Substrates and traditional substrate materials?
Glass Materials Package Substrates use glass materials as substrates, which have better thermal conductivity, lower dielectric constant and better mechanical stability than traditional FR4 and other materials. This makes it perform better in high-performance electronic products.
What types of electronic products are Glass Materials Package Substrates suitable for?
Glass Materials Package Substrates are suitable for a wide range of electronic product types, including communication equipment, high-performance computing equipment, automotive electronics, medical equipment, and more. Its excellent performance makes it outstanding in areas requiring high-density integration and reliability.
What is the manufacturing process of Glass Materials Package Substrates?
Manufacturing Glass Materials Package Substrates typically includes steps such as substrate preparation, pattern transfer, etching, drilling, plating, and surface treatment. The manufacturing process is similar to traditional substrate manufacturing, but requires greater precision and temperature control.
How reliable are Glass Materials Package Substrates?
Glass Materials Package Substrates have excellent reliability, and their stable mechanical properties and good thermal conductivity ensure the long-term stable operation of electronic products. It performs well in a variety of environmental conditions and meets stringent application requirements.
How much does Glass Materials Package Substrates cost?
Glass Materials Package Substrates may be more expensive than traditional substrate materials, but their performance advantages can significantly improve product performance and reliability, making them highly cost-effective in some high-end applications.