Embedded Components PCB Manufacturing.Embedded Components PCB Manufacturing refers to the process of integrating electronic components directly onto the printed circuit board (PCB) during fabrication. This advanced technique eliminates the need for separate assembly, reducing production costs and enhancing reliability. Through precision engineering, components such as resistors, capacitors, and integrated circuits are seamlessly embedded within the PCB substrate. This method streamlines the assembly process, minimizes soldering errors, and optimizes space utilization within electronic devices. Embedded Components PCB Manufacturing revolutionizes electronics manufacturing, offering compact, lightweight, and durable solutions for a wide range of applications, from consumer electronics to aerospace systems.
In the electronics industry, embedded component PCB manufacturing plays a vital role. Embedded Components PCB manufacturing is a precise and complex process involving many aspects from design to cost estimation. This article will take you deep into all aspects of embedded component PCB manufacturing and present you with a comprehensive guide. The development of embedded component PCB technology has become an important trend in the field of electronic equipment manufacturing. It not only improves the integration and reliability of circuit boards, but also greatly saves the volume and weight of products.
What is an embedded component PCB?
Embedded Components PCB (Embedded Components PCB) is an innovative and advanced PCB manufacturing technology that embeds electronic components directly into the PCB board, thereby achieving the compact design and high performance requirements of the circuit board. Compared with traditional surface assembly technology, embedded component PCB can use space more efficiently and improve the density and functionality of the circuit board. So, how to embed electronic components directly into the PCB board?
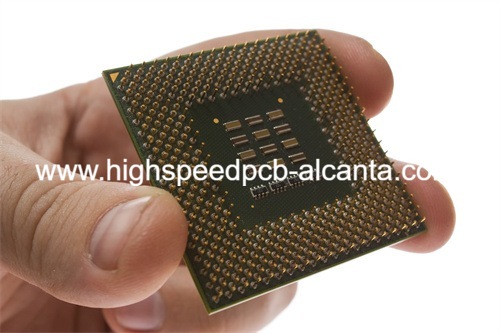
Embedded Components PCB Manufacturing
First, the manufacturing process of embedded component PCB starts with the preparation of raw materials. Usually, manufacturers choose high-quality fiberglass reinforced resin (FR-4) as the substrate material because it has good insulation properties and mechanical strength, making it suitable for the manufacture of electronic equipment.
Next, the designer will use CAD software to design and layout the circuit based on circuit requirements and space constraints. When designing a circuit, designers need to consider the size, arrangement, and connection of components with other components to ensure the stability and reliability of the circuit.
The manufacturer then prints the circuit layer onto the substrate and removes the excess copper layer through steps such as chemical etching and cleaning to form the outlines and connection points of the circuit. This process requires high-precision equipment and process control to ensure the accuracy and quality of the circuit.
After the circuit is formed, manufacturers perform processing processes such as drilling and electroplating to prepare for further processing and assembly of the circuit board. Drilling is to make holes in the circuit board to install components and make connections; while electroplating is to form a conductive layer on the hole wall to enhance the stability and reliability of the connection.
Finally, the manufacturer will embed the electronic components directly into the PCB board and fix it on the board through welding and other processes. Compared with traditional surface assembly technology, embedded component PCB does not require additional component mounting and connection steps, thus greatly simplifying the manufacturing process and improving production efficiency and quality control levels.
In general, embedded component PCB embeds electronic components directly into the PCB board through precise design and manufacturing processes, achieving the compact design and high-performance requirements of the circuit board. The application of this technology will bring new possibilities and opportunities to the manufacturing and application of electronic devices.
What is the design process for embedded component PCB?
Embedded component PCB design is a precise and critical process, which directly affects the performance and reliability of the final product. Designers need to go through a series of steps to ensure that the PCB design meets the requirements and fully functions.
Determine design requirements: First, designers need to fully communicate with customers to understand the functional requirements, performance indicators and special requirements of the product. This information will guide designers to make reasonable decisions in the subsequent design process.
Schematic design: After determining the design requirements, the designer will begin schematic design. They will draw the schematic diagram of the PCB based on the requirements and circuit functions provided by the customer. The key at this stage is to accurately understand the circuit structure and ensure that the connections and functions of each component are correctly represented.
Placement and routing: Once the schematic design is completed, the next step is the placement and routing stage. Designers need to consider the location and connection of components, as well as the size and shape of the PCB board. They use CAD software to place components and connect them, paying attention to the path and length of wiring to ensure the stability and reliability of signal transmission.
Embedded component selection: During the layout and routing process, designers need to select suitable embedded components. The selection of these components depends on the product’s functional requirements, performance specifications, and budget constraints. Designers need to weigh various factors to ensure that the selected components can meet the requirements of the product and match the design of the PCB board.
CAD software design and simulation: CAD software plays an important role in the entire design process. Designers use CAD software for design and simulation, which can quickly verify the feasibility of the design plan and make necessary adjustments and optimizations. Through the simulation function of CAD software, designers can simulate the working conditions of circuits, predict potential problems and solve them in time.
Review and revision: After the design is completed, the design team will conduct a comprehensive review of the PCB design. They will check various aspects such as circuit connections, component layout, wiring paths, etc. to ensure that the design meets the requirements and is error-free. If necessary, the designer will make modifications and optimizations until the customer’s needs and standards are met.
Generate design files: Finally, the designer will generate corresponding manufacturing files based on the designed PCB files. These files include layout diagrams, layer stack diagrams, Gerber files, etc., which will be used in the subsequent PCB manufacturing process.
To sum up, the design process of embedded component PCB involves multiple key steps, from schematic design to application of CAD software, to final review and file generation. Each step is crucial and requires designers to carefully Design and strict control.
What is the manufacturing process of embedded component PCB?
Manufacturing embedded component PCB is a complex and precise process, involving precise operation and strict control of multiple links. The following are the main process steps for manufacturing embedded component PCBs and how they are completed:
Before manufacturing embedded component PCB, the required substrate materials, electronic components, covering layer materials, etc. need to be prepared. These materials must meet specific standards and specifications to ensure the quality and performance of the final product.
First, conductive ink or other conductive materials are coated on the surface of the substrate through a printing process to form a conductive pattern. This step usually uses screen printing technology to evenly coat conductive materials on the surface of the substrate through a template to form the required circuit pattern.
Next, the electronic components need to be precisely positioned on the conductive layer. This step is usually accomplished with the help of automated equipment, which uses visual recognition and mechanical positioning to accurately place the components in their predetermined positions.
After positioning the components, the next step is to solder the components with the conductive layer. Surface mount technology (SMT) or other soldering processes are usually used to fix the components on the conductive layer by heating and melting the solder and ensuring a good electrical connection.
After the embedded components are soldered, they need to be covered with a protective material (usually resin or polymer) to protect the circuit from the external environment. This step is usually accomplished by coating or spraying to ensure that the covering layer evenly and completely covers the entire circuit board surface.
After completing all process steps, the manufactured embedded component PCB needs to be subjected to final inspection and testing. This includes visual inspection, electrical testing, functional testing, etc. to ensure that the product meets design requirements and customer needs.
Through precise control and optimization of the above process steps, manufacturers can produce high-quality, highly reliable embedded component PCBs to meet the needs of various application fields.
How to estimate the cost of embedded component PCB?
When estimating the cost of an embedded component PCB, there are several factors that need to be considered, and these factors will directly affect the price of the final product. Here are some of the main factors:
The cost of embedded component PCBs is affected by the materials chosen. Different types of substrates, copper thickness, embedded component materials, etc. will all have an impact on costs. Generally speaking, using high-performance materials will increase costs, while low-cost materials may sacrifice certain performance and quality.
The process steps and technologies required to manufacture embedded component PCBs are also important factors affecting costs. For example, some special process requirements or the need for additional processing steps may increase costs. High-precision processing equipment and technology may also increase manufacturing costs.
PCB board design and quantity are another key factor affecting cost. Generally speaking, customized PCB design and low-volume production will cost more than mass production. In addition, PCBs with special shapes or layers may require additional processing steps, further increasing costs.
The type, specification and quantity of embedded components will directly affect the cost. Some special models or mass-customized components may become a major source of cost. In addition, the availability of embedded components and supply chain conditions may also affect costs.
Different manufacturers and supply chain channels will have different impacts on the cost of embedded component PCBs. Some manufacturers may offer more competitive prices, but there may be differences in quality and service. Choosing the right manufacturers and supply chain partners is important to controlling costs.
When estimating the cost of embedded component PCBs, you also need to take into account the additional services and fees that may be involved, such as sample production, fast delivery, special packaging, etc. These additional services and fees will have an impact on the total cost.
To sum up, the cost estimation of embedded component PCB involves multiple factors, including material cost, manufacturing process, board type and quantity, embedded component cost, manufacturer and supply chain, etc. Understanding and rationally evaluating these factors can help customers more accurately estimate the cost of embedded component PCBs and make appropriate decisions.
What materials are used in embedded component PCBs?
When manufacturing embedded component PCBs, commonly used materials include FR-4, FR-5, polyimide (PI), polyetherketone (PEEK), etc. Each material has unique characteristics and applicable scenarios, and we will introduce them one by one below.
FR-4 is one of the most commonly used PCB substrate materials with good mechanical properties, insulation properties and thermal stability. Features include:
Good electrical properties: It has good insulation and dielectric properties to meet the requirements of most applications.
High mechanical strength: It has high mechanical strength and stiffness, and is suitable for scenarios that need to withstand certain mechanical stress.
Good heat resistance: It has good high temperature resistance and is suitable for applications in high temperature environments.
Applicable scenarios: FR-4 is commonly used in PCB manufacturing in general electronic products, communication equipment, computer equipment and other fields.
FR-5 is an improved material of FR-4 with higher glass transition temperature and thermal stability. Features include:
Higher thermal stability: Has a higher glass transition temperature and can maintain stability at higher temperatures.
Better mechanical properties: Compared with FR-4, FR-5 has better mechanical strength and heat resistance.
Excellent chemical resistance: good resistance to chemical solvents and corrosive substances.
Applicable scenarios: FR-5 is often used in PCB manufacturing in high-end electronic products, aerospace equipment and other fields that require high temperature resistance and chemical corrosion resistance.
Polyimide is a high-performance engineering plastic with excellent temperature resistance, insulation and chemical stability. Features include:
Extremely low dielectric constant and dielectric loss: excellent high frequency performance and signal transmission performance.
Ultra-high temperature resistance: With extremely high glass transition temperature and thermal stability, it can maintain stability under extreme high temperatures.
Excellent mechanical properties: It has good mechanical strength and stiffness and is suitable for high-demand application scenarios.
Applicable scenarios: Polyimide is often used in PCB manufacturing in high-frequency communication equipment, aerospace equipment, medical equipment and other fields. It is especially suitable for applications in special environments such as high temperature, high frequency and high-speed transmission.
Polyetherketone is a high-performance thermoplastic with excellent temperature resistance, chemical stability and mechanical properties. Features include:
High temperature resistance: It has a high glass transition temperature and thermal stability, and can maintain stability under extreme high temperatures.
Excellent chemical stability: good resistance to chemical solvents and corrosive substances.
Good mechanical properties: It has high mechanical strength, stiffness and wear resistance, and is suitable for high-demand application scenarios.
Applicable scenarios: Polyetherketone is often used in PCB manufacturing in electronic products, auto parts, medical equipment and other fields under harsh environments such as high temperature, high pressure and chemical corrosion.
By selecting appropriate materials, PCB manufacturing needs can be met in different scenarios and product performance and reliability can be improved.
Who makes embedded component PCBs?
The manufacturing of embedded component PCBs involves a variety of specialized technologies and equipment, so the choice of manufacturer is crucial. When choosing a manufacturer, customers need to consider factors such as its technical strength, equipment sophistication, quality control level, and customer service quality. Below we will introduce our company’s advantages and services as an embedded component PCB manufacturer.
As a professional embedded component PCB manufacturer, our company has advanced production equipment and technical team. We use the latest PCB manufacturing technology, have high-precision printing equipment, advanced etching machines and drilling machines, etc., to meet customers’ needs for various complex PCB boards.
Our company focuses on product quality and implements strict quality control processes. From raw material procurement to manufacturing to product inspection, we strictly follow the ISO quality management system to ensure that every embedded component PCB meets customer requirements and standards.
Customer service is one of the important tenets of our company. We have a professional customer service team that can respond to customer needs and problems in a timely manner and provide professional technical support and solutions. We focus on communication and cooperation with customers and strive to provide customers with satisfactory services and products.
We provide customized solutions according to the different needs of customers. Whether it is plate type, size, material or process flow, we can adjust and customize it according to the customer’s specific requirements to ensure that the product can fully meet the customer’s needs.
As a professional embedded component PCB manufacturer, our company has advanced technology and equipment, strict quality control system, and excellent customer service. We are committed to providing customers with high-quality, customized embedded component PCB solutions, growing together with customers and creating a better future.
What are the five key characteristics of great customer service?
As a customer, excellent customer service is crucial when choosing an embedded component PCB manufacturer. So, how do we judge the quality of a manufacturer’s customer service? Here are five key characteristics that can help us evaluate and select the right manufacturer:
Prompt response: A quality manufacturer should be able to respond promptly to customer inquiries and needs. Whether it’s via email, phone, or online chat, they should respond quickly to show that they care about and respect their customers. Being able to provide support and solutions quickly in emergencies is also a reflection.
Professional knowledge: An excellent manufacturer should have extensive industry knowledge and experience and be able to provide customers with professional advice and technical support. They should understand the latest manufacturing technologies and standards, be able to provide customized solutions according to customer needs, and be able to provide valuable opinions and suggestions during the design and manufacturing process.
Customized solutions: Every customer’s needs are unique, and a quality manufacturer should be able to provide personalized solutions based on the customer’s specific needs. They should be able to flexibly adjust manufacturing processes and production plans to meet customers’ specific requirements and be willing to work with customers to find the best solutions.
Good communication: Communication is the foundation of good customer service. Manufacturers should be able to maintain close communication with customers, provide timely updates on manufacturing progress and order status, and be able to promptly resolve customer questions and concerns. They should be able to understand their clients’ needs and express their ideas and suggestions clearly to ensure smooth communication between both parties.
After-sales support: A quality manufacturer should provide comprehensive after-sales support and services. Whether it is technical support after product delivery or timely handling of quality problems when they arise, they should be able to go all out to ensure customer satisfaction and product quality.
Through the evaluation of the above key characteristics, we can better judge the customer service quality of an embedded component PCB manufacturer. When choosing a manufacturer, we should pay attention to these characteristics to ensure that we are getting not only quality products, but also quality service and support.
Frequently Asked Questions
What are the main differences between Embedded Components PCB and traditional PCB?
Embedded Components PCBs, as the name suggests, involve embedding electronic components directly into the PCB substrate during the manufacturing process. This results in a more compact design, reduced size, and enhanced performance compared to traditional PCBs where components are soldered onto the surface. Embedded Components PCBs also offer improved thermal management and reliability due to shorter interconnections.
What is the maximum size of an Embedded Components PCB?
The maximum size of an Embedded Components PCB depends on several factors, including the manufacturing capabilities of the PCB manufacturer and the specific requirements of the application. However, with advancements in manufacturing technology, Embedded Components PCBs can be produced in larger sizes than ever before, often rivaling the dimensions of traditional PCBs.
What is the minimum line width/spacing achievable in Embedded Components PCB manufacturing?
The minimum line width and spacing achievable in Embedded Components PCB manufacturing depend on various factors, including the capabilities of the manufacturing equipment, the type of substrate used, and the design requirements. Generally, with modern manufacturing techniques such as laser drilling and advanced lithography, line widths and spacings as small as a few micrometers can be achieved.
How does Embedded Components PCB manufacturing impact the overall cost compared to traditional PCB manufacturing?
Embedded Components PCB manufacturing typically involves additional steps such as embedding components and specialized equipment, which can increase the initial manufacturing costs compared to traditional PCB manufacturing. However, the overall cost-effectiveness depends on factors such as the complexity of the design, the desired performance specifications, and the intended application. In many cases, the benefits of compactness, improved performance, and reliability outweigh the slightly higher manufacturing costs.