Flip Chip BGA Substrate Manufacturer.As a Flip Chip BGA Substrate Manufacturer, we specialize in crafting advanced interconnection solutions for semiconductor devices. Our expertise lies in designing and producing high-quality substrates that enable efficient mounting and connection of integrated circuits onto PCBs. With a focus on innovation and precision engineering, we deliver substrates that meet the demands of modern electronics, ensuring optimal performance and reliability.
With the rapid development of electronic technology, Flip Chip BGA (Ball Grid Array) substrate, as a key component of modern electronic equipment, is gradually becoming the focus of the industry. This article will delve into the key technologies of Flip Chip BGA substrate to provide readers with a comprehensive understanding and reference.
What is Flip Chip BGA Substrate?
Flip Chip BGA Substrate is an advanced packaging technology commonly used in semiconductor devices and electronic equipment. It uses Flip Chip technology and BGA (Ball Grid Array) packaging structure to provide a more efficient and reliable solution for the connection and layout of electronic components.
In Flip Chip BGA Substrate, the chip is flip-chip mounted directly on the substrate instead of the traditional substrate-facing mounting method. This means that the chip’s connection pins (usually metal solder balls) are connected to contact points on the substrate, forming a dense network of connections. This design enables a more compact circuit layout and improves circuit integration and performance.
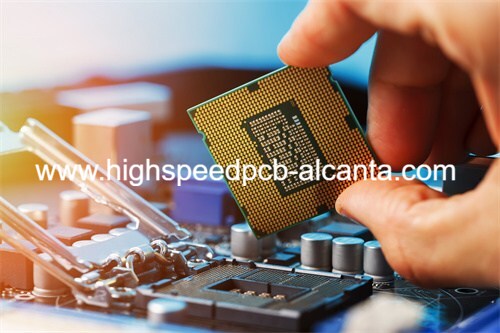
Flip Chip BGA Substrate Manufacturer
The main components include substrate materials, conductive layers, solder balls and packaging layers. Substrate materials usually use high-performance dielectric materials, such as fiberglass-reinforced epoxy (FR-4) or polyimide (PI), to provide good mechanical and electrical properties. The conductive layer is made of copper and builds the circuit paths and connection points. Solder balls play an important role in connecting the chip and the substrate. They can carry electrical signals and provide reliable connections. The encapsulation layer is used to protect the chip and connection points, improving overall reliability and durability.
Flip Chip BGA Substrate is widely used in various fields, including consumer electronics, communication equipment, automotive electronics, etc. Its advantages include high-density layout, excellent electrical performance and good thermal management capabilities, making it an indispensable part of modern electronic equipment.
Overall, the development of Flip Chip BGA Substrate technology has promoted progress and innovation in the electronics industry, providing strong support for higher-performance and more reliable electronic devices.
Flip Chip BGA Substrate design Reference Guide.
Flip Chip BGA (Ball Grid Array) substrate design is a key part of modern electronic equipment. This guide is intended to provide designers with a comprehensive Flip Chip BGA substrate design reference to ensure design reliability, performance and manufacturability.
Before designing Flip Chip BGA substrate, designers need to understand basic knowledge, including Flip Chip technology principles, BGA packaging structure, substrate material selection, etc. This knowledge lays the foundation for design and helps to understand the various considerations in the design process.
A series of design specifications need to be followed during the design process, including layout and routing rules, minimum line width/line spacing, pad size, safety spacing, etc. Proper compliance with specifications ensures that the design meets electrical performance, thermal management, and manufacturability requirements.
Choosing the right substrate material is critical. Common substrate materials include FR-4, polyimide (PI), high-frequency dielectric materials, etc. Different application scenarios require substrate materials with different properties to meet electrical, thermal and mechanical requirements.
Flip Chip BGA substrate design usually adopts a multi-layer structure. Designers need to reasonably plan the layer layout to ensure the separation of signal and power planes and the continuity of ground planes to improve electrical performance and anti-interference capabilities.
Signal integrity needs to be paid attention to during the design process, including impedance matching, signal transmission path optimization, signal lead length control, etc. By optimizing the design, the signal transmission rate and stability can be improved.
Flip Chip BGA substrate design needs to consider good thermal management, including reasonable layout of radiators, ventilation holes, heat dissipation copper foil, etc., to ensure stable operating temperatures of the chip and circuit board and improve system performance and reliability.
The feasibility of manufacturing must be considered during the design process, including the selection of parameters such as board thickness, aperture, pad spacing, etc., to ensure that the design can smoothly enter the manufacturing stage and meet production requirements.
Designers can use professional design software, such as Altium Designer, Cadence Allegro, etc., to design Flip Chip BGA substrates. These tools provide a rich library of features and resources to help improve design efficiency and quality.
Flip Chip BGA substrate design is a complex and critical task that requires designers to have deep professional knowledge and rich experience. This guide provides a series of design references, hoping to help designers better cope with challenges and achieve successful design implementation.
What material is used in Flip Chip BGA Substrate?
Flip Chip BGA substrates are constructed from a variety of materials, each of which plays an important role to ensure its performance and reliability.
First of all, the substrate material is the main body of the Flip Chip BGA substrate. Commonly used substrate materials include fiberglass reinforced epoxy resin (FR-4) and polyimide (PI). FR-4 material has good mechanical strength and heat resistance and is suitable for most application scenarios, while polyimide has higher heat resistance and chemical resistance and is suitable for applications in high-temperature environments or special process requirements.
Secondly, the metal layer is a key component in building the conductive path of the Flip Chip BGA substrate. Copper is usually used as the metal layer material. It has excellent electrical conductivity and can be processed into various shapes and thicknesses through different processes to meet the requirements of different applications. The thickness and structural design of the metal layer are critical to the substrate’s electrical conductivity and thermal management capabilities.
In addition, solder balls are an important part of connecting the chip and the substrate, and their material and size directly affect the connection quality and reliability. Commonly used solder ball materials include tin-lead alloys and lead-free solders. Tin-lead alloy solder balls have good welding performance and mechanical strength, but are limited by environmental protection requirements, while lead-free solder is the future development trend and has the advantages of environmental protection and high reliability.
To sum up, the material selection of the Flip Chip BGA substrate is crucial. The characteristics of the substrate material, metal layer, solder ball and other components need to be comprehensively considered to meet the performance, reliability and environmental requirements of different application scenarios.
What size are Flip Chip BGA Substrate?
The size of Flip Chip BGA substrate varies depending on application scenarios and design requirements. Typically, they can come in a variety of sizes and shapes to meet the requirements of different devices and systems. In electronic devices, the size of Flip Chip BGA substrates is often affected by space constraints and performance requirements.
Generally speaking, the size of Flip Chip BGA substrate usually ranges from a few millimeters to tens of millimeters, depending on factors such as chip size, pin density, and connector layout. For example, in small electronic devices such as smartphones or tablets, Flip Chip BGA substrates may be relatively small to fit into the compact internal space of the device; whereas in large systems such as servers, network equipment, or industrial control systems, Flip Chip BGA substrates may May be larger to accommodate more circuits and components.
In addition, Flip Chip BGA substrates can also come in various shapes, usually rectangular or square, but can also be customized into other shapes, such as circular or irregular shapes, according to specific design requirements.
In general, the size and shape of the Flip Chip BGA substrate are determined based on specific applications and design requirements, and can be flexibly adjusted while ensuring performance and reliability.
The Manufacturer Process of Flip Chip BGA Substrate.
The manufacturing process of Flip Chip BGA (Ball Grid Array) substrate is a complex and precise process involving multiple key steps to ensure that the quality and performance of the final product meet the requirements.
First, the manufacturing process begins with the substrate preparation stage. At this stage, choosing the right substrate material is crucial. Common substrate materials include fiberglass-reinforced epoxy (FR-4) and polyimide (PI), whose mechanical and electrical properties are critical to the performance of the final product. Surface treatment of the substrate is also essential to ensure that the metal layer can adhere firmly.
Next comes the metal layer preparation stage. Forming conductive paths on the substrate surface is one of the key steps in manufacturing Flip Chip BGA substrates. Commonly used methods include chemical etching or copper plating processes. Through these processes, the metal layer is accurately formed on the surface of the substrate for subsequent welding processes.
Then comes the solder ball mounting stage. Precise placement of solder balls on the substrate is a critical step to ensure a good connection between the chip and the substrate. The size and position of the solder balls need to be precisely controlled to ensure alignment and connection quality with the chip pins.
Next comes the chip flipping and mounting stage. One of the core technologies of Flip Chip BGA substrate is to flip the chip directly and accurately position it on the substrate. During this step, the correct positioning of the chip is critical to ensure proper connection to the solder balls.
This is followed by the welding solidification phase. The solder balls are solidified through methods such as hot pressing or hot air to ensure a stable and reliable connection between the chip and the substrate. At this stage, temperature and pressure control are crucial to ensure welding quality.
Finally comes the testing and quality control phase. The manufactured Flip Chip BGA substrates are fully tested and quality controlled to ensure compliance with specifications and requirements. This includes visual inspection, dimensional measurements, electrical testing, etc. to ensure product performance and reliability are up to standard.
Overall, the manufacturing process of Flip Chip BGA substrates involves multiple critical steps, each of which requires precision operations and strict quality control to ensure the quality and performance of the final product.
The Application area of Flip Chip BGA Substrate.
Flip Chip BGA substrate is widely used in various fields. Its high performance, high reliability and compact packaging form make it the first choice for many electronic devices. The following are the main application areas of Flip Chip BGA substrates:
Consumer electronics: Consumer electronics such as smartphones, tablets, and digital cameras are one of the main application areas of Flip Chip BGA substrates. Due to the stringent requirements for performance, volume and power consumption of consumer electronics, the high-density layout and excellent electrical performance of Flip Chip BGA substrates make it an ideal choice for these devices.
Communication: Flip Chip BGA substrate plays an important role in communication equipment, such as base station equipment, routers, optical fiber communication equipment, etc. These devices require high-speed signal transmission and stability, and the short-distance connection and good signal transmission performance of the Flip Chip BGA substrate can meet these requirements.
Automotive electronics: Many electronic systems in modern cars, such as in-car navigation systems, in-car entertainment systems and intelligent driving assistance systems, use Flip Chip BGA substrates. The automotive environment has high requirements for high temperature resistance and vibration resistance of electronic equipment, and the excellent thermal management and reliability of Flip Chip BGA substrate make it an ideal choice for the automotive electronics field.
Industrial control: Industrial control equipment and automation systems are also one of the important application areas of Flip Chip BGA substrates. These devices often require high performance and reliability, and the high-density layout and excellent electrical performance of Flip Chip BGA substrates can meet the stringent requirements of industrial environments.
Medical equipment: The field of medical equipment has extremely high requirements for the reliability and stability of electronic equipment, and Flip Chip BGA substrates are widely used in high-end medical equipment such as medical imaging equipment and diagnostic equipment due to their excellent performance and reliability.
To sum up, Flip Chip BGA substrate has a wide range of applications in various fields. Its high performance and reliability make it a key component of modern electronic equipment, driving the development and innovation of various industries.
What are the advantages of Flip Chip BGA Substrate?
As an advanced form of modern electronic packaging technology, Flip Chip BGA substrate (Ball Grid Array) has many significant advantages and provides key support for the performance and reliability of electronic equipment.
First, the Flip Chip BGA substrate achieves higher integration and density. By flip-mounting the chip directly onto the substrate and using ball connection points for connections, a more compact circuit layout can be achieved. This compact design makes the distance between electronic components shorter, which helps reduce the size of the circuit board, making the entire device thinner, lighter and more portable.
Secondly, Flip Chip BGA substrate has excellent electrical properties. Since the connection distance between the chip and the substrate is shorter, the resistance and delay of signal transmission are smaller, which is beneficial to improving the signal transmission rate and stability. This is particularly important for high-speed data transmission and processing application scenarios, such as communication equipment, computer servers, etc.
In addition, Flip Chip BGA substrate also has good thermal management properties. Since the chip is mounted directly on the substrate, heat can be conducted and dissipated more efficiently, thus lowering the operating temperature of the entire system. This helps improve system performance and reliability, extends equipment life, and reduces the impact of heat on other components.
In addition, the manufacturing process of Flip Chip BGA substrate is relatively mature and has high production efficiency and consistency. Through modern automated production lines and quality control technology, large-scale production can be achieved and the stability and reliability of product quality can be guaranteed. This provides manufacturers of various types of electronic equipment with reliable solutions and reduced manufacturing costs.
To sum up, Flip Chip BGA substrate has many advantages such as high integration, excellent electrical performance, good thermal management performance and mature manufacturing process. It is one of the indispensable key technologies in modern electronic equipment.
FAQ
What is Flip Chip BGA substrate?
Flip Chip BGA (Ball Grid Array) substrate is a packaging technology, which is characterized by flipping the chip directly onto the substrate and connecting it to the substrate through solder balls. This design optimizes circuit layout and signal transmission paths, improving performance and reliability.
What is the manufacturing process of Flip Chip BGA substrate?
The process of manufacturing Flip Chip BGA substrate includes steps such as substrate preparation, metal layer preparation, solder ball installation, chip flip installation, solder curing, testing and quality control. These steps ensure the quality and reliability of the substrate.
What fields are Flip Chip BGA substrates suitable for?
Flip Chip BGA substrates are widely used in consumer electronics, communications, automotive electronics and other fields. For example, smartphones, base station equipment, car navigation systems, etc. all use Flip Chip BGA substrate technology.
How to choose a suitable Flip Chip BGA substrate material?
When selecting Flip Chip BGA substrate materials, you need to consider factors such as its mechanical properties, electrical properties, and application environment. Common substrate materials include fiberglass reinforced epoxy (FR-4) and polyimide (PI).
How is Flip Chip BGA substrate different from other packaging technologies?
Compared with traditional packaging technology, Flip Chip BGA substrate uses a method of directly flipping the chip and mounting it on the substrate. It has higher integration and performance advantages and is suitable for high-density, high-performance electronic equipment.