Embedded Cavity PCB Manufacturing.Embedded Cavity PCB Manufacturing involves creating printed circuit boards (PCBs) with embedded empty spaces or cavities within the board structure. These voids can accommodate various components, such as sensors, chips, or batteries, providing a compact and integrated solution. The process integrates precise milling or routing techniques during PCB fabrication to achieve the desired cavity dimensions and shapes. This advanced manufacturing method enhances PCB functionality, allowing for more complex designs and improved performance in applications like aerospace, automotive, and medical devices.
In modern electronics, printed circuit boards (PCBs) are the backbone of electronic devices, seamlessly integrating electronic components into devices from smartphones to spacecraft. Among many PCB manufacturing technologies, embedded cavity PCB manufacturing stands out for its complex and indispensable process, enabling compact, high-performance electronic systems. In this comprehensive guide, we take a deep dive into embedded cavity PCB manufacturing and reveal its importance in the electronics industry.
What is an embedded cavity PCB?
Embedded cavity PCB is a specially designed printed circuit board (PCB for short) in which a cavity or space of a certain depth is embedded. These cavities can come in various shapes and sizes and are usually located inside the PCB rather than on the surface. Compared with traditional single-layer or double-layer PCB, embedded cavity PCB has a more complex structure and more functions.
In modern electronic products, embedded cavity PCB plays a key role. They not only provide basic electrical connection functions, but also provide a variety of important functions for electronic systems through their special design.
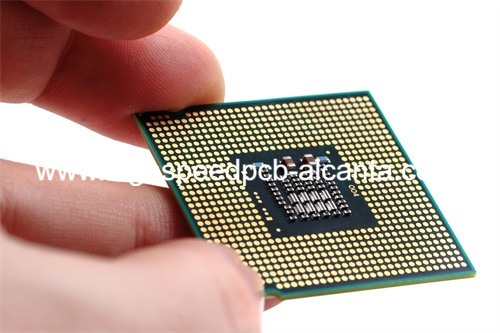
Embedded Cavity PCB Manufacturing
First, embedded cavity PCB provides a highly integrated solution for electronic devices. By creating cavities inside the PCB, electronic components can be safely embedded within them, allowing for a compact design of the circuit. This design minimizes the size and weight of electronic equipment while improving system stability and reliability.
Secondly, embedded cavity PCB can also improve the heat dissipation performance of electronic systems. The cavity inside the PCB can be used to install a radiator or heat dissipation device, effectively reducing the operating temperature of electronic components and improving the performance and life of the system.
In addition, embedded cavity PCB can also be used to reduce electromagnetic interference (EMI) and improve signal integrity. By dividing different cavity areas inside the PCB, sensitive electronic components can be effectively isolated, reducing interference and noise, thereby improving the anti-interference ability and stability of the system.
In general, embedded cavity PCB plays an irreplaceable role in the modern electronics field. Through their unique design and versatility, they provide new possibilities for the design and manufacturing of electronic products and promote the development and progress of electronic technology.
How to design embedded cavity PCB?
Embedded cavity PCB design is a precise and complex process, which requires engineers to fully understand the circuit requirements and properly consider the structure, size and layout of the embedded cavity in the design. The following are the key steps in designing an embedded cavity PCB:
Before designing an embedded cavity PCB, it is first necessary to clarify the function and performance requirements of the circuit. This includes determining aspects such as the circuit’s power consumption, signal transmission rate, EMI requirements, and interface requirements with other components.
Select an appropriate cavity structure based on circuit requirements and equipment space constraints. Common cavity structures include square, rectangular, circular, etc. Engineers need to choose according to the actual situation.
For high-power circuits, thermal management is critical. In the design, consideration should be given to how to optimize heat conduction and heat dissipation through the cavity structure to ensure stable operation of the circuit.
Arrange various electronic components reasonably on the PCB to minimize circuit board area occupation and ensure signal integrity. At the same time, considering the existence of the embedded cavity, the location of the components needs to be reasonably arranged to ensure that the structure and function of the cavity are not affected.
Determine the size and location of the cavity based on the layout of the circuit board and the functional requirements of the cavity. This takes into account factors such as the overall size of the circuit board, the interaction of the cavity with other components, and how components are mounted inside the cavity.
During the design process, special attention should be paid to signal integrity and electromagnetic compatibility (EMI/EMC) issues. Adopt appropriate shielding and grounding design to reduce signal interference and electromagnetic radiation and ensure the stability and reliability of the circuit.
Use advanced PCB design software, such as Altium Designer, Cadence Allegro, etc., to design embedded cavity PCBs. These tools provide a rich set of features and capabilities that help engineers complete design tasks quickly and accurately.
Before finalizing the design, conduct simulation and simulation analysis of the circuit to evaluate the performance and stability of the design. Through simulation software, potential problems can be discovered and adjustments made to ensure design reliability and optimized performance.
Finally, detailed design documents are generated based on the design results, including circuit schematics, PCB layout drawings, cavity design drawings, etc., to facilitate subsequent manufacturing and production processes.
Through the above steps, engineers can effectively design embedded cavity PCBs to meet the needs of different electronic devices and ensure their performance and reliability.
What is the manufacturing process of embedded cavity PCB?
In the manufacturing process of embedded cavity PCB (Printed Circuit Board), electronic components, wires and other materials are assembled together through a series of precise steps to achieve the functions and performance required by the design. The manufacturing process of embedded cavity PCB will be introduced in detail below.
Design preparation stage: The first step in manufacturing embedded cavity PCB is design preparation. Engineers use CAD (computer-aided design) software to draw PCB wiring diagrams and cavity designs based on customer needs and design specifications. At this stage, the size, shape, location of the cavity and other relevant design requirements need to be considered.
Material preparation and selection: Next, select the appropriate substrate material and other key materials. Common substrate materials include FR-4, Rogers, etc., while the conductive layer usually uses copper. In addition, materials for filling the cavity need to be prepared, such as thermoplastic resin.
Cavity processing: Cavity processing on the PCB substrate is one of the key steps in manufacturing embedded cavity PCBs. This process often uses precision machining equipment, such as laser drills or CNC milling machines. According to the design requirements, engineers accurately cut out the cavity on the substrate to ensure that the size and shape of the cavity comply with the design specifications.
Conductive layer preparation: After the cavity processing is completed, the conductive layer is prepared. This involves covering the surface of the substrate with a thin layer of copper foil and using methods such as chemical etching to remove unwanted parts to form wires and pads for circuit connections.
Lamination and lamination: Next, different layers of materials are laminated according to the design specifications to form a complete PCB structure. This involves placing conductive layers, substrate material, fill material, etc. together in sequence. Then, it is pressed by a laminating machine to ensure that the layers are firmly bonded and form a tight cavity structure.
Track production and testing: After completing the PCB lamination, track production and testing are performed. Make circuit traces by printing or spraying, connect various electronic components, and conduct electrical performance testing and reliability testing to ensure that the PCB meets design requirements and industry standards.
Surface treatment and assembly: Finally, the surface treatment and assembly of the PCB are performed. This includes processes such as cleaning the PCB surface, coating protective layers, and soldering components. After assembly is completed, final quality checks and testing are performed to ensure the PCB’s performance and reliability meet expected levels.
To sum up, manufacturing embedded cavity PCB is a complex and precise process involving multiple key steps and specialized equipment. Through strict quality control and exquisite craftsmanship, high-quality, high-performance embedded cavity PCBs can be produced to meet the needs of various applications.
How to make embedded cavity PCB?
The production process of embedded cavity PCB is a highly precise process involving multiple complex steps and specialized equipment. Below we’ll dive into the main stages of this process:
Design preparation: Before manufacturing the embedded cavity PCB, detailed design documents need to be prepared first. These files include PCB layout, dimensions, cavity locations and dimensions, and other key parameters. Designers use advanced CAD software to create these designs and ensure they meet customer requirements and industry standards.
Substrate Preparation: The first step in the production process is to prepare the substrate for the PCB. Typically, the substrate is made of fiberglass reinforced epoxy (FR-4) material. The surface of the substrate must be clean and coated to protect the copper layer to ensure final electrical connectivity and reliability.
Cavity Processing: Once the substrate is ready, the next critical step is to process the cavity. Cavities are typically created by drilling, milling, or etching the substrate. These machining processes require high-precision equipment and strict control to ensure that the size and shape of the cavity meet the design requirements.
Cavity Filling: After the cavity is machined, it needs to be filled to meet specific application needs. Filling materials are usually epoxy, polyimide (PI) or other high temperature resistant materials. The purpose of filling the cavity is to enhance the mechanical strength of the PCB, improve thermal conductivity, and protect internal circuits and components.
Lamination and welding: After filling the cavity, the multi-layer PCB boards are pressed together through a lamination process. In this process, each layer must be stacked one after another according to the design requirements, and solidified through high temperature and pressure to form the final multi-layer structure. After lamination is complete, a soldering process is used to connect the components on the circuit board, ensuring a strong and reliable electrical connection.
Surface Preparation: Finally, the surface on the PCB needs to be treated to protect the copper layer from environmental corrosion and provide solderability. Common surface treatment methods include tin plating, gold plating, lead plating, etc. These treatments can not only improve the corrosion resistance and reliability of the PCB, but also facilitate the subsequent assembly process.
Through the above steps, the production process of embedded cavity PCB is completed. This is a comprehensive project that requires precision equipment, superb technology and strict quality control to ensure that the performance and reliability of the final product meet customer expectations and requirements.
How much does an embedded cavity PCB cost?
As a highly customized technology, embedded cavity PCB needs to consider multiple factors during the manufacturing process, so its cost may increase compared with traditional ordinary PCB. Let’s take a deeper look at the cost components and influencing factors of embedded cavity PCB manufacturing.
First of all, the cost of embedded cavity PCB is affected by the selected materials. Compared with ordinary PCBs, embedded cavity PCBs may require more special substrate materials to meet their design requirements. For example, if the design requires higher thermal conductivity or mechanical strength, selecting a special substrate material will increase the cost.
The manufacturing of embedded cavity PCB requires advanced processing technology and equipment. For example, creating cavities using techniques such as laser drilling and controlled-depth milling requires expensive equipment and high-precision machining processes, which also increases manufacturing costs.
The design of embedded cavity PCB is usually more complex than ordinary PCB because factors such as the shape, size and location of the cavity need to be taken into consideration. Complex designs may require more engineer time and resources, increasing the cost of the design phase.
Production scale is also one of the key factors affecting costs. Low-volume production typically results in higher unit costs because fixed costs need to be spread over smaller volumes of output. In contrast, mass production enables higher efficiencies and lower unit costs.
Embedded cavity PCB manufacturing requires a high degree of technical expertise and experience, which will also affect costs to a certain extent. Experienced manufacturers can often provide higher quality products, but their services often come with additional costs.
To sum up, the cost of embedded cavity PCB depends on many factors, including material selection, processing technology, design complexity, production scale and technical expertise. Although the manufacturing cost may be higher, the corresponding performance advantages and application value brought by the embedded cavity PCB are often worth the investment. When choosing a manufacturer, be sure to consider the above factors to ensure you get the best value for money and quality assurance.
What materials are embedded cavity PCBs made of?
In the manufacturing process of embedded cavity PCB, it is crucial to choose the appropriate material, because the choice of material directly affects the performance, stability and life of the PCB. Generally, embedded cavity PCBs are made of a wide variety of materials. Here are some of the common materials:
The substrate is the main body of the PCB and supports the circuit components and wires. Common substrate materials include:
FR-4 (Fiberglass Reinforced Epoxy): FR-4 is one of the most commonly used substrate materials and has good insulation properties and mechanical strength, making it suitable for most general applications.
Rogers: Rogers materials have excellent dielectric properties and thermal stability and are commonly used in high-frequency and microwave circuit design.
Ceramics: Ceramic substrates have excellent high-frequency characteristics and high-temperature resistance, and are suitable for high-performance, high-frequency application scenarios.
The conductive layer is the copper foil on the PCB that is used to make circuit connections. Conductive layer materials include:
Copper foil: Copper foil is the most commonly used conductive layer material and has good conductivity and processability.
Silver: Silver foil is used as a conductive layer material in some high-end applications because of its higher conductivity properties.
One of the features of embedded cavity PCB is the internal cavity structure, and filler materials are used to fill the cavity to improve mechanical stability and insulation performance. Common filling materials include:
Epoxy Resin: Epoxy resin is a commonly used filling material with good adhesion and heat resistance.
Polytetrafluoroethylene (PTFE): PTFE has excellent chemical resistance and insulation properties, and is suitable for applications in some special environments.
In addition to the above main materials, embedded cavity PCB may also use other auxiliary materials, such as thermal conductive film, filling media, etc., to improve the heat dissipation performance and mechanical strength of the PCB.
To sum up, the manufacturing of embedded cavity PCB usually uses a combination of multiple materials to achieve comprehensive optimization of electrical characteristics, thermal management and mechanical performance. When selecting materials, reasonable matching and design must be carried out according to specific application scenarios and requirements to ensure that the PCB has the required performance and reliability.
Who makes embedded cavity PCBs?
In the manufacturing process of embedded cavity PCB, choosing the right manufacturer is crucial. As a manufacturer of our company, we are committed to providing excellent quality and professional services to create outstanding embedded cavity PCB solutions for our customers.
As a manufacturer, we have many years of experience and expertise in meeting our customers’ needs for high-performance, high-reliability embedded cavity PCBs. Our manufacturing process uses the most advanced equipment and technology to ensure product quality and stability.
In our manufacturing facility, we have an experienced team that is proficient in the design, processing and assembly of embedded cavity PCBs. They strictly follow the quality management system to ensure that each embedded cavity PCB meets customer requirements and standards.
Our manufacturing process not only focuses on technology, but also on communication and cooperation with customers. We work closely with our customers to understand their needs and expectations and provide customized solutions. We are committed to establishing long-term and stable cooperative relationships and providing customers with continuous support and services.
As an embedded cavity PCB manufacturer, our goal is to continuously improve product quality and customer satisfaction, and create greater value and competitive advantage for customers. We will continue to invest in R&D and innovation, and constantly improve our manufacturing processes to meet our customers’ changing needs and challenges.
No matter the size of your project, we are willing to work with you to provide you with high-quality embedded cavity PCB solutions. By choosing us as your manufacturing partner, you will receive reliable technical support and quality customer service to achieve success together.
What are the five qualities of great customer service?
Excellent customer service is one of the keys to a successful business. By delivering an exceptional customer experience, businesses can build strong customer relationships, enhance brand reputation, and achieve long-term business growth. Here are five key traits that help businesses provide excellent customer service:
Great customer service starts with proactive communication. Businesses should actively stay in touch with customers to understand their needs and feedback. Regular communication builds trust, improves customer satisfaction, and resolves potential issues promptly.
Customers expect prompt responses when asking questions or making requests. Quick response not only demonstrates the company’s professionalism and dedication, but also enhances customers’ trust in the company. By establishing effective communication channels and response mechanisms, companies can better meet customer needs.
Every customer is unique, so personalized attention is an important part of providing great customer service. Understand customers’ preferences, habits and needs, provide customized solutions and services based on their individual needs, and treat customers as partners rather than just transaction objects.
Customers may encounter various problems and challenges when using products or services. Enterprises need to have the ability to solve problems, quickly and effectively solve the difficulties encountered by customers, and ensure customer experience and satisfaction. Timely and effective problem solving can not only regain customers, but also establish a good image of the company.
Excellent customer service is a continuous improvement process. Enterprises need to continuously collect customer feedback, analyze customer needs and behaviors, and timely adjust and improve service strategies and processes. Through continuous improvement, companies can continuously improve customer service levels and win long-term customer support and loyalty.
In general, high-quality customer service is the key to a company’s success. It requires companies to have proactive communication, timely response, personalized care, problem-solving abilities and a spirit of continuous improvement. By continuously improving customer service levels, companies can win the trust and support of customers and achieve long-term business growth and development.
Frequently Asked Questions
What are the primary advantages of Embedded Cavity PCBs?
Embedded Cavity PCBs offer several advantages, including enhanced thermal management, reduced electromagnetic interference (EMI), improved signal integrity, and increased mechanical robustness. The integration of cavities within the PCB substrate allows for efficient heat dissipation, enabling the design of compact and high-performance electronic systems.
How does Embedded Cavity PCB manufacturing impact thermal management?
The incorporation of cavities within the PCB substrate enhances thermal management by providing additional space for heat dissipation. This facilitates the efficient removal of heat generated by electronic components, preventing overheating and ensuring optimal performance and reliability of the system.
What industries benefit the most from Embedded Cavity PCB technology?
Embedded Cavity PCB technology finds applications across various industries, including aerospace, telecommunications, automotive electronics, medical devices, and industrial automation. These industries often require compact and reliable electronic systems with stringent thermal and performance requirements, making Embedded Cavity PCBs an ideal choice.
Can Embedded Cavity PCBs be customized to accommodate specific design requirements?
Yes, Embedded Cavity PCBs can be customized to meet specific design requirements and application needs. Manufacturers offer tailored solutions, allowing for flexibility in cavity dimensions, shapes, positions, and material selections. Customization ensures optimal integration of electronic components and adherence to performance specifications.