FC-LGA Package Substrates Manufacturer.FC-LGA package substrates manufacturer specializes in crafting high-quality substrates tailored for FC-LGA packages, ensuring optimal performance and reliability in electronic devices. With cutting-edge technology and meticulous attention to detail, they produce substrates that meet stringent industry standards. Their expertise lies in designing and manufacturing substrates that facilitate seamless integration and robust connectivity, enabling electronic devices to function flawlessly. Whether for consumer electronics or industrial applications, their commitment to excellence ensures that every substrate they produce delivers exceptional performance, making them a trusted partner for leading electronic manufacturers worldwide.
With the rapid development of electronic technology, FC-LGA (Flip Chip – Land Grid Array) packaging substrate has become an indispensable and important component in modern electronic products. It has significant advantages in improving signal transmission speed, enhancing system performance and supporting high-density integration. This article will introduce in detail the definition, design guidelines, material selection, size specifications, manufacturing process, application fields and its unique advantages of FC-LGA packaging substrate. It aims to provide readers with a comprehensive understanding and guidance, and help to make more practical applications. Good selection and design of appropriate packaging substrates.
What are FC-LGA Package Substrates?
FC-LGA (Flip Chip – Land Grid Array) packaging substrate is an advanced packaging technology that is widely used in the connection of high-performance integrated circuits (ICs). It can significantly improve signal transmission speed and system performance by flipping the chip directly onto the substrate.
Traditional IC packaging technology usually uses wire bonding to connect the chip to the substrate. However, this method has many limitations, especially in high-speed and high-density applications, where the electrical performance of wire bonding often fails to meet the needs. In contrast, FC-LGA packaging technology has many unique advantages.
First, the FC-LGA packaging substrate directly connects the chip’s solder balls (solder bumps) to the contact pads (pads) on the substrate through flip chip technology. This method reduces the length of the signal transmission path, thereby reducing signal delay and loss, and significantly increasing the signal transmission speed. In addition, flip-chips can also support higher pin density, allowing the package to accommodate more signal channels and meet the needs of complex circuits.
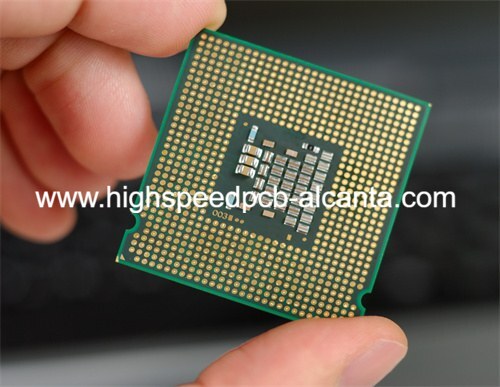
FC-LGA Package Substrates Manufacturer
Secondly, the thermal performance of FC-LGA packaging substrate is also much better than traditional packaging. The flip-chip design increases the contact area between the chip and the substrate, improves the heat conduction path, effectively reduces the chip’s operating temperature, and improves the reliability and stability of the system. Especially in high-performance computing and communication equipment, good heat dissipation performance is a key factor to ensure long-term stable operation of the system.
In addition, the FC-LGA packaging substrate has better mechanical and electrical properties. Traditional wire bonding methods are prone to connection breakage when subjected to mechanical stress, while flip-chip solder ball connections are stronger and more resistant to mechanical stress, reducing connection failures caused by mechanical vibration or thermal expansion. At the same time, the low inductance and low resistance characteristics of the solder ball connection make the electrical performance more superior and meet the needs of high-speed signal transmission.
In practical applications, FC-LGA packaging substrates are widely used in high-performance computing, communication equipment, medical electronics, automotive electronics, aerospace and other fields. Especially in high-density and high-performance ICs such as servers, CPUs, GPUs and ASICs, FC-LGA packaging technology has become a standard choice. As the performance and reliability requirements of electronic products continue to increase, the application prospects of FC-LGA packaging substrates will be broader.
To sum up, FC-LGA packaging substrate, as an advanced packaging technology, is gradually becoming the mainstream choice for high-performance IC packaging due to its significant advantages in signal transmission speed, thermal management, mechanical performance and electrical performance. Through continuous technological innovation and optimization, FC-LGA packaging substrate will provide more powerful support for the performance improvement and function expansion of electronic products.
FC-LGA Package Substrates design Reference Guide.
When designing an FC-LGA packaging substrate, several key factors need to be considered, including electrical performance, thermal performance, mechanical strength and manufacturing feasibility. Each factor has an important impact on the performance and reliability of the final product, so designers must consider these factors during the design process to ensure the success of the design.
Electrical properties
Electrical performance is the core of FC-LGA package substrate design. Designers need to ensure the integrity of signal transmission and the stability of power distribution. First, designers need to understand how the chip is electrically connected to the substrate, which typically involves using solder balls or bumps to connect the chip and substrate. In order to ensure signal integrity, the signal path must be optimized to reduce signal reflection and crosstalk. This can be achieved by controlling the length, width and spacing of the wiring, as well as using differential signaling and shielding techniques.
Thermal properties
High-performance chips generate a lot of heat during operation, and good thermal management is the key to ensuring system stability and lifespan. Designers need to design effective thermal conduction paths to quickly transfer the heat generated by the chip to the substrate and further dissipate it. This is usually achieved by using highly thermally conductive materials, adding thermal vias and fins, and optimizing the heat distribution design of the substrate. Additionally, thermal simulation tools can help designers predict and optimize thermal performance during the design phase.
Mechanical strength
FC-LGA packaging substrates need to withstand various mechanical stresses during use, including thermal expansion and contraction, mechanical vibration and impact caused by thermal cycles. Designers need to choose materials with good mechanical strength and toughness, such as glass fiber reinforced resin, and optimize the structural design of the substrate to enhance its stress resistance. For example, the mechanical strength of the substrate can be improved by increasing the copper layer thickness and optimizing the via distribution.
Manufacturing feasibility
Designers must also consider the feasibility and cost of the manufacturing process when designing FC-LGA packaging substrates. Complex designs may require higher manufacturing precision and more process steps, increasing production costs and time. Therefore, designers need to find a balance between performance and cost. Selecting appropriate manufacturing processes and equipment, adopting standardized designs, and simplifying the manufacturing process as much as possible can help improve production efficiency and reduce costs.
Signal integrity and power distribution consistency
In order to ensure signal integrity and consistent power distribution, designers need to carefully plan the layout of power and ground planes in the design to reduce power supply noise and ground bounce. The use of multi-layer board design can effectively separate the power and signal layers and reduce mutual interference. In addition, the use of decoupling capacitors and filters can further stabilize power distribution and ensure that the chip can obtain a stable power supply under various operating conditions.
In summary, designing an FC-LGA packaging substrate is a complex process that requires comprehensive consideration of multiple factors such as electrical performance, thermal performance, mechanical strength, and manufacturing feasibility. Through reasonable design and optimization, the FC-LGA packaging substrate can be ensured to perform excellent functions and reliability in high-performance electronic products.
What material is used in FC-LGA Package Substrates?
The material selection of FC-LGA packaging substrate is crucial because it directly affects the electrical performance, mechanical strength and thermal management capabilities of the substrate. The following are several commonly used FC-LGA packaging substrate materials and their characteristics:
Glass fiber reinforced resin (such as FR-4)
FR-4 is a common substrate material composed of fiberglass and epoxy resin. It has excellent mechanical strength and electrical insulation properties and can withstand high temperature and high humidity environments. In addition, FR-4 materials have low cost, are easy to process, and are suitable for mass production. FR-4 is typically used in electronics with general performance requirements, but in high-frequency and high-performance applications, higher performance materials may be required.
High frequency materials (such as PTFE)
Polytetrafluoroethylene (PTFE) is a high-frequency material commonly used in applications requiring high-frequency signal transmission. PTFE material has extremely low dielectric constant and dielectric loss, which can ensure the integrity of signal transmission at high frequencies. It also has excellent heat resistance and chemical stability. Due to these excellent properties, PTFE is often used in high-frequency communication equipment, radar systems and high-speed computers. However, PTFE materials are more expensive and difficult to process, so performance and cost need to be weighed when choosing.
Copper foil
Copper foil is the main component of the conductive layer in the substrate material. Copper has excellent electrical and thermal conductivity, making it an ideal circuit conductor material. In FC-LGA packaging substrates, copper foil is usually attached to the substrate through electroplating or copper cladding processes. The thickness and quality of copper foil directly affect the conductive performance and thermal management capabilities of the substrate. In order to reduce losses in signal transmission and improve heat dissipation efficiency, high-quality, uniform thickness copper foil is crucial.
Solder mask
Solder mask is a protective coating covering copper conductors. Its main function is to prevent copper lines from oxidation, short circuits and accidental soldering. Common solder mask materials include epoxy resin and UV-curable resin. A solder mask not only improves the durability of the substrate but also improves its appearance. In high-density and high-precision FC-LGA packaging substrates, solder masks can effectively prevent solder bridging problems and ensure circuit reliability.
Choosing the right material requires trade-offs based on specific application scenarios and performance requirements. For example, in communication equipment that requires high-frequency signal transmission, you may be more inclined to choose high-frequency materials such as PTFE; while in general electronic products, FR-4 materials are sufficient to meet the needs. At the same time, the processing difficulty and cost of the material need to be considered to achieve a balance between performance and economy.
In short, the selection of FC-LGA packaging substrate materials is a complex process that requires comprehensive consideration of electrical performance, mechanical strength, thermal management, cost and other factors. Only through reasonable material selection can the substrate be ensured to have excellent performance and reliability in practical applications.
What size are FC-LGA Package Substrates?
FC-LGA (Flip Chip – Land Grid Array) packaging substrates come in various sizes, ranging from a few millimeters to tens of millimeters, depending on the chip size and application requirements. Standard sizes generally conform to industry standards, but can also be customized to meet specific needs. The size of the FC-LGA package substrate and its related considerations will be discussed in detail below.
First of all, the size range of FC-LGA packaging substrates is relatively wide, which can meet the needs of different types of chips and electronic products. The smaller FC-LGA packaging substrate can be only a few millimeters square and is often used in miniaturized consumer electronics and mobile devices, such as smartphones and wearable devices. This type of small-sized packaging substrate has the characteristics of high density and high integration, which can realize the layout of complex circuits in a limited space and meet the needs of equipment for miniaturization and lightweight.
Medium-sized FC-LGA packaging substrates are usually between 10 mm and 20 mm and are widely used in computers and communication equipment. For example, various control chips and interface chips on the motherboard often use medium-sized FC-LGA packaging substrates. This type of substrate requires a large number of pins and signal lines to be arranged in a limited area, so special attention must be paid to signal integrity and thermal management issues during the design and manufacturing process.
Larger-sized FC-LGA packaging substrates can reach tens of millimeters or even larger, and are mainly used in high-performance computing equipment, servers, and professional graphics processors (GPUs). This type of substrate usually needs to carry more electrical connections and more complex circuit structures, so higher mechanical strength and better heat dissipation performance need to be considered during design. In addition, large-size packaging substrates also require more manufacturing challenges, such as precision control of processes such as lamination, drilling, and electroplating.
When determining the size of the FC-LGA package substrate, multiple factors need to be considered. The first is the size of the chip itself, which is the basic basis for substrate size selection. Secondly, there are application requirements, including electrical performance requirements, thermal management requirements and mechanical strength requirements. For example, high-performance computing devices often require larger substrates to provide better thermal performance and higher electrical performance, while mobile devices tend to choose miniaturized substrates to achieve a balance between portability and aesthetics.
Standard size FC-LGA packaging substrates usually comply with industry standards, which are formulated by relevant industry organizations or standardization bodies, such as JEDEC (Joint Electronic Devices Engineering Committee) and IPC (International Electronic Industry Connectivity Association). These standard sizes help achieve compatibility and interchangeability between different manufacturers, improve production efficiency and reduce costs. However, for some specific applications or customized needs, non-standard size FC-LGA packaging substrates are also widely used. These custom sizes better meet the needs of specific applications, but require more time and resources to be invested in the design and manufacturing process.
To sum up, FC-LGA packaging substrates come in various sizes, depending on the size of the chip and specific application requirements. Standard sizes help improve productivity and compatibility, while custom sizes meet the unique needs of specific applications. When designing the FC-LGA packaging substrate, multiple factors such as electrical performance, thermal management, and mechanical strength need to be comprehensively considered to ensure that the final product can perform well in actual applications.
The Manufacturer Process of FC-LGA Package Substrates.
The process of manufacturing FC-LGA packaging substrates includes multiple critical steps, each of which requires precise operations and strict quality control to ensure the performance and reliability of the final product. The following is the detailed manufacturing process:
Design and layout
Before manufacturing the FC-LGA packaging substrate, detailed design and layout first need to be carried out. This step requires engineers to design an optimized substrate layout based on specific electrical and mechanical requirements. Factors such as signal transmission integrity, power distribution consistency, thermal management, and mechanical strength must be taken into consideration during the design process. Advanced EDA (Electronic Design Automation) tools are often used at this stage to allow for accurate electrical simulation and thermal analysis.
Lithography and Etching
After the design is completed, the next step is the photolithography and etching process. First, the designed circuit pattern is transferred to the substrate material through photolithography technology. Photolithography uses photosensitive materials (photoresist) to undergo chemical changes under ultraviolet light irradiation to reveal circuit patterns on the substrate. Then, the unprotected copper foil portion is removed through chemical etching to form the required circuit pattern. The accuracy of this step directly affects the performance and reliability of the circuit, so strict control and detection are required.
Lamination and drilling
After photolithography and etching are completed, lamination and drilling operations are performed. The lamination process of multi-layer substrates is to press multiple layers of prefabricated substrate materials together under high temperature and high pressure to form a whole. After lamination, precision drilling is required in the substrate to prepare it for subsequent plating and electrical connections. These hole locations (through holes and blind holes) must be accurate to ensure that signals and power can pass smoothly.
Electroplating and surface treatment
After drilling is completed, electroplating and surface treatment are performed. First, electroplating technology is used to plate a thin layer of copper on the inner wall of the drilled hole and the circuit pattern to enhance conductivity. Then, surface treatment is performed, including pad gold plating, nickel gold or other anti-oxidation treatments to protect the circuit and improve soldering performance and reliability. Each step in the process requires highly precise control to ensure surface finish and conductive properties.
Chip flipping
The final step is chip flipping. At this time, the processed chip is flipped directly onto the substrate through solder balls (usually tin-lead alloy or lead-free solder). Chip flipping requires sophisticated equipment and technology to ensure that the solder joints between the chip and the substrate are fully aligned and firmly connected. The flip-chip process not only affects electrical performance, but also involves thermal management and mechanical stability, so it requires special care. After flip-chip is completed, a series of tests are usually required, including electrical performance testing and environmental durability testing, to ensure that the packaging substrate can work stably in actual applications.
Through the manufacturing process of the above detailed steps, the FC-LGA packaging substrate can meet the requirements of high performance and high reliability, and is widely used in computers, communication equipment, medical equipment, automotive electronics, aerospace and other fields. Strict control and fine operation of each step ensure the quality and performance of the final product, meeting the needs of various high-end applications.
The Application area of FC-LGA Package Substrates.
FC-LGA packaging substrate is widely used in various high-performance and high-density electronic products, including the following important fields:
Computers and Servers
In computers and servers, FC-LGA packaging substrates play a vital role. High-performance processors (such as CPUs and GPUs) often use FC-LGA packaging because this packaging method can provide high-speed data transmission and excellent heat dissipation performance, thus meeting the needs of computers and servers for high computing speed and reliability. Especially in data centers and cloud computing environments, FC-LGA packaging substrates help improve the overall performance and efficiency of the system.
Communication device
With the popularization of 5G technology and the rapid development of the Internet of Things (IoT), communication equipment has increasing demand for high-frequency and high-density integrated circuits. FC-LGA packaging substrates are widely used in communication equipment such as base stations, routers and switches. Its excellent electrical performance and thermal management capabilities ensure the stable operation of communication equipment under high frequency and high load. At the same time, the miniaturization characteristics of the FC-LGA packaging substrate help reduce the size of the equipment and improve space utilization.
Medical instruments
In the field of medical devices, the application of FC-LGA packaging substrates is also indispensable. Modern medical equipment, such as high-resolution imaging equipment (such as MRI, CT scanners) and portable monitoring equipment (such as electrocardiographs, blood glucose meters), require high-precision and high-reliability electronic components. FC-LGA packaging substrate provides stable electrical connection and excellent signal transmission performance, ensuring accurate measurement and reliable operation of medical equipment. In addition, the miniaturization and lightweight design based on FC-LGA technology promotes the development of portable medical equipment and improves patient convenience.
Vehicle electronics
Automotive electronic systems continue to increase in complexity and functionality, especially driven by autonomous driving and electric vehicle technologies. FC-LGA packaging substrate plays an important role in automotive electronic systems and is widely used in engine control units (ECUs), advanced driver assistance systems (ADAS) and in-vehicle entertainment systems. Its superior heat dissipation performance and high reliability ensure that electronic systems can operate stably and efficiently in harsh automotive environments.
Aerospace Electronics
In the aerospace industry, electronic systems have extremely stringent reliability and performance requirements. FC-LGA packaging substrate has become the first choice for avionics equipment and spacecraft electronic systems due to its high reliability, high density and excellent electrical performance. Whether in flight control systems, navigation systems, or satellite communication systems, FC-LGA packaging substrates can provide stable and reliable performance to ensure the normal operation of spacecraft in extreme environments. In addition, its efficient thermal management capabilities help maintain the normal temperature of electronic systems in the low gravity and high radiation space environment.
Through the detailed introduction of the above application fields, we can see the importance of FC-LGA packaging substrate in modern high-performance and high-density electronic products. Its excellent electrical performance, thermal management capabilities and reliability ensure the efficient and stable operation of various complex electronic systems. With the continuous advancement of technology, the application prospects of FC-LGA packaging substrates will be broader, promoting the birth of more innovative electronic products.
What are the advantages of FC-LGA Package Substrates?
Compared with traditional packaging methods, FC-LGA (Flip Chip – Land Grid Array) packaging substrate has many advantages, making it widely used in high-performance and high-density electronic products. The following are the detailed advantages of FC-LGA packaging substrates in several key aspects:
High performance
FC-LGA packaging substrate significantly improves signal transmission speed and electrical performance. Traditional packaging methods usually use wire bonding or pin connection, and the signal transmission path is long, which is easily affected by parasitic inductance and parasitic capacitance, resulting in signal attenuation and delay. The FC-LGA package uses flip-chip technology, which allows the chip to be directly connected to the substrate, greatly shortening the signal transmission path, reducing signal attenuation and delay, thereby improving the overall performance of the system. This is particularly important for applications requiring high-speed signal transmission, such as processors and communications equipment.
Miniaturization
Modern electronic products have increasingly higher requirements on size and weight, and FC-LGA packaging substrates perform well in this regard. Because flip-chip technology makes the connection between the chip and the substrate more compact, a higher level of integration can be achieved. This not only helps reduce the size and weight of electronic products, but also enables the integration of more functions in a limited space. This is especially critical for mobile devices, wearables and other electronics that need to be lightweight and miniaturized.
Reliability
FC-LGA packaging substrate also has significant advantages in improving system reliability. Traditional wire bonding and pin connection methods are prone to connection failure when faced with thermal cycles and mechanical stress. The FC-LGA package directly fixes the chip to the substrate through solder balls. It has fewer connection points and is more stable, significantly reducing the risk of connection failure. In addition, flip-chip technology reduces the physical stress between the chip and the substrate, improving the reliability of the entire system, especially in harsh working environments.
Thermal performance
As the performance of electronic devices continues to improve, thermal management has become a critical issue. FC-LGA packaging substrate also has obvious advantages in heat dissipation performance. Since the chip is flipped directly onto the substrate, heat can be conducted to the substrate more efficiently and dissipated quickly through the heat dissipation channels on the substrate. This improved thermal management design effectively reduces the operating temperature of the chip and improves the stability and life of the system. In applications that require efficient heat dissipation, such as high-performance computing and power electronic equipment, the heat dissipation advantages of FC-LGA packaging substrates are particularly obvious.
To sum up, FC-LGA packaging substrate has become an indispensable core component of modern electronic products due to its significant advantages in high performance, miniaturization, reliability and heat dissipation performance. It can meet the ever-increasing performance requirements of electronic products and adapt to various harsh application environments. It is an important direction for the development of electronic packaging technology in the future.
FAQ
What is FC-LGA packaging substrate?
FC-LGA (Flip Chip – Land Grid Array) packaging substrate is a packaging technology that flips the chip onto the substrate and achieves electrical connection through solder balls. Compared with traditional packaging methods, FC-LGA can provide higher signal transmission speed and better thermal management performance, and is suitable for high-performance and high-density integrated circuits.
What are the main materials for FC-LGA packaging substrate?
Commonly used materials include fiberglass reinforced resin (such as FR-4), high-frequency materials (such as PTFE), copper foil, solder masks, and thermally conductive materials. The selection of these materials needs to be weighed based on specific application scenarios and performance requirements to ensure that the substrate has good electrical properties, mechanical strength and heat dissipation capabilities.
What types of chips are FC-LGA packaging substrates suitable for?
FC-LGA packaging substrate is mainly used for high-performance, high-density integrated circuits, such as central processing units (CPUs), graphics processing units (GPUs), application-specific integrated circuits (ASICs) and various high-frequency communication chips. These chips have high requirements for signal transmission speed and thermal management, and FC-LGA packaging can effectively meet these requirements.
How to choose the appropriate FC-LGA packaging substrate material?
When selecting materials, factors such as electrical properties, thermal properties, mechanical strength and manufacturing costs need to be considered. For example, high-frequency materials such as PTFE can be selected for high-frequency applications, while FR-4 can be selected for general applications. In addition, the heat dissipation needs of the substrate must also be considered and appropriate thermal conductive materials must be selected to ensure the stability of the chip under high-power operation.