Embedded Cavity Substrate Manufacturer, Embedded Slot PCB, BGA substrates. and Buried Cavity Substrate manufacture. Open cavity(slot) on the PCB/Substrates or Open Buried Cavity(slot) In the middle of each layer of substrate.We specialize in producing various types of CAVITY PCBS.
In the dynamic realm of PCB design, embedded cavity substrates have emerged as a pivotal element driving technological advancements. They hold a significant and indispensable role in contemporary electronic devices. This article aims to explore the definition, features, and crucial functions of embedded cavity substrates in electronic equipment.
Embedded cavity substrate is an advanced technology introduced in PCB design. It is different from traditional circuit boards in that it incorporates an embedded cavity structure into its design. This innovative design allows embedded cavity substrates to play a unique and important role in modern electronic devices. So, let’s first understand what an embedded cavity substrate is and its definition in the electronics field.
An embedded cavity substrate is an infrastructure designed to provide support and connections for electronic components. Unlike traditional substrates, embedded cavity substrates are special in that they have a cavity embedded in their structure, which brings them unique advantages in terms of thermal management, electrical performance and overall efficiency. So, how are these embedded cavities defined, and what role do they play in practical applications?
First, the embedded cavities of the embedded cavity substrate play a key role in thermal management.This includes improving signal integrity and reducing signal losses, resulting in more reliable electrical performance for electronic devices.
Next, let’s discuss the compact and lightweight design of the embedded cavity substrate. Due to the embedded cavity design, electronic devices can be more compact and lightweight, which is particularly critical in applications where space is limited. This design feature makes embedded cavity substrates an indispensable component in the design of modern electronic devices.
Finally, the design of the embedded cavity substrate also improves overall reliability and durability. Its structural integrity makes electronic devices more stable and durable, providing users with a longer life product experience.
Overall, embedded cavity substrates are an important innovation in modern electronic device design. By in-depth understanding of its definition, characteristics and key roles, we can better understand how this advanced technology drives the development of electronic devices and brings more convenience and benefits to our lives in the evolving field of PCB design. of.
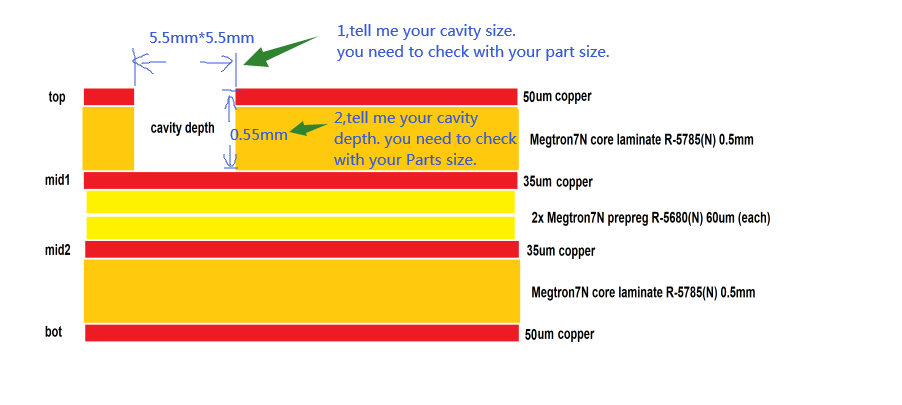
Embedded Cavity Substrate
What types of embedded cavity substrates are there?
In the contemporary electronics industry, various embedded cavity substrates exist, each distinguished by its unique characteristics and application scope. The three primary types are organic embedded cavity substrates, ceramic embedded cavity substrates, and silicon embedded cavity substrates.
Organic embedded cavity substrate
The organic embedded cavity substrate is an embedded cavity structure made of organic substrates. Features include:
Flexibility: Organic substrates usually have good flexibility and plasticity, making it easier for organic embedded cavity substrates to adapt to complex design requirements in certain applications.
Cost-Effectiveness: Organic embedded cavity substrates are generally less expensive to manufacture than other materials, making them suitable for cost-sensitive projects.
The ceramic embedded cavity substrate is made from ceramic materials and possesses remarkable characteristics. It stands out for its exceptional stability at high temperatures, making it well-suited for applications demanding resilience in elevated temperature settings. Furthermore, it showcases outstanding mechanical properties, such as hardness and pressure resistance, ensuring the reliable functioning of electronic equipment in challenging conditions.
In contrast, the silicon embedded cavity substrate, composed of silicon material, offers distinct advantages. It stands out for its exceptional thermal conductivity, facilitating effective heat transfer and dispersion for improved thermal management in electronic devices. Furthermore, silicon embedded cavity substrates typically achieve high levels of integration, allowing for the incorporation of more electronic components in a confined space.
Understanding the distinct features and advantages of each embedded cavity substrate type allows for a more informed selection tailored to specific application needs. This, in turn, enhances the performance and reliability of electronic devices.
What are the advantages of embedded cavity substrates?
As an important part of modern electronic devices, embedded cavity substrates have several significant advantages, making them popular in PCB design.
The use of embedded cavity substrates enhances effective thermal management by integrating a cavity structure within the substrate. This significantly improves heat dissipation, addressing the issue of overheating. This advantage is particularly important for prolonged operation of electronic equipment, ensuring system stability and reliability.
Secondly, embedded cavity substrates can improve electrical performance. The optimized design structure improves signal transmission integrity and reduces signal loss, thereby effectively improving the overall electrical performance. This is particularly critical for application scenarios that require high-speed data transmission or frequent signal exchange, ensuring the stability and reliability of data transmission.
In addition, the embedded cavity substrate also features a compact and lightweight design. By embedding the cavity structure, a more compact and lightweight design can be achieved, thereby meeting the needs of applications with space constraints. Whether in mobile devices, vehicle electronics or other scenarios with limited space, this design advantage can provide greater flexibility and convenience for the actual application of the product.
Embedded cavity substrates enhance the reliability and durability of electronic devices by bolstering structural integrity. This not only enhances equipment’s resistance to vibrations and impacts but also effectively safeguards against component damage or circuit breakage resulting from external environmental changes. The heightened reliability and durability contribute to prolonged electronic equipment usage, leading to reduced maintenance costs and less frequent replacements.
In essence, embedded cavity substrates have become indispensable in contemporary PCB design due to their superior thermal management, enhanced electrical performance, compact and lightweight design, and improved reliability and durability. With ongoing technological advancements and expanding application scenarios, it is expected that embedded cavity substrates will assume a progressively crucial role in the future.
Why choose embedded cavity substrate?
Embedded cavity substrates are gaining popularity in modern electronics, surpassing traditional PCB circuit boards due to their unique design features. Unlike conventional planar structures, embedded cavity substrates incorporate embedded cavities, providing increased flexibility for complex circuit layouts and component configurations.
A key advantage of embedded cavity substrates lies in their enhanced thermal management. The embedded cavities improve heat conduction and dissipation efficiency, effectively lowering the operating temperature of electronic components. This not only extends equipment service life but also enhances performance stability and reliability.
Moreover, embedded cavity substrates exhibit superior electrical performance. The specialized structural design minimizes signal transmission loss and interference, enhancing signal integrity and circuit stability. This is particularly crucial for modern electronic devices requiring high-speed data transmission and precise signal processing.
As electronic devices continue to shrink in size, the compact and lightweight design facilitated by embedded cavity substrates becomes increasingly valuable. This design advantage enables more compact layouts, resulting in smaller dimensions and reduced weight—making embedded cavity substrates particularly well-suited for mobile devices, portable gadgets, and embedded systems.
In summary, embedded cavity substrates outperform traditional PCB circuit boards in terms of unique design features, superior thermal management performance, excellent electrical performance, and compact and lightweight design. In the design of modern electronic equipment, choosing an embedded cavity substrate can not only meet the requirements for performance and reliability, but also enable more flexible and innovative designs.
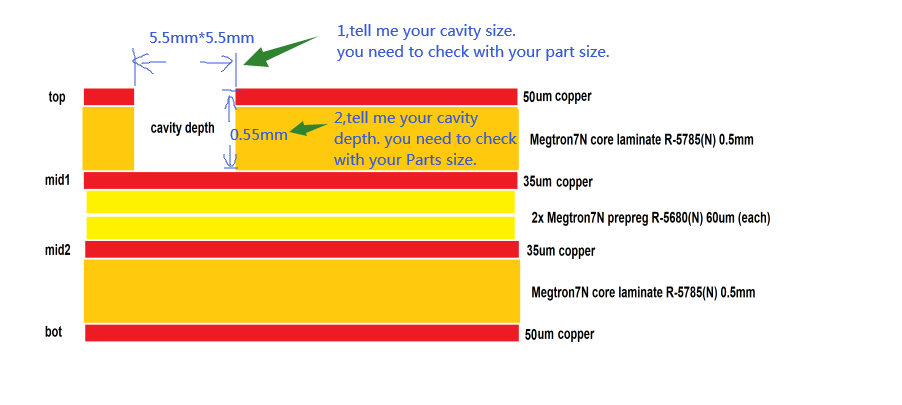
Embedded Cavity Substrate
How to manufacture embedded cavity substrate?
In the field of modern electronic engineering, the manufacturing of embedded cavity substrates is a precise and critical process, involving two key aspects: mainboard manufacturing and substrate manufacturing. The following is a detailed introduction to these two aspects:
Motherboard manufacturing is the first step in the embedded cavity substrate manufacturing process. The key to this stage is to introduce the precision and expertise required to embed the cavity. During the motherboard manufacturing process, there are several key factors to consider to ensure efficient completion:
Effective motherboard design requires meticulous planning of the embedded cavity’s location and dimensions to ensure accurate processing during manufacturing. Precision machining, employing advanced tools like CNC machines and laser cutting, is essential for guaranteeing uniformity and accuracy in creating the embedded cavity. To uphold high standards, rigorous quality control measures must be enforced, verifying that each motherboard aligns with design specifications. This meticulous approach enhances manufacturing efficiency and overall product quality.
Substrate manufacturing
Substrate fabrication is a critical step in manufacturing embedded cavity substrates and involves selecting appropriate materials, employing advanced manufacturing techniques and strict quality control. The following is a detailed introduction to substrate manufacturing:
Material Selection: Opt for premium substrate materials suitable for embedded cavity manufacturing, such as FR-4 fiberglass composites or high-performance ceramic materials.
Processing Technology: Employ advanced processing techniques, including chemical etching, electrochemical copper plating, and laser drilling, to precisely process the substrate. This ensures the accuracy and stability of the embedded cavity.
Embedded Cavity Manufacturing: During substrate production, employ specific processing steps and techniques to form an embedded cavity structure within the substrate, meeting design requirements and functional needs.
Quality Control: Enforce stringent quality control measures, encompassing material testing, process monitoring, and finished product inspection, to guarantee each embedded cavity substrate possesses stable quality and reliable performance.
Through the above manufacturing steps, embedded cavity substrates that meet design requirements and standards can be efficiently manufactured, providing strong support for the development of modern electronic equipment.
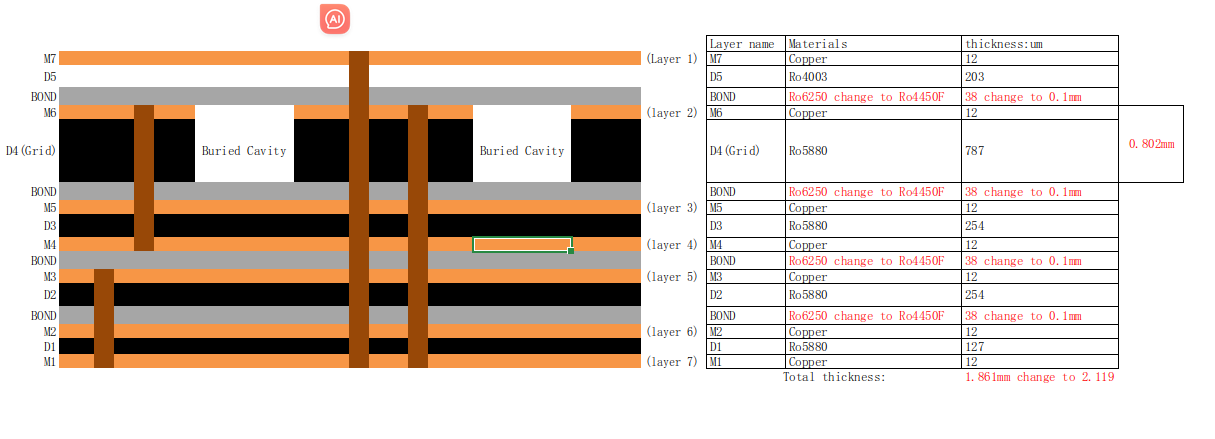
Embedded Cavity Substrate
What are the application areas of embedded cavity substrates?
As an important part of modern electronic equipment, the embedded cavity substrate’s versatility covers various industries and provides strong support for the performance improvement and innovation of various types of equipment. The following are examples of applications of embedded cavity substrates in different fields:
Embedded cavity substrates are essential components in consumer electronics such as smartphones, tablets, and wearables. They contribute to compact designs and efficient thermal management, improving device performance and extending battery life.
In the field of medical devices, embedded cavity substrates are widely used in diagnostic equipment and patient monitoring equipment. These devices are critical for accurate data acquisition and real-time data processing, and the high performance and stability of the embedded cavity substrate can meet these requirements, providing medical personnel with reliable diagnostic and monitoring tools.
Embedded cavity substrates are extensively employed in the telecommunications sector, particularly in high-performance communication equipment. These devices play a crucial role in meeting the stringent demands of big data transmission and intricate communication protocol support. The embedded cavity substrate’s capabilities in high-speed data processing and ensuring reliable performance are instrumental in maintaining the stability of communication networks.This advanced technology provides strong support for diverse communication needs and finds extensive applications in consumer electronics, automobiles, medical equipment, telecommunications, and various industries. Its widespread adoption is pivotal in stimulating innovation and development across sectors, fostering scientific and technological progress, and contributing significantly to economic growth in contemporary society.
Where can I find a reliable embedded cavity substrate manufacturer?
In the era of pursuing advanced electronic devices, embedded cavity substrates have become a key component in the field of innovation. However, in order to ensure excellent quality and performance of electronic devices, it is particularly critical to find reliable embedded cavity substrate manufacturers.
Find out if the supplier has deep industry experience and expertise, particularly in embedded cavity substrate manufacturing.
Assess if suppliers stay current with the latest technologies and manufacturing methods. Verify if they possess crucial certifications, such as ISO certification, ensuring adherence to international standards. Evaluate if the supplier meets other industry-specific certification standards. Examine customer reviews to gauge overall satisfaction, and gather insights on product quality and service from previous customers.
As a supplier to our company, we lead the industry with strong expertise, rich experience and excellent certification results. We have been committed to providing high-quality embedded cavity substrates to meet our customers’ expectations for excellent performance and reliability in electronic devices.
With over a decade of industry experience, our team of seasoned professionals brings extensive expertise to effectively navigate industry norms and cater to individual client requirements. Our manufacturing processes strictly adhere to ISO certified standards, ensuring the consistent delivery of high-quality products.
As a trusted embedded cavity substrate manufacturer, we take pride in serving as reliable suppliers to your company. Beyond delivering superior products, our dedication extends to fostering enduring and prosperous partnerships.
Opting for our services means opting for excellence, reliability, and innovation in the quest for a dependable embedded cavity substrate manufacturer.
Quotation for embedded cavity substrate
In the manufacturing process of modern electronic devices, the selection of embedded cavity substrate is crucial. However, as with any project, budget is an important consideration. Therefore, obtaining an accurate quote for the embedded cavity substrate is critical for budgetary considerations.
First, it is critical to understand the factors that manufacturers may base their quotes on embedded cavity substrates on. These factors typically include specifications, quantities, and customization requirements. In terms of specifications, different embedded cavity substrates have different features and functions, so their costs will also be different. Quantity is another important factor, as purchasing in bulk often results in more competitive prices. Finally, custom requirements may result in additional costs because specialized processes or material selections are required.
In summary, it is advisable to gather quotes from multiple sources when seeking embedded cavity substrate solutions. Varied pricing strategies, production capabilities, and technology levels among manufacturers necessitate a comprehensive comparison to inform decision-making. Beyond price considerations, the manufacturer’s reputation and product quality are crucial factors. Evaluating a manufacturer’s history, customer reviews, certifications, and qualifications helps ensure the timely delivery of high-quality substrates. After obtaining quotes, a detailed analysis considering specifications, quantities, customization requirements, and overall reputation is essential. Clear communication with the chosen manufacturer is vital to prevent misunderstandings or unforeseen costs. Ultimately, obtaining accurate quotes is a critical step for project success, enabling informed budget decisions through a thorough understanding of market dynamics.
Frequently Asked Questions
What are Embedded Cavity Substrates?
Embedded Cavity Substrates are specialized foundations used in PCB design, featuring cavities within their structure. These cavities enhance thermal management and electrical performance in electronic devices.
What types of Embedded Cavity Substrates are available?
There are various types of Embedded Cavity Substrates, including Organic, Ceramic, and Silicon variants. Each type offers distinct characteristics suitable for different applications.
Why choose Embedded Cavity Substrates over traditional PCB boards?
Embedded Cavity Substrates provide superior thermal management and electrical performance due to the incorporation of cavities. They are preferred for applications where space, heat dissipation, and performance are critical factors.
How are Embedded Cavity Substrates manufactured?
Manufacturing Embedded Cavity Substrates involves precise techniques, including selecting suitable materials, forming cavities, and ensuring stringent quality control throughout the process.
How can I ensure the quality of Embedded Cavity Substrates?
Ensuring the quality of Embedded Cavity Substrates involves working with reputable manufacturers, specifying requirements clearly, and conducting thorough testing and inspection procedures.
What is an Embedded Cavity Substrate?
An Embedded Cavity Substrate is a specialized foundation within PCB design, featuring cavities in its structure. It serves as a crucial element, providing support and connectivity for electronic components.
Why choose Embedded Cavity Substrate over other boards?
Embedded Cavity Substrates outshine traditional PCB boards due to their unique design features, making them a preferred choice for applications where thermal management and compactness are critical.