What is FCBGA (ABF) Substrate?
FCBGA (ABF) Substrate Manufacturer.”FCBGA (ABF) Substrate Manufacturer” refers to a company specializing in the production of Flip Chip Ball Grid Array substrates using advanced build-up technologies.
FCBGA (ABF) substrate, the full name is Flip Chip Ball Grid Array (Ajinomoto Build-up Film) substrate, is an advanced semiconductor packaging solution. It uses Ajinomoto Build-up Film (ABF) as the main dielectric material, which has excellent electrical properties and mechanical strength and is widely used in the packaging of high-density electronic components.
In FCBGA technology, flip chip (Flip Chip) is directly mounted on the metal solder ball array of the substrate, which can significantly increase connection density and circuit speed compared with traditional packaging methods. ABF materials not only provide good signal transmission and electrical isolation performance, but also effectively reduce the size and weight of circuit boards, making them suitable for applications that require a high degree of integration and miniaturization.
FCBGA (ABF) substrates are widely used in computers, communication equipment, consumer electronics, medical equipment, aerospace and other fields due to their reliable performance and flexible design features. They not only support the design of complex circuits, but also meet the needs of applications with high electrical performance and thermal management requirements.
In short, FCBGA (ABF) substrate has become an indispensable and important part of the modern electronics industry with its advanced technology and diversified application advantages, promoting the development of electronic products towards higher performance and smaller size.
FCBGA (ABF) Substrate design Reference Guide.
FCBGA (ABF) Substrate Design Reference Guide is a comprehensive manual specially written for engineers and designers engaged in FCBGA substrate design. This guide is dedicated to providing the necessary information and guidance to help professionals design and develop efficient and reliable FCBGA substrates.
In the modern electronics industry, FCBGA (ABF) substrates are popular for their excellent performance in high-density packaging and high-performance applications. To maximize its potential, designers need to master a set of best practices and design rules. This guide details these key aspects and provides the necessary tools and technical support.
During the design process of FCBGA (ABF) substrates, it is crucial to follow best practices. These practices include, but are not limited to: proper floor planning to minimize signal interference and electromagnetic interference; proper power and ground plane design to ensure stable power and grounding; and optimized routing paths to minimize signal delays and losses.
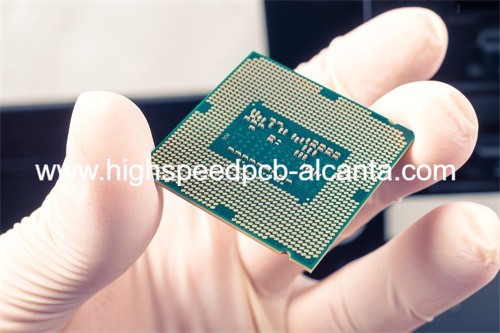
FCBGA (ABF) Substrate Manufacturer
Design rules cover key parameters such as minimum line width/space, aperture size, board thickness, and layer spacing. These rules not only ensure excellent electrical performance, but also help simplify the manufacturing process and improve reliability.
In modern electronic design, the use of professional software tools is indispensable. This guide introduces some popular PCB design software and details how to utilize these tools to implement complex FCBGA substrate layout and routing. These tools not only speed up the design cycle, but also help designers perform simulation analysis and 3D layout verification to ensure the correctness and reliability of the design.
By rationally selecting materials, optimizing design layout and strictly following design rules, designers can achieve efficient and reliable FCBGA substrate design. This guide highlights important decision points during the design process and provides solutions to overcome common design challenges such as thermal management, signal integrity, and EMI control.
The goal of the FCBGA (ABF) Substrate Design Reference Guide is to provide readers with a detailed manual that enables them to deeply understand and become proficient in FCBGA substrate design principles and techniques. Both beginners and experienced designers will gain valuable insights and practical advice for meeting increasingly complex and demanding electronic system design challenges. By following the guidance of this guide, designers can ensure that their designs are not only superior in performance, but can also be implemented smoothly during the manufacturing and testing phases, thereby delivering high-quality and high-reliability products to the market.
What material is used in FCBGA (ABF) Substrate?
FCBGA (ABF) substrate, Flip Chip Ball Grid Array (Ajinomoto Build-up Film) substrate, is a key material used in advanced semiconductor packaging technology. Its main materials include Ajinomoto Build-up Film (ABF) and copper, which play a key role in increasing packaging density and optimizing electrical performance.
First of all, as the main dielectric material of FCBGA substrate, ABF has excellent electrical insulation properties and mechanical strength. ABF is a high-performance multi-layer film material developed by Japan’s Ajinomoto Company and is widely used in the field of high-density circuit packaging. Its excellent electrical insulation properties can effectively isolate signals and power in the circuit, ensuring stable and reliable operation of the circuit. At the same time, the mechanical strength of ABF materials is also very good and can withstand physical stress and environmental changes during the packaging process, ensuring the long-term reliability and stability of the substrate.
Secondly, FCBGA substrate also uses copper as the main conductive material. Copper is one of the most common conductive materials in electronic devices due to its excellent electrical conductivity and processability. In the FCBGA substrate, the copper layer is used to form wires and pads for electrical connections and signal transmission, ensuring fast signal transmission and efficient operation of the circuit. By precisely controlling the thickness and layout of the copper layer, high-density layout and precise connections of complex circuits can be achieved, thereby meeting the stringent packaging technology requirements of modern high-performance electronic devices.
To sum up, the FCBGA (ABF) substrate uses two key materials, ABF and copper, to achieve excellent performance in electrical performance, mechanical strength and packaging density. This advanced semiconductor packaging technology not only promotes the miniaturization and functional integration of electronic devices, but also provides reliable solutions for various application scenarios, playing an important role from consumer electronics to industrial automation. As technology advances and market demands continue to change, FCBGA (ABF) substrates will continue to develop, bringing more innovation and possibilities to future electronic packaging technology.
What size are FCBGA (ABF) Substrate?
The size of the FCBGA (ABF) substrate varies depending on the specific application, which makes it suitable for a wide range of different types of electronic devices. From smartphones and wearable devices to industrial equipment and power electronics, FCBGA (ABF) substrates have demonstrated their flexibility and versatility in various fields.
In consumer electronics, such as smartphones and tablets, FCBGA (ABF) substrates are often very miniaturized. These devices require small substrate sizes to accommodate highly integrated processors, memory, and sensors while maintaining the compact and lightweight nature of the device. The small size of the FCBGA (ABF) substrate enables efficient use of limited space while providing high-density electrical connections to ensure device performance and functional integrity.
On the other hand, in industrial equipment and power electronics applications, FCBGA (ABF) substrates are typically larger. Devices in these areas often need to handle higher power and more complex circuit designs, requiring larger substrates to accommodate large electronic components and heat dissipation facilities. Large-sized FCBGA (ABF) substrates not only accommodate more components, but also provide more space for laying out complex circuits and connections.
In general, the size of the FCBGA (ABF) substrate depends on the specific device design requirements and internal space constraints. As technology advances and market demands change, manufacturers continue to innovate and strive to find a balance between size, performance and power consumption. This flexibility makes FCBGA (ABF) substrates an indispensable component in various electronic products, thereby promoting the diversified and innovative development of modern electronic equipment.
The Manufacturer Process of FCBGA (ABF) Substrate.
The manufacturing process of FCBGA (ABF) substrates is a precise and complex process involving multiple key steps, each of which has an important impact on the quality and performance of the final product.
First, the manufacturing process begins with the preparation of the substrate. Selecting the appropriate substrate is critical to ensuring the electrical performance and mechanical strength of the substrate. FCBGA (ABF) substrates usually use Ajinomoto Build-up Film (ABF) as the main dielectric material, which not only has excellent electrical insulation properties, but can also withstand the mechanical stress required for high-density connections.
Next comes the deposition stage of the copper layer. Copper is deposited on the surface of the substrate to form conductive paths that connect electronic components. Uniform deposition and good adhesion of copper are crucial for the subsequent etching process.
Photoresist application and exposure are the next critical steps. At this stage, a patterned photoresist layer is formed by coating the photoresist on the substrate surface and exposing it to UV light. These patterns define areas where future copper layers will be retained or removed.
This is followed by an etching process, in which the copper that is not protected by the photoresist layer is removed. This step is key to forming conductive paths, ensuring isolation between individual circuits and precise connections.
Drilling is then done to leave space for the formation of vias. Through holes are key conductive channels connecting different layers, and their position and diameter must be precisely controlled to ensure the stability and reliability of the overall circuit.
The component mounting stage involves the precise placement of electronic components on the substrate and their connection to the corresponding conductive paths through a soldering process. In modern manufacturing, surface mount technology (SMT) is often used to achieve efficient automated assembly, ensuring precise positioning of components and stable electrical connections.
The last is the testing phase, where the functions and performance of the FCBGA (ABF) substrate are verified through various testing methods (such as electrical testing, functional testing, etc.). Only through rigorous testing to ensure that the substrate can operate normally under various working conditions can the quality and reliability of the product be guaranteed.
To sum up, the manufacturing process of FCBGA (ABF) substrate is a technology-intensive and delicate process, and each step requires a high degree of professional knowledge and precise equipment control. Through the precise execution of these steps, FCBGA (ABF) substrates that meet high performance and high reliability requirements can be produced and used in advanced electronic equipment in various fields.
The Application area of FCBGA (ABF) Substrate.
As an important part of modern electronic technology, FCBGA (ABF) substrate has been widely used in various industries. With their high integration, strong reliability and excellent electrical performance, they play a key role in consumer electronics, telecommunications, automotive, aerospace, medical equipment and industrial automation.
First of all, FCBGA (ABF) substrates are widely used in the field of consumer electronics. From smartphones and tablets to smart home devices and portable consumer electronics, FCBGA substrates enable miniaturization and high performance of electronic products through its high-density packaging and excellent electrical connectivity.
Secondly, the telecommunications industry is also an important application field for FCBGA (ABF) substrates. Communication equipment, such as base stations, routers and optical fiber transmission equipment, need to process large amounts of data and complex signal processing. FCBGA substrates can provide efficient signal transmission and reliable electrical performance to ensure the stable operation of the equipment.
In the automotive industry, FCBGA (ABF) substrates are widely used in automotive electronic systems. From in-car entertainment systems to vehicle control units (ECUs) and driver assistance systems, FCBGA substrates can carry complex electronic circuits to ensure vehicle safety, comfort and performance.
The aerospace field is also an important application scenario for FCBGA (ABF) substrates. Avionics and satellite communication systems need to operate stably in extreme environments. FCBGA substrates have adapted to complex working environments and challenges through their highly reliable design and manufacturing processes.
In terms of medical equipment, FCBGA (ABF) substrates play a key role in medical imaging equipment, implantable medical devices, and life support systems. They not only support accurate data processing and transmission, but also ensure the stability and safety of medical equipment, which is crucial to the advancement of the medical industry.
Finally, in the field of industrial automation, FCBGA (ABF) substrates are widely used in control systems, sensors and robotics. They can achieve efficient data processing and control functions and improve the automation level and production efficiency of industrial production.
In short, FCBGA (ABF) substrate is not only the core component of various electronic devices, but also an important foundation for promoting modern technological progress and application innovation. Their widespread application has promoted the development of various industries and contributed significantly to the technological progress of human society.
What are the advantages of FCBGA (ABF) Substrate?
FCBGA (ABF) substrates offer several significant advantages over other packaging methods, making them an important choice in today’s electronic product design.
First, FCBGA technology allows for higher connection density and more compact layout through its unique flip-chip design. This characteristic makes it possible to realize complex circuits and multi-function integration in a limited space, which is suitable for the needs of modern electronic equipment for miniaturization and high performance.
Secondly, the FCBGA substrate uses Ajinomoto Build-up Film (ABF) as the dielectric material, which provides the circuit with excellent signal integrity and electrical performance. ABF material not only has good electrical insulation properties, but also helps reduce noise and distortion in signal transmission, improving the stability and reliability of the circuit.
In terms of manufacturing, FCBGA substrates adopt standardized manufacturing processes to ensure the consistency and reliability of product quality. This consistency makes mass production more efficient, reducing costs and increasing the reliability of product delivery.
In addition, the FCBGA substrate also significantly improves heat dissipation performance through flip-chip technology. By directly mounting the chip on the substrate and in contact with the thermal conductive layer, the heat transfer efficiency is effectively improved. This makes the FCBGA substrate particularly suitable for application scenarios that require high-performance computing and long-term stable operation, such as data centers and communication equipment.
Finally, the design flexibility of the FCBGA substrate allows it to be customized to specific needs. Engineers can adjust layout and design parameters to achieve optimal performance and fit based on the device’s specific requirements. This flexibility makes FCBGA substrates not only suitable for consumer electronics, but also widely used in medical equipment, aerospace technology, and industrial automation.
To sum up, FCBGA (ABF) substrate has become one of the indispensable key technologies in today’s electronic design due to its high-density packaging, excellent electrical performance, reliable manufacturing process, superior heat dissipation capability and flexible design characteristics. Promoting the continuous advancement of technological innovation and product progress.
FAQ
What is FCBGA (ABF) substrate?
FCBGA (ABF) substrate is an advanced semiconductor packaging technology, whose full name is Flip Chip Ball Grid Array (Ajinomoto Build-up Film) substrate. It uses Ajinomoto Build-up Film (ABF) as the dielectric material and directly connects the chip to the substrate through flip-chip technology to achieve high-density and high-performance packaging solutions.
What are the advantages of FCBGA (ABF) substrate?
FCBGA (ABF) substrates have multiple advantages over traditional packaging methods. They offer higher connection density and better electrical performance because the ABF material helps maintain good signal integrity. In addition, FCBGA technology supports flexible design and efficient thermal management for complex circuits and high-performance computing applications.
What are the application fields of FCBGA (ABF) substrate?
FCBGA (ABF) substrates are widely used in consumer electronics, telecommunications, automotive, aerospace, medical equipment and industrial automation industries. They are critical components in a variety of devices, including smartphones, computers, medical equipment, communications equipment and satellites.
What is the manufacturing process of FCBGA (ABF) substrate?
The manufacturing of FCBGA (ABF) substrates includes multiple steps such as substrate preparation, copper layer deposition, application and exposure of ABF materials, etching, drilling, component mounting, soldering and testing. The manufacturing process uses advanced technology and automated assembly to ensure product quality and production efficiency.