FCBGA Substrates Manufacturer, Professional FCBGA substrate production company, professional team and equipment, high-precision substrate production is inseparable from high-quality materials, so we use ABF substrate.
This guest article will explore the distinctive features of FCBGA Substrates and shed light on their remarkable contributions to the field of electronic engineering.
Functioning as a crucial electronic component, FCBGA Substrates serve as the vital link between the semiconductor chip and the PCB body. Their innovative design and structure facilitate more efficient electrical connections, establishing them as an indispensable element within the framework of today’s advanced electronic equipment.
Compared with traditional PCB design, FCBGA Substrates achieve more powerful performance in a smaller space, creating more possibilities for the sophistication and compactness of electronic devices.
FCBGA Substrates enables semiconductor chips to be more compactly embedded in the substrate through a unique flipped chip layout. This highly integrated design not only optimizes space utilization, but also helps improve the overall performance of the device.
In this guest article, we will dig deeper into what makes FCBGA Substrates unique and gradually unravel their important role in electronics design and manufacturing. By discussing this innovative technology, we hope readers can more fully understand how FCBGA Substrates has become a leader in electronic engineering and promotes the continuous evolution of electronic devices.
What are the types of FCBGA Substrates?
In today’s evolving PCB engineering field, FCBGA (Flip-Chip Ball Grid Array) Substrates leads the trend with its excellent performance and is redefining the landscape of electronic design and manufacturing. This article will take an in-depth look at the various types of FCBGA Substrates, covering high-density interconnects, organic substrates, and more, each of which is carefully designed to meet specific design needs and technical requirements.
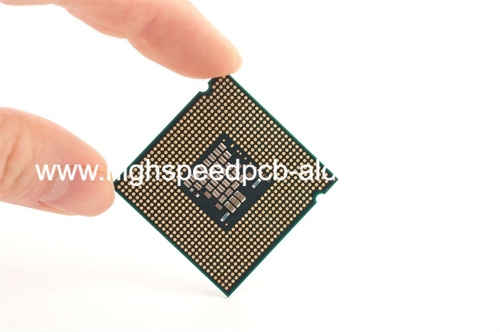
FCBGA Substrates Manufacturer
As a core component of electronic equipment, FCBGA Substrates are uniquely designed to effectively connect semiconductor chips and the rest of the PCB, providing efficient electrical connections for electronic equipment.
High Density Interconnect Type
This type of substrate enables superior electrical performance through smaller, denser connection points. This is critical to meeting the demands of modern electronic devices for small, high-performance designs.
Custom design of organic substrates
Organic substrate type FCBGA Substrates represent an approach tailored to specific needs. This substrate uses organic materials such as FR-4 and polyimide to provide superior electrical performance and stability. Organic substrates excel in high-frequency applications, making them ideal for communications and RF electronics.
Each FCBGA Substrates type presents unique advantages in meeting specific design needs and technical requirements. High-density interconnect types are suitable for scenarios requiring high-performance connections, while organic substrates provide an ideal solution for applications with stringent requirements for stability and high-frequency characteristics.
FCBGA Substrates’ continuous innovation and development has made it a leader in electronic design. As technology advances and design needs continue to evolve, we can expect more new FCBGA Substrates to emerge to meet the evolving electronics market.
Among the various types of FCBGA Substrates, high-density interconnect and organic substrates have demonstrated their excellence in meeting different design needs and technical requirements. As a core component of electronic design, the continuous innovation of FCBGA Substrates drives the development of the entire industry and paves the way for future electronic devices. This range of carefully designed substrate types not only meets current design challenges, but also lays a solid foundation for future electronic innovation.
What are the advantages of FCBGA Substrates?
FCBGA (Flip-Chip Ball Grid Array) substrates stand as a notable advancement in the ever-evolving realm of PCB engineering. Embraced extensively in modern electronic design and manufacturing, these substrates present a myriad of benefits, solidifying their pivotal role in the industry.
Exceptional Electrical Performance
FCBGA substrates distinguish themselves through outstanding electrical performance, establishing a sturdy foundation for electronic devices. The flip-chip configuration significantly minimizes interconnection lengths, thereby reducing signal transmission delays and elevating overall signal integrity. This feature positions FCBGA substrates as an optimal choice for applications demanding rapid data processing and efficient low-latency communication, ensuring peak functionality.
Compact and Efficient Design
The inherent strength of FCBGA substrates lies in their space-efficient design. Leveraging the flip-chip packaging method allows for a more condensed arrangement of components, resulting in heightened component density on the substrate. This not only aids in the downsizing of electronic devices but also enables intricate and sophisticated designs. With the increasing demand for smaller and lighter electronics, FCBGA substrates emerge as a pivotal solution to address these evolving design requirements.
Effective Thermal Management
Thermal management is a critical aspect of electronic design, and FCBGA substrates excel in this domain. The flip-chip configuration enables efficient dissipation of heat generated by electronic components. Direct connection between the semiconductor die and the substrate enhances heat conduction, resulting in improved thermal performance. This ensures the reliability and longevity of electronic devices, even in demanding operating conditions.
In conclusion, the advantages of FCBGA Substrates in modern PCB engineering are multifaceted and impactful. From superior electrical performance that ensures high-speed data processing to space-efficient designs catering to the demand for compact devices, and impeccable thermal management contributing to device reliability, FCBGA Substrates have positioned themselves as a cornerstone in the evolution of electronic design.
In the rapidly evolving landscape of electronic devices, the significance of FCBGA substrates has grown exponentially due to their pivotal role in addressing the complexities of high-performance computing, miniaturization, and thermal management. These substrates stand out as the preferred choice for forward-thinking PCB engineers, playing a crucial role in overcoming design challenges. Opting for FCBGA substrates is not merely a design decision; it represents a strategic leap toward unleashing the complete potential of contemporary electronic systems.
Why choose FCBGA Substrates?
In the ever-evolving field of electronic design and manufacturing, the choice of a suitable substrate holds significant importance. Among the numerous options available, Flip-Chip Ball Grid Array substrates (FCBGA) have emerged as a leading-edge technology, presenting distinct advantages over conventional PCBs in terms of performance, spatial efficiency, and adaptability to advanced technologies. Exploring the factors contributing to the growing preference for FCBGA substrates among design engineers reveals a compelling narrative of technological innovation and enhanced functionality.
Performance Advantages
FCBGA substrates exhibit outstanding performance, primarily manifested in the following key aspects:
Excellent Electrical Performance
Leveraging a flipped chip layout, FCBGA substrates achieve shorter circuit paths, reducing signal transmission delays and enhancing overall electrical performance.
Superior Heat Dissipation Performance
The design of FCBGA substrates facilitates more effective heat conduction. This characteristic not only decelerates the temperature rise of electronic devices but also significantly improves overall heat dissipation. This makes FCBGA substrates particularly well-suited for high-performance and high-density electronic equipment.
Space optimization
In the trend of modern electronic devices pursuing lightness, thinness and size, space utilization efficiency is crucial. FCBGA Substrates shows unique advantages in this regard:
Compact size: Due to its unique chip flip layout, FCBGA Substrates can achieve higher device density, making the overall circuit board more compact and suitable for applications with strict space requirements.
Hierarchical structure optimization: Through high-density interconnection technology, FCBGA Substrates allows multi-level, multi-functional designs to better meet the needs of complex circuits while reducing circuit board size.
Technological adaptability
With the continuous advancement of technology, the technical adaptability of substrates has become increasingly important. FCBGA Substrates has significant advantages at this point:
Facilitating advanced technologies: FCBGA substrates are well-suited for seamless integration with cutting-edge packaging technologies like 3D stacking and advanced packaging materials. This adaptability creates ample room for the incorporation of upcoming technologies.
Seamless integration: FCBGA substrates enable smooth multi-chip integration, catering to the design demands of multifunctional and high-performance devices. This enhances overall system flexibility and functionality.
Scenes of outstanding performance
In practical applications, FCBGA Substrates perform particularly well in the following scenarios:
High-performance computing: Suitable for computing scenarios that require fast data transmission and processing, such as servers and supercomputers.
Portable electronic devices: Under the design requirements of thin, light and short, FCBGA Substrates can meet the dual needs of size and performance, such as laptops and smartphones.
Embedded Systems: For embedded applications that require a high degree of integration and stability, FCBGA Substrates are an ideal choice.
In summary, by choosing FCBGA Substrates instead of other types of boards, you can not only enjoy excellent advantages in performance and space, but also maintain sensitivity to future technologies, allowing your design to remain competitive in the ever-evolving electronics field.
How are FCBGA Substrates made?
The intricate manufacturing process of FCBGA (Flip-Chip Ball Grid Array) substrates is a crucial and complex undertaking that demands a profound comprehension of both motherboard and substrate production. This article will thoroughly explore the intricacies of manufacturing motherboards and FCBGA substrates, shedding light on both subtractive and additive manufacturing processes. Additionally, it will highlight the pivotal role played by cutting-edge materials and technologies in these processes.
Motherboard manufacturing
The motherboard serves as the support platform for FCBGA Substrate, and its manufacturing process involves advanced technologies and materials to achieve optimal performance. Here are the key steps in motherboard manufacturing:
The production of motherboards relies on crucial technologies and techniques that significantly influence overall system performance. Advanced soldering methods, multi-layer lamination technology, and high-precision printed circuit board (PCB) manufacturing play pivotal roles in establishing a robust foundation for motherboard reliability and performance.
FCBGA Substrate Manufacturing
The manufacturing of FCBGA Substrate is an indispensable part of the entire electronic system, providing solid support and reliable connections for the chip. The following are the key steps in FCBGA Substrate manufacturing:
Technology for creating high-density interconnects
The high-density interconnects of FCBGA Substrate, a key feature, are achieved through advanced manufacturing technology. Utilizing fine line width and spacing, coupled with advanced printing and etching techniques, enables the incorporation of more connection points within a limited space. This enhancement significantly improves circuit density and overall performance.
A critical aspect of FCBGA Substrate manufacturing is the careful selection of high-performance substrate materials. Materials such as FR-4 and polyimide are extensively utilized due to their exceptional electrical insulation properties, mechanical strength, and resistance to high temperatures. This ensures that the substrate can operate reliably in diverse environmental conditions.
Understanding the intricacies of these manufacturing processes provides insight into why FCBGA Substrates have become integral components in modern electronic devices. The precision, high performance, and reliability of these substrates are the outcomes of the meticulous combination of advanced manufacturing processes and cutting-edge technologies.
What are the application areas of FCBGA Substrates?
Flip-Chip Ball Grid Array (FCBGA) substrates play a pivotal role in shaping the landscape of electronic design and manufacturing, exerting a profound influence across diverse industries. Their extensive applicability spans from consumer electronics to automotive and medical devices, underscoring their exceptional versatility and adaptability, thereby contributing significantly to advancements in various sectors.
Consumer electronics field
In the field of consumer electronics, FCBGA Substrates provides advanced circuit connections and highly integrated solutions for various devices. For example, FCBGA Substrates are widely used in smartphones, tablets, and smart home devices because of their ability to provide excellent performance in limited space while ensuring high reliability of electronic components.
Automobile industry
Automakers are increasingly adopting FCBGA Substrates to meet the growing demands on electronic systems in modern vehicles. These substrates not only provide advanced connection technology, but also maintain stability under extreme temperature and vibration conditions. Engine control units, infotainment systems and driver assistance technologies in vehicles may all use FCBGA Substrates to ensure reliability and performance.
Medical equipment field
In medical device manufacturing, FCBGA Substrates has demonstrated its advantages in high precision and stability. Medical equipment, such as medical imaging equipment, patient monitoring systems and surgical instruments, often require highly integrated and precise electronic control, which is FCBGA Substrates’ strength. This helps ensure medical devices provide accurate and reliable data and functionality when it matters most.
In the medical field, a medical device manufacturing company successfully used FCBGA Substrates in its new generation of patient monitoring equipment. This innovation makes the device smaller and lighter while maintaining high accuracy and the ability to transmit real-time data.
The multi-field applications of FCBGA Substrates not only reflect its importance in electronic design and manufacturing, but also demonstrate its potential to support innovation in different industries. From consumer electronics to automobiles and medical equipment, FCBGA Substrates is driving technological development in various fields, injecting more possibilities into future electronic products and systems.
Where to find FCBGA Substrates?
In the pursuit of excellence in PCB engineering, finding reliable and high-quality FCBGA Substrates is a key part of ensuring project success. To guide readers towards the right choice, we highlight the following key aspects so that you can make informed decisions and make supplier selection a priority.
Trustworthy manufacturer
When choosing an FCBGA Substrates supplier, the first thing to consider is the manufacturer’s reputation and experience. Choosing a manufacturer with extensive experience and a good reputation guarantees you a proven product that meets high standards of quality. As your supplier, our company provides you with the highest quality FCBGA Substrates with years of experience and excellent reputation.
Professional distributor
In addition to manufacturers, professional distributors are also options worth paying attention to. These distributors often work with multiple manufacturers to provide customers with more choices and ensure that their products comply with various industry standards. With a professional distribution network, our company provides you with a wide range of options to meet the needs of various projects.
When seeking FCBGA Substrates, prioritizing quality is paramount. Select a supplier that adheres to rigorous quality control processes, guaranteeing that each substrate meets the highest standards. Our company’s robust quality assurance procedures ensure precision testing for excellent performance and reliability in every FCBGA Substrate.
Recognizing the unique requirements of each project is essential. Opt for a supplier committed to offering customized solutions. Our company is dedicated to meeting the individual needs of our customers, providing flexible customization options to ensure optimal support for your project.
Ensuring supply chain stability is vital for project success. Choose a reliable supplier to mitigate the risk of material shortages or disruptions. Our company assures a strong and stable supply chain, ensuring the uninterrupted progress of your project according to plan.
In short, choosing a reliable and high-quality FCBGA Substrates supplier is a key factor in ensuring project success. Our company is committed to becoming your preferred supplier, providing the best support for your PCB projects with excellent quality, rich experience and professional services.
How is FCBGA Substrates’ quotation formed?
As the backbone of modern electronic design, the formation of FCBGA Substrates’ quotations involves multiple factors, including substrate type, complexity and production volume. This article will delve into these constraints to provide readers with a clear understanding so that they can more confidently address the cost considerations of FCBGA Substrates.
Effect of substrate type
FCBGA Substrates’ substrate type has a significant impact on its quotation. Different substrate materials, such as FR-4 and polyimide, have different physical and electrical properties, thus incurring different costs during production and processing. Materials with high performance and high temperature resistance usually bring higher manufacturing costs, which directly affects the final quotation.
Complexity Considerations
The complexity of FCBGA Substrates is another factor that cannot be ignored. High-density interconnects and complex wiring structures may require more sophisticated manufacturing processes and more production steps. This results in increased labor costs and requires higher levels of technology and equipment, which has a direct impact on the final quote.
Production volume challenges
Throughput is a crucial consideration. Large-scale production may result in lower costs per component because fixed costs can be spread over more units. However, in small-scale production, the allocation of fixed costs increases relatively, pushing up the cost of each component. The fluctuation of production volume is directly related to the final quotation of FCBGA Substrates, which requires a balance between economic benefits and market demand.
Comprehensive cost considerations
When considering the quotation of FCBGA Substrates, manufacturers need to comprehensively consider the above three factors. By balancing substrate type, complexity and throughput, manufacturers can optimize production processes and reduce manufacturing costs, which ultimately reflects in more competitive quotes. This comprehensive consideration requires manufacturers to work closely together during the design and production phases to ensure that costs are minimized while quality and performance requirements are met.
With a deeper understanding of the impact of substrate type, complexity and production volume on FCBGA Substrates quotes, readers can respond to cost considerations with more confidence. This understanding enables designers, engineers and procurement personnel to make informed decisions to ensure optimal performance and quality within project budgets.
In the world of FCBGA Substrates, cost is not a single number, but a comprehensive consideration. By understanding the impact of substrate type, complexity and throughput, manufacturers and designers can find a balance between innovation and economics to lay a solid foundation for the future of electronic devices.
Frequently Asked Questions (FAQs)
How does the manufacturing process of FCBGA Substrates differ from traditional PCBs?
The manufacturing process involves intricate steps, including high-density interconnect creation and the utilization of advanced materials. FCBGA Substrates often require more precision in assembly due to the flip-chip technology, contributing to their superior performance.
Can FCBGA Substrates be customized for specific design requirements?
Certainly, FCBGA Substrates offer a high degree of customization to meet specific design needs. Engineers can tailor aspects such as substrate materials, interconnect configurations, and thermal properties to align with the requirements of diverse applications.
What considerations influence the cost of FCBGA Substrates?
The cost of FCBGA Substrates is influenced by factors such as substrate type, complexity, and production volumes. Higher complexity and lower production volumes may lead to increased costs, reflecting the precision and advanced technology involved in their manufacturing.
What sets FCBGA Substrates apart from other types of PCBs?
One prevalent query revolves around the distinctive features that differentiate FCBGA Substrates from traditional PCBs. Understanding the unique advantages, such as enhanced electrical performance and superior thermal management, contributes to informed decision-making.
What challenges might arise during the manufacturing process of FCBGA Substrates?
This question addresses concerns related to the production phase. Delving into the complexities of manufacturing, including high-density interconnect creation and the use of advanced materials like FR-4 and polyimide, helps readers comprehend potential challenges and their resolutions.
Are FCBGA Substrates compatible with emerging technologies such as 5G and IoT?
With the rapid evolution of technology, compatibility becomes a crucial consideration. Exploring the adaptability of FCBGA Substrates to emerging technologies ensures that electronic designs remain future-proof.
How does the cost of FCBGA Substrates compare to other types of boards?
Cost considerations are paramount in any engineering project. Readers often seek insights into the factors influencing FCBGA Substrate quotes, including substrate type, complexity, and production volumes, to make informed budgetary decisions.
What role do FCBGA Substrates play in improving the reliability and lifespan of electronic devices?
Reliability is a cornerstone in electronic design. This question aims to understand how FCBGA Substrates contribute to the longevity and robustness of electronic devices, ensuring consistent performance over time.
In what industries and applications are FCBGA Substrates most commonly utilized?
Understanding the diverse applications of FCBGA Substrates is crucial. From consumer electronics to automotive and medical devices, exploring the industries where FCBGA Substrates excel provides valuable insights into their versatility.
Can FCBGA Substrates be customized to meet specific project requirements?
Tailoring substrates to specific project needs is often a concern. Discussing the customization options available with FCBGA Substrates ensures that engineers can adapt these substrates to diverse project requirements.