Cross Blind/Buried Vias PCB Manufacturing.Cross blind/buried vias PCB manufacturing involves the intricate process of creating circuit boards with vias that connect multiple layers while remaining hidden from view. This advanced technique requires precise drilling and plating methods, ensuring optimal conductivity and reliability. Through careful design and fabrication, these vias enable complex interconnections without compromising the integrity of the board. Manufacturers utilize sophisticated equipment and meticulous quality control measures to achieve the desired outcome. The result is a high-density PCB with enhanced functionality, suitable for a wide range of applications demanding compactness and performance.
Do you know how Cross-Blind PCB manufacturing impacts the design and manufacturing of electronic devices? Cross-Blind PCB technology plays an important role in the electronics field. By introducing Cross-Blind technology into the PCB design and manufacturing process, higher circuit density, smaller circuit board size, and better performance can be achieved. The application of this technology not only improves the performance and reliability of electronic devices, but also provides designers with more flexibility and creative space. In this article, we’ll dive into the key aspects of Cross-Blind PCB manufacturing and take you through the secrets of this technology.
What is Cross-Blind PCB?
Cross-Blind PCB (Cross-Blind Printed Circuit Board) is an advanced printed circuit board with complex inter-layer connections and designs. It is different from traditional double-sided or multi-layer PCB because it contains inner signal paths that cross horizontally and vertically, which allows electronic devices to achieve more functions and connections in a smaller space. So, what role does Cross-Blind PCB play in electronic equipment?
First of all, Cross-Blind PCB plays a vital role in the design of modern electronic devices. As electronic devices become increasingly miniaturized, intelligent and feature-rich, traditional double-sided and multi-layer PCBs are often unable to meet their complex connection requirements. The emergence of Cross-Blind PCB fills this gap, allowing engineers to implement more circuits and connections in a smaller space, making device design more flexible and diverse.
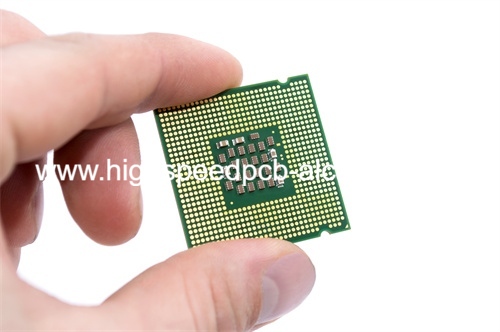
Cross Blind/Buried Vias PCB Manufacturing
Secondly, Cross-Blind PCB plays an important role in improving the performance and reliability of electronic equipment. Due to its complex inter-layer connection design, Cross-Blind PCB is able to achieve higher circuit density and shorter signal transmission paths, thereby improving the response speed and performance stability of electronic devices. In addition, Cross-Blind PCB can also reduce signal interference and electromagnetic interference, improve the anti-interference ability of the equipment, thereby enhancing the reliability and stability of the equipment.
In addition, Cross-Blind PCB also provides more possibilities for functional expansion and innovation of electronic equipment. Through flexible inter-layer connection design, engineers can integrate various sensors, processors, memory and communication modules on Cross-Blind PCB to achieve more diverse and intelligent device functions. For example, complex functions common in modern electronic devices such as smartphones, tablets, and drones are realized with the help of Cross-Blind PCB design.
To sum up, Cross-Blind PCB plays an indispensable role in electronic equipment. It not only makes equipment design more flexible and diverse, improves equipment performance and reliability, but also provides more possibilities for equipment functional expansion and innovation. Therefore, an in-depth understanding of the design principles and manufacturing process of Cross-Blind PCB is of great significance for understanding the development trends and technical applications of modern electronic equipment.
How to design a Cross-Blind PCB?
When designing a Cross-Blind PCB, there are a number of key tips that need to be considered to ensure that the final PCB design meets performance, reliability and manufacturing requirements. Here are the key tips to consider when designing a Cross-Blind PCB:
Inter-layer planning: Cross-Blind PCB usually contains multi-layer design, so reasonable inter-layer planning is required at the beginning of the design. Determine the layout of signal, power, and ground planes to ensure good signal integrity and electromagnetic compatibility.
Avoid signal interference: Due to interlayer wiring, Cross-Blind PCB design requires special attention to signal interference. Signal interference can be effectively reduced by using appropriate inter-layer isolation technology, ground wire planning and electromagnetic compatibility design.
Consider thermal management: Thermal conduction between the signal and power layers in a Cross-Blind PCB affects the thermal management of the board. Therefore, good thermal management strategies, such as the layout of heat dissipation holes and the design of thermal dissipation layers, need to be considered in the design to ensure the stability and reliability of electronic devices.
High-density wiring: Cross-Blind PCB design usually involves high-density wiring, so the optimization of wiring paths and the shortest path for signal transmission need to be considered. Using appropriate wiring rules and wiring inter-layer connection technology can effectively improve the performance and reliability of the circuit board.
Consider manufacturing requirements: When designing a Cross-Blind PCB, you need to consider the requirements of the manufacturing process. Properly plan the size, interlayer connections and aperture design of the circuit board to ensure that the design can be smoothly converted into the actual manufacturing process and that cost and quality requirements can be met.
Use simulation and simulation tools: When designing a Cross-Blind PCB, it is very important to use simulation and simulation tools for circuit simulation and performance analysis. Through simulation analysis, potential design problems can be discovered early and corresponding optimization and adjustments can be made to ensure the reliability and performance of the design.
Consider assembly and testing: Finally, when designing a Cross-Blind PCB, you need to take into account the subsequent assembly and testing process. Properly arranging component locations and connection methods, as well as providing necessary test points and markings, can simplify subsequent assembly and testing work and improve production efficiency and quality.
To sum up, designing Cross-Blind PCB requires comprehensive consideration of multiple factors, including inter-layer planning, signal interference, thermal management, wiring optimization, manufacturing requirements, simulation analysis, and assembly testing. Only by comprehensively considering these key skills can we design a Cross-Blind PCB with excellent performance, reliability and stability.
What is the manufacturing process of Cross-Blind PCB?
When it comes to the manufacturing process of Cross-Blind PCB (cross-blind PCB), its uniqueness and complexity require special attention. Let’s take a closer look at the key steps of this manufacturing process.
First of all, the process of Cross-Blind PCB manufacturing is different from traditional PCB manufacturing because Cross-Blind PCB involves multi-layer stacking and cross-layer connections. Here are the key steps in this manufacturing process:
Before manufacturing Cross-Blind PCB, high-quality substrate materials need to be prepared first. These materials may include fiberglass, copper foil, etc. Choosing the right materials is critical to the performance of the final PCB.
Next, the designer uses CAD software to create a graphical design of the PCB and determine how the cross-layers will be connected. This requires special attention to ensure that the design meets circuit needs and manufacturing requirements.
Cross-Blind PCB typically involves multi-layer stack-ups where cross-layers need to be precisely aligned. During this step, the laminate materials are pressed together and the placement and thickness of each layer must be ensured to be accurate.
In order to create cross-connects in a Cross-Blind PCB, laser drilling is required. These drill holes must be very precise to ensure an accurate connection between the layers.
After the laser drilling is completed, the gaps between the cross-layers are filled, usually with a metallic filler material such as copper. This helps ensure good connection and conductivity.
The connections between the layers of PCB need to be electroplated to enhance its conductive properties and corrosion resistance. This step ensures the long-term reliability of the Cross-Blind PCB.
Finally, the electroplated PCB will be processed into its final form and subjected to strict inspection. This includes visual inspection, connection testing and electrical characteristics testing to ensure the PCB meets specifications.
The above are the key steps in the Cross-Blind PCB manufacturing process. This manufacturing process requires a high degree of technical expertise and sophisticated equipment to ensure the quality and performance of the final product. It is crucial for PCB manufacturers and designers to understand these critical steps to ensure their projects run smoothly and achieve their desired goals.
What are the specific steps for Cross-Blind PCB manufacturing?
Manufacturing Cross-Blind PCB is a complex and precise process that requires a series of specific steps to be strictly followed to ensure the quality and performance of the final product. The following are the main steps in making a Cross-Blind PCB:
Before starting to manufacture a Cross-Blind PCB, the design first needs to be verified to ensure that all circuit connections and inter-layer layout meet the requirements. Then, prepare the materials and equipment required for production, including substrate materials, chemicals, production equipment, etc.
Cross-Blind PCBs usually have a multi-layer structure, where the connections between different layers require special attention. During the design phase, you need to determine how each layer will be laid out and connected, and ensure that the stacking order between layers is correct.
The design pattern is transferred to the substrate surface through photolithography technology, and chemical etching is used to remove the unnecessary copper layer to form the circuit pattern. In Cross-Blind PCB manufacturing, since multi-layer structures need to be taken into account, alignment and precision between different layers need to be ensured during the etching process.
Inner layer connections are formed between different layers of Cross-Blind PCB through laser drilling technology. These drill holes require precise location and size control to ensure accurate interlayer connections during subsequent processes.
In order to enhance the reliability and conductivity of the inner layer connection, copper filling is required after drilling. This step involves filling the drilled hole with copper material and making sure the filled copper connects well to the surrounding circuitry.
Through similar photolithography and etching processes, circuit patterns are formed on the outer layer of Cross-Blind PCB, and surface treatments are performed to enhance the durability and soldering performance of the circuit board.
After manufacturing is complete, it is critical to conduct final inspection and testing of the Cross-Blind PCB. This includes visual inspections, dimensional measurements, electrical testing, and more to ensure the product meets specifications and works properly.
Making adjustments and improvements where necessary based on final inspection and test results is the final step in the manufacturing process. This may involve adjusting process parameters, improving production equipment or optimizing design solutions to improve the quality and performance of Cross-Blind PCB.
By strictly following the above steps, the process of manufacturing Cross-Blind PCB can ensure the quality and reliability of the product to meet the needs of various electronic devices.
What are the advantages of Cross-Blind PCB?
When comparing traditional printed circuit boards (PCBs) and Cross-Blind PCBs, we can see that Cross-Blind PCBs have many unique advantages. We’ll take a closer look at these benefits below.
Cross-Blind PCB allows for cross-connections between circuit layers, which means designers can use the board’s surface area more efficiently. In contrast, traditional PCB designs are limited by the ability to make connections on only a single plane, which limits improvements in circuit density.
Because Cross-Blind PCB allows inter-layer connections, more complex circuit designs can be implemented on smaller board sizes. This is especially important for electronic devices that require a compact design, as it saves space and increases the portability of the device.
The design of Cross-Blind PCB makes signal transmission more stable and reduces the possibility of signal interference and crosstalk. This helps improve the performance of electronic devices and ensures their stability and reliability in different environments.
The design of Cross-Blind PCB allows for more efficient heat dissipation because the layout of the board can be more flexible in considering thermal solutions. This is especially important for high-performance equipment or equipment that needs to run for long periods of time, as it can help maintain the temperature of the equipment within a safe range.
Although the manufacturing process of Cross-Blind PCB may be more complex, in some cases, it can improve manufacturing efficiency. Through reasonable design, Cross-Blind PCB can reduce process steps and material waste in production, thereby reducing manufacturing costs and improving production efficiency.
To sum up, Cross-Blind PCB has obvious advantages over traditional PCB, including increasing circuit density, reducing size, improving performance and stability, improving heat dissipation, and improving manufacturing efficiency. These advantages make Cross-Blind PCB an ideal choice in the design and manufacturing of many electronic devices.
How much does Cross-Blind PCB cost?
When it comes to Cross-Blind PCB manufacturing costs, it’s crucial to understand how they are determined. In this regard, the cost is determined based on multiple factors, including but not limited to material cost, manufacturing process, number of board layers, board thickness, aperture, surface treatment, etc. Let’s take a deeper look:
First of all, material cost is an important factor in determining the manufacturing cost of Cross-Blind PCB. Prices vary widely for different types of substrate materials, copper foil thicknesses, and other chemistries, so all considerations need to be made when choosing the right material.
The manufacturing of Cross-Blind PCB requires special processes, such as laser drilling, interlayer copper filling, etc. These processes are usually more complex and expensive than traditional PCB manufacturing processes. Therefore, the complexity of the manufacturing process also affects the manufacturing cost.
Cross-Blind PCBs usually have multi-layer structures, which increase manufacturing costs. In addition, the thickness of the board will also have an impact on the cost. Generally speaking, thicker boards will cost more than thinner boards.
The accuracy of the hole diameter and hole wall is critical to the manufacturing of Cross-Blind PCB. Smaller and more precise hole diameters require higher manufacturing costs. At the same time, the quality of the hole walls also affects manufacturing reliability and cost.
Finally, surface treatment is also one of the factors that affects the manufacturing cost of Cross-Blind PCB. Different surface treatment processes have different costs, such as HASL, ENIG, OSP, etc. Choosing the appropriate surface treatment method will also affect the manufacturing cost.
Therefore, to understand the manufacturing cost of Cross-Blind PCB, it is necessary to comprehensively consider the above factors and carry out reasonable control and management during the actual manufacturing process. Only in this way can we ensure that manufacturing costs are reduced as much as possible and production efficiency is improved while meeting quality requirements.
What materials are used in Cross-Blind PCB?
During the manufacturing process of Cross-Blind PCB, it is crucial to select the appropriate materials, which need to have high performance, durability and reliability to ensure the stable operation and long-term use of the PCB. The following are the main materials commonly used in Cross-Blind PCB:
Substrate material: The substrate of Cross-Blind PCB usually uses fiberglass reinforced epoxy resin (FR-4) as the substrate material. FR-4 has excellent electrical properties, mechanical strength and high temperature resistance, and is one of the commonly used substrate materials for manufacturing PCBs.
Copper foil: Copper foil is the main conductive layer on PCB and is used to make circuit lines and connection points. In Cross-Blind PCB, high-purity copper foil is usually used to ensure the stability and conductive properties of the circuit.
Filling material: The filling material in Cross-Blind PCB is mainly used to fill the gaps between layers to enhance the mechanical strength and stability of the PCB. Commonly used filling materials include epoxy resin, polyimide (PI), etc.
Covering material: In order to protect the PCB surface from the external environment, the PCB surface is usually covered with a layer of protective material. Commonly used covering materials include epoxy resin, polyurethane, etc. These materials have good insulation properties and corrosion resistance.
Soldering materials: The soldering materials used to connect various components on the PCB are also one of the key materials in Cross-Blind PCB manufacturing. Common soldering materials include solder, solder paste, etc., which can ensure a stable connection between electronic components and PCB.
Special materials: Sometimes, some special materials may need to be used in the manufacturing process of Cross-Blind PCB, such as thermal conductive materials to improve the heat dissipation performance of the PCB, fireproof materials to improve the fireproof rating of the PCB, etc.
To sum up, the manufacturing of Cross-Blind PCB involves the selection and application of multiple materials, which together ensure the performance and reliability of the PCB. The correct selection and use of these materials will help improve the quality and stability of Cross-Blind PCB to meet the design and manufacturing needs of various electronic devices.
Who makes Cross-Blind PCBs?
When choosing the right Cross-Blind PCB manufacturer, there are a number of factors to consider to ensure the quality, reliability and performance of your final product. As a professional electronic equipment manufacturer, our company is committed to providing customers with high-quality Cross-Blind PCB solutions.
First, our manufacturers need to have advanced technology and equipment to ensure the precision and efficiency of the production process. Our manufacturing partners have advanced manufacturing processes and equipment, including the latest laser drilling technology and automated production lines, to meet the manufacturing needs of high-quality Cross-Blind PCBs.
Secondly, the manufacturer’s experience and expertise are also important considerations in selection. Our manufacturing partners have rich experience and professional technical teams, able to provide customers with a full range of technical support and solution customization services. Whether it is technical consultation during the design stage or quality control during the production process, we are able to provide professional support and guidance.
In addition, the manufacturer’s reliability and delivery capabilities are also key considerations in selection. Our manufacturing partners have strict quality management systems and stable supply chain networks to ensure accuracy and reliability of delivery times. Whether it is a small batch order or large-scale production, we are able to meet our customers’ needs and ensure timely delivery.
To sum up, as a professional electronic equipment manufacturer, our company has advanced technology and equipment, rich experience and expertise, and reliable delivery capabilities, and is able to provide customers with high-quality Cross-Blind PCB solutions . We look forward to working with you to jointly promote the development and innovation of the electronics industry.
What are the characteristics of great customer service?
Excellent customer service is crucial when choosing a Cross-Blind PCB manufacturer. A good manufacturer can not only provide high-quality products, but also provide customers with a full range of support and services. Here are the customer service characteristics a quality Cross-Blind PCB manufacturer should have:
Prompt response: A good manufacturer should be able to respond promptly to customer needs and questions, whether through email, phone, or online chat. Timely communication can help customers better understand the progress of the project and solve possible problems in a timely manner.
Professional knowledge: Manufacturers should have extensive industry experience and expertise and be able to provide customers with professional advice and guidance. They should understand the latest technologies and trends in Cross-Blind PCB manufacturing and be able to provide customized solutions according to customer needs.
Customized solutions: An excellent manufacturer should be able to provide customized solutions according to the specific needs of customers, including PCB design, material selection, process flow, etc. They should be able to flexibly adjust production plans to meet customers’ special requirements.
Good communication: Manufacturers should maintain good communication with customers, promptly update project progress, and actively listen to customer feedback and suggestions. They should be able to understand customer needs and communicate and coordinate effectively during the manufacturing process.
After-sales support: An excellent manufacturer should provide customers with comprehensive after-sales support services, including technical support, product warranty and after-sales maintenance. They should be able to provide timely help and support when customers need it and ensure customer satisfaction with products and services.
By providing the above quality customer service characteristics, Cross-Blind PCB manufacturers can establish good cooperative relationships, win the trust and recognition of customers, and achieve a win-win situation.
FAQS
What are the key differences between Cross-Blind PCBs and traditional PCBs?
Cross-Blind PCBs differ from traditional PCBs primarily in their ability to support complex circuitry with multiple layers and interconnected traces, enhancing signal integrity and reducing electromagnetic interference.
How does Cross-Blind PCB manufacturing impact overall product cost?
While Cross-Blind PCBs offer numerous benefits, including increased functionality and reduced size, their manufacturing process can be more intricate and costly compared to conventional PCBs. Factors such as material selection, layer count, and production volume significantly influence the final cost.
What materials are commonly used in Cross-Blind PCB fabrication?
Cross-Blind PCBs often utilize high-quality substrates such as FR-4 epoxy fiberglass, as well as specialized materials like polyimide for flexible circuit applications. Copper foils of varying thicknesses are employed for conductor layers, while solder masks and surface finishes contribute to durability and reliability.
What challenges may arise during Cross-Blind PCB manufacturing?
Cross-Blind PCB manufacturing presents unique challenges, particularly concerning precise layer alignment, via registration, and thermal management. Ensuring consistent quality across multiple layers and minimizing signal distortion require meticulous attention to detail and advanced manufacturing techniques.