CPCORE Structure Substrates Manufacturer, Professional packaging substrate production company, mainly produces high layer substrate, we have more than 10,000 employees of the production plant.
This passage highlights the significance of CPCORE structure manufacturers in the realm of modern electronics. These manufacturers specialize in producing CPCORE structures, essential components in integrated circuit packaging. The CPCORE structure serves as a crucial link between the chip and the external environment, fulfilling functions such as protection, electrical connectivity, and heat dissipation. The design and fabrication of these structures are pivotal, directly impacting the performance and reliability of electronic products.
CPCORE structural fabricators are not merely producers but also drivers of technological innovation and engineering advancement. They constantly introduce new materials, processes, and design concepts to enhance the performance and reliability of CPCORE structures, catering to evolving customer demands. With experienced teams, they offer professional technical support and customized solutions, adapting swiftly to market changes.
In essence, CPCORE structure manufacturers are leading innovators in the electronics industry, propelling its development through continuous innovation and dedicated efforts. Their presence and progress not only ensure customers receive dependable products and services but also contribute to the advancement and expansion of the entire electronics industry ecosystem.
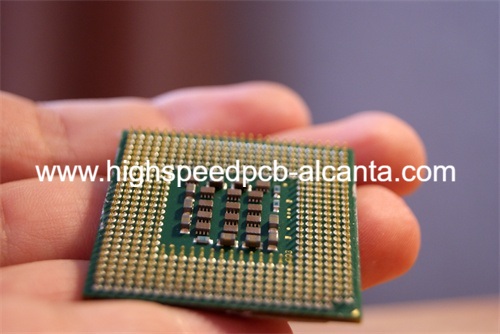
CPCORE Structure Manufacturer
What are the types of CPCORE structure manufacturers?
CPCORE structure manufacturer is one of the companies that plays a key role in the modern electronics industry. These manufacturers are committed to producing and providing various
This passage outlines three distinct sectors within the CPCORE (Chip Package Core) structure manufacturing field, tailored to meet diverse technical requirements in the electronics industry. Firstly, it emphasizes companies dedicated to HDI (High-Density Interconnect) boards, renowned for their ability to integrate numerous circuits into compact designs, particularly prevalent in portable electronic devices. Manufacturers in this sector are esteemed for their technical proficiency and innovative solutions.
The second sector pertains to Rigid-Flex boards, which amalgamate features of both rigid and flexible boards, serving applications requiring bending or folding. These boards find utility in industries such as automotive, aerospace, and medical equipment. Manufacturers specializing in Rigid-Flex boards typically possess considerable experience and technological expertise in merging flexible and rigid circuits.
The third sector centers around manufacturers prioritizing multi-layer board production, where multiple circuit layers are layered together. This type of board is widely used in computer systems, communications, and industrial control applications. Manufacturers in this category are required to have robust production capabilities and technical proficiency due to the complexity of producing multilayer boards.
In summary, the passage underscores the varied expertise and contributions of CPCORE structure manufacturers to the advancement and innovation of the electronics industry. Selecting the appropriate manufacturer hinges on client requirements and project specifications, underscoring the importance of discerning the differences among these manufacturers.
What are the advantages of CPCORE structure manufacturers?
This passage highlights the distinct advantages of CPCORE structure manufacturers compared to other manufacturers. Firstly, they possess superior technical expertise and strength, boasting seasoned R&D teams capable of offering professional support and solutions throughout the design and manufacturing phases. This expertise extends to understanding and researching integrated circuit packaging requirements, enabling them to better fulfill customer needs compared to traditional PCB manufacturers.
Secondly, CPCORE structure manufacturers leverage advanced production equipment and process technology to uphold product quality and performance. Their commitment to incorporating the latest production techniques and equipment, coupled with ongoing process optimization, ensures adherence to the highest quality standards. This continuous innovation fortifies their position in competitive markets.
Moreover, CPCORE structure manufacturers excel in offering customized services, collaborating closely with clients to tailor products to their precise specifications. This personalized approach enhances product competitiveness and market share by addressing individual customer needs effectively.
Additionally, these manufacturers demonstrate flexible production capabilities and expedited lead times, adeptly adjusting production schedules to meet varying order volumes and delivery deadlines. This agility enables timely product delivery, enhancing production efficiency and market responsiveness.
In summary, CPCORE structure manufacturers enjoy a multitude of advantages, including robust technical prowess, quality assurance, tailored services, and agile production capabilities.
The manifestation of these advantages has made CPCORE structure manufacturer the preferred partner of many customers, providing customers with high-quality, high-performance products and services.
What are the benefits of choosing CPCORE structure manufacturer?
Choosing a CPCORE structure manufacturer has significant advantages over other manufacturers, which are mainly reflected in the following aspects:
First of all, CPCORE structure manufacturers have rich experience and expertise and are able to provide customers with more professional solutions. Since the CPCORE structure plays a key role in integrated circuit packaging, manufacturers need to have deep technical strength and industry experience. CPCORE structure manufacturers usually have an experienced technical team that can understand customer needs and provide customized solutions to provide customers with better support and service.
This passage emphasizes the advantages of selecting a CPCORE structure manufacturer, particularly in the realm of integrated circuit packaging. These manufacturers are highlighted for their possession of advanced production equipment and technology, crucial for ensuring high product quality and performance. The link between product quality and the overall stability and reliability of a system is underscored.
Furthermore, the text points out the customization capabilities of CPCORE structure manufacturers, which can cater to the diverse and specific needs of customers. Unlike standardized products, the ability to tailor production to individual requirements enhances customer satisfaction. In conclusion, the passage advocates for the choice of CPCORE structure manufacturers, citing their wealth of experience, professional knowledge, advanced technology, and flexibility in customization as compelling reasons for customers seeking integrated circuit packaging services.
What is the manufacturing process of CPCORE structures?
The manufacturing process of CPCORE structures is a complex and precise process designed to ensure that the final product meets the customer’s specific needs. The following will introduce in detail the manufacturing process of the CPCORE structure and its customized production method.
This passage outlines the manufacturing process of CPCORE structures, a process that involves several key steps tailored to meet customer specifications and ensure high-quality end products.
Design Phase: Engineers collaborate with customers to understand their requirements and formulate a design plan, encompassing chip layout, circuit connections, and packaging.
Raw Material Sourcing: The manufacturer procures necessary materials such as substrates, conductive and insulating layers, and packaging materials crucial for product quality.
Production Stage: Utilizing advanced equipment and techniques, the manufacturer builds the CPCORE structure layer by layer, implementing processes like chemical etching and thin film deposition to create circuit connections and packaging structures.
Inspection and Testing: Completed CPCORE structures undergo rigorous evaluation to confirm adherence to quality standards, involving visual inspection, electrical tests, and reliability assessments.
Customized Production: Manufacturers adapt production methods to fulfill specific customer requirements, adjusting designs, materials, and processes as needed.
Delivery and Service: Upon passing inspection, products are delivered to customers along with comprehensive after-sales support, encompassing technical assistance, maintenance, and warranties.
In summary, the manufacturing process for CPCORE structures integrates design, material procurement, production, testing, customization, and service provision. Through meticulous processes and tailored production approaches, manufacturers deliver high-quality CPCORE products aligned with customer needs.
What are the application fields of CPCORE structure?
The provided passage highlights the significance of the CPCORE (Chip Package Core) structure in integrated circuit packaging, emphasizing its diverse applications across various industries. In the realm of communications, CPCORE structures are extensively utilized in mobile communications equipment, base stations, and satellite communications. These structures serve crucial roles in connecting electronic components, transmitting signals, and safeguarding chips, contributing to the high performance and stability of devices such as mobile phones and routers.
In the medical field, CPCORE structures find widespread use in medical equipment and monitoring instruments. The reliability of these structures ensures data accuracy and stability, enabling them to fulfill vital functions like data transmission and signal processing, thereby supporting the development of the medical industry.
Automotive applications also benefit from CPCORE structures, particularly in electronic systems such as engine control units (ECUs), in-vehicle entertainment systems, and safety systems. The growing demand for these structures in the automotive sector underscores their essential role in connecting components, transmitting data, and protecting electronic elements, ultimately contributing to the intelligence and safety of automobiles.
Industrial control represents another domain where CPCORE structures play a pivotal role. Widely employed in industrial automation equipment, robots, and sensors, these structures provide highly reliable electronic components to ensure the stability and safety of the production process. Key functions such as data transmission and signal processing in industrial control systems are facilitated by CPCORE structures, supporting the modernization of industrial production processes.
In summary, CPCORE structures are widely used in communications, medical, automotive, industrial control and other fields. They play key roles in connecting, transmitting data, protecting electronic components, etc. in these fields, and improve the performance and performance of modern electronic products. Reliability provides an important guarantee. With the continuous advancement of technology and the expansion of application fields, the CPCORE structure will continue to play an important role in promoting the development and innovation of various industries.
How to find the right CPCORE structure manufacturer?
This passage discusses the importance of selecting the right CPCORE structure manufacturer in various industries within the electronics sector, such as communications, computers, consumer electronics, and automobiles. It emphasizes the role of CPCORE structures as crucial components bridging chips and the external environment, highlighting their function in circuit connectivity, support, and protection.
The passage provides tips for identifying suitable manufacturers, including considerations such as industry experience, quality control measures, customization capabilities, production capacity, delivery lead times, and technical support services. It stresses the significance of these factors in ensuring product quality, performance, and successful production.
In essence, the passage underscores the critical nature of selecting a reliable CPCORE structure manufacturer to meet specific product requirements and achieve business objectives effectively.
What is the quotation from CPCORE structure manufacturer?
When choosing a CPCORE structure manufacturer, it is crucial to understand their quotations. However, CPCORE structure manufacturers’ quotations are not fixed but are affected by a variety of factors. Let’s dive into these factors and learn how to get a fair quote.
This paragraph outlines how product specifications and production quantity impact quotations for CPCORE structures. Product specifications, including size, material, layer count, and thickness, directly influence costs and quotations. Higher specifications entail higher manufacturing costs. Additionally, production quantity plays a significant role; larger quantities generally lead to lower costs due to economies of scale. Consequently, increased production quantities often result in more competitive pricing offers.
Process requirements: Different process requirements will lead to different manufacturing costs. Some special process technologies may require higher investment and more complex operating procedures, thereby increasing manufacturing costs and quotations.
This passage discusses various factors that impact the quotation process when dealing with manufacturers. It emphasizes the importance of delivery time requirements, suggesting that urgent delivery requests may lead to increased manufacturing costs. It also highlights the significance of customers being clear about their product needs, including specifications and quantity, to obtain accurate quotations. The recommendation to inquire from multiple manufacturers for price comparison is given, enabling customers to better understand market conditions. Furthermore, it emphasizes the importance of negotiation and communication after receiving quotations, exploring potential cost reductions or flexible cooperation methods. The passage concludes by advising customers to consider not only the quotation but also comprehensive factors such as a manufacturer’s production capacity, quality assurance, and after-sales service when making a decision.
CPCORE structure manufacturer’s quotation is affected by many factors, including product specifications, production quantity, process requirements and delivery lead time. Customers can obtain reasonable quotations through clear needs, multi-party comparison, negotiation and communication, and choose the partner that best suits their needs. Therefore, when choosing a CPCORE structure manufacturer, you should not only pay attention to the quotation level, but also consider comprehensive factors to ensure the best production services and product quality.
Frequently Asked Questions (FAQs)
What types of CPCORE structure manufacturers exist?
CPCORE structure manufacturers can be categorized into various types based on their specialization. These may include those focusing on HDI boards, Rigid-Flex boards, and other types of CPCORE structures. Each type of manufacturer has unique advantages and applications.
What advantages do CPCORE structure manufacturers offer over others?
CPCORE structure manufacturers boast distinct advantages, including higher production efficiency, superior quality control, and the ability to provide flexible custom solutions. These advantages make them the preferred partners for many electronic product manufacturers.
Why should one choose CPCORE structure manufacturers over traditional PCB manufacturers?
CPCORE structure manufacturers bring several advantages compared to traditional PCB manufacturers. They possess extensive experience and expertise, advanced production equipment, and technologies that ensure product quality and performance meet stringent standards.
What is the manufacturing process of CPCORE structures?
The manufacturing process of CPCORE structures involves several stages, including raw material procurement, process design, and production processing. CPCORE structure manufacturers typically customize production to meet specific customer requirements, ensuring products align with their unique application needs.
In which applications are CPCORE structures widely used?
CPCORE structures find extensive applications in various fields, such as communication, healthcare, automotive, and more. CPCORE structure manufacturers play a critical role in providing high-performance and reliable products for these diverse application areas.
How can one find suitable CPCORE structure manufacturers?
Finding suitable CPCORE structure manufacturers can be achieved through methods such as online searches, participating in industry trade shows, and consulting industry experts. Selecting the right CPCORE structure manufacturer is crucial for the successful development and production of products.