FC-LGA Substrates Manufacturer.FC-LGA Substrates Manufacturer specializes in producing high-performance flip-chip land grid array (FC-LGA) substrates, essential components in modern semiconductor packaging. These substrates provide reliable electrical connections and thermal management for integrated circuits, enhancing performance and durability in electronic devices. The manufacturer employs advanced technologies and strict quality control to meet the demands of various industries, including computing, telecommunications, and consumer electronics. Their commitment to innovation ensures they deliver cutting-edge solutions tailored to the evolving needs of the global market.
FC-LGA (Flip Chip Land Grid Array) substrate is an indispensable part of modern electronic equipment. It provides reliable connection and support for electronic components. Through flip-chip packaging technology, FC-LGA substrates play a key role in electronic products, not only improving product performance and reliability, but also promoting innovation and development in the electronics industry. This article will delve into the design principles, manufacturing processes and application fields of FC-LGA substrates to help readers better understand and apply this important technology.
What are FC-LGA Substrates?
FC-LGA substrate, full name Flip Chip Land Grid Array substrate, is an advanced electronic connection technology. Its innovation lies in connecting the chip directly to the substrate through flip chip packaging (Flip Chip) instead of using traditional Welding method. This unique design greatly improves the connection reliability and performance stability of electronic components.
In the FC-LGA substrate, the chip is mounted upside down on the surface of the substrate and connected to the metal grid of the substrate through micro-connection points. This connection method, called Land Grid Array (LGA), has higher density and reliability than traditional welding methods. Through this design, the FC-LGA substrate can not only achieve a more compact layout, but also provide more stable signal transmission and more effective thermal management.
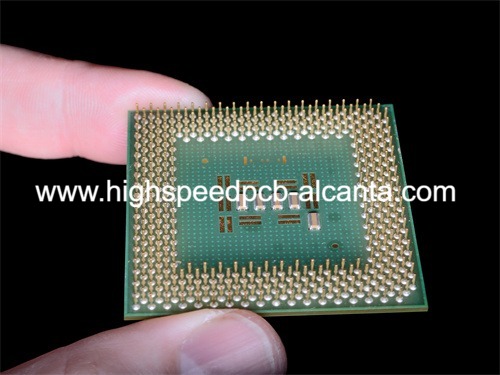
FC-LGA Substrates Manufacturer
One of the main advantages of FC-LGA substrate is its ability to effectively reduce the complexity of circuit layout. Since the chip is directly connected to the substrate, traditional chip packaging and connection lines are no longer required, allowing for a more simplified circuit design. This not only helps reduce the size and weight of the device, but also improves overall system performance and reliability.
In addition, FC-LGA substrate also has better thermal management capabilities. Since the chip is directly connected to the substrate, its heat dissipation efficiency is higher, and the heat can be more effectively transferred to the surface of the substrate, and then dissipated to the external environment through the heat dissipation structure. This has led to the widespread promotion of the application of FC-LGA substrates in high-performance and high-density electronic devices.
In general, FC-LGA substrate, as an advanced electronic connection technology, has brought revolutionary changes to the design and manufacturing of electronic equipment. Its reliable connectivity, excellent signal transmission performance and effective thermal management capabilities make it an indispensable and important component of modern electronic products.
FC-LGA Substrates design Reference Guide.
When designing an FC-LGA (Flip Chip Land Grid Array) substrate, designers need to carefully consider multiple factors to ensure that the final product has excellent performance and reliability. Here are some important design reference guidelines:
Circuit layout
When designing FC-LGA substrate, reasonable circuit layout is crucial. Designers should consider factors such as the length of the signal transmission path, impedance matching, and separation of signals from ground. By optimizing circuit layout, signal interference and crosstalk can be reduced, signal integrity and system performance improved.
Thermal management
FC-LGA substrates generate a large amount of heat during operation, so designers need to take measures to effectively manage and dissipate heat. This includes selecting appropriate heat dissipation materials, designing heat dissipation structures, and rationally arranging heat dissipation components. Through effective thermal management, stable operation of the system can be ensured and the service life of the equipment can be extended.
Signal integrity
When designing FC-LGA substrates, designers must pay attention to maintaining signal integrity. This involves controlling the transmission delay of the signal, maintaining the waveform quality of the signal, and avoiding signal distortion. Adopting appropriate wiring technology, using appropriate signal layer stacking and ground plane planning can effectively improve signal integrity and ensure system stability and reliability.
Professional guide reference
When designing FC-LGA substrates, designers should refer to relevant professional guidelines and standards, such as IPC standards, PCB design manuals, etc. These guides contain a wealth of design experience and best practices that can help designers avoid common design mistakes and ensure designs comply with industry standards and requirements.
To sum up, designing an FC-LGA substrate requires comprehensive consideration of multiple factors such as circuit layout, thermal management, and signal integrity. By following professional guidelines and adopting appropriate design methods, the reliability and performance of the design can be ensured, providing reliable support for the stable operation of electronic equipment.
What material is used in FC-LGA Substrates?
FC-LGA substrate is an advanced technology widely used in today’s electronics industry, and its reliability and performance often depend on the materials used. When designing and manufacturing FC-LGA substrates, it is crucial to select high-quality materials because they directly affect the stability and reliability of the substrate.
First of all, high-density glass fiber is one of the main constituent materials of FC-LGA substrate. This glass fiber has excellent mechanical strength and heat resistance and can withstand high temperature and high frequency working environments. At the same time, high-density glass fiber has good insulation properties, which can effectively isolate signal interference between circuits and ensure the stability and reliability of the substrate.
Secondly, copper foil is also one of the commonly used materials for manufacturing FC-LGA substrates. Copper foil serves as a conductive layer and is precisely pressed onto the surface of the fiberglass substrate to form the conductors and connection points of the circuit. Copper foil has excellent electrical and thermal conductivity properties and can effectively transmit signals and heat to ensure the normal operation of electronic equipment.
In addition to high-density glass fiber and copper foil, FC-LGA substrates may also use other auxiliary materials, such as solder paste, solder resist, etc. These materials play an important role in the manufacturing process to ensure welding quality, improve the oxidation resistance of the substrate, and play an important protective role during maintenance and repair processes.
In general, the materials used in FC-LGA substrates have high quality, high temperature resistance and excellent electrical properties, and are suitable for various working environments and application scenarios. The selection and application of these materials lay a solid foundation for the stability and reliability of FC-LGA substrates, making them an indispensable and important part of modern electronic equipment.
What size are FC-LGA Substrates?
The size of FC-LGA substrates can be customized for different application requirements, making them useful in a variety of electronic devices. From small mobile devices to large server systems, FC-LGA substrates come in a wide range of sizes to meet the needs of different application scenarios.
For small mobile devices, such as smartphones, tablets and wearable devices, a very compact design is usually required, so FC-LGA substrates usually come in smaller sizes. This small-sized substrate can effectively save space, making the device thinner, lighter and more portable, while also providing stable and reliable connection and performance.
For industrial applications such as large server systems or network equipment, larger FC-LGA substrates are usually required to support more electronic components and complex circuit layouts. These large substrates can not only accommodate more components, but also provide more powerful performance and stability to meet the needs of high-performance computing and big data processing.
In addition to size, the shape of the FC-LGA substrate can also be customized according to specific needs. Some applications may require specially shaped base plates to accommodate specific chassis designs or installation space constraints. Therefore, FC-LGA substrate manufacturers are usually able to provide customized design solutions according to customer requirements to ensure a perfect match between the substrate and the device.
In short, the size of FC-LGA substrate is flexible and can be customized according to different application requirements. Whether it is a small mobile device or a large industrial equipment, you can find a suitable FC-LGA substrate to achieve stable and reliable electronic connections and excellent performance.
The Manufacturer Process of FC-LGA Substrates.
The manufacturing process of FC-LGA substrate is a complex and precise process, which involves multiple links and professional technologies to ensure that the quality and performance of the final product meet the expected standards. The manufacturing process of FC-LGA substrate will be introduced step by step below:
Circuit design
The first step in manufacturing FC-LGA substrate is circuit design. This includes determining the layout of the circuit, how it is connected, and where components are located. Designers need to consider circuit complexity, signal integrity, thermal management and other factors to ensure the stability and reliability of the design.
Printing
The next step is to print the circuit pattern onto the substrate through printing technology. Photolithography technology is usually used, that is, the circuit pattern is transferred to the photosensitive covering layer on the surface of the substrate, and then chemical etching is used to remove the unnecessary parts, leaving the desired circuit pattern.
Heat treatment
After printing is completed, the substrate needs to go through a series of heat treatment processes. These processes include preheating, lamination, baking, etc., which are designed to cure the printed circuit pattern so that it can be closely combined with the substrate surface to improve the stability and reliability of the connection.
Welding
After completing the fabrication of the circuit pattern, the next step is to solder the chips and other electronic components to the substrate. In FC-LGA substrates, flip-chip packaging technology is usually used, that is, the chip is flipped onto the substrate through welding and connected to the substrate using solder balls. This requires high-precision equipment and precise process control to ensure the quality and stability of welding.
The entire manufacturing process requires strict process control and quality management to ensure that the quality and performance of the final product meet expected standards. Only carefully designed and precision-manufactured FC-LGA substrates can provide stable and reliable connections and support for electronic devices to meet the needs of different application scenarios.
The Application area of FC-LGA Substrates.
As an advanced electronic connection technology, FC-LGA substrate plays an indispensable role in modern electronic equipment. Its stable and reliable connection and excellent performance make it widely used in various application fields.
First of all, FC-LGA substrate plays an important role in the field of smartphones. As a necessity for people’s daily lives, smartphones have extremely high requirements for connection stability and performance. The precision design and reliable connection of the FC-LGA substrate ensure effective communication between various components inside the mobile phone, thus ensuring the overall performance and stability of the mobile phone.
Secondly, tablet computers are also one of the important application areas of FC-LGA substrates. The thin and light design and high performance requirements of tablet computers pose challenges to circuit connection technology. With its compact size and reliable connections, the FC-LGA substrate provides stable circuit support for tablets, allowing the device to achieve excellent performance while maintaining a lightweight design.
In addition, the server and network equipment fields are also important application scenarios for FC-LGA substrates. Servers and network equipment need to process large amounts of data and complex computing tasks, and have extremely high requirements on the stability and performance of circuit connections. FC-LGA substrate provides reliable circuit support for servers and network equipment through its excellent signal transmission performance and thermal management capabilities, ensuring the stable operation and efficient work of the equipment.
In general, FC-LGA substrates play an important role in electronic devices such as smartphones, tablets, servers, and network equipment. Its stable and reliable connections and excellent performance make it an indispensable component of modern electronic products. part. With the continuous development and innovation of technology, the application fields of FC-LGA substrates will continue to expand, bringing more development opportunities to the electronics industry.
What are the advantages of FC-LGA Substrates?
FC-LGA substrate has many advantages over traditional welding methods, which make it one of the preferred technologies for modern electronic manufacturing.
First, FC-LGA substrate has higher reliability. Traditional welding methods may have problems such as poor welding and broken solder joints. The FC-LGA substrate uses flip-chip packaging technology, which allows the chip to be directly connected to the substrate, reducing the resistance and inductance of the connection and improving the stability of signal transmission. , thereby enhancing the reliability of the entire circuit.
Secondly, FC-LGA substrate has better thermal management capabilities. Flip-chip packaging makes the contact between the chip and the substrate closer, effectively improving the heat conduction efficiency, thereby reducing the chip operating temperature and extending the service life of the equipment. In addition, FC-LGA substrates usually use materials with high thermal conductivity, such as metal heat sinks, thermal conductive glue, etc., to further improve thermal management performance.
In addition, FC-LGA substrate has higher integration level. Flip-chip packaging technology can achieve high-density connections between chips and substrates, making the circuit layout more compact, thereby achieving higher integration and smaller size. This not only helps improve the performance and functionality of the device, but also reduces the size and weight of the product, meeting the needs of modern electronic devices for miniaturization and lightweighting.
In addition, FC-LGA substrates can also improve production efficiency and reduce costs. Flip-chip packaging technology can realize automated production, reduce manual operations, and improve production efficiency. Moreover, due to the high reliability and stability of the FC-LGA substrate, product maintenance and replacement costs are reduced, and the overall production cost is reduced.
In general, FC-LGA substrate, as an advanced connection technology, has higher reliability, better thermal management capabilities and higher integration. It can also improve production efficiency and reduce costs, providing opportunities for electronic manufacturing. Industry has brought great convenience and benefits. In the future design and manufacturing of electronic equipment, FC-LGA substrates will continue to play an important role in promoting the continuous development and progress of the electronics industry.
FAQ
What are the advantages of FC-LGA substrate compared to other connection technologies?
FC-LGA substrate has many advantages compared with traditional welding technology. First, it uses flip-chip packaging technology to connect the chip directly to the substrate, reducing the length of the connection line and improving signal transmission speed and stability. Secondly, the connection method of FC-LGA substrate adopts Land Grid Array (LGA) design, which enhances the reliability and durability of the connection and reduces the risk of disconnection or poor contact. In addition, the FC-LGA substrate has better thermal management capabilities and can effectively dissipate heat, improving the performance and stability of electronic equipment.
What issues need to be paid attention to in the design of FC-LGA substrate?
When designing an FC-LGA substrate, many factors need to be taken into consideration to ensure its performance and reliability. First of all, the circuit needs to be laid out rationally to ensure that the signal transmission path is short and reasonably distributed to reduce signal interference. Secondly, good thermal management design should be considered, including the layout of heat dissipation holes and the selection of heat dissipation materials, to prevent the chip from overheating and affecting performance. In addition, attention should be paid to selecting appropriate materials and processes to ensure the stability of the manufacturing process and the quality of the product.
What is the manufacturing process of FC-LGA substrate?
The manufacturing process of FC-LGA substrate includes multiple steps, starting with circuit design and layout, and then printing the circuit pattern onto the substrate through printing technology. Then heat treatment is performed so that the surface of the substrate is coated with a conductive layer for connecting the chip. Finally, the welding process is carried out to flip-chip the chip onto the substrate and conduct testing and inspection to ensure that the product meets the specifications.
What application fields is FC-LGA substrate suitable for?
FC-LGA substrates are widely used in various electronic devices, including smartphones, tablets, servers, network equipment, etc. Its stable and reliable connection and excellent performance make it an indispensable part of modern electronic products. At the same time, because the FC-LGA substrate has a smaller size and higher integration level, it is also suitable for some application scenarios with high size and performance requirements, such as medical equipment, aerospace and other fields.
What are the maintenance and repair methods of FC-LGA substrate?
Generally, the maintenance and repair of FC-LGA substrates requires professional technical support and equipment. If problems such as connection failure or poor welding occur, it is recommended to contact the original factory or a professional maintenance agency for inspection and maintenance in time. In addition, excessive vibration and collision should be avoided during use to maintain the stability and safety of the equipment and extend the service life of the FC-LGA substrate.