FCBGA Packaging Substrate Manufacturer, specializing in ultra-small trace width and pitch, We use the Showa Denko and ABF(Ajinomoto) core materials produce the FCBGA , SIP, FCCSP package substrates from 2 layer to 20 layers.
FCBGA (Flip-Chip Ball Grid Array) Packaging Substrate emerges as a forefront technology in contemporary electronic engineering, offering robust support for integrated circuits and pushing the boundaries of performance and integration. At the heart of its success lies the innovative flip-chip connection method.
In this state-of-the-art process, the chip is inverted and securely attached to a substrate, with tiny solder balls forming critical connections between the chip and the substrate. This approach significantly reduces the distance between chips, leading to improved signal transmission speed and overall circuit performance.
FCBGA Packaging Substrate showcases several pivotal features that contribute to its exceptional integration capabilities. Firstly, its design enables a higher number of connection points, allowing for the integration of more functional units within a smaller space.
Beyond achieving more compact designs, FCBGA Packaging Substrate excels in delivering outstanding heat dissipation performance, addressing the modern electronic equipment’s demand for both high performance and compact form factors.
As technology progresses, FCBGA Packaging Substrate continues to exhibit promising prospects in electronic engineering. Future trends may include even smaller designs, integration of higher-performance materials, and the development of more intricate integrated circuits to meet the escalating demand for electronic devices.
In summary, FCBGA Packaging Substrate, with its flip-chip connection methodology, not only plays a pivotal role in current electronic engineering applications but also holds immense potential for future innovations and developments in electronic equipment.
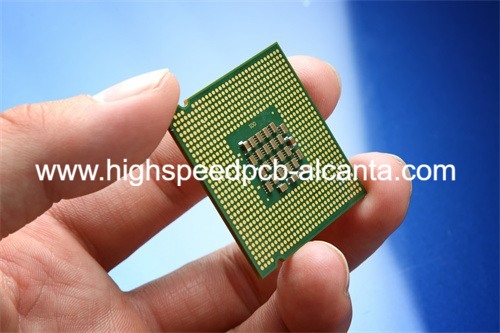
FCBGA Packaging Substrate Manufacturer
What types of FCBGA Packaging Substrate are there?
FCBGA (Flip-Chip Ball Grid Array) packaging substrate stands out as a crucial technology in the realm of packaging, with its diverse designs playing a pivotal role in accommodating a wide array of devices and application scenarios. A comprehensive grasp of the dimensions and structural configurations of these designs is imperative for gaining insight into their varied nature.
First, the types of FCBGA Packaging Substrate can be distinguished based on size. In electronic engineering, devices come in various sizes and shapes, therefore, FCBGA Packaging Substrate is designed in different sizes to meet various packaging needs. From tiny mobile devices to large computer systems, FCBGA Packaging Substrates of different sizes play unique advantages in achieving the goals of compact design and high integration.
Secondly, structural design is another key factor affecting the performance and adaptability of FCBGA Packaging Substrate. Different application scenarios put forward different requirements for the structure of circuit boards. Some applications require higher thermal performance, while others may place more emphasis on the mechanical strength of the board. FCBGA Packaging Substrate meets these needs through different hierarchies and material combinations, providing highly customized solutions for various application scenarios.
When confronted with various devices and application scenarios, engineers and designers must possess a comprehensive understanding of the diverse types of FCBGA (Flip-Chip Ball Grid Array) Packaging Substrate. These variations necessitate distinct layouts and connection methods, directly influencing the device’s performance and stability. Simultaneously, the assortment of sizes and structures empowers engineers with increased design flexibility, enabling them to more effectively cater to customer requirements.
The richness of FCBGA Packaging Substrate diversity not only stems from its widespread applicability but also from its adaptability in size and structural design. Through a profound comprehension of these types, electronic engineers can adeptly choose and apply the FCBGA Packaging Substrate that aligns with the specific demands of their projects. This, in turn, fosters continuous innovation within the realm of electronic engineering.
What are the advantages of FCBGA Packaging Substrate?
FCBGA (Flip-Chip Ball Grid Array) Packaging Substrate stands out as an advanced packaging technology, offering substantial advantages over traditional circuit boards. Beyond its inherent benefits of high integration and compact size, it excels in superior heat dissipation performance, positioning it as a sought-after solution in the realm of electronic engineering.
One of its key strengths lies in its highly integrated design. Utilizing flip-chip connection, the substrate allows for the chip to be inverted and mounted, achieving an elevated level of integration. This innovative approach enables the accommodation of a greater number of electronic components within a confined space, consequently enhancing overall circuit performance and efficiency. The remarkable level of integration makes FCBGA particularly well-suited for devices with limited spatial constraints, granting heightened design flexibility for contemporary electronic devices.
Small size
Due to its advanced packaging technology, FCBGA Packaging Substrate makes the overall size more compact than traditional circuit boards. This is critical for portable devices and embedded systems, which often need to fit more functionality and components into a limited space. The small size design makes FCBGA ideal for use in modern electronics, enabling lighter and more portable devices.
Excellent cooling performance
The FCBGA Packaging Substrate excels in heat dissipation performance, primarily due to its effective utilization of the flip-chip connection method. This approach ensures efficient conduction of the chip’s heat to the substrate, which is subsequently rapidly dissipated through a radiator or other heat dissipation mechanisms. Such a well-thought-out design is instrumental in averting performance issues arising from chip overheating, thereby prolonging the device’s lifespan. The remarkable heat dissipation capabilities of FCBGA Packaging Substrate make it a standout choice for high-performance electronic equipment.
Taken together, FCBGA Packaging Substrate has become an advanced packaging technology that cannot be ignored in today’s electronic engineering field due to its high integration, small size and excellent heat dissipation performance. These advantages make FCBGA shine in meeting the needs of modern equipment, improving performance and expanding application fields.
Why choose FCBGA Packaging Substrate?
This article will intricately explore the reasons behind the preference for FCBGA Packaging Substrate in electronic design, elucidating its advantages over alternative packaging technologies. By drawing on practical application cases, we aim to underscore its significance in electronic engineering.
Foremost, FCBGA Packaging Substrate is chosen in electronic design due to its outstanding performance and adaptability. Employing the flip-chip connection method, FCBGA achieves heightened integration levels, resulting in more compact circuit boards suitable for scenarios demanding a high degree of integration. Furthermore, this packaging technology facilitates a shorter signal transmission path, diminishing signal delays and ultimately enhancing the overall device performance.
In contrast to traditional packaging methods, FCBGA Packaging Substrate boasts notable advantages in heat dissipation. Its design permits direct chip connection to heat dissipation solutions, significantly improving efficiency in heat dissipation. This feature holds paramount importance for high-performance devices, particularly in the realms of computing and communications. Through optimized heat dissipation, FCBGA Packaging Substrate establishes a robust foundation for device reliability and stability.
Practical applications underscore the prominent role of FCBGA Packaging Substrate in electronic design. In the smartphone industry, where compactness and reduced weight are paramount, FCBGA Packaging Substrate finds extensive use in chip packaging.
Its advanced integration capabilities and superior heat dissipation performance empower core components like processors to function with heightened efficiency, delivering exceptional computing performance. This is particularly critical for servers tasked with handling large-scale data and executing complex computing tasks.
Overall, the decision to choose FCBGA Packaging Substrate in electronic design is not accidental. Its excellent performance, compact design, and superior heat dissipation performance make it stand out in many application scenarios. Combined with actual application cases, the advantages of FCBGA Packaging Substrate have become increasingly prominent in electronic engineering, becoming a key factor in promoting innovation and meeting market demand.
What is the manufacturing process of FCBGA Packaging Substrate?
The manufacturing process of FCBGA (Flip-Chip Ball Grid Array) Packaging Substrate is a highly intricate and precise undertaking, encompassing the production steps of the main board and base plate, incorporating a series of advanced processes and technologies.
The manufacturing journey of FCBGA (Flip-Chip Ball Grid Array) Packaging Substrate commences with the careful design of the motherboard and backplane. The design team strategically plans the circuit layout, aiming for optimal proximity between the chip and substrate to achieve a short and efficient connection, ultimately enhancing signal transmission efficiency. This critical phase demands meticulous attention to detail, ensuring that the geometry and dimensions of the motherboard and backplane align precisely with the device’s specifications.
Following the detailed circuit design, cutting-edge manufacturing techniques come into play to transfer the intricately designed circuit diagram pattern onto the motherboard and backplane. Processes such as photolithography or etching may be employed to imprint the circuit diagram onto the substrate surface with exceptional precision. This step is of paramount importance in the manufacturing process, directly impacting the performance and reliability of the FCBGA Packaging Substrate.
Following the accurate printing of the circuit diagram, soldering technology takes center stage. The FCBGA Packaging Substrate utilizes a flip-chip connection method, wherein tiny solder balls facilitate the connection between the chip and the substrate. This phase demands a high degree of precision and employs advanced welding equipment to ensure the strength and reliability of each solder joint, thus safeguarding the overall circuit’s reliability.
Furthermore, the advanced manufacturing process incorporates the multi-layer assembly of FCBGA Packaging Substrate. By strategically layering different materials, higher integration and reduced size can be achieved while enhancing thermal performance. This aspect necessitates meticulous consideration during the design phase to ensure seamless collaboration among the layers.
In the final stages of the manufacturing process, rigorous quality control and testing procedures are implemented. State-of-the-art testing equipment is employed to verify that each FCBGA Packaging Substrate adheres to stringent specifications and standards. This encompassing evaluation includes electrical performance testing, connection reliability assessment, and durability testing, all aimed at ensuring that the final product operates stably and reliably in practical applications.
Overall, the manufacturing process of FCBGA Packaging Substrate relies on highly precise design and advanced manufacturing technology. Through this process, we are able to obtain advanced packaging technologies that are widely used in electronic devices, bringing more possibilities to the development of electronic engineering.
In what fields is FCBGA Packaging Substrate widely used?
FCBGA Packaging Substrate, as an advanced packaging technology, has shown strong application value in multiple electronic equipment fields. Its flexibility and performance make it the preferred packaging solution for a variety of devices. The following will explore the wide range of applications of FCBGA Packaging Substrate in smartphones, computers, communication equipment and other fields.
Smartphone field
The adoption of Flip-Chip Ball Grid Array (FCBGA) packaging substrate in smartphones has emerged as a powerful strategy for boosting performance and optimizing device dimensions. Harnessing FCBGA technology empowers mobile phone manufacturers to craft designs that are not only more compact but also thinner and lighter, all the while maintaining a superior level of integration. This technological approach enables modern smartphones to achieve accelerated data transfer speeds, enhanced processing capabilities, and more advanced graphics performance. It’s worth noting that a multitude of mobile phone chips and processors leverage FCBGA packaging substrate, contributing to an exceptional mobile experience for users.
Computer field
In the computer field, the application of FCBGA Packaging Substrate cannot be ignored. The processor, graphics card and other key components use FCBGA technology to provide excellent performance and cooling. Because FCBGA packaging allows for a tighter chip layout, computer manufacturers are able to accommodate more functional units in a limited space. This provides an ideal solution for the design of high-performance computers and servers while ensuring system stability and reliability.
Communication equipment field
Communication equipment, especially network equipment and communication base stations, have extremely high requirements for high performance and high density. FCBGA Packaging Substrate is ideally suited to meet these needs through its highly integrated and reliable connectivity. In the field of communications, FCBGA Packaging Substrate is widely used in processors, radio frequency modules and communication chips to provide devices with faster and more reliable communication capabilities. This is critical to supporting the smooth operation of modern communications networks.
Through specific practical application cases, we can better understand the application of FCBGA Packaging Substrate in various fields. For example, in smartphones, the application of FCBGA Packaging Substrate makes the phone lighter, has better performance, and improves the user experience. In the computer field, the design of high-performance computers was realized, and in communication equipment, device performance was significantly improved.
The FCBGA Packaging Substrate plays a pivotal role across various domains such as smartphones, computers, and communication equipment, offering robust support for the heightened performance and efficiency of contemporary electronic devices. Its exceptional flexibility and superior performance establish it as an essential component within the realm of electronic engineering today.
How to find high-quality FCBGA Packaging Substrate?
When looking for high-quality FCBGA Packaging Substrate, key decisions and selections are critical to the success of your project. Here are some suggestions to help you find reliable suppliers and ensure you get excellent components.
Establishing direct communication with the manufacturer of FCBGA Packaging Substrate is a crucial initiative in sourcing reliable components. This direct engagement allows for in-depth insights into product quality, production processes, and the latest technological innovations. Such direct channels empower you to gather comprehensive information from the source.
Consider the supplier’s experience and expertise
Selecting a supplier with extensive experience and expertise will help ensure you receive a technologically advanced and standards-compliant FCBGA Packaging Substrate. The manufacturer’s professional background and technical capabilities are key factors in assessing its reliability.
Check out trusted industry recommendations
Finding suppliers that are recommended and approved by the industry is one way to go. This may include recommendations from industry associations, exhibitors at professional trade shows, and recommendations from other electronic engineers. These sources often provide helpful information about the supplier’s reliability and product quality.
Consider quality certifications and standards
Ensure that the selected supplier’s FCBGA Packaging Substrate meets industry standards and quality certification requirements. Knowing whether they hold ISO certification, RoHS certification, etc. will help confirm the reliability and compliance of their products.
Considering these factors will empower readers to identify a reliable supplier for FCBGA packaging substrates in the market. Ensuring collaboration with a seasoned and reputable manufacturer lays the groundwork for a successful project.
How is the quotation of FCBGA Packaging Substrate formed?
When obtaining a quote for FCBGA Packaging Substrate, it is crucial to understand market pricing and the factors that affect price. The following is a detailed analysis of how to form a FCBGA Packaging Substrate quotation.
Market pricing orientation
The market pricing of FCBGA (Flip-Chip Ball Grid Array) Packaging Substrate is influenced by a variety of factors that collectively shape its value. Primarily, the delicate balance between supply and demand emerges as a pivotal determinant. When demand surpasses supply, prices are inclined to ascend; conversely, an oversupply scenario can lead to a decline in prices. Furthermore, the competitive dynamics within the market constitute another crucial factor impacting pricing. In markets marked by intense competition, prices tend to experience downward pressure, whereas a monopoly situation may contribute to comparatively higher prices.
Factors affecting the price of FCBGA Packaging Substrate
Cost of materials constitutes a significant portion of the overall expenses associated with FCBGA (Flip-Chip Ball Grid Array) Packaging Substrate. Diverse materials incur varied costs, and the ultimate price of the end product is intricately tied to the quality and performance of these materials.
Technological innovation: If there are new technological innovations applied to the manufacturing of FCBGA Packaging Substrate, this may improve product performance, but it may also increase production costs, thus affecting the price.
Market demand: When market demand for FCBGA Packaging Substrate increases, the price usually increases. The balance between supply and demand is key to price stability.
Brand influence: Some well-known brands of FCBGA Packaging Substrate usually have higher prices. Brands influence consumers’ purchasing decisions, so some brands may set relatively high prices.
For budget planning, it is crucial to accurately understand the price formation mechanism of FCBGA Packaging Substrate. With an in-depth understanding of market trends and various factors affecting price, companies can better plan project budgets and ensure high-quality FCBGA Packaging Substrate within an economically feasible range.
When considering purchasing FCBGA Packaging Substrate, it is recommended that companies pay close attention to market dynamics and communicate effectively with suppliers to obtain accurate information about current market pricing and future trends. Such information will help companies make informed decisions and ensure successful project implementation.
To sum up, understanding the formation mechanism of FCBGA Packaging Substrate quotation is a key step to ensure the success of the project. Through in-depth research on market pricing and price influencing factors, companies can better formulate budgets and ensure access to high-performance, high-quality FCBGA Packaging Substrate.
What are the common problems with FCBGA Packaging Substrate?
How can one ensure the quality of FCBGA Packaging Substrate components?
Ensuring the quality of FCBGA Packaging Substrate components involves selecting reputable suppliers and manufacturers. It is advisable to verify certifications, review customer feedback, and engage in thorough quality control processes during procurement.
Are there any challenges associated with the manufacturing process of FCBGA Packaging Substrate?
The manufacturing process of FCBGA Packaging Substrate involves intricate steps, including the production of the mainboard and substrate. Challenges may arise in achieving precision during soldering and ensuring the alignment of components. Strict adherence to advanced manufacturing techniques helps overcome these challenges.
How does FCBGA Packaging Substrate contribute to space-saving in electronic devices?
The Flip-Chip design of FCBGA Packaging Substrate allows for a compact footprint by reducing the space required for interconnections. This space-saving feature is particularly advantageous in modern electronic devices where miniaturization is a key consideration.
What future trends are anticipated for FCBGA Packaging Substrate in electronic engineering?
The future of FCBGA Packaging Substrate is expected to involve continuous innovation, with an emphasis on even higher integration, improved materials, and enhanced manufacturing techniques. Its role in enabling advancements in electronic engineering is likely to expand further.
In summary, FCBGA Packaging Substrate represents a crucial aspect of electronic engineering, offering a range of benefits and applications. Addressing these common queries provides a comprehensive understanding of its significance and potential challenges in the field.