CPU Ball Package Substrates Manufacturer.A CPU Ball Package Substrates Manufacturer specializes in producing high-quality substrates for CPU ball grid array (BGA) packaging. These substrates serve as critical components, providing mechanical support and electrical connections between the CPU and the motherboard. By utilizing advanced materials and precise manufacturing processes, they ensure reliable performance and durability in various electronic applications, from consumer devices to industrial systems.
CPU Ball Package Substrates are an indispensable and important part of modern electronic equipment. As a key hub for connecting electronic components, it provides basic support for various electronic devices and systems. This article will delve into the design, materials, dimensions, manufacturing processes, application fields, advantages and FAQs of the CPU ball device substrate, aiming to help readers fully understand this key technology.
What are CPU Ball Package Substrates?
CPU Ball Package Substrates are a key electronic component that provide necessary support and connections for modern electronic equipment. It is a flat plate-like structure usually made of non-conductive material, the most common of which is fiberglass-reinforced epoxy, or FR4. This material has good mechanical properties and high temperature resistance, making it suitable as a substrate for electronic devices.
On the CPU ball device substrate, conductive paths, also known as lines, are created by printing or etching. These lines connect various electronic components on the board, such as processors, memories, sensors, etc., as well as the interactive connections between them. This design enables each electronic component to effectively transmit and communicate data and achieve the normal function of the device.
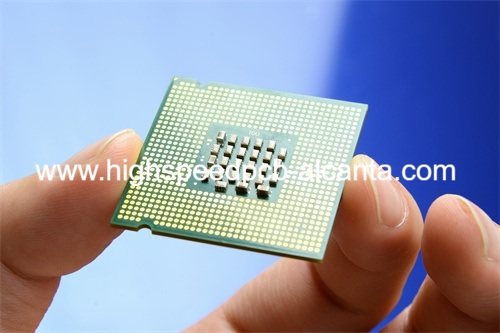
CPU Ball Package Substrates Manufacturer
The design and manufacturing of CPU ball device substrates require highly precise processes. Designers need to consider component layout, circuit design, signal integrity, electromagnetic compatibility and other factors to ensure the performance and reliability of electronic equipment. The manufacturing process involves multiple steps such as the selection and preparation of substrate materials, printing or etching of circuits, application of solder cap layers, assembly and testing. Each step requires precise operation and strict quality control.
CPU ball device substrates are widely used in modern electronic equipment. They are used in a variety of products including mobile phones, tablets, laptops, network equipment, industrial control systems, and more. As electronic equipment continues to develop and become more intelligent, the demand for CPU ball device substrates is also increasing.
In general, CPU ball device substrates are indispensable key components in modern electronic equipment. They provide the necessary conditions for the interaction between various electronic components by providing electrical connections and support, promoting the development of electronic technology. and applications.
CPU Ball Package Substrates design Reference Guide.
The design of the CPU ball device substrate is a critical step in ensuring the proper functionality and performance of the final product. During the design process, several factors need to be considered to ensure proper placement of electronic components and efficient routing of electrical connections on the board. Designers must consider component placement to minimize signal interference and electromagnetic interference. Proper component layout can not only improve signal integrity, but also reduce the noise level of the circuit, thereby improving system performance and stability.
In addition, thermal management is also a crucial consideration during the design process. Modern electronic devices consume increasingly higher amounts of power, so the heat generated by electronic components must be dealt with efficiently. In the design of the CPU ball device substrate, the layout of the heat sink, the design of the heat dissipation path, and the selection of thermally conductive materials need to be considered to ensure that the components can operate within a safe temperature range.
Another important design consideration is manufacturability. Designers need to select suitable materials and manufacturing processes to ensure that the designed substrates can be manufactured stably and reliably in mass production. Reasonable design can not only reduce manufacturing costs, but also improve production efficiency and product quality.
In summary, the design of a CPU ball device substrate involves many aspects, including component layout, signal integrity, thermal management, and manufacturability. By taking these factors into consideration and adopting appropriate design strategies, designers can ensure that the final product has excellent performance and reliability.
What material is used in CPU Ball Package Substrates?
The CPU ball device substrate is a key component in modern electronic equipment, and its material selection is crucial to its performance and reliability. Typically, the CPU ball device substrate is made of materials such as fiberglass reinforced epoxy resin (FR4). FR4 has excellent insulation properties, mechanical strength and heat resistance, and can meet the requirements of most applications. However, in some special applications, other materials may be required.
Ceramics are a common alternative material with excellent high temperature resistance and dimensional stability, making them suitable for high-frequency circuits and applications in high-temperature environments. Polyimide is another common choice, offering excellent chemical stability, mechanical strength and high temperature resistance for performance-critical applications. Metal base materials are mainly used in situations where good thermal conductivity and heat dissipation are required, such as high-power electronic equipment and LED lighting modules.
Material selection depends on the specific application requirements of the CPU ball device substrate, including working environmental conditions, frequency requirements, thermal management needs and other factors. When selecting materials, these factors need to be considered comprehensively and trade-offs made based on the actual situation to ensure that the CPU ball device substrate can operate stably and reliably in various application scenarios.
What size are CPU Ball Package Substrates?
CPU ball device substrate sizes vary depending on the specific application and design of the electronic device or system. This diversity reflects the varying needs of different industries and uses. From small portable devices to large industrial systems, CPU ball device substrates are available in a wide range of flexible sizes.
Miniaturization is an important trend in modern smartphones and wearable devices. Therefore, CPU ball device substrates for these devices are usually very compact to accommodate the small size and thin design of the device. These small substrates often feature tiny packages and high-density layouts to minimize size while ensuring performance and functionality.
In comparison, CPU ball device substrates used in industrial equipment and telecommunications infrastructure tend to be larger. These devices typically need to handle more data and more complex tasks, thus requiring more components and connections. Large substrates can accommodate more electronic components and provide more electrical connection interfaces to meet the performance and expansion needs of the device.
Not only that, some special applications may also require very large CPU ball device substrates. For example, server systems used in data centers may require huge substrates to support large-scale data processing and storage tasks. In these cases, the substrate may be several feet or more in size to accommodate large numbers of processors, memory, and other critical components.
To sum up, CPU ball device substrates come in a wide range of sizes, ranging from small mobile phones and wearable devices to large industrial systems and data center servers. This diversity reflects the unique needs for CPU ball device substrates in different application fields, while also providing flexibility and choice for the design and manufacturing of electronic equipment.
The Manufacturer Process of CPU Ball Package Substrates.
The manufacturing process of CPU ball device substrates is a complex and precise process that involves multiple steps, from substrate preparation to final component assembly and testing. Here’s an overview of the process:
The first is the substrate preparation stage. At this stage, the substrate material is selected and prepared for subsequent processing. Typically, the substrate material is made from fiberglass reinforced epoxy (FR4), but other materials may be used, depending on specific application needs.
Next is layer alignment. At this stage, if the substrate is a multi-layer structure, the alignment between the different layers is crucial. This ensures that the conductive lines formed in subsequent steps connect correctly.
Then comes the etching or printing of the conductive lines. In this step, depending on the design requirements, a metal layer (usually copper) is deposited on the surface of the substrate, and then chemical etching or printing techniques are used to remove the unnecessary metal parts to form the required conductive lines.
Next comes the drilling of component holes. At this stage, holes are drilled into the substrate using high-precision drilling machines for mounting electronic components. The location and size of these holes must be accurate to ensure accurate and reliable component installation.
This is followed by the application of the welded cap layer. Solder capping is typically a protective coating used to cover conductive traces and component holes to prevent corrosion and mechanical damage. It also provides a flat surface for subsequent component installation.
Finally comes component assembly and testing. At this stage, electronic components are mounted to the substrate and connected to conductive traces using soldering or other connection techniques. After the assembly is completed, strict testing and quality control are carried out to ensure that the function and performance of the CPU ball device substrate meet the design requirements.
In general, the manufacturing process of CPU ball device substrates involves multiple complex steps and sophisticated technologies, requiring a high degree of expertise and strict quality control to ensure the quality and reliability of the final product.
The Application area of CPU Ball Package Substrates.
The wide application of CPU ball device substrates in various industries demonstrates its importance and versatility in the development of modern technology. The following is the application range of CPU ball device substrates in different industries:
Consumer Electronics
In the field of consumer electronics, CPU ball device substrates are widely used in various products, such as smartphones, tablets, TVs, audio systems, etc. These devices require high-performance and high-density electronic component layout, as well as stable and reliable electrical connections. The CPU ball device substrate can meet these needs and support the stable operation of the device.
Car
The automotive industry has a growing demand for CPU ball device substrates, which are used in vehicle electronic systems, such as engine control units (ECUs), vehicle entertainment systems, driving assistance systems, etc. In the automotive environment, the CPU ball device substrate needs to be resistant to high temperature, vibration and corrosion to ensure stable performance under harsh conditions.
Aerospace
In the aerospace field, CPU ball device substrates are used in key equipment such as flight control systems, navigation systems, and communication systems. Since the aerospace environment places extremely high demands on electronic equipment, the CPU ball device substrate needs to undergo rigorous testing and certification to ensure its reliability and stability under extreme conditions.
Medical equipment
In the manufacturing of medical equipment, CPU ball device substrates are widely used in various medical equipment such as medical imaging equipment, pacemakers, and blood pressure monitors. These devices have extremely high requirements for precise control and high reliability of electronic components. The CPU ball device substrate can provide stable electrical connections and high-performance circuit layout.
Telecommunications
In the field of telecommunications, CPU ball device substrates are used in network equipment such as communication equipment, base stations, and routers. These devices require high-speed data transmission and stable signal processing capabilities. The CPU ball device substrate can meet these requirements through optimized circuit design and high-quality manufacturing processes.
Automated industry
In the field of industrial automation, CPU ball device substrates are used in various automation equipment such as control systems, sensor networks, and robots. These devices require stable and reliable control circuits and high-speed data processing capabilities. The CPU ball device substrate can provide reliable electrical connections and high-performance circuit layout to support the development and application of industrial automation.
In general, CPU ball device substrates play an important role in various industries, providing important support for the development of modern technology and the performance improvement of various electronic equipment.
What are the advantages of CPU Ball Package Substrates?
The CPU ball device substrate is an indispensable key component in modern electronic equipment. It has many advantages over other wiring methods, providing excellent performance and reliability for various application scenarios.
First, the CPU ball device base plate has a compact size. Due to its design using multi-layer stacking technology, the CPU ball device substrate can accommodate more electronic components and circuits in a relatively small space, making electronic equipment more compact and lightweight.
Secondly, the CPU ball device substrate has high reliability. The advanced technology and quality control measures used in the manufacturing process ensure the stability and reliability of the substrate, allowing it to operate stably in various harsh environmental conditions while reducing failure rates and repair costs.
In addition, the CPU ball device substrate is easy to mass-produce. Using automated production lines and efficient manufacturing processes, the CPU ball device substrate can achieve fast and efficient mass production, thereby reducing production costs and improving production efficiency.
In addition, the CPU ball device substrate can reduce assembly errors. Because its design and manufacturing processes are highly standardized and automated, the component layout and connection methods on the substrate can be precisely controlled, reducing the possibility of human error and improving product consistency and reliability.
In addition, the CPU ball device substrate can improve signal integrity. Through careful design and layout, the signal transmission lines on the substrate can be optimized and optimized, thereby reducing signal distortion and interference and ensuring the stability and reliability of data transmission.
Finally, the CPU ball device substrate also features enhanced thermal performance. The heat dissipation materials and design technologies used in the manufacturing process can effectively conduct heat from key components to the substrate surface, improving heat dissipation efficiency, thereby extending the service life of electronic equipment and protecting the stability of key components.
In summary, the CPU ball device substrate has obvious advantages in compact size, high reliability, ease of mass production, reduced assembly errors, improved signal integrity, and enhanced thermal performance, making it ideal for various electronic devices and systems. choose.
FAQ
What is the design software for CPU ball device substrate?
The design of the CPU ball device substrate usually uses professional electronic design automation (EDA) software, such as Altium Designer, Cadence Allegro and Mentor Graphics PADS. These software provide a wealth of design tools and functions to help engineers implement complex layout and routing.
What are the considerations in material selection for CPU ball device substrates?
When selecting a CPU ball device substrate material, factors to consider include the temperature and humidity of the working environment, required electrical performance, mechanical strength requirements, and cost. Commonly used materials such as FR4 are suitable for general applications, while high-performance materials such as polyimide (PI) may need to be selected for applications under high temperatures or special environments.
What are the manufacturing technologies for CPU ball device substrates?
Manufacturing technologies for CPU ball device substrates include traditional etching, printing, drilling and soldering cap layer applications, as well as advanced multi-layer stacking, blind via and buried via technologies. With the development of technology, more and more innovative manufacturing technologies are being used in the production of CPU ball device substrates to meet increasingly complex design requirements.
How to test the reliability of the CPU ball device substrate?
Reliability testing of CPU ball device substrates includes electrical testing, environmental testing and accelerated reliability testing. Electrical testing is used to verify the correctness and performance of electrical connections; environmental testing simulates conditions such as temperature, humidity, and vibration in different working environments; reliability accelerated testing is performed by subjecting samples to accelerated aging tests such as high temperature, high humidity, and temperature cycles. Assess its long-term stability.
What are the environmental considerations for CPU ball device substrates?
When designing the CPU ball device substrate, the impact of environmental factors on its performance and reliability needs to be considered. For example, in the field of automotive electronics, the CPU ball device substrate needs to be able to withstand the harsh temperature and vibration environment inside the car; while in the aerospace field, the substrate needs to meet the strict environmental standards of avionics products.