Flip Chip Ball Grid Array Substrate Manufacturer.A Flip Chip Ball Grid Array Substrate Manufacturer specializes in crafting advanced substrates essential for cutting-edge semiconductor packaging. Employing precision engineering and innovative techniques, they produce intricate arrays of interconnected circuits on substrates, facilitating efficient signal transmission and thermal management in electronic devices. With a keen focus on quality and reliability, they ensure their substrates meet stringent industry standards, enabling seamless integration into diverse applications, from high-performance computing to consumer electronics. As pioneers in their field, they continually push the boundaries of technology, driving progress in the semiconductor industry.
With the rapid development of electronic technology, Flip Chip Ball Grid Array Substrate (FCBGA), as a key printed circuit board (PCB) type, is attracting increasing attention. FCBGA plays an indispensable role in high-performance electronic devices through its unique design and manufacturing process. This article will conduct an in-depth study of the design principles, manufacturing processes and applications of FCBGA in various industries to help readers fully understand the core concepts and application prospects of this important technology.
What is Flip Chip Ball Grid Array Substrate?
Flip Chip Ball Grid Array Substrate (FCBGA) is an innovative printed circuit board (PCB) whose design and structure provide an ideal platform for high-density integrated circuit (IC) packaging. Compared with traditional packaging technology, FCBGA uses flip-chip packaging technology to directly connect the chip to the PCB substrate through a solder ball array, thereby achieving a more compact and higher-performance electronic device design.
In FCBGA, the chip is placed upside down on the substrate, and its electrical connections are connected to the circuits on the substrate through an array of solder balls. This design makes the chip connection more compact and reliable, while also reducing the length of the signal transmission path and improving signal transmission speed and performance. In addition, FCBGA can also achieve higher integration, integrate more functions into a smaller space, and provide greater flexibility for the design of electronic products.
By adopting FCBGA technology, electronic equipment manufacturers can achieve higher performance and smaller size product designs. For example, in mobile devices such as smartphones and tablets, FCBGA can achieve a more compact design and improve the performance and battery life of the device. In high-performance computing fields such as servers and network equipment, FCBGA can achieve higher integration and faster data processing speeds, improving the overall performance of the equipment.
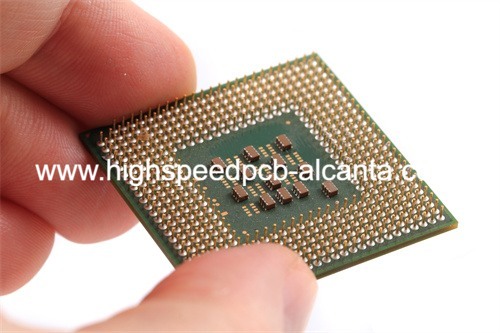
Flip Chip Ball Grid Array Substrate Manufacturer
In addition, FCBGA also has good thermal management performance. Since the chip is directly connected to the PCB substrate, heat can be transferred to the substrate more efficiently and dissipated through components such as heat sinks and cooling fans, thereby maintaining stable performance of the device.
In short, Flip Chip Ball Grid Array Substrate (FCBGA), as an advanced printed circuit board technology, provides electronic equipment manufacturers with higher performance, more compact and more reliable design solutions. As technology continues to advance, FCBGA will continue to play an important role and promote the continuous improvement of the performance and functionality of electronic devices.
Flip Chip Ball Grid Array Substrate design Reference Guide.
Flip Chip Ball Grid Array Substrate (FCBGA) is a critical printed circuit board (PCB) type whose design is critical to the performance of modern electronic devices. The following is a reference guide on FCBGA design, designed to help readers gain an in-depth understanding of its design principles and best practices.
Chip layout
When designing an FCBGA, the layout of the chip is crucial. Optimized chip layout can ensure the stability and reliability of signal transmission and maximize the performance of the device. A reasonable layout should consider factors such as the spacing between chips, the length of signal lines, and interlayer connections.
Solder ball array arrangement
The layout of the solder ball array directly affects the quality and performance of the connection between the chip and the substrate. By carefully designing the arrangement of the solder ball array, better electrical connections and thermal management can be achieved. Reasonable solder ball arrangement should take into account factors such as the chip’s pin layout, signal transmission path, and heat dissipation requirements.
Electrical connections
In FCBGA design, the stability of electrical connections is crucial. By using appropriate design and materials, the reliability of electrical connections can be ensured and the bit error rate and distortion rate of signal transmission can be reduced. Signal integrity and electrical characteristics requirements should be considered in the design to ensure that the device performs to the expected level.
Thermal management
Due to the high integration and high performance requirements of modern electronic equipment, thermal management has become a factor that cannot be ignored in FCBGA design. Through reasonable heat dissipation design and material selection, the operating temperature of the equipment can be effectively reduced and its service life extended. Factors such as chip power consumption, heat dissipation surface area, and heat dissipation methods should be taken into consideration in the design.
Design tools and software
When designing FCBGA, appropriate design tools and software are essential. Various professional PCB design software and simulation tools can help designers complete design tasks quickly and efficiently, and optimize the performance and reliability of equipment. When choosing a design tool, consider factors such as its functionality, ease of use, and compatibility with other software.
By following the above guidelines, designers can better understand and apply FCBGA technology to maximize device performance and improve reliability. At the same time, continuous learning and exploration of new design methods and technologies are also the key for designers to continuously improve their abilities and levels.
What material is used in Flip Chip Ball Grid Array Substrate?
Flip Chip Ball Grid Array Substrate (FCBGA), a key printed circuit board (PCB) type, uses specific materials in its manufacturing process to ensure its performance and reliability. The following will introduce the materials commonly used in FCBGA:
Substrate material
The substrate of FCBGA usually uses fiberglass reinforced epoxy resin (FR4) as the main material. FR4 has good mechanical and electrical properties and is suitable for high-density circuit layouts and complex manufacturing processes. In addition, some FCBGAs for special applications may use polyimide (PI) or metal base materials to meet specific performance requirements.
Metal layer
In the manufacture of FCBGA, the substrate is typically coated with a layer of metal (usually copper) that is used to form electrical connections and contact points for solder balls. This layer of metal undergoes precision machining and chemical treatment during the manufacturing process to ensure welding reliability and connection stability.
Solder ball material
Solder balls are the key component connecting the chip to the substrate, usually using tin-lead alloy or lead-free solder. These solders have good electrical conductivity and solderability, allowing for reliable soldering connections through ball-shaped structures during the manufacturing process.
Packaging materials
Chip packaging in FCBGA usually uses materials such as epoxy resin (Epoxy) or silicone (Silicone). These packaging materials have excellent mechanical strength and thermal stability, which can protect the chip from mechanical damage and environmental effects.
Protective layer material
In order to enhance the durability and environmental adaptability of FCBGA, a protective layer is usually coated on its surface. This protective layer usually uses polyimide film (Polyimide Film) or polymer film (Polymer Film) to prevent moisture, dust and chemical substances from corroding the circuit.
By rationally selecting and optimizing these materials, it is possible to ensure that FCBGA has good electrical properties, mechanical strength and environmental adaptability, thereby meeting the needs of various application scenarios.
What size are Flip Chip Ball Grid Array Substrate?
Flip Chip Ball Grid Array Substrate (FCBGA) dimensions vary depending on its application and requirements. Typically, the size of an FCBGA is determined by the size and density of the chip package, as well as the required electrical connections and thermal performance.
As with most electronic devices, FCBGAs are usually smaller in size to accommodate the compact design trend of modern electronics. For small devices such as smartphones, tablets, and portable consumer electronics, FCBGAs may be only a few millimeters to a few centimeters in size. This small size FCBGA can achieve high integration and performance optimization in a limited space, thus meeting consumer demand for lightweight and thin devices.
However, in some applications, a larger size FCBGA is required to accommodate more chips or implement more complex functions. For example, in areas such as network servers, industrial control systems, and communication infrastructure, larger FCBGAs are usually required to meet high-performance processing requirements and more complex circuit designs. These large-sized FCBGAs may be tens of centimeters or larger in size to accommodate multiple chips and complex electrical connections.
Therefore, the size of FCBGA can vary from a few millimeters to tens of centimeters, depending entirely on the needs and design goals of the specific application. Whether it is a small-sized portable device or a large-scale industrial system, FCBGA can provide critical support for the performance and functionality of electronic devices through its compact design and highly integrated features.
The Manufacturer Process of Flip Chip Ball Grid Array Substrate.
The manufacturing process of Flip Chip Ball Grid Array Substrate (FCBGA) involves multiple precision steps, each of which is critical to the quality and performance of the final product.
The first is substrate preparation. The process of manufacturing an FCBGA begins with selecting an appropriate substrate material, typically high-performance fiberglass-reinforced epoxy (FR4) or other specific materials. The preparation of the substrate includes steps such as cutting, cleaning, and surface treatment to ensure that its surface is smooth, clean, and has good surface properties.
Next comes the fabrication of the solder ball array. The solder ball array is a key component connecting the chip and the substrate. They need to have consistent size, shape and arrangement to ensure a stable and reliable connection. The process of manufacturing solder ball arrays involves precision metal forming, ballooning, alignment and mounting.
Then comes chip packaging. During the chip packaging stage, the flip chip is precisely placed on the substrate and connected to the solder ball array by soldering. This step requires highly precise equipment and process control to ensure that the chip is properly aligned and precisely connected to the solder balls.
Next comes welding. Once the chip is properly packaged on the substrate, the next step is to permanently connect the chip to the substrate through a soldering process. The accuracy and stability of the welding process are crucial to ensuring the quality of the welding connection, which directly affects the reliability and performance of FCBGA.
Finally comes the test. After manufacturing, the FCBGA needs to undergo rigorous testing procedures to verify its electrical connections, signal integrity, and functional performance. Testing includes visual inspection, electrical testing, thermal cycle testing, etc. to ensure that each FCBGA meets specifications.
In short, the manufacturing process of FCBGA requires precision equipment, precise process control and strict quality management to ensure that the final product has high quality, stability and reliability. Only through these fine steps and controls can high-quality FCBGA products that meet market demand be produced.
The Application area of Flip Chip Ball Grid Array Substrate.
As an advanced printed circuit board (PCB) type, FCBGA is widely used in various fields, providing key support for electronic equipment in communications, computers, medical, automotive and other industries. In the field of communications, FCBGA is used to manufacture base station equipment, communication network equipment and mobile communication terminals to ensure the stability and reliability of data transmission. In the computer field, FCBGA is widely used in servers, network equipment and data centers, supporting the development of key technologies such as cloud computing and big data processing. In the medical field, FCBGA is used in medical imaging equipment, patient monitoring equipment and medical diagnostic equipment, providing technical support for the development of the medical industry and improving the accuracy and efficiency of medical diagnosis. In the automotive field, FCBGA is used in key components such as automotive electronic control units (ECUs), in-car entertainment systems, and driving assistance systems, improving the safety, comfort, and intelligence of automobiles. In general, as an advanced electronic packaging technology, FCBGA’s applications not only cover traditional fields such as communications, computers, medical care, and automobiles, but also play an important role in emerging fields such as artificial intelligence and the Internet of Things, promoting the Scientific and technological progress and industrial development in modern society.
What are the advantages of Flip Chip Ball Grid Array Substrate?
FCBGA (Flip Chip Ball Grid Array Substrate), as an advanced printed circuit board (PCB) technology, has shown many advantages in modern electronic manufacturing. Compared with traditional IC packaging technology, its unique features are reflected in the following aspects: aspects:
Higher integration
FCBGA effectively reduces the space requirements of the circuit by flipping the chip and connecting it directly to the substrate. This compact design makes it possible to accommodate more functions and components in a limited space, thereby achieving a higher level of integration.
Smaller package size
Because FCBGA uses a flip-chip packaging method, and the solder ball array is connected to the bottom of the substrate, compared with traditional packaging technology, FCBGA packaging is more compact and smaller in size, which can meet the needs of thin, light and miniaturized electronic equipment. design requirements.
Better cooling performance
FCBGA’s solder ball array connects the chip and the substrate, directly conducts the heat from the chip to the substrate, and then effectively dissipates the heat through a radiator and other methods. Compared with the common gold wire connections in traditional packaging technology, FCBGA has better heat dissipation performance, which helps maintain the stable operating temperature of the chip and improves the reliability and performance of electronic equipment.
More stable electrical connection
FCBGA uses a solder ball array to connect the chip and the substrate. The solder contact area is large and the stability is high. It can effectively reduce the impact of resistance, inductance, etc. on signal transmission, ensuring the stability and reliability of the circuit. Compared with traditional gold wire connections, solder ball connections are less susceptible to external vibration and impact, thereby improving the stability of electrical connections.
To sum up, FCBGA is very popular in today’s electronic manufacturing. Its advantages such as high integration, small package size, excellent heat dissipation performance and stable electrical connection provide more flexibility and flexibility for the design and manufacturing of electronic equipment. Efficient solutions promote the continuous progress and development of electronic technology.
FAQ
How is FCBGA different from other IC packaging technologies?
FCBGA uses flip chip packaging technology to connect the chip and PCB substrate through a solder ball array, while other IC packaging technologies may use plug-in or surface mount technology. The main differences of FCBGA are its more compact design, higher integration and better heat dissipation performance.
What are the advantages of FCBGA?
FCBGA has multiple advantages, including high integration, small package size, excellent heat dissipation performance, stable electrical connection, good signal integrity, etc. These advantages make FCBGA the packaging technology of choice for many high-performance electronic devices.
What factors need to be considered in the design of FCBGA?
When designing an FCBGA, factors such as chip layout, solder ball array arrangement, electrical connections, thermal management, and signal integrity need to be considered. By optimizing the design, better performance and reliability can be achieved.
What steps does the FCBGA manufacturing process include?
The manufacturing process of FCBGA involves multiple steps such as substrate preparation, solder ball array production, chip packaging, welding, and testing. Each step requires precise process control and quality management to ensure the quality and performance of the final product.
What application fields is FCBGA suitable for?
FCBGA is widely used in communications, computers, medical, automotive and other fields. They are used to manufacture various types of electronic devices such as smartphones, servers, medical imaging equipment, and automotive electronic systems.